Mô hình sự phát triển cường độ của vật liệu cường độ thấp có kiểm soát
Bài báo này nghiên cứu việc sử dụng xỉ thép không gi (SSRS) trong việc thay thế xi măng để sản xuất vật liệu cường độ
thấp có kiểm soát (CLSM). Cốt liệu chính của hỗn hợp CLSM được hình thành từ cát song và đất đào theo tỷ lệ theo thể tích 6:4.
Tổng cộng có 12 hỗn hợp vữa được tạo ra khi thay đổi tỷ lệ xi măng thay thế lần lượt là 0%, 10%, 20%, 30% và tỷ lệ nước/chất
kết dính 3.4, 3.6, và 3.8. Trong khi đó, khối lượng chất kết dính được giữ cố định 100 kg/m3. Cường độ chịu nén của các mẫu được
thí nghiệm xác định ở các độ tuổi khác nhau. Kết quả cho thấy, tỷ lệ xỉ thay thế và tỷ lệ nước/ chất kết dính có ảnh hưởng đáng kể
đến cường độ chịu nén của mẫu. Đồng thời, dựa trên kết quả thực nghiệm, các tác giả đã thiết lập thành công mô hình sự phát
triển cường độ chịu nén của vữa CLSM theo thời gian.
Tóm tắt nội dung tài liệu: Mô hình sự phát triển cường độ của vật liệu cường độ thấp có kiểm soát
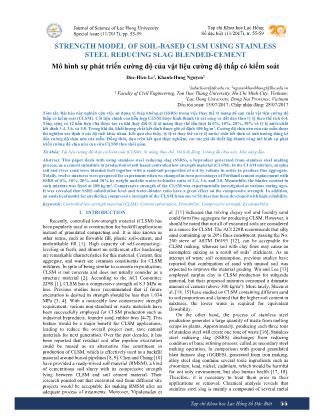
55 Tạp chí Khoa học Lạc Hồng Số Đặc Biệt Journal of Science of Lac Hong University Special issue (11/2017), pp. 55-59 Tạp chí Khoa học Lạc Hồng Số đặc biệt (11/2017), tr. 55-59 STRENGTH MODEL OF SOIL-BASED CLSM USING STAINLESS STEEL REDUCING SLAG BLENDED-CEMENT Mô hình sự phát triển cường độ của vật liệu cường độ thấp có kiểm soát Duc-Hien Le1, Khanh-Hung Nguyen2 1leduchien@tdt.edu.vn, 2nguyenkhanhhung@lhu.edu.vn 1 Faculty of Civil Engineering, Ton Duc Thang University, Ho Chi Minh City, Vietnam; 2Lac Hong University, Dong Nai Province, Vietnam Đến tòa soạn: 15/07/2017; Chấp nhận đăng: 28/07/2017 Tóm tắt. Bài báo này nghiên cứu việc sử dụng xỉ thép không gi (SSRS) trong việc thay thế xi măng để sản xuất vật liệu cường độ thấp có kiểm soát (CLSM). Cốt liệu chính của hỗn hợp CLSM được hình thành từ cát song và đất đào theo tỷ lệ theo thể tích 6:4. Tổng cộng có 12 hỗn hợp vữa được tạo ra khi thay đổi tỷ lệ xi măng thay thế lần lượt là 0%, 10%, 20%, 30% và tỷ lệ nước/chất kết dính 3.4, 3.6, và 3.8. Trong khi đó, khối lượng chất kết dính được giữ cố định 100 kg/m3. Cường độ chịu nén của các mẫu được thí nghiệm xác định ở các độ tuổi khác nhau. Kết quả cho thấy, tỷ lệ xỉ thay thế và tỷ lệ nước/ chất kết dính có ảnh hưởng đáng kể đến cường độ chịu nén của mẫu. Đồng thời, dựa trên kết quả thực nghiệm, các tác giả đã thiết lập thành công mô hình sự phát triển cường độ chịu nén của vữa CLSM theo thời gian. Từ khóa: Vật liệu cường độ tháp có kiểm soát (CLSM); Xi măng thay thế; Độ linh động; Cường độ chịu nén; Khả năng đào Abstract. This paper deals with using stainless steel reducing slag (SSRS), a byproduct generated from stainless steel making process, as a cement substitute in production of soil-based controlled low-strength material (CLSM). In the CLSM mixture, surplus soil and river sand were blended well together with a sand-soil proportion of 6:4 by volume in order to produce fine aggregate. Totally, twelve mixtures were prepared for experiment when we changed in turn percentages of Portland cement replacement with SSRS of 0%, 10%, 20%, and 30% by weight and the water-to-binder ratio of 3.4, 3.6, and 3.8. Meanwhile, the binder content in each mixture was fixed at 100 kg/m3. Compressive strength of the CLSM was experimentally investigated at various curing ages. It was revealed that SSRS substitution level and water-binder ratio have a great effect on the compressive strength. In addition, an analytical model for predicting compressive strength of the CLSM from one to 56 days has been developed with high reliability. Keywords: Controlled low-strength material (CLSM); Cement substitution; Flowability; Compressive strength; Excavatability 1. INTRODUCTION Recently, controlled low-strength material (CLSM) has been popularly used in construction for backfill applications instead of granulated compacting soil. It