Giáo trình Cơ sở cắt gọt kim loại - Chương 5: Hiện tượng nhiệt trong quá trình cắt
Quá trình tạo phoi và thoát phoi khỏi vùng cắt trong quá trình cắt làm xuất hiện
một lượng nhiệt nhất định. Lương nhiệt này sinh ra do sự chuyển đổi từ công cắt gọt.
Thực nghiệm chứng tỏ rằng gần như tất cả công cần thiết trong quá trình cắt đều
chuyển biến thành nhiệt trừ công biến dạng đàn hồi và công kín (công để biến dạng
mạng tinh thể và các bề mặt lớn). Khoảng gần 98% công này chuyển hoá thành nhiệt
tổng cọng phát sinh sau một phút gia công và có thể tính theo công thức sau:
Q = [Kcal/ph] (5.1)
Trong đó: Pz - thành phần lực cắt tiếp tuyến.
v - tốc độ cắt.
Nhiệt lượng cắt được định nghĩa như là lượng nhiệt được sinh ra trong quá trình
cắt sau một phút. Đó chính là công suất nhiệt khi cắt. Còn lượng nhiệt có trên một đơn
vị thể tích hay khối lượng của vật thể được cắt gọi là nhiệt lượng đơn vị (Cal/cm3;
Cal/g).
Nhiệt lượng sinh ra khi cắt làm nóng chi tiết gia công, phoi và dụng cụ cắt.
Nhiệt độ tại các điểm khác nhau có sự tác động của lượng nhiệt khác nhau và gọi là
nhiệt độ cắt tức thời của các điểm khối lượng khảo sát trong vùng cắt. Trung bình cọng
đại số của nhiệt độ các điểm khối lượng của phoi gọi là nhiệt độ trung bình của phoi.
Tương tự ta có nhiệt độ trung bình của dụng cụ và chi tiết gia công. Nhiệt độ trung
bình trên các bề mặt tiếp xúc của vật liệu gia côngvà vật liệu cắt gọi là nhiệt độ cắt, qui
ước gọi tắt là nhiệt cắt.
Tóm tắt nội dung tài liệu: Giáo trình Cơ sở cắt gọt kim loại - Chương 5: Hiện tượng nhiệt trong quá trình cắt
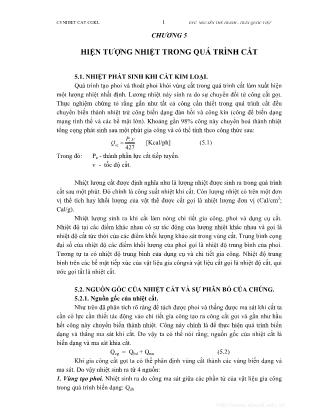
C5 NHIET CAT CGKL 1 GVC NGUYỄN THẾ TRANH - TRẦN QUỐC VIỆT CHƯƠNG 5 HIỆN TƯỢNG NHIỆT TRONG QUÁ TRÌNH CẮT 5.1. NHIỆT PHÁT SINH KHI CẮT KIM LOẠI. Quá trình tạo phoi và thoát phoi khỏi vùng cắt trong quá trình cắt làm xuất hiện một lượng nhiệt nhất định. Lương nhiệt này sinh ra do sự chuyển đổi từ công cắt gọt. Thực nghiệm chứng tỏ rằng gần như tất cả công cần thiết trong quá trình cắt đều chuyển biến thành nhiệt trừ công biến dạng đàn hồi và công kín (công để biến dạng mạng tinh thể và các bề mặt lớn). Khoảng gần 98% công này chuyển hoá thành nhiệt tổng cọng phát sinh sau một phút gia công và có thể tính theo công thức sau: . 427 z cg P vQ = [Kcal/ph] (5.1) Trong đó: Pz - thành phần lực cắt tiếp tuyến. v - tốc độ cắt. Nhiệt lượng cắt được định nghĩa như là lượng nhiệt được sinh ra trong quá trình cắt sau một phút. Đó chính là công suất nhiệt khi cắt. Còn lượng nhiệt có trên một đơn vị thể tích hay khối lượng của vật thể được cắt gọi là nhiệt lượng đơn vị (Cal/cm3; Cal/g). Nhiệt lượng sinh ra khi cắt làm nóng chi tiết gia công, phoi và dụng cụ cắt. Nhiệt độ tại các điểm khác nhau có sự tác động của lượng nhiệt khác nhau và gọi là nhiệt