Giáo trình Truyền động cơ khí (Phần 2)
ưu, nhược điểm:
1. Ưu điểm:
- Có thể truyền chuyển động giữa các trục khá xa nhau (Amax = 8 m).
- Khả năng tải cao hơn đai.
- Hiệu suất truyền động cao hơn so với đai, đạt = 0.96 0.98.
- Lực tác dụng lên trục nhỏ hơn so với truyền động đai vì lực căng ban đầu
không lớn.
- Có thể truyền chuyển động và công suất cùng một lúc đến nhiều trục.
- Không xảy ra sự trượt nên tỉ số truyền i không đổi.
- Kích thước nhỏ so với truyền động đai.
2. Nhược điểm:
- Giá thành tương đối cao vì kết cấu phức tạp.
- Có nhiều tiếng ồn khi làm việc.
- Vận tốc tức thời của xích và đĩa bị dẫn thay đổi theo thời gian (không ổn định).
- Yêu cầu chăm sóc thường xuyên (bôi trơn, ) và phức tạp hơn so với bộ
truyền đai.
- Chóng bị mòn khi làm việc nơi nhiều bụi và bôi trơn không tốt.
Tóm tắt nội dung tài liệu: Giáo trình Truyền động cơ khí (Phần 2)
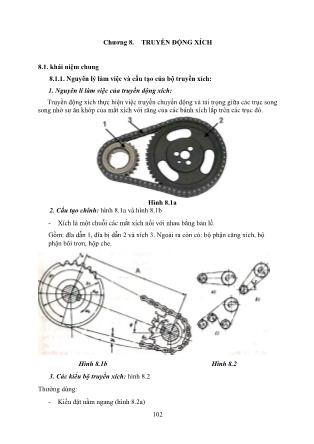
102 Chƣơng 8. TRUYỀN ĐỘNG XÍCH 8.1. khái niệm chung 8.1.1. Nguyên lý làm việc và cấu tạo của bộ truyền xích: 1. Nguyên lí làm việc của truyền động xích: Truyền động xích thực hiện việc truyền chuyển động và tải trọng giữa các trục song song nhờ sự ăn khớp của mắt xích với răng của các bánh xích lắp trên các trục đó. Hình 8.1a 2. Cấu tạo chính: hình 8.1a và hình 8.1b - Xích là một chuỗi các mắt xích nối với nhau bằng bản lề. Gồm: đĩa dẫn 1, đĩa bị dẫn 2 và xích 3. Ngoài ra còn có: bộ phận căng xích, bộ phận bôi trơn, hộp che. Hình 8.1b Hình 8.2 3. Các kiểu bộ truyền xích: hình 8.2 Thƣờng dùng: - Kiểu đặt nằm ngang (hình 8.2a) 103 - Kiểu đặt nằm nghiêng (hình 8.2b) - Kiểu đặt thẳng đứng Thông thƣờng bộ truyền xích có 1 trục dẫn và 1 trục bị dẫn, nhƣng đôi khi có nhiều trục bị dẫn (nhƣ hình 8.2c) 8.1.2. Ƣu, nhƣợc điểm: 1. Ưu điểm: - Có thể truyền chuyển động giữa các trục khá xa nhau (Amax = 8 m). - Khả năng tải cao hơn đai. - Hiệu suất truyền động cao hơn so với đai, đạt = 0.96 0.98. - Lực tác dụng lên trục nhỏ hơn so với truyền động đai vì lực căng ban đầu không lớn. - Có thể truyền chuyển động và công suất cùng một lúc đến nhiều trục. - Không xảy ra sự trƣợt nên tỉ số truyền i không đổi. - Kích thƣớc nhỏ so với truyền động đai. 2. Nhược điểm: - Giá thành tƣơng đối cao vì kết cấu phức tạp. - Có nhiều tiếng ồn khi làm việc. - Vận tốc tức thời của xích và đĩa bị dẫn thay đổi theo thời gian (không ổn định). - Yêu cầu chăm sóc thƣờng xuyên (bôi trơn, ) và phức tạp hơn so với bộ truyền đai. - Chóng bị mòn khi làm việc nơi nhiều bụi và bôi trơn không tốt. 8.1.3. Phạm vi ứng dụng: - Truyền chuyển động giữa các trục song song dùng đƣợc với khoảng cách trục A 8 m. - Truyền động xích đƣợc dùng rộng rãi trong máy nông nghiệp và máy vận chuyển (xe đạp, xe máy, ), trong máy công cụ và tay máy công nghiệp .v.v.., với công suất nhỏ và trung bình (N 18 kW), tốc độ xích đến 15 m/s và tỉ số truyền đến i= 8. 8.2. Bộ truyền xích 8.2.1. Các loại xích truyền động: 1. Xích con lăn (còn gọi là xích ống con lăn): 104 - Đƣợc sử dụng rộng rãi, thƣờng dùng trong các bộ truyền làm việc quay 2 chiều, có va đập, hay gặp có ở các máy xây dựng, máy làm đƣờng. - Cấu tạo: Xích con lăn một dãy (hình 8.3) sau: pc b0 1 2 3 4 5 6 Hình 8.3Cấu tạo mắc xích 1-má xích trong; 2-má xích ngoài; 3-ống; 4-chốt; 5-con lăn (đƣợc lồng tự do với ống 3 Gồm: má xích (trong và ngoài): 1 và 2 chốt 4+ má xích ngoài: mắt xích ngoài ống 3+ má trong: mắt xích trong 2. Xích ống: hình 8.4 - Nếu bỏ con lăn của xích con lăn trên thì đó là cấu tạo của xích ống. - Do không có con lăn nên xích ống và răng đĩa xích ăn khớp với nó cũng chóng mòn hơn. Hình 8.4 Cấu tạo xích ống một dãy - Ít sử dụng hơn, đƣợc dùng trong máy vận chuyển loại nhẹ. 