Giáo trình môn Hướng dẫn thiết kế ô tô
Mô men ma sát của ly hợp :
Ly hợp phải có khả năng truyền hết mô-men xoắn lớn nhất của động cơ Memax.
Để bảo đảm yêu cầu truyền hết mô-men xoắn lớn nhất của động cơ trong mọi điều
kiện làm việc, thì ta phải có :
M
ms = Memax.β (1-1)
Trong đó :
M
ms : Mô-men ma sát cần thiết của ly hợp, [N.m].
M
max : Mô-men xoắn lớn nhất của động cơ, [N.m]. (Lấy theo số liệu đề cho, đối
với máy kéo mô-men này lấy bằng mô men định mức Mn của động cơ).
β : Hệ số dự trữ của ly hợp.
Hệ số dự trữ ly hợp β phải đủ lớn (β>1) để bảo đảm cho ly hợp truyền hết mô-men
xoắn động cơ trong mọi điều kiện làm việc của nó (khi các bề mặt ma sát bị dầu mở rơi
vào, khi các lò xo ép bị giảm tính đàn hồi, khi các tấm ma sát bị mòn.v.v.). Mặc khác hệ
số β không được lớn quá, vì như thế ly hợp không làm tốt chức năng bảo vệ an toàn cho
hệ thống truyền lực khi quá tải.
Tóm tắt nội dung tài liệu: Giáo trình môn Hướng dẫn thiết kế ô tô
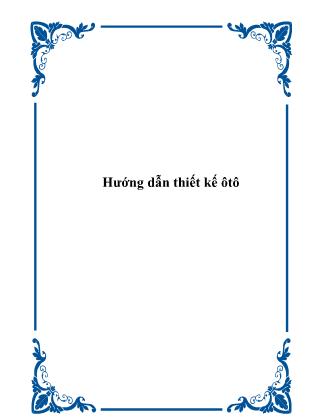
Hướng dẫn thiết kế ụtụ H−ớng dẫn thiết kế ôtô: (Phần truyền lực trên ôtô) - Ngành Cơ khí Ôtô Ch−ơng 1 : Thiết kế ly hợp ôtô Mục đích của việc thiết kế môn học phần ly hợp ôtô nhằm xác định các thông số cơ bản của ly hợp ôtô. Đó là tính toán xác định số l−ợng và kích th−ớc bề mặt ma sát, cơ cấu ép và cơ cấu điều khiển của ly hợp nhằm bảo đảm các yêu cầu của ly hợp trong mọi điều kiện làm việc của ôtô. 1. Tính toán đĩa bị động và đĩa ép: 1.1. Mô men ma sát của ly hợp : Ly hợp phải có khả năng truyền hết mô-men xoắn lớn nhất của động cơ Memax. Để bảo đảm yêu cầu truyền hết mô-men xoắn lớn nhất của động cơ trong mọi điều kiện làm việc, thì ta phải có : Mms = Memax.β (1-1) Trong đó : Mms : Mô-men ma sát cần thiết của ly hợp, [N.m]. Mmax : Mô-men xoắn lớn nhất của động cơ, [N.m]. (Lấy theo số liệu đề cho, đối với máy kéo mô-men này lấy bằng mô men định mức Mn của động cơ). β : Hệ số dự trữ của ly hợp. Hệ số dự trữ ly hợp β phải đủ lớn (β>1) để bảo đảm cho ly hợp truyền hết mô-men xoắn động cơ trong mọi điều kiện làm việc của nó (khi các bề mặt ma sát bị dầu mở rơi vào, khi các lò xo ép bị giảm tính đàn hồi, khi các tấm ma sát bị mòn.v.v..). Mặc khác hệ số β không đ−ợc lớn quá, vì nh− thế ly hợp không làm tốt chức năng bảo vệ an toàn cho hệ thống truyền lực khi quá tải. Hệ số β th−ờng đ−ợc xác định bằng thực nghiệm; có tính đến các yếu tố nh− đã nêu và đặc biệt chú ý xét đến điều kiện làm việc nặng nhọc của xe, đặc tính động lực học của xe thiết kế. Giá trị của β có thể tham khảo theo số liệu ở bảng B1-1 nh− sau : Bảng B1-1 : Bảng chọn hệ số dự trữ ly hợp β Loại xe Trị số β Xe du lịch 1,35 ữ 1,75 Xe tải, khách, máy kéo vận tải (không kéo mooc) 1,60 ữ 2,25 Ô tô tải có mooc (hoặc tính năng thông qua cao) 1,80 ữ 3,00 Máy kéo nông nghiệp kiểu ly hợp th−ờng đóng 2,00 ữ 2,50 Chú ý : Giá trị giới hạn trên đ−ợc chọn cho xe làm việc trong điều kiện nặng nhọc (nh− tải trọng lớn, xe hoạt động trong nhiều loại đ−ờng, hoặc kiểu ly hợp không điều chỉnh đ−ợc). GVC. Ths. Lê Văn Tụy - Khoa Cơ khí Giao thông - Tr−ờng Đại học Bách khoa - ĐHĐN 1 H−ớng dẫn thiết kế ôtô: (Phần truyền lực trên ôtô) - Ngành Cơ khí Ôtô Ng−ợc lại xe làm việc trong điều kiện không năng nhọc, có đặc tính động lực học tốt thì chọn về phía giới hạn nhỏ. Vậy, căn cứ vào chủng loại xe và điều kiện làm việc th−ờng xuyên của nó mà ta chọn hệ số β thích hợp; từ đó xác định đ−ợc mô-men ma sát cần thiết của ly hợp theo công thức (1-1) nhằm có thể truyền hết mô-men xoắn của động cơ trong mọi điều kiện hoạt động. 1.2. Bán kính hình vành khăn của bề mặt ma sát đĩa bị động : Nếu gọi lực ép tổng cộng do cơ cấu ép tạo ra là F [N], đặt tại bán kính trung bình Rtb [m] của đĩa bị động, thì mô-men ma sát của ly hợp Mms [N.m] do cơ cấu ép tạo ra là : Mms = à.F.Rtb.zms (1-1b) Trong đó : à : Hệ số ma sát