độ cắt tức thời của các điểm khối lượng khảo sát trong vùng cắt. Trung bình cọng đại số của nhiệt độ các điểm khối lượng của phoi gọi là nhiệt độ trung bình của phoi. Tương tự ta có nhiệt độ trung bình của dụng cụ và chi tiết gia công. Nhiệt độ trung bình trên các bề mặt tiếp xúc của vật liệu gia côngvà vật liệu cắt gọi là nhiệt độ cắt, qui ước gọi tắt là nhiệt cắt. 5.2. NGUỒN GỐC CỦA NHIỆT CẮT VÀ SỰ PHÂN BỐ CỦA CHÚNG. 5.2.1. Nguồn gốc của nhiệt cắt. Như trên đã phân tích rõ ràng để tách được phoi và thắng được ma sát khi cắt ta cần có lực cần thiết tác động vào chi tiết gia công tạo ra công cắt gọt và gần như hầu hết công này chuyển biến thành nhiệt. Công này chính là để thực hiện quá trình biến dạng và thắng ma sát khi cắt. Do vậy ta có thể nói rằng; nguồn gốc của nhiệt cắt là biến dạng và ma sát khia cắt. Qcg = Qbd + Qms (5.2) Khi gia công cắt gọt ta có thể phân định vùng cắt thành các vùng biến dạng và ma sát. Do vậy nhiệt sinh ra từ 4 nguồn: 1. Vùng tạo phoi. Nhiệt sinh ra do công ma sát giữa các phần tử của vật liệu gia công trong quá trình biến dạng: Qdh C5 NHIET CAT CGKL 2 GVC NGUYỄN THẾ TRANH - TRẦN QUỐC VIỆT Nếu xem vùng tạo phoi như là một mặt trượt duy nhất thì qua nghiên cứu lượng nhiệt này có thể xác định qua biểu thức sau: 1. 427 c c dh P vQ = (5.3) Trong đó: Pc - lực theo phương trượt vc1 - vận tốc trượt. 2. Vùng tiếp xúc của phoi và mặt trước dao. Nhiệt sinh ra do công biến dạng đàn hồi và ma sát ngoài: Qdm Lượng nhiệt xuất hiện trên mặt trước dao là do 2 nguồn: do tác dụng của lực ma sát trong ở lớp vật liệu phoi gần sát mặt trước kháng lại biến dạng đàn hồi và lực ma sát ngoài trên mặt tiếp xúc. 3. Vùng tiếp xúc của mặt sau dao và mặt cắt của chi tiết gia công. Nhiệt sinh ra do sự chuyển đổi công ma sát: Qms 4. Nhiệt sinh ra do công đứt phoi: Qdp 5.2.2. Sự phân bố nhiệt cắt. Các lượng nhiệt sinh ra được truyền và phân tán vào phoi Qf, dụng cụ cắt Qd, chi tiết gia công Qct và môi trường Qmt. Từ điều kiện cân bằng nhiệt ta có thể viết: Qdh + Qdm + Qms + Qdp = Qf + Qd + Qct + Qmt (5.4) Phương trình (5.4) được gọi là phương trình thu phát nhiệt trong quá trình cắt. phoi dao chi tiết v Hình 5.1- Nguồn gốc và sự phân bố nhiệt cắt C5 NHIET CAT CGKL 3 GVC NGUYỄN THẾ TRANH - TRẦN QUỐC VIỆT Sơ đồ trên mô tả tổng quát hướng các nguồn nhiệt trong phoi cắt, dụng cụ, chi tiết gia công và ngoài môi trường. 