3. Xích răng: - So với xích con lăn, nó chịu tải cao hơn, làm việc ổn định và ít ồn hơn. 105 - Giá thành cao và ít đƣợc sử dụng. - Cấu tạo nhƣ hình 8.5 sau: Má xích + miếng lót = mắt xích. Hình 8.5 8.2.2. Vật liệu chế tạo xích: - Má xích thƣờng làm bằng thép cán nguội có hàm lƣợng cacbon trung bình (thép 45, 50 ) hoặc thép hợp kim cán nguội (40X, 40XH, ). - Vật liệu làm bản lề (chốt, ống, con lăn) thƣờng là thép cacbon hoặc thép hợp kim thấp: 15, 20, 15X, 20X, 8.2.3. Đĩa xích: 1. Cấu tạo: hình 8.6 Đĩa xích có hình dạng giống bánh răng. Hình dạng kích thƣớc profin răng đƣợc qui định theo tiêu chuẩn. Hình 8.6 - B: chiều rộng xích - h: chiều cao răng xích. - d: đƣờng kính vòng chia 106 - de: đƣờng kính vòng đỉnh - di: đƣờng kính vòng chân - Z: số răng đĩa xích 2. Vật liệu chế tạo đĩa xích: - Đĩa xích chịu tải trọng nhỏ, không có va đập (từ bên ngoài) và vận tốc v<3 m/s : thì chế tạo bằng gang CЧ21- 40 hoặc gang xám có độ bền cao hơn. - Với tải trọng và vận tốc lớn hơn dùng thép cacbon hoặc thép hợp kim nhƣ thép: 40, 40X, 40X, - Đĩa xích có đƣờng kính trên 200 mm nên chế tạo ghép: vành ngoài bằng thép, thân đĩa bằng gang. 8.3. Những thông số chính của bộ truyền 8.3.1. Bƣớc xích : t (mm) - Đây là thông số và đƣợc tiêu chuẩn hoá. - Chọn xích lấy t theo dãy số tiêu chuẩn, tra bảng (8.1). - Khi làm việc ở vận tốc cao nên chọn t nhỏ, cần thiết thì tăng số dãy xích (với xích con lăn) hoặc tăng chiều rộng xích (với xích răng). Trị số lớn nhất của bước xích và số vòng quay giới hạn n1g (vg/ph) của đĩa xích dẫn Z1 Bảng 8.1 Z1 n1g (vg/ph), khi bƣớc xích t, mm 12 15 20 25 30 40 45 50 (12,7) (15,875) (19,05) (25,4) (31,75) (38,1) (44,45) (50,8) Xích con lăn 20 2780 2000 1520 800 725 540 430 350 25 2900 2070 1580 830 750 560 445 365 30 3000 2150 1640 870 780 580 460 375 Xích răng 17 - 35 3300 2650 2200 1650 1300 - - - 8.3.2. Đƣờng kính đĩa xích : d (mm) (còn gọi là đường kính vòng chia của đĩa xích). Hình 8.7. 107 - Đĩa xích cấu tạo giống bánh răng, khi xích và răng đĩa ăn khớp nhau thì tâm các bản lề nằm trên vòng chia của đĩa xích nên đƣờng kính d đƣợc tính theo nhƣ sau: 1. Đường kính vòng chia của đĩa dẫn d1: d1 = 1 sin Z t (8-1) Trong đó: t - bƣớc xích (mm) Z1- số răng đĩa dẫn (răng) 2. Đường kính vòng chia của đĩa bị dẫn d2: d2 = 2 sin Z t (8-2) Trong đó: Z2 – số răng đĩa bị dẫn. 8.3.3. Số răng đĩa xích Z (răng): Thông thƣờng bộ truyền xích đƣợc dùng trong hộp giảm tốc nên số răng đĩa dẫn Z1 nhỏ hơn đĩa bị dẫn Z2 . 1. Số răng đĩa dẫn Z1 : tra theo bảng 8.2 Bảng 8.2 Bảng hướng dẫn chọn số răng đĩa xích dẫn Z1 Loại xích Tỷ số truyền i 1 - 2 2 - 3 3 - 4 4 - 5 5 - 6 6 Số răng Z1 Xích ống con lăn 30 - 27 27 - 25 25 - 23 23 - 21 21 - 17 17 – 15 Xích răng 35 - 32 32 - 30 30 - 27 27 - 23 23 - 19 19 - 17 Chọn Z1 theo Z1 min và góc xoay của bản lề không lớn quá. Z1 Z1 min (8-3) - Z1 min 19 khi v 2 m/s - Z1 min = 13 15 khi v 2 m/s 2. Số răng đĩa bị dẫn Z2: Tính theo công thức sau: Z2 = i. Z1 Z2 max (8-4) 108 - Z2 max 80 120: đối với xích con lăn. - Z2 max 120 140: đối với xích răng. Có sự giới hạn số răng đĩa bị dẫn Z2 là do sau một thời gian làm việc xích sẽ bị mòn và bƣớc xích sẽ tăng thêm một lƣợng t, khi đó đƣờng kính vòng chia sẽ tăng một trị số là d nhƣ hình vẽ: hình 8.7. Theo công thức : d = Z t sin (8-5) Hình 8.7 8.3.4. Khoảng cách trục A (mm): Chọn A: Amin A Amax (8-6) 1. Khoảng cách trục nhỏ nhất Amin : Đƣợc qui định theo hai điều kiện sau: + Góc ôm trên đĩa dẫn 1 120 o thì Amin d2 – d1 + Để hai đĩa xích không chạm vào nhau thì: Amin 0,5 (de1 + de2) + (30 50) (8-7) Trong đó: de1, de2: là đƣờng kính vòng đỉnh răng của đĩa xích dẫn và bị dẫn. Đối với xích con lăn: de = t(cotg /Z + (0,5 0,6)). Đối với xích răng : de = t. cotg /Z. 2. Khoảng cách trục lớn nhất Amax : Đƣợc giới hạn theo công thức: Amax 80. t (8-8) Để dung hoà hai giới hạn trên người ta thường tính A theo công thức sau: A = (30 50)t (8-9) 109 8.3.5. Số mắt xích X: Khi đã chọn đƣợc khoảng cách trục A, ta tính số mắt xích X theo công thức sau: X t A.2 + 0,5(Z1 + Z2) + 0,25 (Z2 Z1) 2 . 