Giáo trình Tiện
Nguyên lý chuyển động:
Quá trình cắt gọt trên máy tiện được thực hiện được là nhờ sự phối hợp 2 chuyển
động:
a. Chuyển động chính:
Là chuyển động quay tròn của phôi, là chuyển động tạo ra vận tốc cắt, chuyển
động này tiêu thụ phần lớn công suất của máy. Khi vật quay tròn, nếu đưa dao vào cắt gọt
sẽ tạo thành vòng tròn mờ trên bề mặt chi tiết. Muốn tạo mặt trụ ta cho dao tịnh tiến
vuông góc với tâm máy.
b. Chuyển động tiến (chuyển động chạy dao):
Là chuyển động tịnh tiến của dao trong quá trình cắt gọt. Bảo đảm cho dao liên tục
cắt gọt vào lớp kim loại mới.
Bạn đang xem 20 trang mẫu của tài liệu "Giáo trình Tiện", để tải tài liệu gốc về máy hãy click vào nút Download ở trên
Tóm tắt nội dung tài liệu: Giáo trình Tiện
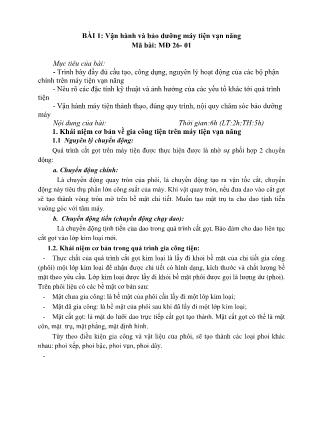
BÀI 1: Vận hành và bảo dưỡng máy tiện vạn năng Mã bài: MĐ 26- 01 Mục tiêu của bài: - Trình bày đầy đủ cấu tạo, công dụng, nguyên lý hoạt động của các bộ phận chính trên máy tiện vạn năng - Nêu rõ các đặc tính kỹ thuật và ảnh hưởng của các yếu tố khác tới quá trình tiện - Vận hành máy tiện thành thạo, đúng quy trình, nội quy chăm sóc bảo dưỡng máy Nội dung của bài: Thời gian:6h (LT:2h;TH:5h) 1. Khái niệm cơ bản về gia công tiện trên máy tiện vạn năng 1.1 Nguyên lý chuyển động: Quá trình cắt gọt trên máy tiện được thực hiện được là nhờ sự phối hợp 2 chuyển động: a. Chuyển động chính: Là chuyển động quay tròn của phôi, là chuyển động tạo ra vận tốc cắt, chuyển động này tiêu thụ phần lớn công suất của máy. Khi vật quay tròn, nếu đưa dao vào cắt gọt sẽ tạo thành vòng tròn mờ trên bề mặt chi tiết. Muốn tạo mặt trụ ta cho dao tịnh tiến vuông góc với tâm máy. b. Chuyển động tiến (chuyển động chạy dao): Là chuyển động tịnh tiến của dao trong quá trình cắt gọt. Bảo đảm cho dao liên tục cắt gọt vào lớp kim loại mới. 1.2. Khái niệm cơ bản trong quá trình gia công tiện: - Thực chất của quá trình cắt gọt kim loại là lấy đi khỏi bề mặt của chi tiết gia công (phôi) một lớp kim loại để nhận được chi tiết có hình dạng, kích thước và chất lượng bề mặt theo yêu cầu. Lớp kim loại được lấy đi khỏi bề mặt phôi được gọi là lượng dư (phoi). Trên phôi liệu có các bề mặt cơ bản sau: - Mặt chưa gia công: là bề mặt của phôi cần lấy đi một lớp kim loại; - Mặt đã gia công: là bề mặt của phôi sau khi đã lấy đi một lớp kim loại; - Mặt cắt gọt: là mặt do lưỡi dao trực tiếp cắt gọt tạo thành. Mặt cắt gọt có thể là mặt côn, mặt trụ, mặt phẳng, mặt định hình. Tùy theo điều kiện gia công và vật liệu của phôi, sẽ tạo thành các loại phoi khác nhau: phoi xếp, phoi bậc, phoi vụn, phoi dây. - 1 - Phoi xếp (Hình 1-1a) được tạo thành khi gia công kim loại cứng với tốc độ nhỏ. VD: khi gia công thép có độ cứng cao. Các phần tử riêng biệt của phoi này có mối liên kết yếu hoặc tách rời nhau. - Phoi bậc (Hình 1-2b) được tạo thành khi gia công kim loại trung bình, nhôm và các hợp kim của nó với tốc độ trung bình. Nó tạo thành dải, mặt dưới nhẵn còn mặt sau có hình răng cưa. - Phoi dây (Hình 1-3c, d) được tạo thành khi gia công thép mễm, đồng, chì, thiếc và một số chất dẻo với tốc độ cắt lớn. Phoi tạo thành dây dài hoặc xoắn lò xo. - Phoi vụn (Hình 1-4đ) được tạo thành khi gia công vật liệu giòn như gang, đồng đỏ. 1.3.Cấu tạo máy tiện vạn năng. Máy tiện ren vít vạn năng là loại máy thông dụng nhất trong nhóm máy tiện. Nó được các nhà máy sản xuất máy tiện trên thế giới không ngừng cho ra đời những loại máy mới với mức độ hoàn chỉnh cao. Tại Việt Nam nhà máy sản xuất máy công cụ số 1 đã sản xuất hàng loạt máy tiện ren vít vạn năng như T616, T630, và loại máy phổ biến hiện nay là T620. Máy tiện ren vít vạn năng có thể gia công rất nhiều loại chi tiết, nhưng chủ yếu là các loại chi tiết có bề mặt tròn xoay và cắt ren. Tuy máy tiện ren vít vạn năng có nhiều cỡ, nhiều loại nhưng nó có những đặc điểm