1. Nhiệt truyền vào phoi cắt. Lượng nhiệt phoi nhận được được truyền từ 2 nguồn nhiệt: nguồn Q5 của vùng biến dạng trượt (mặt tạo phoi) và nguồn Q6 trên mặt trước dao. lượng nhiệt này chiếm khoảng 75% tổng lượng nhiệt sinh ra khi cắt Qcg. 2. Nhiệt truyền vào dụng cụ. Một phần lượng nhiệt Q3 sinh ra trên bề mặt tiếp xúc của phoi với mặt trước dao cùng với một phần lượng nhiệt Q4 khác sinh ra từ ma sát của bề mặt sau dao với bề mặt cắt truyền vào dụng cụ khi cắt. Lượng nhiệt này chiếm khoảng 20% Qcg. 3. Nhiệt truyền vào chi tiết gia công. Có hai dòng nhiệt hướng vào chi tiết gia công đó là: q1 và q2. Lượng nhiệt chi tiết nhận được Q1 từ dòng nhiệt sinh ra trong mặt trượt q1 và lượng nhiệt Q2 từ dòng nhiệt sinh ra từ mặt sau dao q2. Lượng nhiệt này chiếm khoảng 4% Qcg. 4. Nhiệt truyền vào môi trường. Một phần nhiệt khác của quá trình cắt truyền từ bề mặt tự do của phoi, dụng cụ và chi tiết gia công vào môi trường chung quanh Q7, Q8, Q9 . Lượng nhiệt này phụ thuộc vào nhiều yếu tố như lượng dung dịch trơn nguội tưới vào vùng cắt, tốc độ cắt, chiều dày lớp cắt... Sự phân tích lý thuyết tóm tắt về sự thu phát nhiệt của quá trình cắt giúp đánh giá ảnh hưởng của các thông số cơ bản của cắt gọt đến sự xuất hiện và sự dẫn nhiệt khi Chi tiết gia công Dụng cụ Phoi x x y1 y q1 q5 q2 q4 q3 q6 q9 q8 q7 q10 Hình 5.2- Sơ đồ hướng các nguồn nhiệt C5 NHIET CAT CGKL 4 GVC NGUYỄN THẾ TRANH - TRẦN QUỐC VIỆT cắt. Tuy nhiên việc xác định sự thu nhận nhiệt và truyền phát nhiệt bằng tính toán là rất khó và không chính xác. Tóm lại mỗi nguồn nhiệt sinh ra có một phạm vi tác dụng nhất định. Phần lớn nhiệt lượng sinh ra do biến dạng trên mặt cắt (biến dạng trượt) nằm lại trong phoi nhưng phoi lại thoát ra ngoài, một phần nhỏ truyền sang dụng cụ cắt nhưng dụng cụ lại luôn nằm trong vùng cắt. Các kết quả thực nghiệm nghiên cứu về nhiệt cắt cho ta một số nhận xét sau: • Khi tăng tốc độ cắt, lượng nhiệt truyền vào dao giảm. Đó là do sự chậm trễ của tốc độ truyền nhiệt so với tốc độ chuyển đọng của phoi. Tức là vì thời gian để thoát phoi rất ngắn nên nhiệt chưa kịp truyền sang dao. • Khi gia công thép chịu nhiệt, lượng nhiệt truyền vào dao tăng lên nhiều hơn so với khi gia công thép kết cấu. Điều đó là vì thép chịu nóng có sức bền và độ dẻo cao hưon nên công cắt lớn và do đó lượng nhiệt sinh ra lớn, đồng thời các loại thép chịu nhiệt đều có tính dẫn nhiệt kém. Tuy rằng lượng nhiệt truyền vào dao không nhiều nhưng do tính truyền nhiệt của vật liệu làm dao thấp và do dao liên tục tiếp xúc với vùng sinh nhiệt nên nhiệt độ trên dao thường cao hơn so với nhiệt độ trung bình của phoi và chi tiết. 5.3. ẢNH HƯỞNG CỦA NHIỆT CẮT ĐẾN QUÁ TRÌNH CẮT. Ảnh hưởng của nhiệt cắt đến quá trình cắt thường được nghiên cứu theo 3 quan điểm: • Theo độ chính xác gia công. • Theo chất lượng bề mặt đã gia công. • Theo khả năng cắt của dao. 5.3.1. Ảnh hưởng của nhiệt cắt đến độ chính xác gia công. Độ chính xác gia công khi cắt gọt được quyết định bởi vị trí tương quan giữa dao và chi tiết gia công trong quá trình cắt. Do vậy sự biến dạng về nhiệt của dao và chi tiết gia công do ảnh hưởng của nhiệt khi cắt được quan tâm khảo sát. Về quá trình trao đổi nhiệt, ta biết rằng nếu cung cấp một lượng nhiệt Q cho một vật có thể tích V (cm3), tỷ nhiệt c (J/kg.0K), khối lượng riêng γ (kg/cm3), thì độ tăng của nhiệt độ của vật thể được xác định: 0Qθ = ( ) c.