2.A t (8 8) X: phải đƣợc lấy tròn và là số chẳn 8.3.6. Chiều dài xích L(mm): Tính theo công thức: L = X.t (8 11) Trong đó: X số mắt xích, t bƣớc xích. 8.4. Tính toán truyền động xích 8.4.1. Các dạng hỏng: - Mòn bản lề: làm bƣớc xích tăng lên, xích ăn khớp không chính xác với răng đĩa. Nên bản lề bị mòn nhiều, xích thƣờng xuyên bị trƣợt ra khỏi đĩa hoặc có thể bị đứt. Để giảm mòn cần bôi trơn xích và hạn chế áp suất trong bản lề xích. - Xích đứt vì mỏi: xảy ra đối với các bộ truyền kín, vận tốc cao, tải lớn (ít gặp) dẫn đến. - Ngoài ra, con lăn bị rỗ hoặc vỡ, răng đĩa xích bị mòn hoặc do chế tạo không tốt, chốt và ống có thể bị long ra. - Trong các dạng hỏng kể trên, mòn bản lề là dạng chủc yếu nên tính xích về mòn là tính toán cơ bản để thiết kế bộ truyền xích. Mặt khác va đập cũng ảnh hƣởng đến tuổi thọ và sự làm việc của bộ truyền, cũng thƣờng tiến hành kiểm nghiệm số lần va đập của một mắt xích trong 1 giây. 8.4.2. Tính xích theo áp suất cho phép : - Điều kiện để xích làm việc trong 1 khoảng thời gian tƣơng đối lớn (20003000 giờ) là áp suất sinh ra trong bản lề phải nhỏ hơn áp suất cho phép [p] p = p kS Fk x t . . (8-12) Trong đó: -Ft : lực vòng -S = d0. b0 : diện tích tính toán của bản lề xích một dãy (d0-đƣờng kính chốt, b0- chiều dài ống). Có thể lấy :S = 0,28. t2 (8-13) -k: hệ số điều kiện sử dụng xích. k = kđ. ka.k0. kđc. kb (8-14) 110 kđ: hệ số tải trọng động, nếu dẫn động bằng động cơ điện và tải trọng ngoài tác dụng lên bộ truyền tƣơng đối êm kđ= 1, Nếu tải trọng có va đập kđ = 1,2 1,5 Nếu va đập mạnh kđ = 1,8 ka: hệ số xét đến chiều dài xích , xích càng dài thì số lần vào khớp của mỗi mắt xích trong một đơn vị thời gian càng ít, xích sẽ ít mòn hơn. A = (30 50). t ka=1 A< 25.t ka = 1,25 A = ( 60 80). t ka = 0,8 k0: xét đến cách bố trí bộ truyền: Nếu bố trí bộ truyền nằm ngang 1 góc < 600 thì k0= 1. Nếu bố trí bộ truyền nằm ngang 1 góc > 600 thì k0= 1,25. kđc: hệ số xét đến khả năng điều chỉnh bộ căng xích: Nếu trục có thể điều chỉnh đƣợc kđc=1. Nếu dùng đĩa căng xích loại con lăn căng xích kđc=1,1. Nếu trục không điều chỉnh đƣợc kđc = 1,25. kb: hệ số xét đến điều kiện bôi trơn: Nếu bôi trơn liên tục kb= 0,8. Nếu bôi trơn nhỏ giọt kb= 1. Nếu bôi trơn định kỳ kb= 1,5. kx: hệ số xét đến số dây xích. Với x = 1, 2, 3, 4 kx= 1 - 1,7 - 2,5 - 3 Trị số [p] cho theo bảng (8.3) Bảng 8.3 Áp suất cho phép [p] về bền mòn của xích t, mm [p], Mpa, khi n1, vg/ph < 50 200 400 600 800 800 1200 1600 2800 Xích con lăn 12,7 - 15,875 35 31,5 28,5 26 24 22,5 21 18,5 14 19,05 - 25,4 35 30 26 23,5 21 19 17,5 15 - 31,75 - 38,1 35 29 24 21 18,5 16,5 15 - - 111 44,45 - 50,8 35 26 21 17,5 15 - - - - Xích răng 12,7 - 15,875 20 18 16,5 15 14 13 12 8,5 8 19,05 – 25,4 20 17 15 13 12 11 8 8,5 - 31,75 20 16,5 14 12 8,5 9,5 7 - - Trị số công suất cho phép [N], kW, của bộ truyền xích (với Z01 = 25) Bảng 8.4 Cỡ xích Bƣớc xích t, mm [N], kW, khi số vòng quay đĩa nhỏ n01 ,vg/ph 50 200 400 600 800 800 1200 1600 Xích con lăn 1 dãy P 12,7 -9000-2 12,7 0,19 0,68 1,23 1,68 2,06 2,42 2,72 3,20 P 12,7 –18000-1 12,7 0,35 1,27 2,29 3,13 3,86 4,52 5,06 5,95 P 12,7–18000-2* 12,7 0,45 1,61 2,91 3,98 4,90 5,74 6,43 7,55 P 12,875-23000-1 15,875 0,57 2,06 3,72 5,08 6,26 7,34 8,22 9,65 P 12,875-23000-2* 15,875 0,75 2,70 4,88 6,67 8,22 9,63 8,8 12,7 P 19,05 -32000* 19,05 1,41 4,80 8,38 11,4 13,5 15,3 16,9 19,3 P 25,4 -56700* 25,4 3,20 11,0 19,0 25,7 30,7 34,7 38,3 43,8 P 31,75 -88500* 31,75 5,83 19,3 32,0 42,0 49,3 54,9 60,0 - P 38,1 -127000* 38,1 8,5 34,8 57,7 75,7 88,9 99,2 88 - P 44,45-172400* 44,45 14,7 43,7 70,6 88,3 81 - - - P 50,8 – 226800* 50,8 22,9 68,1 18 138 157 - - - Xích răng Chiều rộng B=8 mm 12,7 0,13 0,49 0,88 1,23 1,53 1,80 1,97 2,28 15,875 0,19 0,69 1,25 1,72 2,15 2,52 2,76 3,20 19,05 0,28 0,98 1,74 2,30 2,79 3,20 3,50 4,00 25,4 0,46 1,59 2,79 3,70 4,52 5,12 5,60 6,40 Chú thích: Xích có dấu * đƣợc chế tạo 1 dãy, 2 dãy và 3 dãy Để tính toán thiết kế xích được thuận tiện hơn, công thức trên được biến đổi thành: 112 Nt= N k Nkkk x nz ... (8-15) Trong đó: Nt: công suất tính toán. [N]: công suất cho phép của bộ truyền xích một dãy, có bƣớc t, số răng đĩa dẫn Z01= 25 và số vòng quay đĩa dẫn n01 cho trong bảng (8.4). Khi sử dụng số liệu trong bảng (8-4), ta lấy kz= 1 25 Z , kn= 1 01 n n , trị số n01 tùy thuộc việc chọn trị số [N] theo cột trong bảng. 8.4.3. Kiểm nghiệm số lần va đập của mắt xích trong 1 giây: Cần đảm bảo điều kiện số lần va đập trong 1 giây là: u = L v.4 = 1000 . 1000.60 .. .4 tX tnZ = X nZ .15 . [u] (8-16) [u]: số lần va đập cho phép, tra ở bảng (8-5) theo loại xích và bƣớc xích. Bảng 8-5 Số lần va đập cho phép [u] trong 1 giây Loại xích Bƣớc xích t, mm 12 hoặc 15 hoặc 19,05 25 hoặc 30 hoặc 35 hoặc 44,45 50 hoặc 12,7 15,87 hoặc 20 25,4 31,75 40 hoặc 45 50,8 Xích ống con lăn 60 45 35 30 25 20 15 12 Xích răng 80 65 50 30 25 - - - 8.4.4. Khoảng cách trục và điều chỉnh khoảng cách trục: 8.4.4.1-Xác định khoảng cách trục: A(mm): nhƣ hình 8-1 ở mục trƣớc. Chọn A: Amin A Amax (8-17) 1. Khoảng cách trục nhỏ nhất Amin :đƣợc qui định theo hai điều kiện sau: a) Góc ôm trên đĩa dẫn 1 120 o thì Amin d2 – d1 (8-18) Trong đó: - d1 :đƣờng kính vòng chia của đĩa dẫn:d1 = 1 sin Z t (8-19) 113 - d2: đƣờng kính vòng chia của đĩa bị dẫn:d2 = 2 sin Z t (8-20) Z1- số răng đĩa dẫn (răng): Z1 Z1 min= 17 Z2 – số răng đĩa bị dẫn (răng): Z2 = i. Z1 Z2 max= 120 t - bƣớc xích (mm)-tra bảng 8.1 b) Để hai đĩa xích không chạm vào nhau thì: Amin 0,5 (de1 + de2) + (30 50) (8-21) Trong đó: de1, de2: là đƣờng kính vòng đỉnh răng của đĩa xích dẫn và bị dẫn. Đối với xích con lăn: de = t [cotg /Z + (0,5 0,6)]. (8-22) Đối với xích răng : de = t. cotg /Z. (8-23) 2. Khoảng cách trục lớn nhất Amax : Đƣợc giới hạn theo công thức: Amax 80. t (8-24) Để dung hoà hai giới hạn trên người ta thường tính sơ bộ khoảng cách trục A theo công thức sau: A = (30 50)t (8-25) 3. Số mắt xích X: Khi đã chọn đƣợc khoảng cách trục A, ta tính số mắt xích X theo công thức sau: X t A.2 + 0,5(Z1 + Z2) + 0,25 (Z2 Z1) 2 . 2.A t (8 26) X: phải đƣợc lấy tròn và là số chẳn Chiều dài L (mm) của xích tính theo công thức: L = X.t (8 27) Trong đó: X số mắt xích, t bƣớc xích. 4. Tính chính xác khoảng cách trục A: A= 0,25.t 2 122 2121 .25,05,0 ZZ ZZXZZX (8-28) 8.4.4.2. Điều chỉnh khoảng cách trục A: Để xích khỏi chịu lực căng quá lớn cần rút khoảng cách trục A đƣợc tính theo công thức (8-28) một khoảng A: Đối với bộ truyền nằm ngang hoặc nghiêng dƣới 600 thì A đƣợc rút ngắn một khoảng : A = (0,002 0,004). A (8-29) Đối với bộ truyền nằm nghiêng 600 trở lên thì không cần điều chỉnh A =0 114 8.4.5. Cơ học truyền động xích: 1. Vận tốc và tỉ số truyền: Hình 8.8 2. Vận tốc và tỉ số truyền tức thời: - Vì mắt xích ăn khớp với các răng của đĩa xích theo hình đa giác cho nên vận tốc của xích và tỉ số truyền thay đổi theo thời gian. - Ta có vận tốc tuyệt đối của mắt xích: v1 = r1. 