Thiết kế và chế tạo đồ gá hàn - cắt tự động thép ống công suất vừa
Trong gia công cơ khí, việc cắt các phôi ống dài thành
các phôi ngắn hoặc hàn các đoạn phôi ống ngắn là việc khá
thường xuyên. Để đảm bảo được độ chính xác về kích thước, hình
dáng theo yêu cầu cũng như đạt năng suất cao thì cần thiết phải
dùng đồ gá. Bài báo đã tiến hành nghiên cứu thiết kế và chế tạo
đồ gá hàn và cắt tự động cho các thép ống công suất vừa. Kết quả
cho thấy đồ gá sau khi được chế tạo hoàn chỉnh đã làm việc tin
cậy, các sản phẩm được tạo ra nhờ sự hỗ trợ của đồ gá này có
chất lượng cao. Bên cạnh đó, đồ gá còn có những ưu điểm là kết
cấu tinh gọn có thể di chuyển dễ dàng trên các công trường, có
tính ứng dụng cao, giá thành thấp và dễ dàng vận hành. Từ đó, có
thể ứng dụng được trong các nhà xưởng hay các cơ sở gia công
cơ khí trong việc hàn và cắt.
Tóm tắt nội dung tài liệu: Thiết kế và chế tạo đồ gá hàn - cắt tự động thép ống công suất vừa
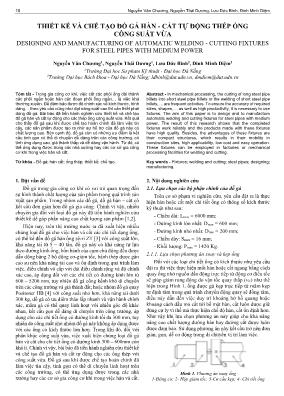
10 Nguyễn Văn Chương, Nguyễn Thái Dương, Lưu Đức Bình, Đinh Minh Diệm THIẾT KẾ VÀ CHẾ TẠO ĐỒ GÁ HÀN - CẮT TỰ ĐỘNG THÉP ỐNG CÔNG SUẤT VỪA DESIGNING AND MANUFACTURING OF AUTOMATIC WELDING - CUTTING FIXTURES FOR STEEL PIPES WITH MEDIUM POWER Nguyễn Văn Chương1, Nguyễn Thái Dương1, Lưu Đức Bình2, Đinh Minh Diệm2 1Trường Đại học Sư phạm Kỹ thuật - Đại học Đà Nẵng 2Trường Đại học Bách khoa - Đại học Đà Nẵng; ldbinh@dut.udn.vn, dmdiem@dut.udn.vn Tóm tắt - Trong gia công cơ khí, việc cắt các phôi ống dài thành các phôi ngắn hoặc hàn các đoạn phôi ống ngắn là việc khá thường xuyên. Để đảm bảo được độ chính xác về kích thước, hình dáng theo yêu cầu cũng như đạt năng suất cao thì cần thiết phải dùng đồ gá. Bài báo đã tiến hành nghiên cứu thiết kế và chế tạo đồ gá hàn và cắt tự động cho các thép ống công suất vừa. Kết quả cho thấy đồ gá sau khi được chế tạo hoàn chỉnh đã làm việc tin cậy, các sản phẩm được tạo ra nhờ sự hỗ trợ của đồ gá này có chất lượng cao. Bên cạnh đó, đồ gá còn có những ưu điểm là kết cấu tinh gọn có thể di chuyển dễ dàng trên các công trường, có tính ứng dụng cao, giá thành thấp và dễ dàng vận hành. Từ đó, có thể ứng dụng được trong các nhà xưởng hay các cơ sở gia công cơ khí trong việc hàn và cắt. Abstract - In mechanical processing, the cutting of long steel pipe billets into short steel pipe billets or the welding of short steel pipe billets, ... are frequent activities. To ensure the accuracy of required sizes, shapes, ... as well as high productivity, it is necessary to use fixtures. The aim of this paper is to design and to manufacture automatic welding and cutting fixtures for steel pipes with medium power. The result of this research shows that the completed fixtures work reliably and the products made with these fixtures have high quality. Besides, the advantages of these fixtures are their compact structures, which results in their mobility in construction sites, high applicability, low cost and easy operation. These fixtures can be employed in factories or mechanical processing facilities for welding and cutting. Từ khóa - Đồ gá; hàn cắt; ống thép; thiết kế; chế tạo. Key words - Fixtures; welding and cutting; steel pipes; designing; manufacturing. 