cơ bản giống nhau. Do đó, ta chỉ cần đi sâu vào một vài máy để có thể hiểu được nhiều kiểu máy khác. Một máy tiện ren vít vạn năng được cấu tạo bởi các bộ phận sau: a. Thân máy: Được đúc bằng gang dùng để lắp các cơ cấu chính của máy. Mặt trên của máy là băng trượt dùng để dẫn hướng cho xe dao và ụ sau. Thân máy được đặt trên 2 bệ máy. b. Ụ trước: Là một hộp đúc bằng gang, bên trong lắp các bộ phận làm việc chủ yếu của máy như hộp tốc độ, trục chính, cơ cấu đảo chiều . Trục chính là một trục rỗng, đầu bên phải có lắp đồ gá để kẹp phôi. Trục chính nhận chuyền động từ động cơ thông qua đai chuyền, các bộ bánh răng và khớp nối ly hợp Nhờ có các cơ cấu này ta thay đổi được tốc độ quay của trục chính vì vậy ụ trước còn gọi là hộp tốc độ. Hình 1-1: Các loại phoi tiện. a) Phoi xếp; b) Phoi bậc; c) Phoi dây xoắn; d) Phoi dây hình dải; đ) Phoi vụn. 2 c. Xe dao: Là bộ phận của máy dùng để gá kẹp dao và bảo đảm cho dao chuyển động theo các chiều khác nhau. Chuyển động của dao có thể thực hiện bằng tay hay bằng cơ khí vì nhờ có trục trơn và trục vít me (khi cắt ren). Xe dao gồm có: + Bàn trượt dọc: di chuyển dọc theo chiều của băng máy. + Bàn trượt ngang: chuyển động vuông góc với tâm trục chính. Trên bàn trượt ngang có con trượt trên có thể chuyển động bất kỳ góc độ nào so với trục chính và có ổ gá dao. + Hộp xe dao: Trong hộp có bố trí cơ cấu biến chuyển động quay của trục trơn và vít me thành chuyển động tịnh tiến của dao thông qua cơ cấu bánh răng thanh răng hay vít me đai ốc hai nửa. d. Hộp bước tiến: Là cơ cấu truyền chuyển động từ trục chính đầu trục trơn và trục vít me thông qua bộ bánh răng thay thế đồng thời để biến đổi trị số của bước tiến. e. Bộ bánh răng thay thế: Dùng đ ể đ iề u chỉ nh bước tiế n củ a xe dao theo yêu cầ u khi tiệ n trơn và đ iề u chỉ nh bước ren cầ n thiế t bằ ng cách lựa chọ n những cặ p bánh ră ng thay thế cho phù hợp. f. Ụ sau: Dùng đ ể đỡ các chi tiế t dà i khi gia công hoặ c đ ể gá và tị nh tiế n các loạ i dụ ng cụ cắ t như mũ i khoan, ta rô, Cũ ng có thể đ iề u chỉ nh sau đ ể tiệ n các chi tiế t có dạ ng hình côn. g. Thiết bị điện: Chứa các thiết bị điều khiển điện như công tắc, khởi động từ để đóng ngắt, đảo chiều động cơ. Hình 1.2: Hình dạng bên ngoài của máy tiện ren vít vạn năng. 1 – Ụ trước với hộp tốc độ; 2 – Bộ bánh răng thay thế; 3 – Hộp bước tiến; 4 – Thân máy; 5 – Hộp xe dao; 6 – Xe dao; 7 – Ụ sau; 8 – Tủ điện. 3 h. Nguyên lý hoạt động: - Chuyển động chính: là chuyển động quay tròn của phôi thông qua mâm cặp. đây là chuyển động tạo ra quá trình cắt gọt. phôi quay tròn n (v/phút) - Chuyển động chạy dao thường thực hiện theo hướng song song và thẳng góc với tâm của chi tiết gia công, đây là chuyển động để quá trình cắt diễn ra dễ dàng và liên tục từ khi bắt đầu đến khi kết thúc gia công. S= mm/vòng. Sd-sn ( có thể quay tay) - Chuyển động cắt phụ : dùng tay để điều khiển tay quay: tiến dọc, ngang. i. Công dụng: 50% cắt gọt kim loại, gia công vật tròn, trục côn, định hình , ren. 2. Vận hành máy tiện 3. Chăm sóc máy và các biện pháp an toàn khi sử dụng máy tiện 3.1 Quy tắc an toàn khi làm việc trên máy tiện: a. Trước khi làm việc: - Quần áo phải gọn gàng (Hình 1-1): cổ tay áo phải gài lại, cho áo vào trong quần (hoặc dùng áo sơ mi liền quần), tóc cuốn gọn cho vào trong mũ để quần áo và tóc không bị cuốn vào trong máy. Mắt phải đeo kính bảo hộ (hình 1-2) hình 1-1 hình 1-2 - Kiểm tra máy: phải xem xét các bộ phận bao che bánh răng, đai truyền, bộ bánh răng thay thế, dây tiếp đất, đèn chiếu sáng cục bộ (bảo đảm ánh sáng không làm chói mắt), kiểm tra máy chạy không tải, kiểm tra công tắc đóng mở máy, bộ phận điều khiển phanh hãm, hệ thống bôi trơn làm nguội và thiết bị nâng cẩu. - Không làm việc khi máy bị hỏng. - Vị trí làm việc phải gọn gàng, sạch sẽ. Chuẩn bị đầy đủ tại chỗ làm việc