tr−ợt giữa các đôi bề mặt ma sát (tấm ma sát với đĩa ép và tấm ma sát với bánh đà). zms : Số đôi bề mặt ma sát; phụ thuộc vào số đĩa bị động của ly hợp: + Ly hợp một đĩa bị động : zms = 2 + Ly hợp hai đĩa bị động : zms = 4 Gọi p [N/m2] là áp suất pháp tuyến sinh ra ở các đôi bề mặt ma sát d−ới tác dụng lực ép F, và với giả thiết áp suất p là phân bố đều trên toàn bộ bề mặt ma sát (p = const). Với R1, R2 là bán kính trong và ngoài của hình vành khăn thì mô-men ma sát của đĩa bị động ly hợp Mms do cơ cấu ép tạo ra đ−ợc viết lại ở dạng triển khai theo kích th−ớc của tấm ma sát: (1-1c) ms 3 R 3 2ms z)K1(RpM −πà= Trong đó : p : áp suất pháp tuyến của các bề mặt ma sát, [N/m2]. KR : Hệ số tỷ lệ giữa bán kính trong và ngoài bề mặt ma sát, KR = 2 1 R R . Suy ra bán kính ngoài R2 [m] của bề mặt ma sát đĩa bị động ly hợp đ−ợc xác định theo áp suất làm việc của các bề mặt ma sát. R2 = ( )3 3Rms maxe K1.p...z.2 M..3 −πà β (1-2) • Giá trị áp suất làm việc của các bề mặt p là một trong những thông số quan trọng quyết định đến l−ợng mòn của các bề mặt ma sát khi ly hợp tr−ợt trong quá trình đóng ly hợp sau gài số. Trong đó vành ma sát th−ờng làm bằng vật liệu có hệ số ma sát cao GVC. Ths. Lê Văn Tụy - Khoa Cơ khí Giao thông - Tr−ờng Đại học Bách khoa - ĐHĐN 2 H−ớng dẫn thiết kế ôtô: (Phần truyền lực trên ôtô) - Ngành Cơ khí Ôtô nh−ng mềm hơn thép và gang. Vì vậy trong tính toán thiết kế phải chọn giá trị áp suất làm việc p nhỏ hơn hoặc bằng giá trị cho phép [p] = 1,4.105 ữ 2,5.105 [N/m2] nhằm bảo đảm tuổi thọ cần thiết cho chúng giữa hai lần sữa chữa thay thế. Giá trị giới hạn trên đ−ợc áp dụng cho ôtô có động cơ nhiều xy lanh (lớn hơn 4), đặc tính động lực của xe tốt và làm việc trong điều kiện đ−ờng sá tốt (ít phải sang số) và ng−ợc lại ôtô có động cơ ít xy lanh, đặc tính động lực của xe không tốt và làm việc trong điều kiện đ−ờng sá xấu. • Hệ số tỷ lệ KR có thể chọn theo kinh nghiệm bằng KR = 0,53 ữ 0,75. Giá trị nhỏ chỉ dùng cho xe có động cơ tốc độ trung bình và thấp và đặc tính động lực xe tốt (ít phải sang số). Với động cơ cao tốc, nếu chọn hệ số KR bé (tức R1 và R2 khác nhau lớn) thì chênh lệch tốc độ tr−ợt tiếp tuyến ở mép trong và mép ngoài của vành tấm ma sát sẽ lớn, gây ra sự mòn không đều từ trong ra ngoài làm cho thời hạn phục vụ của tấm ma sát sẽ giảm. Vì vậy đối với động cơ cao tốc nên chọn hệ số tỷ lệ kR về phía giới hạn trên. • Hệ số ma sát à phụ thuộc vào nhiều yếu tố : vật liệu và tình trạng của đôi bề mặt ma sát, tốc độ tr−ợt t−ơng đối, nhiệt độ và áp suất trên bề mặt ma sát. Đối với ly hợp ma sát cơ khí ôtô máy kéo, hệ số ma sát giữa phê-ra-đô đồng với gang (hoặc thép) thì hệ số ma sát à có thể đạt đến 0,35. Tuy vậy, do ảnh h−ởng của các yếu tố nhiệt độ, tốc độ tr−ợt .v.v.. nên khi tính toán chỉ chọn trong khoảng à = 0,22 ữ 0,30. • Số đôi bề mặt ma sát zms th−ờng chọn bằng 2 (tức ly hợp một đĩa bị động). Chỉ đối với máy kéo hoặc ôtô tải lớn; có mô-men cực đại của động cơ lớn (từ 465 [N.m] trở lên), làm việc trong điều kiện nặng nhọc thì mới chọn zms = 4 (ly hợp có hai đĩa bị động). Trong tính toán thiết kế, bán kính ngoài có thể R2 có giá trị quá lớn v−ợt quá giới hạn đ−ờng kính bề mặt ma sát của bánh đà động cơ (tham chiếu bảng B1-2). Lúc đó R2 phải đ−ợc tính lặp lại với zms = 4. Bảng B1-2: Giới hạn của đ−ờng kính ngoài vành ma sát D2 Mômen cực đại động cơ Memax[Nm] không lớn hơn Số vòng quay t−ơng ứng nN [v/ph] không nhỏ hơn Đ−ờng kính cho phép D2 [mm] không lớn hơn ≤ 88 ữ 240 ≥ 7000 ữ 10000 ≤ 180 ữ 240 ≤ 200 ữ 375 ≥ 4500 ữ 5000 ≤ 250 ữ 325 ≤ 400 (465) ữ 685(1080)* ≥ 3000 ữ 4000 ≤ 340 ữ 400 ≤ 1080(1420)* ≥ 2500 ữ 3000 ≤ 420 Chú thích * : Giá trị trong dấu ngoặc đơn t−ơng ứng với ly hợp có thể 2 đĩa bị động. GVC. Ths. Lê Văn Tụy - Khoa Cơ khí Giao thông - Tr−ờng Đại học Bách khoa - ĐHĐN 3 H−ớng