1. Đặt vấn đề Đồ gá trong gia công cơ khí có vai trò quan trọng đến sự hình thành chất lượng của sản phẩm trong quá trình sản xuất sản phẩm. Trong nhóm các đồ gá, đồ gá hàn – cắt có kết cấu đơn giản hơn đồ gá gia công. Chính vì vậy, nhiều chuyên gia đối với loại đồ gá này đã tiến hành nghiên cứu thiết kế để góp phần nâng cao chất lượng sản phẩm [1,2]. Hiện nay, trên thị trường nước ta đã xuất hiện nhiều chủng loại đồ gá cho việc hàn và cắt các chi tiết dạng ống, có thể kể đến đồ gá hàn ống sê-ri ZT [3] với công suất lớn, khả năng tải từ 5 – 40 tấn, đồ gá này có khả năng tự lựa theo đường kính ống, bốn bánh của cụm chủ động đều được dẫn động bằng 2 bộ động cơ-giảm tốc, bánh thép được gắn cao su nên khả năng tải cao và ổn định trong quá trình làm việc, điều chỉnh vô cấp với dải điều chỉnh rộng và độ chính xác cao, áp dụng đối với các chi tiết có đường kính lớn từ 600 – 5200 mm, tuy nhiên đồ gá cồng kềnh khó di chuyển trên các công trường và giá thành đắt; hoặc nhóm đồ gá quay Positoner HB [4] với công suất nhỏ hơn, khả năng tải dưới 300 kg, đồ gá có ưu điểm tháo lắp nhanh và vận hành chính xác, mâm gá có thể quay linh hoạt với nhiều góc độ khác nhau, kết cấu gọn dễ dàng di chuyển trên công trường, áp dụng cho các chi tiết ống có đường kính tối đa 300 mm, tuy nhiên do công suất nhỏ nhóm đồ gá này không áp dụng được với các ống có kích thước lớn hơn. Trong khi đó, đối với phân khúc công suất vừa, việc xuất hiện chủng loại đồ gá hàn và cắt cho chi tiết ống có đường kính 300 – 600mm còn khá ít. Chính vì vậy, bài báo đã tiến hành nghiên cứu thiết kế và chế tạo đồ gá hàn và cắt tự động cho các ống thép với công suất vừa. Đồ gá sau khi được chế tạo hoàn chỉnh đã làm việc tin cậy, tinh gọn có thể di chuyển linh hoạt trên các công trường, có thể ứng dụng được trong các nhà xưởng hay các cơ sở gia công cơ khí trong việc hàn và cắt. 2. Nội dung nghiên cứu 2.1. Lựa chọn các bộ phận chính của đồ gá Trên cơ sở phạm vi nghiên cứu, yêu cầu đặt ra là thực hiện hàn hoặc cắt một chi tiết ống có thông số kích thước kỹ thuật như sau: - Chiều dài: Lmax = 6000 mm; - Đường kính lớn nhất: Dmax = 600 mm; - Đường kính nhỏ nhất: Dmin = 200 mm; - Chiều dày: Smax = 16 mm; - Khối lượng: Pmax = 1420 Kg. 2.1.1. Lựa chọn phương án xoay và kẹp ống Đối với các loại chi tiết ống có kích thước như yêu cầu đặt ra thì việc thực hiện mối hàn hoặc cắt ngang bằng cách quay ống nhờ nguồn dẫn động trực tiếp từ động cơ điều tốc sẽ giúp giảm rung động do vận tốc quay thấp (vlv) như thể hiện trong Hình 1, ống được gá kẹp trực tiếp từ mâm kẹp tự định tâm trong quá trình chuyển động quay sẽ đồng tâm, điều này dẫn đến việc duy trì khoảng hở hồ quang hoặc khoảng cách đầu mỏ cắt tới bề mặt hàn, cắt luôn được giữ đúng cự ly vì thế mà thực hiện chế độ hàn, cắt ổn định hơn. Như vậy khi lựa chọn phương án này giúp cho khả năng nâng cao chất lượng đường hàn hay đường cắt được luôn được đảm bảo. Sử dụng phương án này kết cấu trở nên đơn giản, gọn, dễ cơ động trong di chuyển vị trí làm việc. Hình 1. Phương án xoay ống 1-Động cơ; 2- Hộp giảm