những cần thiết cho quá trình làm việc như: dụng cụ cắt, dụng cụ đo, gá lắp, chi tiết kẹp chặt, hộp đựng dụng cụ, chi tiết, phôi và bục chứa. - Nơi làm việc gọn gàng, sạch sẽ thì bảo đảm được an toàn và nâng cao năng suất lao động. - Nếu máy hỏng điện hoặc hỏng cơ, phải ngừng làm việc và báo cho đốc công hoặc thợ điện, thợ cơ đến sửa chữa. b. Khi làm việc: - Nếu phôi và chi tiết gia công có khối lượng hơn 20kg, khi gá lắp trên máy phải dùng palăng, cẩu. Chỉ dỡ những thiết bị nâng cẩu ra khi vật đã được gá kẹp vững chắc. Kẹp thật 4 chắc vật gia công trên máy (trong mâm cặp, mũi tâm hoặc trên trục gá). Không nối dài thêm tay quay chìa khóa mâm cặp, chìa khóa để gá dao trên ổ dao. - Không dùng căn đệm để lót thêm vào ổ khóa khi chìa khóa không đúng cỡ (tránh làm hư mũ ốc và chìa khóa). - Phải rút chìa khóa ra khỏi mâm cặp và ổ dao, sau khi đã gá xong vật làm và dao. - Dụng cụ phải gá đúng vị trí và bảo đảm vững chắc. Khi gá dao chỉ dùng số căn đệm ít nhất. Trước khi cho máy chạy, phải cho dao cách xa vật làm và trước khi dừng máy, phải rút dao ra. Chọn chế độ cắt hợp lý theo sổ tay kỹ thuật hoặc theo sơ đồ công nghệ. - Phải tắt máy khi không làm việc, khi đo, khi điều chỉnh và sửa chữa máy. Thu dọn nơi làm việc, bôi trơn máy và điều chỉnh khi giải lao và lúc mất điện. - Không tháo dỡ các nắp che an toàn và bộ phận bảo hiểm, không tháo các nắp che của thiết bị điện, không mở các tủ điện, không sờ vào các đầu dây và các mối nối trên dây điện (hình 1-3). - Không dùng tay để hãm mâm cặp hoặc vật làm khi chúng còn đang quay, mà phải dùng cơ cấu phanh để hãm lại. Khi làm việc, phải dùng kính bảo hiểm hoặc lưới chắn phoi và nắp che mâm cặp. - Khi tiện thép với tốc độ cao, phải dùng dao có cơ cấu hoặc rãnh bẻ phoi. Nếu tiện gang phải có chắn phoi. - Không thu dọn phoi hoặc lau máy khi máy còn đang làm việc. Sau khi máy dừng, dùng móc sắt hoặc bàn chảy để gạt và quét phoi. (hình 1-4) - Khi gá những vật làm dài trên mâm cặp, phải dùng mũi tâm ụ sau để đỡ. Nếu trục không cứng vững, khi gia công phải sử dụng giá đỡ. Không xiết quá chặt các vấu của giá đỡ vào vật làm, phải thường xuyên bôi trơn các vấu, kịp thời thay các vấu bị mòn. - Nếu mâm cặp lắp với trục chính bằng ren, phải có cơ cấu hãm để mmâm cặp không tự rời ra. Hình 1-3: Nắp che mâm cặp. a. Vị trí khi kẹp chặt vật gia công. b. Vị trí khi gia công. HÃY THU DỌN PHOI BẰNG QUE SẮT VÀ CHỔI ! Hình 1-4 5 - Khi dùng mũi tâm ụ sau loại cố định, phải thường xuyên cho dàu vào lỗ tâm, thỉnh thoảng phải kiểm tra và điều chỉnh để cho mũi tâm và lỗ tâm không có độ rơ, không rút mũi tâm ra khỏi lỗ tâm khi máy đang làm việc. Khi gia công những vật nặng (khối lượng trên 30kg) phải dùng mũi tâm tự bôi trơn. - Không đeo găng tay hoặc bao tay khi đang làm việc. Nếu ngón tay bị đau, phải băng lại và đeo găng cao su. Lau tay bằng giẻ sạch. Không sử dụng giẻ đã lau máy để lau tay vì giẻ có rất nhiều phoi nhỏ (dầm thép). - Không để dung dịch làm nguội hoặc dầu bôi trơn đổ ra chỗ bục đứng hay trên nền nhà, xung quanh chỗ làm việc. Nếu thấy dầu trong thùng đã cạn, phải gọi thợ cho dầu đến để đổ thêm dầu. - Không đứng dựa vào máy khi làm việc. - Chỉ làm việc khi các dụng cụ thiết bị đảm bảo yêu cầu kỹ thuật. Phải kiểm tra lại các cơ cấu kẹp ở dao lắp ghép. Khi sờ vào máy, nếu thấy có điện giật, phải tắt máy, báo cho đốc công hoặc người trực điện biết. c. Sau khi làm việc: - Phải tắt động cơ điện. - Thu dọn dụng cụ, lau chùi máy sạch sẽ và bôi trơn. - Sắp xếp gọn gàng các chi tiết và phôi vào nơi quy định. 5.2. Kiểm tra, bảo dướng máy tiện. a.Kiểm tra độ chính xác của máy: Việc kiểm tra độ chính xác của máy dược tiến hành sau khi chế tạo hoàn tất hoặc sau mỗi kỳ sửa chữa vừa hoặc sửa chữa lớn. Kiểm tra độ chính xác của máy gồm những nội dung cơ bản sau: - Kiểm tra độ đảo hướng kính tại cổ trục chính của máy. Độ đảo cho phép đối với máy gia công các chi tiết có đường kính D 400 mm bằng 0,006 – 0,015 mm. Dùng đồng hồ so đặt trên băng máy, đưa đầu đo tiếp xúc với cổ trục kiểm lắp trên máy, quay nhẹ trục chính với tốc độ 10 - 20 vòng/phút để kiểm tra. - Kiểm tra độ đồng tâm giữa tâm của trục chính và tâm của mũi nhọn ụ sau. Sai lệch cho phép (tâm của mũi nhọn ụ sau cao hơn tâm của trục chính) là 0,1 mm. Khi kiểm tra, quay vôlăng để nòng ụ sau thò ra hết chiều dài của nó: Điều chỉnh cho ụ sau cách mũi tâm trục chính một khoảng bằng1/2 khoảng cách lớn nhất giữa hai mũi tâm. Giữa hai mũi tâm gá trục kiểm, còn đồng hồ so đặt trên xe dao. Đưa đầu đo của đồng hồ so tiếp xúc với trục kiểm và tịnh tiến xe dao dọc theo băng máy để kiểm tra. Quá trình kiểm tra phải tiến hành theo hai hướng: mặt nằm ngang và thẳng đứng. - Kiểm tra độ song song giữa đường tâm của trục chính với hướng tiến dọc của bàn xe dao. Sai lệch cho phép theo phương thẳng đứng là 0,03 mm; theo phương nằm ngang là 0,015 mm trên chiều dài 300 mm. Trong lỗ trục chính, gá trục kiểm hình trụ đã tôi và mài chính xác. Đồng hồ so đặt trên xe dao. Đưa đầu đo của đồng hồ so tiếp xúc với mặt trục kiểm và tịnh tiến xe dao dọc theo băng máy để kiểm tra. 6 Để đảm bảo độ chính xác của máy tiện phải kiểm tra nhiều lần (18 – 25 lần). b. Quy tắc cơ bản bảo dưỡng máy tiện: Để đảm bảo khả năng làm việc lâu dài của máy, người thợ tiện cần phải thường xuyên bảo dưỡng máy, lau chùi sạch sẽ, tự sửa chữa những hỏng hóc nhỏ, kịp thời báo cáo những hỏng hóc không tự sửa chữa được. Người thợ tiện cần phải thực hiện các quy tắc bảo quản máy như sau: 1 - Trước khi nhận ca, người thợ tiện phải nhận máy từ người giao ca và khi nhận phải thực hiện các công việc: - Xem xét toàn bộ máy và mở máy; - Kiểm tra bộ phận phanh hãm, cho máy chạy với tốc độ chậm và lắng nghe xem trong hộp tốc độ, hộp bước tiến và hộp chạy dao có tiếng kêu khác thường không. - Kiểm tra mắt dầu và bộ phận bơm dầu. Khi máy chạy chậm xem bánh răng cso làm việc không; - Xem xét trên băng máy có vết xước hoặc hư hỏng không; - Kiểm tra hành trình làm việc của xe dao, bàn trượt ngang, bàn trượt dọc. Đóng mở các tay gạt tự động tiến dọc, tiến ngang và tục kết vít me; - Kiểm tra bơm nước làm mát và hệ thống ống dẫn; - Kiểm tra hệ thống chiếu sáng trên máy, bộ phận che an toàn, cơ cấu bảo hiểm và dây tiếp đất của máy. 2 – Bôi trơn kịp thời và đúng vị trí theo sơ đồ chỉ dẫn. Trước khi bôi trơn, phải lau sạch các lỗ cho dầu, bảo đảm đủ dầu trong hộp tốc độ, hộp bước tiến và hộp xe dao. 3 – Trong thời gian làm việc, không để phôi, các chi tiết, dụng cụ cắt gọt, dụng cụ đo trên băng máy, mà phải đặt trên khay gỗ hoặc khay nhựa rồi để trên băng máy. 4 – Để kẹp chặt ổ dao, không dùng búa hay thanh kim loại để gõ vào tay hãm ổ dao. Theo định kỳ phải tháo ổ dao ra, lau sạch các mặt tựa, rửa sạch bằng dầu lửa và lau chùi ổ chốt định vị. 5 – Không để động cơ máy chạy liên tục trong thời gian dài. Phải tắt khi đo các phôi (chi tiết) đang gia công, khi điện cúp. Khi không cần sự ăn dao tự động của bàn dao thì phải ngắt cơ cấu truyền chuyển động tịnh tiến. Đưa tay gạt của bộ phận đảo chiều về vị trí không (thẳng đứng). 6 – Khi làm việc xong, phải lau chùi máy sạch sẽ, không để phoi, bụi bẩn, nước bám vào băng máy và bàn dao. Giẻ lau, bàn chảy, khi lau phoi không được để lại vết và sợi dính trên bề mặt lau. Ít nhất theo chế độ, mỗi tháng một lần tổng vệ sinh máy và nơi làm việc: Rửa máy bằng dầu hòa tan và lau sạch, dùng bàn chảy cọ rửa nắp che, thay dung dịch làm nguội, rửa trục vít me, lau sạch băng máy, puli, bộ bánh răng thay thế, tháo các nắp che, lau sạch bên trong, quét dọn xung quanh vị trí làm việc. Sau khi đã tổng vệ sinh bôi trơn toàn bộ máy theo bảng hướng dẫn. 7 – Máy phải được gá chặt trên móng máy. 7 BÀI 2: Đặc điểm của quá trình cắt khi tiện Mã bài: MĐ 26- 02 Mục tiêu của bài: - Trình bày đầy đủ các yếu tố của chế độ cắt khi tiện. - Phân tích rõ sự biến dạng của kim loại khi cắt, lực cắt, ảnh hưởng của lực cắt. - Trình bày được hiện tượng rung động và nhiệt phát sinh trong quá trình cắt. Nội dung của bài: Thời gian:2h (LT:2h;TH:0h) 1. Bản chất của quá trình cắt gọt kim loại Thực chất của quá trình cắt gọt kim loại là l ... ần điều chỉnh cho lưỡi cắt của dao tiện chạm vào mặt đầu của phôi, điều chỉnh vạch số “0” trên du xích trùng với vạch chuẩn. Có thể chạy dao dọc bằng tay khi tiện trụ bậc bằng cách quay tay quay bàn dao dọc và quan sát trị số trên du xích cho tới khi đạt được kích thước chiều dài cần tiện thì dừng lại. Còn khi thực hiện chạy dao dọc tự động, trong quá trình dao dịch chuyển cần phải quan sát trị số trên du xích ở tay quay bàn xe dao dọc, khi gần tới kích thước chiều dài của bậc cần tiện thì phải ngắt chạy dao tự động và thực hiện chạy dao bằng tay cho đến vạch có giá trị bằng đúng kích thước chiều dài của bậc cần tiện. c. Chọn chế độ cắt: -Chế độ cắt khi tiện trụ bậc cũng tương tự như khi tiện trụ suốt, cũng phụ thuộc vào vật liệu gia công và vật liệu làm dao, vào lượng dư gia công, độ nhám bề mặt, độ cứng vững của dao và phôi, phương pháp gá phôi và dao, dung dịch bôi trơn và làm nguội cũng như các yếu tố khác. -Tuy nhiên, do đường kính của phôi nhỏ dần sau mỗi bậc, nên ta có thể tăng dần số vòng quay cho phù hợp với đường kính phôi. 3.Các dạng sai hỏng, nguyên nhân và cách khắc phục: Nguyên nhân khuyết tật Cách khắc phục Vị trí mặt đầuvà mặt bậc không đảm bảo yêu cầu - Điều chỉnh du xích bàn xe dao không chính xác (không khử hết độ rơ). - Chú ý khử hết độ rơ của máy. - Ngắt tự động không kịp thời. - Ngắt tự động khi dao còn cách vạch dấu 2 – 3 mm, sau đó tiến dao bằng tay để cắt hết lượng dư (đến vạch dấu). - Dùng cữ dọc trong quá trình gia công nhưng chi tiết bị đẩy theo chiều trục do gá không vững chắc. Không có cữ chặn mặt đầu. - Gá phôi vững chắc, dùng cữ chặn mặt đầu Mặt bậc không vuông góc với đường tâm chi tiết - Dao bị đẩy do bàn xe dao ngang có độ rơ. - Điều chỉnh độ rơ của bàn dao ngang - Dao bị đẩy do gá dao quá dài. - Rút ngắn dao lại. 4. Các bước tiến hành tiện 4.1. Tiện thô: - Khi tiện trục bậc, sau khi gá phôi lên mâm cặp 3 chấu tự định tâm, ta chỉnh mũi dao trùng với mũi tâm của ụ động, chọn chế độ cắt (v, t, s) phù hợp. - Cắt thử một đoạn 3 5 mm, kiểm tra kích thước trước khi tiện suốt chiều dài bậc. 4.2. Tiện tinh: (bán tinh+tinh) - Chọn lượng chạy dao nhỏ, chiều sâu cắt ít, lưỡi dao phải sắc bén, bán kính mũi dao đủ lớn và dùng dung dịch tưới nguội trong quá trình cắt. 4.3.Kiểm tra: 37 - Khi sử dụng thước cặp và thước đo chiều sâu để kiểm tra kích thước chiều dài các bậc của trục bậc, độ chính xác sẽ cao hơn so với thước lá và căn mẫu, thông thường sai số trong khoảng 0,1 mm. Dùng panme kiểm tra kích thước đường kính bậc của trục bậc. 4.4.Vệ sinh máy móc: - Sau buổi thực tập phải vệ sinh máy và nơi thực tập: - Dùng tay đóng các công tắc của máy, đảm bảo an toàn điện. - Dùng cọ, bàn chảy quét sạch phoi trên máy. - Dùng cọ, giẻ lau sạch, lau khô các khe của máy. - Bơm dầu cho máy, chống gỉ. - Dọn và đổ phoi đúng nơi qui định. - Trả lại các thiết bị, đồ dùng học tập đúng nơi qui định. - Làm vệ sinh nhà xưởng nơi thực hành. 38 Bài 7. Tiện rãnh và cắt đứt Mục tiêu của bài: - Trình bày đầy đủ các yêu cầu kỹ thuật đối với bề mặt cắt và rãnh cắt trên chi tiết gia công. - Tiện được các loại rãnh vuông, rãnh tròn, rãnh hình thang và cắt đứt chi tiết đúng quy trình, yêu cầu kỹ thuật, thời gian quy định và an toàn. Nội dung của bài: Thời gian:5h (LT:0h;TH:5h) 1. Yêu cầu kỹ thuật của bề mặt cắt và rãnh cắt Tiện trụ ngắn, có rãnh ngoài là phương pháp gia công cơ khí nhằm tạo bề mặt ngoài