dẫn thiết kế ôtô: (Phần truyền lực trên ôtô) - Ngành Cơ khí Ôtô Bán kính trong của bề mặt ma sát R1 [m] đ−ợc xác định thông qua hệ số tỷ lệ KR đã chọn khi tính toán bán kính ngoài R2 ở trên. Tức là: R1 = KRR2 (1-2b) 1.3. Diện tích và bán kín trung bình của hình vành khăn tấm ma sát : Diện tích hình vành khăn tấm ma sát S [m2]: S = π (1-3) )RR( 2122 − Bán kính trung bình hình vành khăn của tấm ma sat Rtb [m]: Rtb = 2 1 2 2 3 1 3 2 3 2 RR RR − − (1-3b) 1.4. Lực ép của cơ cấu ép: Sau khi đã xác định đ−ợc các thông số kích th−ớc của vành ma sát, ta dễ dàng xác định đ−ợc lực ép cần thiết của cơ cấu ép phải tạo ra mà theo đó bảo đảm áp suất làm việc đã chọn và thỏa mãn mô-men ma sát yêu cầu: F = mstb maxe zR. M. à β (1-4) 1.5. Công tr−ợt riêng của ly hợp : Việc xác định kích th−ớc của bề mặt ma sát theo điều kiện áp suất làm việc không v−ợt quá giá trị cho phép nh− trên ch−a đủ để đánh giá khả năng chống mòn của ly hợp. Khi các ly hợp khác nhau có cùng áp suất làm việc nh−ng với ôtô máy kéo có trọng l−ợng khác nhau thì sự hao mòn của ly hợp sẽ khác nhau. Quá trình đóng êm dịu ly hợp bao giờ cũng kèm theo sự tr−ợt ly hợp giữa các đôi bề mặt ma sát. Sự tr−ợt của ly hợp làm cho các bề mặt ma sát mòn, đồng thời sinh nhiệt nung nóng các chi tiết tiếp xúc với các bề mặt trựơt. Nếu c−ờng độ tr−ợt quá mạnh sẽ làm mòn nhanh các bề mặt ma sát và nhiệt sinh ra sẽ rất lớn, có thể làm cháy cục bộ các tấm ma sát, làm nung nóng lò xo ép từ đó có thể làm giảm khả năng ép của chúng. Vì vậy, việc xác định công tr−ợt, công tr−ợt riêng để hạn chế sự mòn, khống chế nhiệt độ cực đại nhằm bảo đảm tuổi thọ cho ly hợp là hết sức cần thiết. Để đánh giá tuổi thọ của ly hợp theo điều kiện tr−ợt, ng−ời ta dùng chỉ tiêu công tr−ợt riêng; đ−ợc xác định bằng công tr−ợt trên một đơn vị diện tích làm việc của các bề mặt ma sát, kí hiệu lr [J/m 2] : )( 21 2 2 RRz Ll ms r −= π (1-5) GVC. Ths. Lê Văn Tụy - Khoa Cơ khí Giao thông - Tr−ờng Đại học Bách khoa - ĐHĐN 4 H−ớng dẫn thiết kế ôtô: (Phần truyền lực trên ôtô) - Ngành Cơ khí Ôtô Trong đó : L : Công tr−ợt tổng cộng của ly hợp, [Jun]. zms : Số đôi bề mặt ma sát. R2 : Bán kính ngoài hình vành khăn bề mặt ma sát, [m]. R1 : Bán kính trong hình vành khăn của bề mặt ma sát, [m]. Sự tr−ợt của ly hợp diễn ra ngay sau khi gài số và thực hiện đóng ly hợp. Điều đó có thể xẫy ra lúc xe đang chạy hoặc khi bắt đầu khởi hành xe; trong đó tr−ờng hợp xe bắt đầu khởi hành sẽ có công tr−ợt lớn nhất vì lúc này sự chênh lệch tốc độ giữa bánh đà động cơ và tốc độ trục ly hợp (xe đang đứng yên) là lớn nhất. Sự tr−ợt ly hợp khi khởi hành xe cũng có thể có hai tr−ờng hợp : sự tr−ợt ly hợp do đóng ly hợp đột ngột hoặc sự tr−ợt ly hợp do đóng ly hợp từ từ. - Khi đóng ly hợp đột ngột (lái xe thả nhanh bàn đạp ly hợp) làm cho đĩa ép lao nhanh vào đĩa bị động, thời gian tr−ợt ngắn nh−ng lực ép tăng lên nhanh làm cho xe bị giật mạnh, gây tải trọng động lớn đối với hệ thống truyền lực (do quán tính lao vào của đĩa ép, làm tăng thêm lực ép, mô men ma sát ly hợp tăng lên và do vậy ly hợp có thể cho phép truyền qua nó một mô men quán tính lớn hơn mô men ma sát tính toán theo 1-1). - Khi đóng ly hợp từ từ : Việc đóng ly hợp hợp từ từ tạo đ−ợc sự êm dịu cần thiết cho ly hợp và hệ thống truyền lực. Đó là một trong những yêu cầu quan trọng của ly hợp nhằm bảo đảm tính êm dịu và không sinh ra va đập cho hệ thống truyền lực. Tuy nhiên sự đóng từ từ ly hợp làm cho thời gian tr−ợt kéo dài và do vậy công tr−ợt sẽ tăng lên. Qua khảo sát quá trình tr−ợt ly hợp khí đóng êm diu, chúng ta có trình tự các b−ớc để tính công tr−ợt L[Jun] của ly hợp nh− sau: 1.5.1 Mô men quán tính qui dẫn Ja [kg.m 2]: Mô men quán tính khối l−ợng qui dẫn Ja đ−ợc xác định từ điều kiện cân bằng động năng khi ôtô đang chuyển động nh− sau : t2 oph 2 bxma a )iii( r