1 (8-29) Thành phần nằm ngang: vxích = v1. cos = 1. r1.cos (8-30) Trong đó: v1: là vận tốc của đĩa dẫn Với - 11 ZZ Nhận xét: 1 không đổi, nhưng 1 thay đổi nên vxích thay đổi - Xét trên đĩa xích bị dẫn: vxích = v2. cos = 2. r2.cos (8-31) với - 22 ZZ 2 = cos. cos. 2 11 r r (8-32) 2 thay đổi theo chu kỳ, vớigóc quay 1 = const Tỉ số truyền tức thời: i= 2 1 thay đổi Chú ý: Để giảm bớt chuyển động không đều răng, ta cần: 115 Tăng số đĩa xích (chủ yếu Z1) Lấy chiều dài của nhánh dẫn là bội của bánh xích. 3. Vận tốc và tỉ số truyền trung bình: - Vận tốc trung bình v (m/s): v = 1000.60 .. 11 tZn = 1000.60 .. 22 tZn (8-33) Trong đó: - Z1, Z2: số răng của đĩa dẫn và đĩa bị dẫn. - n1, n2: số vòng quay trong một phút của đĩa dẫn và đĩa ... ịnh Fa Đối với ổ bi, ổ đũa trụ ngắn, ổ bi lòng cầu hai dãy thì Fa là tổng các lực dọc trục ngoài tác động lên ổ. Còn đối với các ổ đỡ chặn thì ngoài lực dọc trục bên ngoài tác động lên ổ còn có lực dọc trục phụ Si do lực hƣớng tâm Fri tác dụng lên ổ gây nên Si = e ’ Fri (12-6) Trong đó: e’ tra theo bẳng sau Bảng 12.1 Loại ổ Hệ số e, Ổ côn α = 12 – 360 0,83e Ổ bi đỡ chặn α = 120 0,57(Fr/C0) 0,22 α = 150 0,58(Fr/C0) 0,14 α 180 e Để xác định giá trị lực dọc trục ta có phƣơng trình cân bằng lực: Fa – Fa1 + Fa2 = 0 (12-7) Vì Fa2 và Fa1 không bằng nhau, do đó để xác định chúng ta cần thêm một phƣơng trình. Lực dọc trục phụ S1 do lực hƣớng tâm gây nên có tác dụng làm tác các vòng ổ ra khỏi ổ lăn theo phƣơng dọc trục. Để hiện tƣợng này không xảy ra thì các giá trị lực Fa2 và Fa1 phải thỏa mãn điều kiện sau: Fa1 S1 và Fa2 S2. Bảng 12.2 Tỷ lệ giữa các lực Lực dọc trục S1 S2 Fa > 0 Fa1 = S1 Fa2 = S1 + Fa S1 < S2 Fa > S2 – S1 S1 ≤ S2 Fa ≤ S2 – S1 Fa1 = S2 - Fa Fa2 = S2 185 Ngoài ra một trong hai ổ phải có giá trị Fai = Si. sau khi sử dụng phƣơng pháp thử ta xác định các giá trị Fa2 và Fa1 theo bảng 12.1 theo sơ đồ hình 11.12 SA RA A D Fa2 SD RD Hình 11.12 Sơ đồ xác định tổng lực dọc trục tác dụng lên ổ 1. Tải trọng quy ƣớc Q tác động lên ổ Đối với ổ đỡ và ổ đỡ chặn thì tải trọng quy ƣớc Q là tải trọng hƣớng tâm không đổi Qr. Đối với ổ chặn và ổ chặn đỡ là tải trọng dọc trục không đổi Qa. Giá trị Qr và Qa đƣợc xác định theo công thức sau: Q = Qr = (XVFr + YFa)KσKt (12-8) Q = Qa = (XFr + YFa)KσKt (12-12) Trong đó: Fr,Fa – tổng các lực hƣớng tâm và dọc trục tác động lên ổ Kσ – hệ số xét đến ảnh hƣởng đặc tính tải trọng đến tuổi thọ ổ, chọn theo bảng 12.3: Bảng 12.3 Đặc tính tải trọng Kσ Thiết bị vận hành ngắn hạn hoặc không lên tục: thiết bị gia dụng, cần trục lắp máy và máy xây dựng, máy kéo 1,0 ÷ 1,1 Các thiết bị nhƣ trên nhƣng đòi hỏi độ tin cậy cao hơn: máy nâng, ô tô, máy nông nghiệp 1,1 ÷ 1,2 Máy làm việc một ca, nhƣng không đủ tải: động cơ điện tiêu chuẩn, hộp giảm tốc, động cơ máy bay 1,2 ÷ 1,3 Máy làm việc một ca, đủ tải: máy cắt kim loại và gia công gỗ, máy in, máy dệt, cần trục gầu ngoạm 1,3 ÷ 1,4 Máy làm việc liên tục: hệ thống dẫn động thiết bị cán, máy nén khí, đầu máy xe lửa, 1,5 ÷ 1,7 Máy cán ống, lò chuyển động quay, hệ thống dẫn động thiết bị tàu thủy, thang máy 1,7 ÷ 2,0 Các thiết bị quang trọng làm việc suốt ngày đêm: máy phát điện công xuất lớn, máy và thiết bị chế biến giấy, máy thông khí và máy bơm hầm mỏ, 2,0 ÷ 2,5 186 Kt – hệ số xét ảnh hƣởng nhiệt độ (t oC) đến tuổi thọ ổ: t o C ≤ 100 150 175 200 250 Kt 1,00 1,11 1,15 1,25 1,40 X,Y- hệ số tải trọng hƣớng tâm và dọc trục (bảng 11.3 và 11.4) V – hệ số tính đến vòng nào quay, V = 1 nếu vòng trong quay và V = 1,2 nếu vòng ngoài quay. Bảng 12.4 Hệ số X, Y cho các loại ổ lăn một dãy theo TCVN 4173: 2008 Loại ổ α Fa/Co Fa/(VFr) ≤ e Fa/(VFr) > e e X Y X Y Ổ bi đỡ một dãy 0 0,014 * 0,021 0,028 0,042 0,056 0,070 0,084 0,11 0,17 0,28 0,42 0,56 1 0 0,56 2,30 2,15 1,1212 1,85 1,71 1,63 1,55 1,45 