của chi tiết có các dạng rãnh khác nhau theo yêu cầu của bản vẽ, các rãnh này có thể dùng để thoát dao khi tiện ren, lắp cữ hãm, lắp xéc măng, .v.v. Cắt đứt là bước cuối cùng của nguyên công tiện để có được một sản phẩm riêng biệt hoặc khi cần cắt đứt phôi. Học sinh phải gia công được các dạng rãnh khác nhau (rãnh vuông, rãnh hình thang, rãnh cung tròn, ) và phải đảm bảo các yêu cầu kỹ thuật: - Bề mặt rãnh phải phẳng (không lồi, lõm). - Bề mặt rãnh vuông góc với đường tâm chi tiết. - Các thành rãnh phải song song với nhau. - Độ nhẵn bóng bề mặt. 2. Phương pháp tiện rãnh ngoài và cắt đứt 2.1 Phôi: Phôi tròn (25 x 80 mm). 2.2Dụng cụ đo: - Kiểm tra kích thước chiều sâu, chiều rộng của rãnh có thể sử dụng (Hình 7-1): Thước kẹp (1/10), thước đo sâu, dưỡng đo rãnh, panme (1/100). - Kiểm tra tổng hợp các kích thước của rãnh bằng dưỡng chuyên dùng, độ chính xác căn cứ vào khe sáng giữa rãnh và dưỡng đo. Hình 7-1: Kiểm tra chiều sâu của rãnh a, Kiểm tra bằng thước cặp có đuôi đo sâu. b, Kiểm tra bằng dưỡng 2.3Dụng cụ cắt: a. Dao cắt rãnh ngoài và cắt đứt: 39 Dao cắt rãnh và cắt đứt (Hình 7-2) thường có ba kiểu: dao trái, dao phải và dao cắt có hai lưỡi cắt phụ đối xứng. Xét về lưỡi cắt chính, dao cắt rãnh có lưỡi cắt chính thẳng và dao cắt rãnh định hình (vuông, thang, tròn, ); dao cắt đứt có hai kiểu: dao cắt đứt có lưỡi cắt chính thẳng và dao cắt đứt có lưỡi cắt chính nghiêng. Hình 7-2: Dao cắt rãnh Dao cắt rãnh và dao cắt đứt về cơ bản là giống nhau, dao cắt đứt có đầu dao được vuốt dài hơn so với dao cắt rãnh. Trên phần cắt gọt của dao cắt rãnh và cắt đứt đều có lưỡi cắt chính và hai lưỡi cắt phụ ở hai bên. Tại giao điểm của lưỡi cắt chính và lưỡi cắt phụ thường được mài tròn với bán kính r = 0,2 – 0,3 mm nhằm tăng độ bền mũi dao. Mỗi lưỡi cắt phụ mài nghiêng hợp với hướng tiến của dao một góc nghiêng phụ 1 = 2 = 1 0 – 3 0 . Góc sau phụ ở hai bên được mài 1 = 2 = 1 0 – 30, để giảm ma sát giữa mặt sau phụ với thành rãnh. Trên mặt trước của dao mài một cung tròn có bán kính R = 75 mm, tạo điều kiện cho phoi được cuộn lại dễ dàng và dễ thoát ra ngoài. Chiều rộng lưỡi cắt phụ thuộc vào đường kính phôi cần cắt, thông thường là 3 - 8 mm. - Trong trường hợp cắt đứt, để mặt đầu của phôi cắt không còn gờ lồi ở gần tâm hoặc những phôi sau khi cắt không cần vạt mặt đầu, dao cắt đứt thường được mài với lưỡi cắt nghiêng với góc nghiêng chính = 100 150. a. Gá và điều chỉnh dao tiện cắt rãnh và cắt đứt: Gá dao cắt rãnh và dao cắt đứt: - Khi cắt rãnh và cắt đứt, dao phải gá đúng tâm máy. Nếu dao gá thấp tâm thì khi tiến gần tới tâm của phôi (khi cắt đứt), phần phôi cắt ra sẽ gãy và để lại trên bề mặt phôi một lõi nhỏ, trường phôi không gãy thì lưỡi cắt chính của dao sẽ không cắt được tới tâm phôi và nằm phía dưới lõi trụ nhỏ, dễ làm mẻ lưỡi cắt hoặc đè gãy dao, đặc biệt đối với dao hợp kim. Nếu dao gá cao hơn tâm máy, khi dao cắt gần tới tâm phôi, mặt sau của dao sẽ tỳ vào phần lõi còn lại, khi đó dao không thể cắt tiếp được nữa. - Đối với dao cắt cán thẳng có phần cắt là hợp kim cứng (Hình 7-3) hoặc bằng thép gió, cần phải gá sao cho cán dao vuông góc với trục của phôi để mặt sau phụ của dao không cọ sát vào hai bên thành rãnh. Đối với dao cắt rãnh khi gá dao còn phải bảo đảm cho lưỡi cắt chính của dao song song với trục của phôi. Hình 7-3: Dao cắt đứt gắn hợp kim 40 * Điều chỉnh dao cắt rãnh: Sau khi gá đặt dao cắt đúng yêu cầu, cần điều chỉnh dao cắt để đảm bảo khoảng cách giữa các rãnh hoặc giữa rãnh với mặt đầu của phôi theo bản vẽ: - Điều chỉnh dao cắt bằng sự dịch chuyển bàn dao dọc trên; - Điều chỉnh khoảng cách của rãnh bằng thước lá; - Điều chỉnh dao cắt bằng thước cặp; - Kích thước chiều sâu của rãnh đạt được trong quá trình cắt, căn cứ vào du xích trên tay quay của bàn dao ngang, chiều rộng rãnh phụ thuộc vào chiều rộng