g GGJ δ⎟⎟⎠ ⎞ ⎜⎜⎝ ⎛ += (1-5a) Trong đó : Ga : Trọng l−ợng toàn bộ của ôtô, [N]. Gm : Trọng l−ợng toàn bộ của rơ mooc hoặc đoàn xe kéo theo, [N]. g : Gia tốc trọng tr−ờng, g = 9,81 [m/s2]. rbx : Bán kính làm việc của bánh xe chủ động, [m]. ih,ip,io : Tỷ số truyền t−ơng ứng của hộp số, hộp số phụ và truyền lực chính. δt : Hệ số tính đến các khối l−ợng chuyển động quay trong hệ thống truyền lực; trong tính toán có thể lấy bằng δt = 1,05 ữ 1,06. GVC. Ths. Lê Văn Tụy - Khoa Cơ khí Giao thông - Tr−ờng Đại học Bách khoa - ĐHĐN 5 H−ớng dẫn thiết kế ôtô: (Phần truyền lực trên ôtô) - Ngành Cơ khí Ôtô 1.5.2 Mô men cản chuyển động qui dẫn Ma [N.m]: Mô men cản chuyển động của xe qui dẫn về trục ly hợp đ−ợc tính bằng : [ ] tt bx maa i r PGGM ηψ ω++= )( (1-5b) Trong đó : ψ : Hệ số cản tổng cộng của đ−ờng. Pω : Lực cản của không khí, [N]. it : Tỷ số truyền chung hệ thống truyền lực (it = ih.ip.io). ηt : Hiệu suất thuận của hệ thống truyền lực. Các thông số khác đã đ−ợc chú thích. 1.5.3 Tính thời gian tr−ợt ly hợp trong các giai đoạn (t1 và t2): Chúng ta có thể chọn một trong hai cách tính sau: a) Tính theo thời gian tr−ợt tổng cộng của ly hợp t0 : Chọn thời gian đóng ly hợp êm dịu : t0 = 1,1 ữ 2,5 [s] (chọn thời gian càng lớn, quá trình đóng ly hợp càng êm dịu nh−ng công tr−ợt sẽ tăng). Tính hệ số kết thúc tr−ợt kđ (kđ >0) ly hợp từ ph−ơng trình : 2 max max 0 ).( .2).(. aed aaeed MMk JMk t − −= ωω (1-5c) Tính thời gian tr−ợt t1, t2 : ⎪⎪⎩ ⎪⎪⎨ ⎧ −= − ω−ω= )MM.k( M tt )MM.k( J.2).( t amaxed a 21 amaxed aae 2 (1-5c’) Trong đó kđ là hệ số kết thúc tr−ợt; xác định tỷ số của mômen ma sát hình thành so với mômen cực đại động cơ mà tại đó ly hợp bắt đầu hết tr−ợt (kđ = Mms/Memax). Trong hệ ba ph−ơng trình trên kđ là ẩn số phụ của hệ ph−ơng trình. b) Tính theo hệ số c−ờng độ tăng mômen K: Chọn hệ số K (đặc tr−ng cho c−ờng độ tăng mômen K = Mms/t0): - Xe du lịch và khách : K = 50 ữ 150 [N.m/s]. - Xe vận tải hàng hóa : K = 150 ữ 750 [N.m/s]. Tính thời gian tr−ợt t1, t2 : GVC. Ths. Lê Văn Tụy - Khoa Cơ khí Giao thông - Tr−ờng Đại học Bách khoa - ĐHĐN 6 H−ớng dẫn thiết kế ôtô: (Phần truyền lực trên ôtô) - Ngành Cơ khí Ôtô ⎪⎪⎩ ⎪⎪⎨ ⎧ −= = K Jt K Mt aea a )(2 2 1 ωω (1-5d) Kiểm tra thời gian tr−ợt tổng cộng : t1 + t2 = t0 ∈ (1,1 ữ 2,5 [s]). Nếu không thõa quá trình chọn K và tính t1, t2 sẽ đ−ợc lặp lại. 1.5.4 Tính công tr−ợt tổng cộng của ly hợp L [J] 2aea2 1 aea ).(J2 1t 3 2 2 t)..(ML ω−ω+⎟⎠ ⎞⎜⎝ ⎛ +ω−ω= (1-5e) Trong đó : t1 : Thời gian tr−ợt của giai đoạn I, đ−ợc xác định từ (1-5c hoặc 1-5d). t2 : Thời gian tr−ợt của giai đoạn II, đ−ợc xác định từ (1-5c hoặc 1-5d). Chú ý : c ) Khi đóng ly hợp êm dịu, công tr−ợt L phụ thuộc rất lớn vào trọng l−ợng của xe. Khi tăng trọng l−ợng (hoặc kéo thêm đoàn xe) thì công tr−ợt tăng nhanh (vì L tỷ lệ với Ma, Ja, t1, t2 mà tất cả các thông số này đều tăng theo sự tăng của trọng l−ợng xe). d ) Khi tăng giá trị tỷ số truyền của hệ thống truyền lực thì công tr−ợt giảm (vì Ma, Ja, t1, t2 tỷ lệ nghịch với tỷ số truyền). Điều đó cho ta kết luận rằng khi khởi hành xe, ta phải khởi hành với số truyền thấp của hộp số (ih1) để giảm công tr−ợt của ly hợp. e ) Khi khởi hành xe tại chỗ công tr−ợt là lớn hơn cả (vì lúc đó ωa = 0 nên hiệu số ωe - ωa là lớn nhất). Động cơ càng cao tốc, công tr−ợt càng lớn. Trong tính toán, có thể lấy tốc độ góc động cơ ωe bằng tốc độ góc ứng với mô men cực đại (ωe = ωM) và tính toán kiểm tra công tr−ợt riêng ứng với chế độ khởi hành xe tại chỗ (ωa = 0 ). Giá trị công tr−ợt riêng tính theo công thức (1-5) phải nằm trong giới hạn cho phép (tính cho số truyền thấp ihI với hệ số cản tổng cộng của đ−ờng ψ = 0,02). Xe con : lr ≤ 1000 [KJ/m2] Xe khác tải và khách : lr ≤ 800 [KJ/m2] f ) Để có thể đơn giản hơn trong tính toán, Giáo s− A.I Gri-skê-vich đề nghị sử dụng công thức tính công