1,31 1,15 1,04 1,00 0,112 0,21 0,22 0,24 0,26 0,27 0,28 0,30 0,34 0,38 0,42 0,44 Ổ bi đỡ chặn 36000 46000 66000 12 18 ÷ 20 24 ÷ 26 30 35; 36 40 0,014 0,0212 0,057 0,086 0,11 0,17 0,212 0,43 0,57 - - 1 1 0 0 0,45 0,43 0,41 0,312 0,36 0,35 1,81 1,62 1,46 1,34 1,22 1,13 1,04 1,01 1,00 1,00 0,87 0,76 0,64 0,57 0,30 0,34 0,37 0,41 0,45 0,48 0,52 0,54 0,54 0,57 0,68 0,80 0,1212 1,14 Ổ đũa côn - - 1 0 0,40 0,4cotα 1,5tan α Ổ bi chặn đỡ 45 60 75 - - - 0,66 0,122 1,66 1 1 1 1,25 2,17 4,67 Ổ đũa chặn đỡ - - - - tanα 1 1,5tan α Ổ bi lồng cầu 1 0 0,4 0,60/e 187 Ổ đũa lồng cầu Chú ý: Chọn theo 0,014 nếu Fa/Co < 0,014 Bảng 12.5 Hệ số X, Y cho các loại ổ lăn hai dãy TCVN 4173: 2008 Loại ổ α Fa/Co Fa/(VFr) ≤ e Fa/(VFr) > e e X Y X Y Ổ bi đỡ 0 0,014 0,028 0,056 0,084 0,11 0,17 0,28 0,42 0,56 1 0 0,56 2,30 1,1212 1,71 1,55 1,45 1,31 1,15 1,04 1,00 0,112 0,22 0,26 0,28 0,30 0,34 0,38 0,42 0,44 Ổ bi đỡ chặn 36000 46000 66000 12 18 ÷ 20 24 ÷ 26 30 35; 36 40 0,014 0,0212 0,057 0,086 0,11 0,17 0,212 0,43 0,57 - - 1 1 2,08 1,84 1,612 1,52 1,312 1,30 1,20 1,16 1,16 1,012 0,122 0,78 0,66 0,55 0,74 0,70 0,67 0,63 0,60 0,57 2,124 2,63 2,37 2,18 1,128 1,84 1,612 1,64 1,62 1,63 1,41 1,24 1,07 0,123 0,30 0,34 0,37 0,41 0,45 0,48 0,52 0,54 0,54 0,57 0,68 0,80 0,125 1,14 Ổ đũa côn - - 1 0,45cotα 0,67 0,67cotα 1,5tanα Ổ bi chặn đỡ 45 60 75 - 1,18 1,120 3,812 0,512 0,54 0,52 0,66 0,122 1,66 1 1 1 1,25 2,17 4,67 Ổ đũa chặn đỡ - - 1,5ta nα 0,67 tanα 1 1,5tanα Ổ bi lồng cầu 1 0,63/e 0,65 0,128/e Ổ đũa lồng cầu 1 0,68/e 0,67 1,0/e Khi tỷ số Fa/VFr < e thì tải trọng dọc trục Fa không ảnh hƣởng đến khả năng tải của ổ. 188 Nếu chế độ tải trọng thay đổi theo bậc thì tải trọng quy ƣớc tƣơng đƣơng QE xác định theo tải trọng quy ƣớc Qi bậc thứ i: 3 3 ( ) i i E i Q L Q L (12-10) 2. Tuổi thọ ổ lăn Công thức xác định tuổi thọ L của ổ: m C L Q (12-11) Còn gọi là công thức xác định tuổi thọ theo độ bền mỏi Nếu tính đến xác suất làm việc không hỏng, vật liệu chế tạo và điều kiện vận hành thì tuổi thọ của ổ xác định theo công thức sau: 1 23 m C L a a Q (12-12) Trong đó a1, a23 là các hệ số. Hệ số α1 phụ thuộc vào xác suất làm việc không hỏng R(t) 1,5 1 ln ln 0,9 R t a Bảng 12.6 R(t) 0,12 0,125 0,126 0,127 0,128 0,1212 a1 1,0 0,62 0,53 0,44 0,33 0,21 Hệ số a23 – hệ số xét đến ảnh hƣởng vật liệu chế tạo và điều kiện vận hành của các loại ổ lăn. Giá trị a23 quyết định tuổi thọ ổ khác nhau giữa các công ty sản xuất: đối với công ty SKF (Thụy Điển) thì a23 = 0,072,5; FAG (Đức) a23 = 0,12,5; NSK (Nhật) a23 = 0,21. Hệ số này đƣợc xác định cho ba trƣờng hợp làm việc sau: 1 – Điều kiện làm việc bình thƣờng 2 – Các bề mặt làm việc đƣợc bôi trơn thủy động đàn hồi 3 – Vòng ổ và con lăn đƣợc chế tạo từ thép đặc biệt nhƣ thép xỉ điện, thép chân không. Các bề mặt làm việc đƣợc bôi trơn thủy động, đàn hồi, trục không bị cong vênh. 189 Bảng 12.7 Hệ số a23 Loại ổ 1 2 3 Ổ bi Ổ đũa trụ ngắn, ổ bi lòng cầu hai dãy Ổ đũa côn Ổ đũa lòng cầu hai dãy 0,7 ÷ 0,8 0,5 ÷ 0,6 0,6 ÷ 0,7 0,3 ÷ 0,4 1 0,8 0,12 0,6 1,2 ÷ 1,4 1 ÷ 1,2 1,2 ÷ 1,3 0,8 ÷ 1 Tuổi thọ ổ tính bằng giờ Lh và tuổi thọ tính bằng triệu vòng quay L có sự liên hệ nhau: 610 60 h L L n (12-13a) hoặc 6 60 10 h nL L (12-13b) Trong đó n là số vòng quay của ổ, vg/ph. Nếu tải trọng thay đổi liên tục thì tuổi thọ tƣơng đƣơng xác định theo công thức: hE HE hL K L (12-14) trong đó: h L = i t - tổng số giờ làm việc KHE – hệ số chế độ tải trọng (bảng 12.14). Công thức xác định khả năng tải động khi biết thời gian làm việc L (tính bằng triệu vòng quay) và tải trọng quy ƣớc Q (N): Ctt = QL l/m (12-15) Khi đó, ta chọn ổ lăn theo điều kiện khả năng tải trọng động nhƣ sau: Ctt = ≤ C (12-16) Giá trị khả