tốc; 3-Cơ cấu kẹp; 4- Chi tiết ống ISSN 1859-1531 - TẠP CHÍ KHOA HỌC VÀ CÔNG NGHỆ ĐẠI HỌC ĐÀ NẴNG, SỐ 11(132).2018, QUYỂN 2 11 Ngoài ra với phương án này dễ dàng thiết lập thêm phương án quay mâm kẹp chi tiết hàn, cắt ở nhiều góc độ khác nhau làm tăng thêm khả năng làm việc của đồ gá như hàn, cắt chi tiết ở nhiều vị trí nằm trong khoảng từ 0o ÷ 90o. Với các chi tiết ống có đường kính nằm trong khoảng từ 200 ÷ 600mm có nhiều phương án kẹp, song để gá kẹp cũng như tháo phôi được nhanh chóng, đồng thời có thể sử dụng dễ dàng, dễ tìm kiếm trên thị trường thì lựa chọn phương án gá kẹp bằng mâm kẹp 3 chấu tự định tâm [6] sẽ trở nên phù hợp hơn hết, như thể hiện trong Hình 2. Hình 2. Mâm cặp 3 chấu 2.1.2. Lựa chọn hệ truyền động làm việc chính Việc thiết kế bộ truyền cho đồ gá phải đảm bảo một số yêu cầu đặt ra như: + Kết cấu chung của toàn đồ gá phải gọn. + Khi truyền chuyển động làm việc phải êm, không rung chấn. + Bộ truyền phải thay đổi góc độ làm việc đồng thời với mâm kẹp chi tiết để thực hiện các góc độ hàn, cắt từ 0o ÷ 90o. + Đáp ứng vận tốc đầu ra làm việc của mâm kẹp (vlv = 0,1 ÷ 1m/ph). Như vậy, để đáp ứng được các yêu cầu đặt ra, nhận thấy sự cần thiết phải sử dụng động cơ giảm tốc để thiết lập nguồn động lực làm việc của đồ gá. Trong phạm vi của đề tài, công suất của động cơ dùng để truyền momen xoắn cho mâm cặp và ống thép. Ta có công suất cần thiết được tính theo công thức: t ct P P = (1) Với Pct: công suất cần thiết trên trục. Pt: Công suất tính toán trên trục máy công tác. : Hiệu suất chung (= 0,75). Công suất tính toán trên trục công tác được tính theo công thức: . 1000 tt lv F v P P= = (2) Trong đó: F - là trọng lượng của mâm kẹp và ống (N) F = (Mống + Mmâmkẹp).g = (1420 + 40).9,8 = 14310 (N) v - vận tốc dài của ống (m/s) . . 3,14.600.2,5 0,0785( / ) 60.1000 60.1000 D n v m s = = = Do đó: 14310.0,0785 1,12(Kw) 1000 lv P = = Như vậy: 1,15 1,5( ) 0,75 ct P Kw= = Chọn động cơ kí hiệu DK42-6 với Nđc = 1,7(Kw) và số vòng quay nđc = 925 vg/ph [5]. Bên cạnh đó, tốc độ làm việc của mâm kẹp lại nhỏ dẫn đến tỷ số truyền chung của hộp giảm tốc là uchung = ndc/nlv= 925/2,5 = 370. Đối với động cơ giảm tốc với tỷ số truyền lớn, có thể sử dụng nhiều biện pháp để giảm tốc, chẳng hạn sử dụng bộ giảm tốc bánh răng hành tinh nhiều cấp hoặc cũng có thể sử dụng bộ giảm tốc bánh răng Cycloid (bộ truyền bánh răng con lăn). Trong phần này, tác giả đề xuất biện pháp sử dụng bộ truyền bánh răng cycloid vì đặc điểm ăn khớp của loại bộ truyền này không có khe hở cạnh răng nên làm việc êm, không gây va chạm khi đổi chiều quay, bộ truyền bánh răng Cycloid có kết cấu nhỏ gọn, trọng lượng nhẹ, tỷ số truyền lớn, hiệu suất truyền động cao, khả năng tải lớn, tâm trục ra và tâm trục vào đều nằm trên một đường thẳng (đồng trục),Với tỷ số truyền lớn như vậy, tiến hành thiết kế hộp giảm tốc bánh răng cycloid 2 cấp như thể hiện trong Hình 3. Phân phối tỷ số truyền cho cấp nhanh và cấp chậm: 370 19 nh ch i i= = = Với mục đích giảm thiểu việc chế tạo nhiều bánh răng cycloid có kích thước khác nhau, đồng thời mang lại kết cấu nhỏ gọn cho hộp giảm tốc, tác giả tiến hành thiết kế bộ truyền bánh răng cycloid cấp nhanh và cấp chậm có kích thước giống nhau. Hình 3. Sơ đồ nguyên lý truyền động làm việc chính 1-Động cơ; 2-Bánh răng cycloid; 3-Vành răng chốt; 4-Mâm kẹp Dựa trên số liệu ban đầu, thông qua các công thức tính toán, ta được các thông số của bộ truyền như thể hiện trong Bảng 1 và Bảng 2. Bảng 1. Thông số cơ bản của bộ truyền bánh răng Cycloid (mm) Số răng zc Độ lệch tâm a Bán kính vòng tròn qua tâm các con lăn của vành răng chốt rp Đường kính của con lăn trên vành răng chốt drp Đường kính chốt trên vành răng chốt dsp Bề rộng bánh răng cycloid b 19 4 150 26 20 15 Bảng 2. Thông số hình học của bánh răng Cycloid (mm) Đường kính vòng chân bánh răng cycloid dfc Đường kính vòng đỉnh bánh răng cycloid dac Chiều cao răng h Đường kính vòng tròn qua tâm các lỗ chốt ra Dw Đường kính chốt ra dsw Đường kính con lăn chốt ra drw Đường kính lỗ chốt ra dw 230 246 8 145 16 30 38 2.1.3. Lựa chọn bộ truyền động điều khiển góc quay cụm công tác Trong thực tế khi gia công hàn, cắt chúng ta thường gặp các chi tiết dạng ống hoặc một số các chi tiết có biên dạng hình tròn như mặt bích, bánh đà Xuất phát từ yêu cầu đặc thù trong gia công, chế tạo một số chi tiết có thể thực hiện việc hàn, cắt theo phương nằm ngang cũng có một số chi tiết phải thực hiện theo phương thẳng đứng hoặc một 12 Nguyễn Văn Chương, Nguyễn Thái Dương, Lưu Đức Bình, Đinh Minh Diệm góc bất kỳ náo đó trong phạm vi từ 0o÷90o. Phạm vi của bài báo đi sâu nghiên cứu và tạo ra đồ gá có tính tích hợp để thực hiện hàn, cắt các chi tiết ở nhiều vị trí khác nhau nhằm đáp ứng một số yêu cầu đặt ra như đã nêu ở trên, như thể hiện trong Hình 4. Hình 4. Các góc độ làm việc của cơ cấu công tác a) Hàn góc ở vị trí bằng theo phương ngang; b) Cắt bằng ống theo phương ngang; c) Hàn góc ở vị trí bằng theo phương nghiêng 45o; d) Hàn góc ở vị trí bằng theo phương đứng; e) Cắt ở vị trí bằng theo phương đứng Nhận thấy phương án điều khiển góc quay thông qua motor giảm tốc có sử dụng phanh từ là phù hợp với đặc điểm, kết cấu và nguyên lý làm việc chung của đồ gá. Bên cạnh đó, với đặc thù trục công tác nằm vuông góc với trục động cơ, kết hợp tốc độ đầu ra nhỏ, nên trong phần thiết kế cơ cấu điều khiển góc quay của trục công tác, ta chọn hộp giảm tốc mang bộ truyền bánh răng cycloid – kết hợp bộ truyền bánh răng nón như thể hiện trong Hình 5. Hình 5. Sơ đồ nguyên lý truyền động điều khiển góc quay 1-Động cơ; 2-Bánh răng cycloid; 3-Vành răng chốt; 4-Bánh răng côn Dựa theo số liệu ban đầu, tính chọn động cơ kí hiệu DK51-6 với Nđc = 2,8(kw) và số vòng quay nđc = 950 vg/ph [5]. Bên cạnh đó, tính được các thông số hình học của các bộ truyền bánh răng cycloid cấp nhanh như thể hiện trong Bảng 3 và Bảng 4. Bảng 3. Thông số cơ bản của bộ truyền bánh răng Cycloid (mm) Số răng zc Độ lệch tâm a Bán kính vòng tròn qua tâm các con lăn của vành răng chốt rp Đường kính của con lăn trên vành răng chốt drp Đường kính chốt trên vành răng chốt dsp Bề rộng bánh răng cycloid b 31 2 80 16 8 8 Bảng 4. Thông số hình học của bánh răng Cycloid (mm) Đường kính vòng chân bánh răng cycloid dfc Đường kính vòng đỉnh bánh răng cycloid dac