is also known as other terms, such as flowable fill, plastic soil-cement, and unshrinkable fill [1]. High capacity of self-compacting/- leveling in fresh, and almost no settlement after hardening are remarkable characteristics for this material. Cement, fine aggregate, and water are common constituents for CLSM mixtures. In spite of being similar to concrete in production, CLSM is not concrete and does not usually consider as a structure material [2]. According to the ACI Committee 229R [1], CLSM has a compressive strength of 8.3 MPa or less. Previous studies have recommended that if future excavation is desired its strength should be less than 1.034 MPa [3, 4]. With a noticeably low compressive strength requirement, various non-standard or waste materials have been successfully employed for CLSM production such as industrial byproducts, foundry sand, rubber tires [4-7]. This feature would be a major benefit for CLSM applications, leading to reduce the overall project cost, save natural materials for next generation. Over the past decades, it has been reported that residual soil after pipeline excavation could be reused as an alternative fine constituent in production of CLSM, which is effectively used as a backfill material around buried pipelines [8, 9]. Chen and Chang [10] have provided a ready-mixed soil material (RMSM), a kind of cementitious soil slurry with its compressive strength lying between CLSM and soil cement material. Their research pointed out that excavated soil from different site projects would be acceptable for making RMSM after an adequate process of treatments. Moreover, Vipulanadan et al. [11] indicated that mixing clayey soil and foundry sand could form fine aggregate for producing CLSM. However, it should be noted that not all of excavated soils are considered as a source for CLSM. The ACI 229R recommends that silty sand containing up to 20% fines constituent, passing the No. 200 sieve of ASTM D6193 [12], can be acceptable for CLSM making, whereas soil with clay fines may cause an incomplete mixing as a result of soils’ stickiness. As an attempt of waste soil consumption, previous studies have reported that combination of sand with unused soil was expected to improve the material grading. Wu and Lee [13] employed surplus clay in CLSM production for subgrade material, but their proposed mixtures consumed a dramatic amount of cement (above 300 kg/m3). More lately, Sheen et al. [14, 15] have studied on CLSM containing different sand to soil proportions and claimed that the higher soil content in mixtures, the lower water is required for equivalent flowability. On the other hand, the process of stainless steel production generates a large quantity of waste from melting scraps in plants. Approximately, producing each three tons of stainless steel will create one tone of waste [16]. Stainless steel reducing slag (SSRS) discharges from reducing condition of basic refining process, called as secondary steel making operation. In comparison with ground granulated blast furnace slag (GGBFS), generated from iron making, alloy steel slag contains several toxic ingredients such as chromium, lead, nickel, cadmium, which would be harmful for not only environment, but also human health [17, 18]. Therefore, it is necessary to treat them prior to their applications or removal. Chemical analysis reveals that stainless steel slag is mainly a compound of several metal Lê Đức Hiển, Nguyễn Khánh Hùng 56 Tạp chí Khoa học Lạc Hồng Số Đặc Biệt oxides (e.g., CaO, SiO2, and Al2O3), which is similar to GGBFS. In addition, literature observation showed that stainless steel reducing slag is highly variable in chemical composition [18]. Generally, the CaO and Al2O3 contents are found to be higher than those of other slag, whereas the FeO or Fe2O3 is observed to be much less [16]. In practice, a large quantity