năng tải động C có thể tra bảng hoặc xác định theo các công thức sau: Bảng 12.8 Ổ bi Dw ≤ 25,4 mm Dw > 25,4 mm 0,7 2/3 1,8cos o w C f i Z D 0,7 2/3 1,43,65 cos o w C f i Z D Ổ đũa 0,7 3/4 29/273,65 cos o w w C f iL Z D Dw – đƣờng kính bi; i – số dãy cong lăn; - góc tiếp xúc; fo – hệ số tỷ lệ; đƣợc chọn phụ thuộc vào tỷ số Dwcos /Dpw đối với ổ bi và ổ đũa; Lw – chiều dài con lăn. 190 Trình tự chọn ổ lăn Thông số biết trƣớc: 1. Sơ đồ tính toán với giá trị và hƣớng tải trọng tác dụng (biết đƣợc từ phần tính trục) 2. Số vòng quay ổ 3. Đƣờng kính vòng trong d 4. Điều kiện làm việc và kết cấu 5. Thời gian làm việc của ổ Lh. Khi tính toán cần chú ý rằng nếu trên trục lắp hai ổ giống nhau thì ta chọn theo ổ chịu tải trọng lớn nhất. Ta tiến hành chọn ổ lăn có số vòng quay n > 1 vg/ph theo trình tự sau: - Chọn loại ổ lăn theo tải trọng hoặc kết cấu. - Chọn cỡ ổ theo trình tự sau: a) Đối với ổ có lực dọc trục Fa = 0, các bước tiếp tục theo: 1- Xác định phản lực Fr tổng cộng tác dụng lên ổ 2- Chọn các hệ số Kσ, Kt, V (bảng 12.2) theo điều kiện làm việc. Bởi vì không có lực dọc trục thì hệ số X = 1 và Y = 0. Tính tải trọng quy ƣớc tác dụng lên ổ Q 3- Xác định tuổi thọ tính bằng triệu vòng quay L Tính khả năng tải động tính toán của ổ Ctt 4- Chọn cỡ ổ theo điều kiện Ctt < C và n < ngh (giá trị C trong phụ lục 12.1 – 12.8 tài liệu [5]). Nếu không chọn đƣợc cỡ ổ thì chia thời gian làm việc Lh của ổ cho 2, 3 hoặc 4... hoặc thay loại ổ, sử dụng hai ổ trên một gối đỡ,... cho đến lúc thỏa điều kiện trên. b) Đối với ổ có lực dọc trục Fa ≠ 0, các bước tiếp theo: 1- Xác định phản lực Fr tổng cộng tác dụng lên ổ 2- Với giá trị đƣờng kính vòng trong và loại ổ đã chọn theo bảng tra, ta chọn sơ bộ ổ cỡ trung hoặc nhẹ với các giá trị khả năng tải động C và khả năng tải tĩnh Co (trong phụ lục 12.1 – 12.8 tài liệu [5]). Đối với ổ đũa côn, không cần tiến hành bƣớc này. 3- Đối với ổ bi đỡ chặn hoặc ổ đũa côn ta tính lực dọc trục phụ S1 và S2 theo bảng 12.1 ta chọn tải trọng dọc trục tác dụng lên ổ. 191 4- Chọn các hệ số Kσ, Kt, V (bảng 12.2) theo điều kiện làm việc. 5- Xác địn tỷ số Fa/Co và chọn hệ số e theo bảng 12.3 hoặc 12.4. Sau đó tính tỷ số Fa/VFr) và so sánh với e, ta chọn đƣợc các hệ số X và Y. 6- Xác định tuổi thọ tính bằng triệu vòng quay L Tính tải trọng quy ƣớc tác dụng lên Q 7- Tính khả năng tải động tính toán của ổ Ctt 8- So sánh giá trị Ctt vừa tính phải thỏa mãn điều kiện Ctt < C. Nếu không thỏa mãn thì tao chọn cỡ nặng hơn, nếu quá dƣ tải thì ta chọn cỡ nhẹ hơn và tính toán lại đến lúc nào thỏa điều kiện trên. Nếu không thỏa thì chia thời gian làm việc của ổ cho 2, 3 hoặc 4,... cho đến lúc thỏa điều kiện trên hoặc thay loại ổ, sử dụng hai ổ trên một gối đỡ. - Xác định lại tuổi thọ của ổ - Trong một số trƣờng hợp cần thiết ta cần kiểm trả khả năng tải tĩnh của ổ - Trong một số trƣờng hợp cần thiết ta cần kiểm tra số vòng quay tới hạn ổ Ví dụ 12.1 Chọn cỡ ổ cho ổ bi đỡ với các số liệu: lực dọc trục Fa = 600N; lực hƣớng tâm Fr = 2200N; Lh = 5000giờ; số vòng quay n = 800vg/ph. Tính tải trọng tĩnh. Giải: 1. Do lực dọc trục Fa nên ta chọn trƣớc cỡ ổ là cỡ nhẹ có kí hiệu 206 với C = 15300N và Co = 10200N (phụ lục 12.1 [5]). 