γ.V KΔ (5.5) Độ thay đổi chiều dài L theo phương nào đó của vật thể là: ΔL = α.Δθ.L (mm) (5.6) Như vậy nếu ta xét trường hợp khi tiện một chi tiết có được đường kính là D theo thiết kế trên bản vẽ , nếu nhiệt lượng truyền vào cho chi tiết là Qct thì nhiệt độ trên chi tiết sẽ tăng lên một lượng Δθ xác định và đường kính của chi tiết sẽ thay đổi một lượng là ΔD: C5 NHIET CAT CGKL 5 GVC NGUYỄN THẾ TRANH - TRẦN QUỐC VIỆT ΔD = α.Δθ.D (mm) (5.7) Mặt khác, nhiệt lượng Qd truyền vào dụng cụ cũng sẽ làm cho dụng cụ tăng chiều dài về phía tâm chi tiết. Khác với chi tiết, vật liệu trên dao là không đồng nhất giữa phần cắt và phần cán dao, do vậy sự biến dạng của dao theo chiều dài dưới tác dụng của nhiệt cắt phức tạp hơn rất nhiều. Ỏ đây ta phải khảo sát biến dạng dài của dao trong mối quan hệ phức hợp: dL = f(L,F,σ ,v,s,t...)Δ (5.8) trong đó: F - là tiết diện thân dao σd - là độ bền vật liệu dao. v,s,t - là chế độ cắt. Sau quá trình cắt, khi chi tiết về nhiệt độ thường, đường kính thực tế của chi tiết gia công sẽ là: tD = D - (α.Δθ.D + ΔL) (5.9) 5.3.2. Ảnh hưởng của nhiệt cắt đến chất lượng bề mặt gia công. Chất lượng bề mặt đã gia công của chi tiết được đặc trưng bởi độ nhấp nhô bề mặt và tính chất cơ - lý lớp sát bề mặt. Nhiệt cắt có ảnh hưởng chủ yếu đến sự thay đổi tính chất cơ - lý lớp bề mặt chi tiết gia công. Ta biết rằng, khi kim loại bị đốt nóng đến một nhiệt đọ nào đó thi tổ chức kim tương của chúng sẽ thay đổi. Sự thay đổi này dẫn đến sự thay đổi về cơ - lý tính của kim loại. Mặt khác, trong quá trình cắt sự tăng giảm đột ngột về nhiệt độ trên bề mặt gia công kết hợp với sự dao động của lực cắt sẽ tạo nên ứng suất dư và vết nứt tế vi trên lớp kim loại sát trên bề mặt, đồng thời trên đó kim loại cũng bị biến cứng hay hoá bền. Nói chung các ảnh hưởng này đều theo chiều hướng bất lợi cho yêu cầu về cắt gọt. 5.3.3. Ảnh hưởng của nhiệt cắt đến khả năng làm việc của dao. Những kết quả nghiên cứu về cắt gọt cho thấy rằng khi cắt kim loại, đặc biệt khi cắt ở tốc độ cao thì yếu tố quyết định lớn nhất đến khả năng cắt của dao đó là nhiệt cắt, tiếp đến mới là ma sát. Khả năng cắt gọt của dao được đánh gía bởi tuổi bền dao thông qua việc xác định độ lớn của các dạng mài mòn dao cụ thể. Dưới tác dụng của nhiệt khi cắt vật liệu của dao sẽ có sự thay đổi về tính chất cơ - lý - hoá, đặc biệt độ cứng, độ bền giảm, tính chống mòn cũng giảm... dẫn đến mài mòn dao nhanh chóng, hậu quả là thời gian sử dụng dao vào cắt gọt cũng bị rút ngắn đi, dao nhanh chóng mất khả năng cắt gọt. Tóm lại, nhiệt cắt ngoài ảnh