of steel making slag has been usually employed in production of aggregates for road pavement or concrete purposes, and in fertilizer production [19, 20]. Lately, however, there has been a potential application of these wastes as a hydraulic supplementary after relevant treatments [17, 19, 21]. The present study is addressed toward providing strength model of an environment-friendly and low-cost CLSM using both SSRS and Portland cement as combined binder and surplus soil as fine constituent. The findings derived from the research are expected to contribute a deep understanding and corrected usage of hazardous and excavating wastes as recycled sources that is a beneficial solution in making green building materials. 2. LABORATORY STUDIES 2.1 Materials used and mix-proportion The SSRS used in this study has the specific gravity of 2.84 and the specific surface area of 4515 cm2/g, Blaine. It was obtained form Lihwa Corp. (Taiwan). Ordinary Type I Portland cement (OPC) conformed to ASTM C150 [22] with the specific gravity of 3.15 and specific surface area of 3851 cm2/g was used in mixtures. The chemical and physical properties of the SSRS and OPC were shown in Table 1. Table 1. Chemical and physical properties of OPC and SSRS Analysis results OPC, Type I SSRS § Chemical analysis (%) Silicon dioxide, SiO2 Aluminum oxide, Al2O3 Ferric oxide, FeO/Fe2O3 Calcium oxide, CaO Magnesium oxide, MgO Sulfur trioxide, SO3 Potassium oxide, K2O Sodium oxide, Na2O Titanium oxide, TiO2 Loss of ignition, L.O.I 20.87 4.56 3.44 63.14 2.82 2.06 - - - 2.30 22.97 4 0.08 51.26 8.1 - - - 0.09 - § Physical properties Fineness (cm2/g) Specific gravity 3851 3.15 4551 2.84 Fine aggregate was formed by well mixing concrete sand and surplus soil together in order to desirably improve the distribution of particles. The soil was obtained from a construction site (after eliminating almost organic substances) where the proposed CLSM is expected to use as a backfilled material for basement wall. Physical test shows that the collected surplus soil was a sandy-clayey soil, brown in color, and had the liquid limit (LL) and plastic index (PI) of 22 and 2.3, respectively. Also, its fine ingredient (passing No. 200 sieve) was found to be nearly 11% and was classified as a SP-SM soil (poorly graded sand with silt) in accordance with the Unified Soil Classification System (USCS) [23]. The excavated soil used in the work was dried in air condition to evaporate majority of water content before use. Results of the sieve analysis of materials were plotted in Fig. 1. Fineness modulus of the sand, soil, and combination were 2.60, 1.24, and 2.06, respectively. The sand to soil proportion was chosen at a predetermined ratio of 6:4. The goal of mix design for the proposed CLSM is expected to achieve the essential requirements of excavatable CLSM with hand tools, commonly expressed in term of the 28-day unconfined compressive strength being less than 1.034 MPa [4, 8, 24]. The experimental work was conducted on three mix groups, namely M34, M36 and M38, corresponding to three levels of water-to-binder ratio (w/b), e.g. 3.4, 3.6, and 3.8, respectively. Moreover, the binder (OPC and SSRS) dosage was fixed at 100 kg/m3 for each mixture (about 5% of total mixture’s weight). In each mix group, SSRS substituted for OPC with various ratios, such as 0% (reference), 10%, 20%, and 30%, by weight. Fig. 1 Grain-size distribution of the sand, soil and combination. 