600 0,059 10200 a o F C , chọn e = 0,26 theo bảng 12.3. Tỷ số 600 0,272 2200 a r F F > e = 0,26 cho nên theo bảng 12.3 ta chọn: X = 0,56 và Y = 1,71 2. Tải trọng quy ƣớc Q: Q = (XVFr + YFa)KσKt = (0,56.1.2200 + 1,71.600).1.1 = 2258N 3. Thời gian làm việc tính bằng triệu vòng quay: 6 6 60 60.5000.800 240 10 10 h L n L triệu vòng 4. Khả năng tải động tính toán 192 32258 240 14032,3m t C Q L N 5. Vì Ct < C = 15300 N, do đó ta chọn cỡ nhẹ là hợp lý. Nếu Ct >> C hoặc Ct << C thì ta chọn lại cỡ ổ và lặp lại quy trình. Ví dụ 12.2 Sơ đồ chọn ổ cho trục 1: SA RA SB RB A B Fa1 Chọn =16o - Hệ số khả năng làm việc: C=Q (n.h) 0,3 Cbảng Công thức 8 1 1 158 Với: n= 374,35 vòng/phút h=18000 giờ - Tải trọng Q: Q=(Kv.R+m.At).Kn.Kt Công thức 8 6 1 159 Với: m= 1,5 Hệ số Bảng 8 2 1 161 Kt=1: Hệ số tải trọng (với tải trọng tĩnh) Bảng 8 3 1 162 Kn=1: Hệ số nhiệt độ (nhiệt độ làm việc dƣới 100 o C) Bảng 8 4 1 162 Kv=1: vòng trong ổ quay Bảng 8 5 1 162 1180,232 2 2 22280,54 2567,84R Y X A A A (N) 193 1115,582 2 2 25407,09 5520,97R Y X B B B (N) 1,3 . 1,3.2567,84. 957,216 1S R tg tg A o A (N) 1,3 . 1,3.5520,97. 1 2058,6 05S R g g ot t B B (N) - Tổng lực chiều trục: At = SA-Fa1-SB = 1257,21 -1075,81 – 2058,05= - 2176,65 Nhƣ vậy At hƣớng về gối trục bên trái. Vì lực hƣớng tâm ở hai gối trục gần bằng nhau, nên ta chỉ cần tính đối với gối trục bên phải(ở đấy lực Q lớn hơn) và chọn ổ cho gối trục này, còn gối trục kia lấy cùng loại. QA = (1. 2567,84+1,5. 2176,65). 1. 1= 13471,88(N) = 1347,18 (daN) C = 1347,18. (374,35. 18000) 0,3 = 150657,412 Với d= 30 (mm). Tra bảng 18 1 349 P Ổ đũa côn đỡ chặn cỡ trung, ta có: Kí hiệu quy ƣớc d (mm) D (mm) đƣờng kính ngoài B (mm) Chiều rộng Cbảng Hệ số khả năng làm việc 7306 30 62 21,5 57000 12.3.3. Tính ổ lăn theo khả năng tải tỉnh Tải trọng Q tăng khi ta giảm tuổi thọ L của ổ, và Q đƣợc giới hạn bởi độ bền tĩnh hay còn gọi là khả năng tãi tĩnh Co. Khả năng tải tĩnh sử dụng để chọn ổ lăn khi số vòng quay n < 1vg/ph, ngoài ra còn dùng để kiểm tra ổ lăn sau khi chọn theo khả năng tải động. Điều kiện để chọn và kiểm tra ổ: Qo < Co (12-17) Trong đó Qo là tải trọng tĩnh quy ƣớc. Khả năng tải tĩnh Co là tải trọng tĩnh gây nên tại vùng tiếp xúc chịu tải lớn nhất giữa con lăn và rãnh vòng với biến dạng dƣ tổng cộng bằng 0,0001 đƣờng kính con lăn. Ứng suất lớn nhất sinh ra tại điểm tiếp xúc với ổ bi là 3000Mpa và đối với ổ đũa là 5000Mpa. Tải trọng tĩnh quy ƣớc Qo xác định theo công thức: 194 - Đối với ổ đỡ và ổ đỡ chặn: chọn một trong hai giá trị lớn nhất sau đây: Qo = XoFr + YoFa và Qo = Fr (12-18) Trong đó Xo, Yo là hệ số tải trọng hƣớng tâm và dọc trục - Đối với ổ chặn và ổ chặn đỡ : Qo = Fa + 2,3Frtanα (12-112) Khi α = 120o (ổ chặn) thì: Qo = Fa Hệ số Xo, Yo đƣợc chọn theo bảng (12.6) Bảng 12.12 Hệ số Xo và Yo Loại ổ Xo Yo Ổ bi đỡ Ổ bi đỡ chặn với góc: α = 12o α = 26o α = 36o 0,6 0,6 0,5 0,5 0,5 0,5 0,37 0,28 Ổ bi lòng cầu và ổ đũa côn 0,5 0,22cotα CÂU HỎI ÔN TẬP 1- Cấu tạo ổ lăn? Ổ lăn đƣợc phân loại nhƣ thế nào? Sử dụng ổ lăn trong trƣờng hợp nào? 2- Các dạng hỏng của ổ lăn? 3- Trình bày các phƣơng pháp cố định vòng trong và vòng ngoài ổ lăn? 4- Khi nào ta sử dụng đĩa chắn dầu hoặc vòng chắn dầu? 195 TÀI LIỆU THAM KHẢO [1]. Trịnh Chất, Cơ sở thiết kế máy và chi tiết máy, Nhà xuất bản khoa học kỹ thuật, 1994. [2]. Trịnh Chất, Lê Văn Uyển, Tính toán thiết kế hệ dẫn động cơ khí, Tập 1&2, Nhà xuất bản giáo dục, 1993. [3]. Nguyễn Trọng Hiệp, Chi tiết máy, Tập 1 & 2, Nhà xuất bản Đại học và giáo dục chuyên nghiệp, 1994. [4]. Nguyễn Văn Lẫm, Nguyễn Trọng Hiệp, Thiết kế chi tiết máy, Nhà xuất bản giáo dục, 1993. [5]. Nguyễn Hữu Lộc, Nguyễn Tuấn Kiệt, Phan Tấn Tùng, Nguyễn Thanh Nam, Cơ sở thiết kế máy, Phần I và II, Trƣờng Đại học Bách Khoa Tp HCM, 2002. [6]. GS.TSKH. Đinh Gia Tƣờng, Nguyên lý máy, Nhà xuất bản khoa học kỹ thuật, 2001. [7]. Trần Ngọc Nhuần, Nguyễn Hoàng Lĩnh, Nguyễn Vĩnh Phối, Trần Văn Thùy, Nguyên lý máy, Nhà xuất bản Xây dựng, 2018. [8]. ThS. Nguyễn Quốc Bảo, Bài giảng Vẽ cơ khí (dùng cho SV bậc Đại học), tài liệu lƣu hành nội bộ (Trƣờng ĐH Phạm Văn Đồng), 2019.
File đính kèm:
giao_trinh_truyen_dong_co_khi_phan_2.pdf