hưởng trực tiếp đến độ chính xác gia công, chất lượng lớp bề mặt gia công và khả năng cắt gọt của dao, còn ảnh hưởng đáng kể đến máy và đồ gá trong hệ thống công nghệ. C5 NHIET CAT CGKL 6 GVC NGUYỄN THẾ TRANH - TRẦN QUỐC VIỆT 5.4. CÁC PHƯƠNG PHÁP XÁC ĐỊNH NHIỆT CẮT. Qua nghiên cứu và từ thực tế cắt gọt ta thấy rằng nhiệt cắt có ảnh hưởng rất lớn đến quá trình cắt, do vậy cần phải xác định được độ lớn của chúng trong những trường hợp cắt gọt cụ thể. Tuỳ thuộc vào mục đích nghiên cứu mà ta có thể xác định nhiệt cắt trên dao, trên chi tiết, trên phoi hoặc ở môi trường chung quanh. Sự phân tích lý thuyết về sự thu nhận nhiệt của quá trình cắt cho khả năng đánh giá đựoc ảnh hượng của các thông số cơ bản có liên quan đến quá trình cắt đến sự xuất hiện và sự dẫn nhiệt khi cắt, tuy nhiên việc xác định sự thu nhận nhiệt bằng tính toán là rất khó và không chính xác nên chỉ thường được áp dụng khi việc đo đạc nhiệt độ trực tiếp khó khăn hoặc không thể tiến hành được. Ngày nay với sự phát triển của các ngành khoa học, kỹ thuật đo nhiệt nói chung và đo nhiệt cắt nói riêng ngày càng hoàn hảo. Do vậy việc xác định nhiệt cắt bằng cách đo là phổ biến. Tuy nhiên với mục tiêu nghiên cứu, người ta còn tiến hành xác định nhiệt cắt bằng tính toán. 5.4.1. Xác định nhiệt cắt bằng phương pháp đo. Việc đo nhiệt cắt có thể thực hiện theo nhiều phương pháp. 1. Đo nhiệt cắt thông qua đo nhiệt lượng phoi cắt. Phương pháp này đơn giản, dễ sử dụng và thực hiện nhưng kết quả đo ít chính xác. Dựa vào định luật bảo toàn năng lượng: trong hệ cân bằng về nhiệt thì lượng nhiệt toả ra bằng lượng nhiệt thu vào, ta xây dựng hệ thống thí nghiệm như sau: Dùng bình đựng nước 1 có ống 2 để hứng phoi khi cắt. Bình được cách nhiệt với môi trường nhờ lớp chân không giữa bình và võ 3. Nước trong bình 1 được xác 1 2 3 4 4 Hình 5.3 - Dụng cụ do nhiệt độ phoi C5 NHIET CAT CGKL 7 GVC NGUYỄN THẾ TRANH - TRẦN QUỐC VIỆT định có khối lượng mn, tỷ nhiệt cn với nhiệt độ ban đầu θ0. Bình được đặt sát vào vị trí cắt và trực tiếp hứng lấy phoi cắt rơi xuống. Nhiệt lượng từ phoi sẽ toả ra làm cho nhiệt độ nước trong bình tăng lên khi hệ cân bằng về nhiệt ta đo được nhiệt độ của toàn hệ bằng nhiệt kế 4. Để đảm bảo nhiệt độ trong bình đồng đều dùng cánh khuấy 5 để khuấy nước. Nếu gọi nhiệt độ của phoi khi cắt cần xác định là θf và nhiệt độ nhiệt kế đo được khi hệ cân bằng là θk, khối lượng phoi trong bình hứng được là mf, tỷ nhiệt cf. Theo nguyên lý cân bằng nhiệt lượng thì nhiệt lượng phoi toả ra bằng nhiệt lượng nước nhận được, do vậy ta có: 0. ( ) . ( )f f f k n n kc m c mθ θ θ θ− = − Suy ra: 0 . ( ) . n n f k k f f m c m c θ θ θ θ= − + (5.10) 2. Đo nhiệt cắt dựa theo nguyên lý pin nhiệt điện (cặp ngẫu nhiệt) Nguyên lý của phương pháp này dựa trên hiện tượng