2.2 Specimen preparation and testing procedures Unconfined compressive strength test was conducted on 100x200-cylindrical samples as per ASTM D4832 [25]. Fresh CLSM conformed the acceptance of flow consistency (200-300 mm) was filled in 100 mm diameter and 200 mm height moulds without requirement of vibration or compaction due to high flowability and self-compacting capacity of the material. All the cylinders were covered with wet burlap for 2-3 days and then slightly removed from the moulds. Thereafter, the specimens were carefully transferred and stored in curing environment (23 0C and 100% relative humidity) until achieving the testing ages (e.g., 07-, 28-, and 56 days). During demoulding and handling process, all samples must be no damages or scratches. Each strength test was done on three cylinders and the averages were obtained. 3. RESULTS AND DISCUSSIONS 3.1 Compressive strength development with times Compressive strength of the proposed CLSM was tested at 1-, 7-, 28-, and 56 days. All the 28-day cylindrical groups have the average compressive strength of 0.42-0.81 MPa, which were well-matched the acceptable range (0.35-1.034 MPa) for excavatable CLSM [4, 8, 24]. The strength development of 10% SSRS specimens was typically illustrated in Fig. 2. As expected, a longer age of curing is a higher compressive strength due to continuation of cementitious-hydrated process. The strength-time relationships can be analytically expressed in a logarithmic function of (where a, b are experimental coefficients; t is the curing age, days). The R- squared values were found to be equal or greater than 0.97, and this strongly confirms that the logarithmic formula are highly reliable for describing strength evolution of the soil- based CLSM. An analogous strength developing behavior 57 Mô hình sự phát triển cường độ của vật liệu cường độ thấp có kiểm soát Tạp chí Khoa học Lạc Hồng Số Đặc Biệt for CLSM prepared with Class C fly ash was also published by Türkel [26]. 3.2 Effects of w/b and SSRS substitution level on compressive strength Constituent materials and quantities have a great contribution to the performance of the CLSM because of being different in water demand. Among them, water-to- binder ratio, cement content, as well as aggregate’s characteristics are widely admitted to be major factors [24]. In general, increasing the w/b may be accompanied by a noticeable strength reduction. It is an expected result for cementitious materials, usually reported in literature due to forming high pore volume in the matrix [13, 27]. For example, as seen in Fig. 3, when w/b varied from 3.4 to 3.8, the associated compressive strength at 56 days decreased approximately by 18% (0.88–0.72 MPa) and 14% (0.65–0.57 MPa) for specimens without and with 30% SSRS replacement, respectively. Fig. 2 The compressive strength development as slag replacement level of 10% Fig. 3 The 56-day compressive strength with respect to water- binder ratio. Moreover, Figs. 4(a)-(c) indicate that the compressive strength of SSRS specimens is significantly lower than that of control (without slag) at any testing ages. A gradual increase in slag content could result in a steady strength reduction for all samples at each curing age, up to 56 days. For instance, for M34 mixture with 30% SSRS substitution, the strength at 01-, 07-, 28-, and 56 days was declined by approximately 38%, 39%, 27%, and 25% in comparison with the controls, respectively. Similarly, for the M36 and M38 mixtures, the corresponding strength drop were 34%, 41%, 18%, 23% and 29%, 37%, 32%, 31%, respectively. From Fig. 4, there are best-fit straight line expressed well relationship between compressive strength and slag replacement level (R2 ³ 0.82), and this result was in agreement with the previous research of Shafigh et al. [28], who studied on lightweight concrete. In addition, it is revealed that the strength loss had a tendency to be higher at early age (one day) and lower at later ages (28- and 56 days). This behavior is logical because SSRS is not as good as OPC in contributing to strength, especially at early ages. (a) M34 (b) M36 (c) M38 Fig. 4 Relationship between compressive strength and SSRS ratio. On the other hand, the 56-day compressive strength of 30% SSRS specimens was