lưỡi cắt chính, nếu chiều rộng lưỡi cắt chính nhỏ hơn chiều rộng ranh thì dịch chuyển dao theo hướng dọc dựa vào du xích bàn dao dọc. * Điều chỉnh dao cắt đứt: Điều chỉnh dao cắt đứt tương tự điều chỉnh dao cắt rãnh, ngoài ra còn có một số yêu cầu sau: - Điều chỉnh dao cắt đứt cách mặt đầu chấu cặp khoảng 3 - 5 mm; - Điều chỉnh cho lưỡi cắt phụ bên phải của dao cắt cách mặt đầu của phôi một khoảng l bằng đúng chiều dài của phôi cần cắt. 2.4 Gá chi tiết lên máy tiện: Khi tiện rãnh ngoài, phôi được định vị và kẹp chặt tương tự như khi tiện trụ ngoài. Phôi được định vị và kẹp chặt trên mâm cặp 3 chấu tự định tâm hoặc mâm cặp không tự định tâm. Khi tiện rãnh trong và cắt đứt trên máy tiện, phôi thường được định vị và kẹp chặt trên mâm cặp 3 chấu tự định tâm. 2.5 Quá trình hình thành các kích thước rãnh khi cắt rãnh: a. Cắt các rãnh hẹp: - Các rãnh hẹp và các kích thước của rãnh không yêu cầu chính xác, được cắt với một hành trình công tác của dao, chiều rộng lưỡi cắt chính bằng chiều rộng rãnh. Chiều rộng rãnh cắt có thể cắt đến 5 mm, còn trên các phôi đặc biệt cứng vững và các máy cứng vững có thể cắt các rãnh có chiều rộng đến 10 – 20 mm. - Các rãnh hẹp và chính xác về kích thước chiều rộng rãnh và vị trí so với mặt đầu hoặc mặt gờ của phôi thì được cắt với ba hành trình cắt: + Trong hành trình cắt thứ nhất (bước 1), tiện sơ bộ rãnh với dao cắt rãnh có chiều rộng lưỡi cắt chính nhỏ hơn chiều rộng rãnh từ 1 – 2 mm, chiều sâu cắt sơ bộ nhỏ hơn chiều sâu của rãnh từ 0,5 – 1 mm; + Bước hai, cắt tinh một bên của rãnh đạt kích thước đã cho, xác định vị trí của rãnh và phần đáy tiếp xúc với thành rãnh; + Bước ba, cắt tinh lần cuối thành rãnh còn lại và phần đáy rãnh tiếp xúc với thành rãnh thứ hai bảo đảm kích thước chiều rộng và chiều sâu của rãnh. b. Cắt các rãnh có chiều rộng lớn: Khi cắt các rãnh có chiều rộng lớn, để đạt các kích thước của rãnh theo yêu cầu thường phải cắt qua nhiều bước: 41 - Bước 1: Dùng thước hoặc dưỡng vạch dấu giới hạn rãnh. Sau đó, điều chỉnh dao sao cho dao trùng với mép của thước hoặc dưỡng. Sau khi điều chỉnh dao đúng vị trí, cho dao thực hiện chạy dao ngang tới chiều sâu nhỏ hơn chiều sâu của rãnh trên bản vẽ 0,5mm. - Bước 2: Sau đó, rút dao ra khỏi rãnh vừa cắt vừa dịch chuyển dao nhằm nới rộng rãnh bằng bàn xe dao dọc và quan sát vòng chia độ ở tay quay bàn xe dao ngang cho tới khi đạt chiều sâu như bước 1. Chiều rộng của lớp cắt thứ hai bằng hoặc nhỏ hơn chiều rộng lưỡi cắt chính. Bước 2 có thể được lặp lại nhiều lần tùy vào chiều rộng rãnh cần cắt. - Bước 3: hành trình cắt cuối cùng đảm bảo chiều rộng rãnh cần cắt. Sau khi điều chỉnh dao, thực hiện chạy dao ngang theo du xích ngang tới chiều sâu toàn bộ của rãnh được cho trên bản vẽ. - Bước 4: Sau đó giữ nguyên du xích ngang và thưc hiện chạy dao dọc – tiện tinh đáy rãnh – bằng cách quay tay quay bàn xe dao dọc. c. Cắt các rãnh định hình: Khi cắt các rãnh định hình có hai trường hợp: - Cắt rãnh định hình qua một hành trình cắt với dao cắt có biên dạng của lưỡi cắt trùng với biên dạng của rãnh cần cắt là phương pháp cắt rãnh định hình hở có năng suất cao. Tuy nhiên, phương pháp này chỉ dùng khi cắt các rãnh không quan trọng, có kích thước không lớn và các rãnh không có yêu cầu về độ chính xác. - Cắt rãnh định hình qua nhiều hành trình cắt, bao gồm hai bước: cắt thô rãnh được thực hiện bằng cắt dao cắt rãnh thông thường và cắt tinh rãnh bằng các dao tiện tinh định hình. Việc phân chia thành hai bước sẽ tạo điều kiện để nâng cao năng suất và tăng tuổi thọ của dao cắt rãnh định hình. 2.6 Quá trình cắt đứt: Khi cắt đứt, ngoài việc điều chỉnh dao cắt để đảm bảo các kích thước của phôi, còn phải điều chỉnh chiều dài đầu dao, đặc biệt khi cắt các phôi có đường kính lớn, vì lưỡi cắt của dao cần phải cắt tới tâm của phôi. Để điều chỉnh chiều