tr−ợt L (tính bằng [J]) nh− sau: 2)( 2 max max e ae e a MM MJL ω−= (1-5’) Trong đó : Memax : Mô men quay cực đại của động cơ, [Nm]. GVC. Ths. Lê Văn Tụy - Khoa Cơ khí Giao thông - Tr−ờng Đại học Bách khoa - ĐHĐN 7 H−ớng dẫn thiết kế ôtô: (Phần truyền lực trên ôtô) - Ngành Cơ khí Ôtô Ma : Mô men cản chuyển động của xe qui dẫn về trục ly hợp, [Nm]. Ja : Mô men quán tính khối l−ợng của xe qui dẫn về trục ly hợp, [kgm2] ωe : Tốc độ góc của trục khuỷu động cơ khi đóng ly hợp êm dịu, [rad/s]. Tốc độ góc ωe đ−ợc xác định theo chủng loại động cơ : - Đối với động ... c trung gian và tất cả các chi tiết gắn trên trục trung gian, [kg.m2]. ia : Tỷ số truyền của cặp bánh răng luôn luôn ăn khớp của hộp số. Jzk : Mô men quán tính khối l−ợng của bánh răng bị động (quay trơn trên trục thứ cấp đồng thời ăn khớp với bánh răng chủ động trên trục trung gian) của cặp bánh răng gài số thứ k, [kg.m2]. ik : Tỷ số truyền của hộp số ứng với cặp bánh răng gài số thứ k. GVC. Ths. Lê Văn Tụy - Khoa Cơ khí Giao thông - Tr−ờng Đại học Bách khoa - ĐHĐN 84 H−ớng dẫn thiết kế ôtô: (Phần truyền lực trên ôtô) - Ngành Cơ khí Ôtô m : Số l−ợng bánh răng quay trơn trên trục thứ cấp (th−ờng xuyên ăn khớp với bánh răng chủ động trên trục trung gian). Jl : Mô men quán tính khối l−ợng của bánh răng số lùi có quan hệ động học th−ờng xuyên với bánh răng trên trục trung gian cùng với các khối l−ợng quay theo khác qui dẫn về trục của nó, [kg.m2]. il : Tỷ số truyền của các bánh răng số lùi; tính từ trục sơ cấp hộp số đến bánh răng số lùi có quan hệ động học với bánh răng trên trục trung gian. ) Xác định các đại l−ợng thành phần của (2-37): a) Mômen quán tính J1: J1 = Jtr1 + Jlh Với: Jtr1 là mô men quán tính khối l−ợng của trục sơ cấp hộp số (chính là trục ly hợp) và Jlh là mô men quán tính khối l−ợng của đĩa bị động ly hợp; cũng đ−ợc xác định theo (2-36b) nh− sau: J1 = ( ) 2 RR.b.. 2 R.l.. 4 1tr 4 lhlh 4 1tr1 −ρπ+ρπ (2-37b) Ơ đây: l1 : Chiều dài trục ly hợp, theo kết quả (2-35c) ta có : l1 = 140,6 [mm]. Rtr1 : Bán kính trục ly hợp, theo kết quả (2-35) ta có : Rtr1 = 11,25 [mm]. blh : Chiều rộng trung bình đĩa bị động; có thể lấy gần đúng bằng bề dày x−ơng đĩa ly hợp. blh = 1,2 [mm] (blh ≈ 1,5 ữ 2 [mm]). Rlh : Bán kính ngoài dĩa ly hợp; theo kết quả (1-17) ta có: Rlh = 142 [mm]. Thế số vào (2-37b) ta có : J1 = ( ) 2 25,11142.5,1.10.7800. 2 25,11.6,140.10.7800. 44949 −π+π −− = 915,0048 [kg.mm2]. b) Mômen quán tính : 2a2iJ − 2 a2iJ − = (2-37c) 2a m 1k zk2tr i.JJ − = ⎟⎠ ⎞⎜⎝ ⎛ + ∑ Với: Jtr2 là mô men quán tính khối l−ợng của trục trung gian hộp số. Jzk là mô men quán tính khối l−ợng của bánh răng thứ k gắn trên trục trung gian; đã xác định với giá trị màu xanh (nét đậm) ở cột J và J’ của bảng B2- 4 có tổng bằng 2859,336 [kg.mm2]. ia là tỷ số truyền cặp bánh răng luôn ăn khớp; đã đ−ợc xác định ở B2-2. Thế số vào (2-37c) ta có: 2 a2iJ − = ( ) 249 4583,1.336,2859 2 75,12.324.10.7800. −− ⎟⎟⎠ ⎞ ⎜⎜⎝ ⎛ +π = 2151,253 [kg.mm2]. GVC. Ths. Lê Văn Tụy - Khoa Cơ khí Giao thông - Tr−ờng Đại học Bách khoa - ĐHĐN 85 H−ớng dẫn thiết kế ôtô: (Phần truyền lực trên ôtô) - Ngành Cơ khí Ôtô c) Mômen quán tính qui dẫn của các bánh răng trên trục thứ cấp Jz3: Jz3 = ∑ (2-37d) = −m 1k 2 k ' zk i.J Với: J’zk là mô men quán tính khối l−ợng của bánh răng thứ k gắn trên trục thứ cấp; giá trị màu tím (nét nghiêng đậm) ở cột J’ của bảng B2-4. ik là tỷ số truyền của số truyền thứ k hộp số; đã đ−ợc xác định ở B2-2. Thế số vào (2-37d) ta có: Jz3 = ⎟⎠ ⎞⎜⎝ ⎛ +++ 806,0 951,40 317,1 107,76 907,1 338,486 6029,3 802,1689 = 786,9602 [kg.mm2]. Với sơ đồ tính ở hình H2-2 ta có mômen quán tính khối l−ợng của các bánh răng số lùi qui dẫn về trục ly hợp bằng không (vì không có quan hệ động học th−ờng xuyên với trục ly hợp - trừ khi gài số lùi). Thế tất cả vào công thức (2-37) ta có mômen quán tính khối l−ợng tổng cộng qui dẫn về trục ly hợp bằng: J∑ = 915,0048 + 2151,253 + 786,9602 = 3853,218 [kg.mm2]. = 0,003853 [kg.m2]. 3.3.2 Mômen ma sát yêu cầu của bộ đồng tốc: Mômen ma sát yêu cầu của bộ đồng tốc đ−ợc xác định theo công thức (2-21): c kms t iJM ω∆= ∑ 2 (2-38) Trong đó : J∑ : Mô-men quán tính của bánh răng gài số và của tất cả các khối l−ợng chuyển động quay trong hộp số có quan hệ động học với trục sơ cấp hộp số (th−ờng là trục ly hợp); đ−ợc qui dẫn về trục sơ cấp, [kg.m2]. Theo kết quả vừa tính đ−ợc ở trên J∑ = 0,003853 [kg.m2]. ik : Tỷ số truyền thứ k của hộp số t−ơng ứng với chế độ tính toán của đồng tốc (tính từ trục sơ cấp đến bánh răng gài số cần tính toán). Trong ví dụ này ta tính cho bộ đồng tốc cho hai số truyền 3-2; tức là : ih3 = 1,317 và ih2 = 1,907 (bảng B2-2). ∆ω : Chênh lệch tốc độ góc giữa hai bánh răng gài số, [rad/s]. Chúng đ−ợc xác định theo (2-21b): 1 11 ± −=∆ kk eo ii ωω (2-38b) Trong đó : 1±ki : Tỷ số truyền tính từ trục sơ cấp đến trục bộ đồng tốc của hộp số ứng với số truyền vừa nhả số (để tiến hành gài số thứ ik). GVC. Ths. Lê Văn Tụy - Khoa Cơ khí Giao thông - Tr−ờng Đại học Bách khoa - ĐHĐN 86 H−ớng dẫn thiết kế ôtô: (Phần truyền lực trên ôtô) - Ngành Cơ khí Ôtô Trong ví dụ này, khi tính cho số truyền ik = ih3 thì là i1±ki h2 và ih4; còn khi tính cho số truyền ik = ih2 thì là i1±ki h3 và ih1 . ωeo : Tốc độ góc của động cơ khi bắt đầu chuyển số, [rad/s]. Giá trị này đ−ợc xác định theo bảng kinh nghiệm B2-1 nh− sau: Bảng B2-1: Tốc độ góc động cơ ωeo[rad/s] khi bắt đầu sang số. Chế độ Động cơ xăng (Carbuaratơ) Động cơ sang số Xe du lịch Xe tải và khách Diezel Từ số thấp lên số cao (0,6ữ0,7)ωN (0,7ữ0,8)ωN và ≥ ωM (0,75ữ0,85)ωN Từ số cao về số thấp (0,4ữ0,5)ωN (0,5ữ0,6)ωN, và ≥ ωM (0,9ữ1,0)ωM Trong đó : ωN, ωM t−ơng ứng là tốc độ góc của động cơ ứng với công suất cực đại, mô-men cực đại của động cơ. Với xe thiết kế là du lịch thì: + Khi chuyển từ số thấp lên số cao ta chọn: ωeo = 0,7.ωN = 0,7.586,432 = 410,5024 [rad/s]; + Khi chuyển từ số cao về số thấp ta chọn: ωeo = 0,4.ωN = 0,4.586,432 = 234,5728 [rad/s]. tc : Thời gian làm đồng đều tốc độ giữa bộ đồng tốc và bánh răng gài số, [s]. Với ôtô du lịch: tc = 0,15 ữ 0,30 [s] cho số cao và tc = 0,50 ữ 0,80 [s] cho số thấp. Chọn thời gian chuyển số cho cao (số ba ih3) là: + Từ thấp lên số cao: 0,30 [s]. + Từ số cao về số thấp: 0,20 [s] Chọn thời gian chuyển số cho thấp (số hai ih2) là: + Từ thấp lên số cao: 0,80 [s]. + Từ số cao về số thấp: 0,50 [s] Thế số vào (2-38) và (2-38b) ta có : Mms(2-3) = 3,0 1. 907,1 1 317,1 1.5024,410.317,1.003853,0 2 − = 2,14807 [N.m]. Mms(4-3) = 20,0 1. 00,1 1 317,1 1.5728,234.317,1.003853,0 2 − = 1,88827 [N.m]. GVC. Ths. Lê Văn Tụy - Khoa Cơ khí Giao thông - Tr−ờng Đại học Bách khoa - ĐHĐN 87 H−ớng dẫn thiết kế ôtô: (Phần truyền lực trên ôtô) - Ngành Cơ khí Ôtô Mms(1-2) = 8,0 1. 6029,3 1 907,1 1.5024,410.907,1.003853,0 2 − = 1,77481 [N.m]. Mms(3-2) = 5,0 1. 317,1 1 907,1 1.5728,234.907,1.003853,0 2 − = 1,54376 [N.m]. 3.3.3 Bán kính ma sát của bộ đồng tốc: Nếu gọi Rms là bán kính trung bình của vành côn ma sát bộ đồng tốc, thì mô men ma sát đ−ợc tạo ra do lực ép Q tác dụng lên đôi bề mặt ma sát của đồng tốc có quan hệ với Mms xác định theo (2-22b) nh− sau : à α . sin. Q MR msms = (2-39) Trong đó : Q : Lực ép tác dụng theo chiều trục lên đôi bề mặt ma sát, [N]. Lực ép Q do lực điều khiển P trên cần số tạo ra và đ−ợc xác định nhờ công thức (2-22c) nh− sau : (2-39b) dkdkdk .i.PQ η= Trong đó : P : Lực danh nghĩa tác dụng lên cần điều khiển. Với xe du lịch P = 70 [N]. idk : Tỷ số truyền đòn điều khiển, trong tính toán có thể lấy idk = 1,5 ữ 2,5. Chọn idk = 1,5. ηdk : Hiệu suất của cơ cấu điều khiển; có thể chọn ηdk = 0,85 ữ 0,95. Chọn ηdk = 0,85 à : Hệ số ma sát giữa đôi bề mặt ma sát. Với vật liệu của đôi bề mặt ma sát là đồng thau và làm việc trong dầu thì à ≈ 0,06 ữ 0,07. Chọn à = 0,07. α : Góc côn của đôi bề mặt ma sát (xem các hình H4-15, hình H4-16). Với vật liệu của đôi bề mặt ma sát là đồng thau thì góc côn α tốt nhất là 6 ữ 70. Chọn α = 70. Thế số vào (2-39) ta có : Rms(2-3) = 07,0.85,0.5,1.70 )180/1416.3*7sin(.14807,2 = 0,04190 [m] GVC. Ths. Lê Văn Tụy - Khoa Cơ khí Giao thông - Tr−ờng Đại học Bách khoa - ĐHĐN 88 H−ớng dẫn thiết kế ôtô: (Phần truyền lực trên ôtô) - Ngành Cơ khí Ôtô Rms(4-3) = 07,0.85,0.5,1.70 )180/1416.3*7sin(.76238,1 = 0,03683 [m] 07,0.85,0.5,1.70 )180/1416.3*7sin(.77481,1 Rms(1-2) = = 0,03462 [m] Rms(3-2) = 07,0.85,0.5,1.70 )180/1416.3*7sin(.54376,1 = 0,03011 [m] Thống nhất chọn bán kính ma sát của bộ đồng tốc 2-3 là Rms = 0,042 [m]. Chọn bán kính h∙m R β : Khi thiết kế, tuỳ thuộc vào kiểu đồng tốc (xem các hình H4-15, hình H4-16) mà giá trị trung bình của Rβ ≈ (0,75 ữ 1,25)Rms. Trong ví dụ này với xe du lịch ta chọn đồng tốc kiểu vành răng hãm (hình H4-16b). Vì vậy ta có thể chọn bán kính phản lực Rβ = 1,2.Rms = 1,2.0,042 = 0,050 [m]. 3.3.4 Chiều rộng bề mặt vành ma sát của bộ đồng tốc: Chiều rộng bề mặt vành côn ma sát bms [m] có thể xác định theo (2-23c) nh− sau: bms ≥ απ η sin.R.p..2 .i.P msN dkdkdk (2-40) Trong đó : pN là áp suất pháp tuyến hình thành ở bề mặt đôi ma sát. Với vật liệu của vành côn ma sát th−ờng đ−ợc làm bằng đồng thau và đ−ợc bôi trơn bằng dầu trong cac-te của hộp số thì giá trị áp suất làm việc cho phép nằm trong khoảng pN ≈ (1,0 ữ1,5) [MN/m2]. Chọn pN = 1,00 [MN/m 2]. Các thông số khác đã chú thích và xác định ở trên. Thế số vào (2-40) ta có : bms ≥ )180/1416.3*7sin(.042,0.10..2 85,0.5,1.70 6π ≥ 0,00278 [mm] Chọn bms = 0,005 [mm]. 3.3.5 Góc nghiêng của bề mặt h∙m β : Góc nghiêng bề mặt hãm đ−ợc xác định theo công thức (2-24) nh− sau : GVC. Ths. Lê Văn Tụy - Khoa Cơ khí Giao thông - Tr−ờng Đại học Bách khoa - ĐHĐN 89 H−ớng dẫn thiết kế ôtô: (Phần truyền lực trên ôtô) - Ngành Cơ khí Ôtô βα à β tg R Rms ≥ .sin . (2-41) Các thông số đã chú thích và đã đ−ợc tính toán ở trên. Thế số vào (2-41) ta có: β≥ tg 05,0).180/1416.3*7sin( 042,0.07,0 Hay tgβ ≤ 0,48136 Suy ra β ≤ 25,704240 Chọn β = 250 3.3.6 Tính toán kiểm tra các thông số cơ bản của đồng tốc : Khi tính toán đồng tốc theo ph−ơng pháp trình bày trên, chúng ta đã giả thiết rằng trong quá trình gài đồng tốc thì vận tốc xe không đổi. Thực tế, khi gài đồng tốc, do cắt ly hợp (hoặc giảm vị trí cung cấp nhiên liệu cho động cơ về chế độ không tải - đối với ôtô sử dụng ly hợp thủy lực) nên tốc độ xe giảm trong quá trình gài số. Do vậy các chi tiết nối với trục sơ cấp hộp số sẽ chuyển động chậm dần theo tốc độ của xe trong thời gian gài đồng tốc. Điều này sẽ làm cho chênh lệch tốc độ thực tế tăng lên khi chuyển số từ thấp lên cao; và ng−ợc lại khi chuyển số từ số cao về số thấp, chênh lệch tốc độ sẽ giảm do vậy thời gian chuyển số thực tế giảm. 3.3.6.1 Mômen ma sát thực tế của đồng tốc : Mômen ma sát thực tế của đồng tốc đ−ợc xác định theo (2-22) nh− sau: α à sin .. ms ms RQ M = (2-42) Trong đó: à : Hệ số ma sát của vành ma sát, à = 0,07. α : Góc côn của vành ma sát, α = 70. Rms : Bán kính trung bình vành côn ma sát, Rms = 0,042 [m]. Q : Lực gài tác dụng lên vành ma sát của đồng tốc [N]. Đã đ−ợc xác định ở (2-39b). Thế số ta có : Mms = )180/1416.3*7sin( 042,0.07,0.85,0.5,1.70 = 2,14807 [N.m]. 3.3.6.2 Thời gian chuyển số thực tế của đồng tốc : Thời gian chuyển số thực tế khi gài đồng tốc t−ơng ứng là : ( )ckms kc iJM iJ t ε ω 2 2 ∑ ∑ ∆= m (2-43) ở đây : GVC. Ths. Lê Văn Tụy - Khoa Cơ khí Giao thông - Tr−ờng Đại học Bách khoa - ĐHĐN 90 H−ớng dẫn thiết kế ôtô: (Phần truyền lực trên ôtô) - Ngành Cơ khí Ôtô Dấu (-) ứng với tr−ờng hợp gái số từ số thấp lên số cao. Dấu (+) ứng với tr−ờng hợp gái số từ số cao về số thấp. εc chính là gia tốc góc của trực thứ cấp do xe giảm tốc độ khi sang số. Gia tốc εc đ−ợc xác định từ quá trình giảm tốc của xe trong khi sang số : ckbx ck c R ig ηδ ψε .. ..