Chiều cao răng h Đường kính vòng tròn qua tâm các lỗ chốt ra Dw Đường kính chốt ra dsw Đường kính con lăn chốt ra drw Đường kính lỗ chốt ra dw 140 148 4 90 10 20 24 Đồng thời, sau khi tính toán thu được thông số của bộ truyền bánh răng nón cấp chậm như sau: + Mô đun mặt nón lăn: ms = 1,5 mm + Chiều dài nón: L = 75 mm + Góc ăn khớp: o20= + Góc mặt nón lăn (nón chia): 1= 15o; 2 = 74o + Đường kính vòng lăn (vòng chia): d1 = 33 mm; d2 = 165mm + Đường kính vòng đỉnh: De1 = 36 mm; De2 = 166 mm 2.2. Lựa chọn phương án điều chỉnh vô cấp tốc độ động cơ Sự khác biệt giữa đồ gá hàn, cắt các chi tiết dạng ống so với các loại đồ gá hàn, cắt các chi tiết theo đường thẳng trên cùng mặt phẳng ở chổ: các chi tiết có thể có sự khác nhau về kích thước đường kính. Vậy nên khi thực hiện việc hàn, cắt mỗi chi tiết thì tương ứng với đó là có sự thay đổi về vận tốc quay của cơ cấu công tác. Nếu như xét trong điều kiện khi hàn, cắt một chi tiết nào đó có cùng chiều dày, nhưng khác nhau về đường kính, trong trường hợp này thì chi tiết nào có đường kính càng lớn thì vận tốc quay càng nhỏ và ngược lại. Vận tốc hàn, cắt được quy ước là (m/ph; mm/ph). Hình 6. Biến tần Invt Goodrive 10 Như vậy đối với các loại động cơ giảm tốc việc tính toán chọn công suất động cơ cũng như vận tốc đầu ra chỉ được thực hiện một lần. Nếu như tỉ số truyền càng lớn điều đó cũng đồng nghĩa với việc kích thước và khối lượng chung của động cơ sẽ tăng lên, giá thành đầu tư sẽ cao. Mặt khác vận tốc đầu ra cũng chỉ cố đinh ở một giá trị. Trên cơ sở những phương pháp giảm tốc độ động cơ đã đề cập ở trên. Để đáp ứng yêu cầu nhiệm vụ của đề tài đặt ra thì phương pháp thay đổi tốc độ động cơ thông qua việc thay đổi tần số vẫn là giải pháp có nhiều tính năng ưu việt hơn cả, như thể hiện trong Hình 6. Điểm đặc biệt nhất của hệ truyền động biến tần - động cơ là có thể điều chỉnh vô cấp tốc độ động cơ. Tức là thông qua việc điều chỉnh tần số và có thể điều chỉnh tốc độ động ISSN 1859-1531 - TẠP CHÍ KHOA HỌC VÀ CÔNG NGHỆ ĐẠI HỌC ĐÀ NẴNG, SỐ 11(132).2018, QUYỂN 2 13 cơ thay đổi theo ý muốn trong một dải rộng. Sử dụng biến tần, cũng có nghĩa là mặc nhiên được hưởng rất nhiều các tính năng thông minh, linh hoạt như là tự động nhận dạng động cơ; tính năng điều khiển thông qua mạng; có thể thiết lập được 16 cấp tốc độ; khống chế dòng khởi động động cơ giúp quá trình khởi động êm ái (mềm) nâng cao độ bền kết cấu cơ khí; giảm thiểu chi phí lắp đặt, bảo trì; tiết kiệm không gian lắp đặt; các chế độ tiết kiệm năng lượng, Khi sử dụng biến tần sẽ không còn những nỗi lo về việc không làm chủ, khống chế được năng lượng quá trình truyền động bởi vì chúng ta có thể kiểm soát được nó thông qua các chế độ bảo vệ quá tải, quá nhiệt, quá dòng, quá áp, thấp áp, lỗi mất pha, lệch pha của biến tần. 3. Kết quả và thảo luận 3.1. Mô hình thực nghiệm đồ gá hàn, cắt Hình 7. Mô hình thực nghiệm Hình 8. Kết cấu các bộ truyền động a. Bộ truyền động làm việc chính; b. Bộ truyền động điều khiển góc quay Sau khi gia công các chi tiết chính của thiết bị, tiến hành lắp ráp thu được kết cấu đồ gá như thể hiện trong Hình 7 và Hình 8. Đồ gá sau khi lắp ráp