dài đầu dao phải tiến hành đo đường kính phôi. Căn cứ vào đường kính phôi, điều chỉnh chiều dài đầu dao nhô ra khỏi ổ dao lớn hơn bán kính phôi. Đưa dao tới mặt đầu của phôi, quay tay quay bàn dao ngang cho tới khi lưỡi cắt chính của dao vượt qua tâm hoặc tới tâm của phôi mà cán dao không được chạm vào bề mặt trụ ngoài của phôi. Phôi có đường kính lớn, dao không cắt đến tâm được, mặt khác do trọng lượng của phôi làm cho nó gãy sớm dễ gây ra tai nạn do phôi gãy văng ra, thậm trí làm kẹt dao. Do đó, khi lưỡi cắt chính cách tâm 2 – 3 mm phải rút dao ra khỏi rãnh, tắt máy và bẻ gãy phôi. Nếu cắt đứt phôi cứng, nhất là những phôi có đường kính lớn, tiến dao bằng bàn trượt ngang, đồng thời mở rộng rãnh cắt bằng bước tiến dọc cả hai phía từ 1 – 2 mm bằng Hình 7-4: Cắt gọt bằng phương pháp gá dao và chi tiết gia công quay theo chiều ngược lại. 42 cách quay tay quay bàn xe dao dọc về hai phía một cách đều đặn, quá trình tiếp tục cho tới khi dao gần tới tâm của phôi, nhằm tránh hiện tượng kẹt phôi trong rãnh cắt và cắt nhẹ nhàng hơn. Nếu phôi có đường kính lớn hoặc những phôi có lượng dư phân bố không đều, tăng độ cứng vững của dao, dùng dao cắt đầu cong và gá úp dao, chi tiết gia công quay ngược chiều cắt gọt (Hình 7-4). Cắt gọt bằng phương pháp này, phoi tự rơi xuống máng hứng không làm xảy ra hiện tượng kẹt phoi. Khi cắt đứt phôi dạng ống thành từng khoang nhỏ, để đảm bảo an toàn trong khi cắt nên dùng thanh đỡ gá vào nòng ụ động. Sau khi cắt đứt, các chi tiết sẽ mắc vào thanh đỡ và người thợ chỉ cần gạt chúng về phía ụ động. Chú ý: - Khi cắt đứt các phôi đặc không vượt quá đường kính phôi 60mm; - Khi cắt đứt các phôi đặc, lúc dao tiến gần vào tới tâm chi tiết (khoảng 0,5 bán kính của phôi), giá trị bước tiến cần giảm 40% - 50%. - Khi dao tịnh tiến gần vào tới tâm chi tiết (khoảng 0,5 bán kính của phôi), nên ngắt chạy dao tự động, thực hiện chạy dao bằng tay để tránh dao bị gãy. 2.7 Chọn chế độ cắt: Bước tiến khi cắt rãnh và cắt đứt nhỏ hơn khi tiện trụ ngoài hoặc khi xén mặt đầu. Khi cắt chi tiết có đường kính nhỏ hơn 60 mm, chọn bước tiến s = 0,1 – 0,15 mm/vòng. Nếu đường kính lớn hơn chọn s = 0,3 mm/vòng. Tốc độ cắt nhỏ hơn 15% - 20% khi tiện trụ ngoài. Tuy nhiên, do đường kính của phôi nhỏ dần sau mỗi bậc, nên ta có thể tăng dần số vòng quay cho phù hợp với đường kính phôi. Khi cắt rãnh hoặc cắt đứt phôi thép, do có ma sát lớn giữa mặt sau của dao với phôi, nên trong quá trình cắt cần phải sử dụng dung dịch làm nguội và tưới liên tục vào vùng cắt gọt để giảm ma sát giữa mặt sau với phôi. 3. Các dạng sai hỏng, nguyên nhân và cách khắc phục: Các khuyết tật Nguyên nhân Cách khắc phục - Chiều rộng rãnh sai. - Chiều rộng của dao cắt sai. - Kiểm tra sai khi tiện rãnh bằng cách cho dao tiến hai phía hoặc cho dao ăn liên tục. - Mài dao lưỡi rộng hoặc thay thế dao có chiều rộng lưỡi cắt nhỏ. - Cắt thử theo vạch dấu, dùng cử chặn cả hai bên xe dao. - Chiều sâu rãnh sai. - Tính toán trên du xích sai - Không khử hết độ rơ bàn dao ngang. - Dao tự hút vào chi tiết gia công. - Kiểm tra cẩn thận chiều sâu cắt bằng dưỡng hoặc thước đo sâu. - Khử độ rơ. - Mài lại dao để giảm góc thoát. Kẹp chặt lại dao. - Thành bên của rãnh không vuông - Dao gá không vuông góc. - Dao có góc nghiêng phụ 1 - Kiểm tra lại dao sau khi gá. - Mài lại dao. 43 Các khuyết tật Nguyên nhân Cách khắc phục góc với đường tâm chi tiết. nhỏ. - Vị trí rãnh sai so với mặt đầu hoặc bậc của chi tiết. - Điều chỉnh dao theo cữ sai. - Kiểm tra lại dao và cữ. - Dao bị bập sâu vào rãnh. - Bàn trượt ngang có độ rơ lớn. - Trục chính bị đảo. - Điều chỉnh lại độ rơ. - Điều chỉnh lại ổ trục trước. - Độ nhẵn bề mặt kém. - Dao cơ chiều rộng lưỡi cắt lớn. - Dao gá dài. - Sử dụng dao lưỡi cắt hẹp, mở rộng rãnh khi cắt, dùng dao có độ cứng vững cao.
File đính kèm:
giao_trinh_tien.pdf