observed to decrease by about 25%, in average, comparing to the controls. This result was different from conventional concrete. Previous studies on concrete have reported that with a similar slag content in replacement with OPC, the compressive strength could be Lê Đức Hiển, Nguyễn Khánh Hùng 58 Tạp chí Khoa học Lạc Hồng Số Đặc Biệt comparable to that of plain concrete at 28- or 56 days [29- 31]. It is believed that very high water-binder ratio in CLSM mixture comparing to normal concrete is responsible for above strength reduction. Also, as a speculation, there would be a considerable strength gain in later ages beyond 56 days, which has been experimentally claimed by Shariq et al. [32], when they studied on concrete incorporating with GGBFS. Türkel [26] has been published a study on CLSM made with puzzolanic cement and Type C fly ash, in which its strength evolution was described with a similar manner. 3.3 The early and later-age strength relationships Fig. 5 demonstrates the relationship between the one-day and later compressive strength of the CLSM specimens. The strength at 01-, 07-, 28-, and 56 days were ranged from 0.13-0.25 MPa, 0.53-0.55 MPa, 0.42-0.81 MPa, and 0.57-0.88 MPa, respectively. It can be realized that a higher one-day compressive strength a higher is certainly long-term strength and vice versa. In addition, the 07-, 28-, and 56-day compressive strength are approximately 1.52, 3.72, 4.52 times as high as the one-day strength, in averages, respectively. Also, from Fig. 5, the correlations between one- day strength and 7-, 28,- 56-day strength can be expressed in linear forms; and these regression lines are graphically observed to be almost parallel, which was similar to the reports published by Wu and Lee [13], and Shafigh et al. [28]. This statement implies that there was probably a proportion of long-term strength to early strength, and it is helpful to predict later strength as soon as possible. Fig. 5 Later-ages strength versus one-day strength 3.4 Compressive strength model Developing a predicted-strength model being modified from the expression of Du et al. [24] is an additional attempt on this issue. Their predicted model was employed water-to- cement ratio as only variable for describing strength evolution of air-entrained CLSM mixture containing bottom ash as fine aggregate. Based on the experimental data, compressive strength of the proposed CLSM up to 56 days can be analytically evaluated via the following equation (1), which was derived from the regression approach with two independent variables of mixing proportion, viz. water-to- binder ratio and percentage of slag replacement: (1) where, is the compressive strength at curing ages of t (days); is the water-to-binder ratio; ps (%) is the percentage of SSRS replacement; a(t), b1(t), and b2(t) are coefficients depending on curing ages, t (days), determined as follows via regression analysis: Moreover, ACI Committee 209 [33] recommends the following equation (2) for evaluating cylinder compressive strength of concrete, based on the compressive strength measuring at 28 days, : (2) Fig. 6 indicates that the predicted strength from equation (1) was reasonably closer to the measured one than that of from equation (2), evidenced by the fact that almost the data points (marked in circles) are located within an error range of ± 10%. Indeed, equation (1), taking into account w/b and slag replacement ratio, gives a well-fitted result in strength prediction with a high determination coefficient (R2 = 0.97), a good indicator to check the “goodness” of the proposed formula. Fig. 6 Comparison of measured and predicted strength 4. REMARKS Several concluding remarks can be withdrawn from this study: An equation for predicting the strength development has been reasonably established via regression technique, in which two mix proportion