xong, có thể gá chi tiết tại nhiều góc độ khác nhau, cho thấy sự chắc chắn của mô hình thực nghiệm, như thể hiện trong Hình 9. Hình 9. Các góc độ làm việc thiết bị 3.2. Vận hành thực nghiệm 3.2.1. Hàn liên kết mặt bích - ống Hình 10. Hàn liên kết mặt bích - ống a. Vị trí 450; b. Vị trí 900 Hình 11. Sản phẩm sau khi hàn Với việc khi hàn ở vị trí 450, kim loại que hàn sẽ có xu hướng chảy dốc xuống vũng hàn tạo cho mối hàn có chất lượng tốt nhất (độ sâu ngấu được đồng đều) so với khi hàn tại các góc độ khác, như thể hiện trong Hình 10 và Hình 11. Ngoài ra, thiết bị hàn dễ dàng xoay được nhiều vị trí khác nhau sẽ thuận lợi hơn cho việc hàn các đối tượng vật liệu khác nhau (khối lượng, hình dạng, kết cấu). 3.2.2. Cắt ống Hình 12. Cắt ống Hình 13. Sản phẩm cắt thủ công (a) và cắt tự động (b) Thiết bị làm việc với tốc độ vô cấp, dễ dàng lựa chọn phương án cắt tùy thuộc vào đường kính cũng như chiều dày chi tiết, tạo nên sự nổi bật của thiết bị gá trong việc cắt tự động, như thể hiện trong Hình 12. Bằng mắt thường, có thể quan sát thấy sản phẩm sau khi được cắt tự động có được chất lượng tốt (đường cắt đều) như thể hiện trong Hình 13. Bên cạnh đó, tốc độ cắt ổn định hơn so với việc cắt thủ công thông thường hiện nay. 4. Kết luận Qua khảo sát thực tế trên thị trường, phân tích đặc điểm và phạm vi ứng dụng của các chủng loại đồ gá hàn cắt các a) b) 14 Nguyễn Văn Chương, Nguyễn Thái Dương, Lưu Đức Bình, Đinh Minh Diệm chi tiết dạng ống, bài báo đã đề xuất một đồ gá mới để có thể phục vụ cho việc hàn, cắt tự động ứng với công suất vừa. Sau khi lựa chọn và tính toán các thông số hình học của các bộ phận chính của máy, tiến hành gia công và lắp ráp đã cho ra mô hình thực nghiệm của đồ gá mới này. Đồ gá chế tạo đã làm việc có độ tin cậy cao, các sản phẩm được tạo ra nhờ sự hỗ trợ của thiết bị này có chất lượng cao, kết cấu máy tinh gọn có thể di chuyển dễ dàng trên các công trường, có tính ứng dụng cao, giá thành thấp và dễ dàng vận hành. Từ đó, có thể đưa vào sử dụng tại các cơ sở hay phân xưởng gia công cơ khí trong lĩnh vực hàn cắt chi tiết dạng ống với công suất tầm trung. Lời cảm ơn Nghiên cứu này được tài trợ bởi Quỹ phát triển tiềm lực Khoa học Công nghệ của Trường Đại học Sư phạm Kỹ thuật - Đại học Đà Nẵng trong đề tài có mã số T2018-06-98. TÀI LIỆU THAM KHẢO [1] Shinde S.N., Kshirsagar S., Patil A., Parge T. and Lomte R. , “Design of Welding Fixtures and Positiners”, International Journal of Engineering Research and General Science, Volume 2, Issue 5, 2014, pp 681-689. [2] Naveen A.M., Girisha V.A. and Pruthvi H. M. , “Design and analysis of welding fixture for motor case assembly”, International Journal of Mechanical And Production Engineering, Volume 2, Issue 8, 2014, pp 54-59. [3] https://vegatec.com.vn/san-pham/do-ga-han-ong-seri-zt-265/ [4] [5] Nguyễn Trọng Hiệp, Nguyễn Văn Lẫm, Thiết kế chi tiết máy, Nhà xuất bản giáo dục, 2007. [6] chau-tu-dinh-tam-may-tien-90.html [7] https://vi.wikipedia.org/wiki/Biến_tần (BBT nhận bài: 18/8/2018, hoàn tất thủ tục phản biện: 17/10/2018)
File đính kèm:
thiet_ke_va_che_tao_do_ga_han_cat_tu_dong_thep_ong_cong_suat.pdf