nhiệt điện. Khi nung nóng đầu nối của hai dây dẫn từ hai kim loại khác nhau thì xuất hiện trên đầu cuối tự do của dây dẫn một lực nhiệt điện động tỷ lệ thuận với nhiệt độ của chỗ nối. Từ đó suy ra bằng việc đo lực nhiệt điện động có thể xác định nhiệt độ tại vùng tiếp xúc của hai kim loại này. Tại đầu dây đầu nối bị nung nóng làm cho có sự trao đổi điện tích nên trong dây dẫn xuất hiện các điện tích khác dấu, nếu nối kín mạch thì trong mạch sẽ sinh một dòng nhiệt điện; ta có thể dùng mili volt kế để đo điện thế trong mạch. Theo nguyên lý này, việc đo nhiệt cắt có thể theo nhiều phương án khác nhau. a. Phương án pin nhân tạo (hai kim loại riêng biệt). Khoan vào dụng cụ một lỗ có đường kính khoảng 1-2mm sát mũi dao và cách mặt trước dao khoảng f=0,2mm. Đặt vào đáy lỗ khoan đầu nóng của cặp pin nhiệt điện ví dụ như cặp kim loại sắt và konstantan. Cặp pin nhiệt điện được cách điện với dao. Hai đầu nguội được nối với đồng hồ mV kế. Thông qua hiệu điện thế đọc được trên đồng hồ ta xác định được nhiệt độ tại điểm sát đáy lỗ. ● ● ● kim loại A kim loại B điểm nóng (đầu nối) θ2 các điểm lạnh (hai đầu tự do) θ1 miliVolt-kế Hình 5.4 - Cặp ngẫu nhiệt (pin nhiệt điện) C5 NHIET CAT CGKL 8 GVC NGUYỄN THẾ TRANH - TRẦN QUỐC VIỆT Phương án này có ưu điểm là đo được nhiệt độ tại bất kỳ điểm nào trên dao, chi tiết. Nhưng có nhược điểm lớn là việc chuẩn bị công phu và phức tạp, số lần thí nghiệm bị hạn chế do mặt trước bị mòn, nhiệt độ đo được không phải trên mặt trước dao như mong muốn. b. Phương án pin nửa nhân tạo (có một kim loại ngoại lai) c. Phương án pin tự nhiên. Trong phương án này cả hai thành phần của pin đều do vật liệu dao và vật liệu gia công tạo nên. Lực nhiệt điện động xuất hiện tỷ lệ thuận với nhiệt độ trung bình của các điểm tiếp xúc giữa vật liệu gia công và vật liệu dao. Phương án này cần phải cách điện dụng cụ và chi tiết đồng thời chú ý để nhiệt độ của những điểm giữa vật liệu gia công và vật liệu làm dao, nơi nối máy đo, trong suốt thời gian đo là hằng số. Những dụng cụ thoả mãn tốt nhất điều kiện đo này là dụng cụ nguyên khối vật liệu, nếu dùng dụng cụ có gắn các mảnh hợp kim cứng thì nơi nối vật liệu dao và thân Hình 5.5 - Sơ đồ đo nhiệt cắt bằng pin nhân tạo Dao cũng được khoan lỗ chuẩn như trên, đặt vào lỗ khoan dây konstantan hàn dính tại đáy lỗ và được cách điện cách nhiệtvới kim loại dao. Sự khác nhau cơ bản của phương án này là một phần tử của ngẫu nhiệt là vật liệu dụng cụ hay là chi tiết, phần thứ hai là kim loại dây. Ưu điểm của phương án này là đo được nhiệt độ trên sát mặt trước dao nhưng không đo được nhiệt độ sát lưỡi cắt dao. Hình 5.6 - Đo nhiệt cắt bằng pin bán nhân tạo C5 NHIET CAT CGKL 9 GVC NGUYỄN THẾ TRANH - TRẦN QUỐC VIỆT dao bị nung nóng và xuất hiện “ngẫu nhiệt ký sinh” làm