variables (w/b and SSRS ratio) as well as curing ages were taken account. Also, a verified test was independently conducted to validate the performance of the predicted formula. Testing result exhibited that the proposed model is highly reliable to evaluate compressive strength. However, the suggested formula should be further considered in practical uses because it has been built up based on limited data. Increasing SSRS substitution ratio would lead to decrease the compressive strength because the reducing slag is not as good as OPC in contributing to strength, particularly at early ages. With 30% slag replacement, the 56-day compressive strength was observed a drop of 14-18% compared to the controls made with pure cement; and this strength reduction was expected in design due to convenience for controlling excavatability. 5. ACKNOWLEDGEMENT The author would like to thank Professor Sheen Yeong- Nain of National Kaohsiung University of Applied Sciences for the constructive discussions. R² = 0.97 0.00 0.15 0.30 0.45 0.60 0.75 0.90 1.05 0.00 0.15 0.30 0.45 0.60 0.75 0.90Measured strength (MPa) Data points 59 Mô hình sự phát triển cường độ của vật liệu cường độ thấp có kiểm soát Tạp chí Khoa học Lạc Hồng Số Đặc Biệt 6. REFERENCES [1] ACI-229R, Controlled-low strength materials (reproved 2005). Farmington Hills (MI), 2005. [2] Kuo, WT., Wang, HY., Shu, CY., Su, DS., "Engineering properties of controlled low-strength materials containing waste oyster shells", Construction and Building Materials, 46(0), 128- 33, 2013. [3] Lachemi, M., Hossain, KMA., Shehata, M., Thaha, W., "Controlled low strength materials incorporating cement kiln dust from various sources", Cement and Concrete Composites, 30(5), 381-92, 2008. [4] Taha, RA., Alnuaimi, AS., Al-Jabri, KS., Al-Harthy, AS., "Evaluation of controlled low strength materials containing industrial by-products", Building and Environment, 42(9), 3366- 72, 2007. [5] Folliard, KJ., Du, L., Halmen, C., Trejo, D., Leshchinsky, D., Sabol, S., NCHRP Report 597: Development of a Recommended practice for Use of controlled low-strength Material in highway construction, The National Academies Press; 2008. [6] Nataraja, MC., Nalanda, Y.. "Performance of industrial by- products in controlled low-strength materials (CLSM)", Waste Management, 28(7), 1168-81, 2008. [7] Wang, HY,, Chen, BT,, Wu, YW., "A study of the fresh properties of controlled low-strength rubber lightweight aggregate concrete (CLSRLC)", Construction and Building Materials, 41(0), 526-31, 2013. [8] Finney, AJ., Shorey, EF., Anderson, J., "Use of native soil in place of aggregate in controlled-low strength material (CLSM)", International Pipelines Conference, Atlanta, Georgia, United States, 1-13. 2008. [9] Wu, JY., "Soil-based flowable fill for pipeline construction", Proceedings of Pipelines 2005: Optimizing Pipeline Design, Operations, and Maintenance in Today’s Economy,. Houston, Texas, USA., 925-38, 2005. [10]Chen, JW, Chang, CF., "Development and Application of the Ready-Mixed Soil Material", Journal of Materials in Civil Engineering, 18(6), 722-29, 2006. [11]Vipulanandan, C., ASCE, M., Weng, Y. and Zhang, C., "Designing flowable grout mixes using foundry sand", Clay and Fly Ash, Advances in grouting and ground modification, 215-33, 2000. [12]ASTM: D6913., Standard test methods for particle-size distribution (Gradation) of soils using sieve analysis, 2009. [13]Wu, JY., Lee, MZ., Benefical Reuse of construction surplus clay in CLSM, International Journal of Pavement Research and Technology, 4(5), 293-300, 2011. [14]Sheen, YN., Zhang, LH., Le, DH., "Engineering properties of soil-based controlled low-strength materials as slag partially substitutes to Portland cement", Construction and Building Materials, 48: 822-9, 2013. [15]Sheen, Y-N., Huang, L-J, Wang, H-Y., Le, D-H., "Experimental study and strength