= (2-43b) Trong đó : g là gia tốc trọng tr−ờng (g = 9,81 [m/s2]). ψ là hệ số cản tổng cộng của đ−ờng, khi tính toán chọn ψ = 0,02. ick, ηck tỷ số truyền và hiệu suất truyền lực tính từ bánh răng gài đang tính của đồng tốc đến bánh xe chủ động ôtô Rbx . Với sơ đồ bố trí đồng tốc trên trục thứ cấp thì tỷ số truyền ick = i0 = 4,3543 Chọn hiệu suất từ hộp số đến bánh xe chủ động ηck = 0,9 δ hệ số xét đến các khối l−ợng quay trong hệ thống truyền lực đến lực quá tính chuyển động tính tiến của ôtô. Có thể chọn gần đúng δ = 1,05. Rbx là bán kính bánh xe, Rbx = 0,33 [m] Thế số vào (2-43b) ta có: εc = 9,0.33,0.05,1 3543,4.02,0.81,9 = 2,7395 [rad/s2] Thế kết quả εc và các thông số đã biết vào (2-43) ta tính đ−ợc thời gian chuyển số thực tế của bộ đồng tốc nh− sau: tc(2-3) = ( ) 907,1 1317,1 17395,2.317,1.003853,014807,2 5024,410.317,1.003853,0 2 2 −− = 0,303 [s] tc(4-3) = ( ) 00,11317,1 17395,2.317,1.003853,014807,2 5728,234.317,1.003853,0 2 2 −+ = 0,174 [s] tc(1-2) = ( ) 6029,3 1907,1 17395,2.317,1.003853,014807,2 5024,410.907,1.003853,0 2 2 −− = 0,673 [s] tc(3-2) = ( ) 317,1 1907,1 17395,2.317,1.003853,014807,2 5728,234.907,1.003853,0 2 2 −+ = 0,353 [s] Thời gian sang số thực tế là phù hợp với lý thuyết tính toán và nằm trong giới hạn kinh nghiệm cho phép. 3.3.6.3 Công tr−ợt của đôi bề mặt côn ma sát của đồng tốc : Công tr−ợt do ma sát tr−ợt của đôi bề mặt ma sát đồng tốc Lms[J] có thể đ−ợc xác định theo công thức đề xuất của giáo s− Griskevich nh− sau: GVC. Ths. Lê Văn Tụy - Khoa Cơ khí Giao thông - Tr−ờng Đại học Bách khoa - ĐHĐN 91 H−ớng dẫn thiết kế ôtô: (Phần truyền lực trên ôtô) - Ngành Cơ khí Ôtô 2 t).t..(ML cccmsms ε±ω∆= (2-44) Trong đó: Mms : Mômen ma sát của đồng tốc, đ−ợc xác định theo (2-42): Mms = 2,14807[N.m] ∆ω : Chênh lệch tốc độ góc giữa hai số truyền; đ−ợc xác định theo (2-21c). εc : Gia tốc góc chậm dần, đ−ợc xác định theo (2-43b): εc = 2,7395 [rad/s2] tc : Thời gian chuyển số thực tế và đ−ợc xác định theo (2-43). Thế số đã biết vào (2-44) ta có: Lms(2-3) = 2 303,0.303,0.7395,2 907,1 1 317,1 1.5024,410.14807,2 ⎟⎟⎠ ⎞ ⎜⎜⎝ ⎛ +− = 31,59486 [J] Lms(4-3) = 2 174,0.174,0.7395,2 00,1 1 317,1 1.5728,234.14807,2 ⎟⎟⎠ ⎞ ⎜⎜⎝ ⎛ −− = 10,48703 [J] Lms(1-2) = 2 673,0.673,0.7395,2 6029,3 1 907,1 1.5024,410.14807,2 ⎟⎟⎠ ⎞ ⎜⎜⎝ ⎛ +− = 74,57095 [J] Lms(3-2) = 2 353,0.353,0.7395,2 317,1 1 907,1 1.5728,234.14807,2 ⎟⎟⎠ ⎞ ⎜⎜⎝ ⎛ −− = 20,518 [J]. 3.3.6.4 Công tr−ợt riêng của đôi bề mặt côn ma sát của đồng tốc : Công tr−ợt riêng của đồng tốc đ−ợc đánh giá bởi công tr−ợt của đôi bề mặt vành ma sát trên một đơn vị diện tích của vành ma sát theo (2-27) nh− sau: msms ms r b.R..2 Ll π= (2-45) Trong đó : Lms : Công tr−ợt của vành ma sát [J]; vừa đ−ợc xác định (2-44). Rms : Bán kính ma sát của vành ma sát, đã xác định ở (2-39): Rms = 0,042 [m]. bms : Chiều rộng bề mặt vành ma sát, vừa xác định ở (2-40): bms = 0,005 [m]. Thế số ta có: lr(2-3) = 005,0.042,0..2 59486,31 π = 23945,08 [J/m2] = 23,945 [KJ/m2]. lr(4-3) = 005,0.042,0..2 48703,10 π = 7947,901 [J/m2] = 7,948 [KJ/m2]. GVC. Ths. Lê Văn Tụy - Khoa Cơ khí Giao thông - Tr−ờng Đại học Bách khoa - ĐHĐN 92 H−ớng dẫn thiết kế ôtô: (Phần truyền lực trên ôtô) - Ngành Cơ khí Ôtô lr(1-2) = 005,0.042,0..2 57095,74 π = 56515,75 [J/m2] = 56,516 [KJ/m2]. lr(3-2) = 005,0.042,0..2 518,20 π = 15550,16 [J/m2] = 15,550 [KJ/m2]. Giá trị công tr−ợt riêng lớn nhất của đồng tốc 2-3 là 56,516 [KJ/m2] nhỏ hơn giới hạn cho phép ( ≤ 100 [KJ/m2]) đối với xe con, tải và khách cở nhỏ. GVC. Ths. Lê Văn Tụy - Khoa Cơ khí Giao thông - Tr−ờng Đại học Bách khoa - ĐHĐN 93
File đính kèm:
giao_trinh_mon_huong_dan_thiet_ke_o_to.pdf