formulation of soil-based controlled low- strength material containing stainless steel reducing slag", Construction and Building Materials, 54:1-9, 2014. [16]Huaiwei, Z., Xi, H., "An overview for the utilization of wastes from stainless steel industries", Resources, Conservation and Recycling, 55(8), 745-54, 2011. [17]Sheen, YN., Wang, HY., Sun, TH., "A study of engineering properties of cement mortar with stainless steel oxidizing slag and reducing slag resource materials", Construction and Building Materials, 40: 239-45, 2013. [18]Yildirim, IZ., Prezzi, P., "Chemical, Mineralogical, and Morphological Properties of Steel Slag", Advances in Civil Engineering, 13, 2011. [19]Kriskova, L., Pontikes, Y., Cizer, Ö., Mertens, G., Veulemans, W., Geysen D., et al., "Effect of mechanical activation on the hydraulic properties of stainless steel slags", Cement and Concrete Research, 42(6), 778-88, 2012. [20]Pellegrino, C., Cavagnis, P., Faleschini, F., Brunelli, K., "Properties of concretes with black/oxidizing electric arc furnace slag aggregate", Cement and Concrete Composites, 37(0), 232- 40, 2013. [21]Adolfsson, D., Robinson, R., Engström, F., Björkman, B., "Influence of mineralogy on the hydraulic properties of ladle slag", Cement and Concrete Research, 41(8), 865-71, 2011. [22]ASTM: C150, Standard Specification for Portland Cement, 2002. [23]Das B., Principles of Geotechnical engineering, 7th ed: Cengage Learning; 2007. [24]Du. L., Folliard, KJ., D. T., "Effects of Constituent materials and quantities on water demand and compressive strength of controlled low-strength material", Journal of Materials in Civil Engineering, 14(6): 485-9, 2002. [25]ASTM: D4832, Standard test method for preparation and testing of controlled low strength material (CLSM) Test Cylinders, 2002. [26]Türkel, S., "Long-term compressive strength and some other properties of controlled low strength materials made with pozzolanic cement and Class C fly ash", Journal of Hazardous Materials, B137:261-6, 2006. [27]Mehta, PK., Monteiro, P., "Concrete, microstructure, properties and materials", 3ed. New York: McGraw-Hill Professional, 2006. [28]Shafigh, P., Jumaat, MZ., Mahmud, HB., Alengaram, UJ., "Oil palm shell lightweight concrete containing high volume ground granulated blast furnace slag", Construction and Building Materials, 40: 231-8, 2013. [29]Beushausen, H., Alexander, M., Ballim, Y., "Early-age properties, strength development and heat of hydration of concrete containing various South African slags at different replacement ratios", Construction and Building Materials, 29(0),533-40, 2012. [30]Chen, B., Liu, J., "Experimental application of mineral admixture in lightweight concrete with high strength and workability", Construction and Building Materials, 22: 655-59, 2008. [31]Wang, H-Y., Lin, C-C., "A study of fresh and engineering properties of self-compacting high slag concrete (SCHSC)", Construction and building materials, 42(0, 132-6, 2013. [32]Shariq, M., Prasad, J., Abbas, H., "Effect of GGBFS on age dependent static modulus of elasticity of concrete", Construction and Building Materials,; 41(0), 411-8, 2013. [33]ACI-Committee, 209, Prediction of Creep, shrinkage, and temperature effects in concrete structures, Farmington Hills (MI),1999. BIOGRAPHY Dr. Duc-Hien Le Was born in 1979, Binh Dinh Province, Vietnam. He completed the Ph.D program in Civil Engineering at KUAS, Taiwan. He is now lecturer of Faculty of Civil Engineering, Ton Duc Thang University. His studies are related to construction materials, Sustainable materials in construction Mr. Hung-Khanh Nguyen Was born in 1979, Tieng Giang Province, Vietnam. He is working a lecturer at Faculty of Civil Engineering, Lac Hong University. His studies are related to construction, application software
File đính kèm:
mo_hinh_su_phat_trien_cuong_do_cua_vat_lieu_cuong_do_thap_co.pdf