cho kết quả đo bị sai lệch. Tuy nhiên phương án này có nhược điểm là đối với một cặp vật liệu dao và chi tiết đều phải lập sơ đồ chuẩn trước khi đo. Có thể điều chỉnh đo nhiệt độ bằng ngẫu nhiệt trực tiếp (pin tự nhiên) bằng phương án hai dao. Cặp ngẫu nhiệt được tạo thành bằng hai vật liệu làm dao khác nhau của hai dao cùng vào cắt. Vật liệu gia công tạo giữa hai dao một cầu dẫn điện. Các dao sử dụng phải được cách điện, cách nhiệt. Khi cắt phải đảm bảo cůng chế độ cắt và phải giữ hai điểm nguội có nhiệt độ như nhau và không đổi. Phương án này chỉ cần tiến hành lập đồ thị chuẩn khi thay cặp dao, còn khi thay chi tiết thì không cần. d. Đo nhiệt cắt theo nguyên lý quang học. Ở phương pháp này khi cắt tia nhiệt phát ra từ một điểm nhất định của trường nhiệt độ của chi tiết hay dụng cụ được bắt bởi hai thấu kính và các thiết bị tập trung tia nhiệt, nhận cường độ tia quang nhiệt, pin nhiệt và đồng hồ đo. Hình 5.8 - Hiện tượng ngẫu nhiệt ký sinh Hình 5.7 - Đo nhiệt cắt bằng pin tự nhiên 1 dao Hình 5.9 - Đo nhiệt cắt bằng pin tự nhiên 2 dao C5 NHIET CAT CGKL 10 GVC NGUYỄN THẾ TRANH - TRẦN QUỐC VIỆT Thuận lợi chính của phương pháp này là có thể cho phép đạt được tính tổng quan về nhiệt độ của những vị trí khác nhau của chi tiết gia công, dao và phoi, khi mà các phương pháp trước đây không đo được. Nhưng phương pháp này có nhược điểm là khó điều chỉnh, lắp đặt khó khăn và dụng cụ tương đối phức tạp. Ngoài ra ta có thể đo nhiệt bằng tế bào quang. Ở dây phần tử nhận nhiệt là tế bào quang ví dụ PbS (sunfit chì), thực chất là điện trở mà khi lộ sáng phóng xạ thì nó thay đổi điện trở không đáng kể. Trước hết tế bào nhìn thấy qua lỗ trên nguồn sáng. Nguồn sáng được đặt ở khoảng cách khá xa để đảm bảo các tia sáng song song. Vì dụng cụ tiến về phía trước do đó bề mặt trượt đi đến đúng lỗ và bịt nó phía trên, cắt mất nguồn sảng và tạo ra sự thay đổi điện thế trong tế bào quang. Hiện nay người ta còn dùng các dụng cụ đo nhiệt bằng phương pháp chụp ảnh qua tia hồng ngoại, dụng cụ đo băng tia lazer. Hình 5.11 - Sơ đồ vàmạch điện để đo nhiệt cắt bằng tế bào quang Hình 5.10 - Đo nhiệt cắt theo nguyên lý quang học C5 NHIET CAT CGKL 11 GVC NGUYỄN THẾ TRANH - TRẦN QUỐC VIỆT 5.4.2. Xác định nhiệt cắt bằng phương pháp tính toán. Việc tính toán nhiệt cắt cũng được thực hiện bằng hai hướng: - Tính toán bằng những công thức lý thuyết. - Tính toán bằng những phương trình thực nghiệm. 1. Tính toán nhiệt cắt theo lý thuyết. Nhiều công trình lý thuyết về tính toán nhiệt cắt đã được nghiên cứu và cho ta các công thức tính toán nhiệt độ cắt xuất hiện trên chi tiết, phoi hay dao. Qua khảo sát người ta thấy rằng trường nhiệt độ của phoi, dụng cụ và chi tiết khi gia công nói chung là không ổn định. Sự phân bố ổn định nhiệt độ đạt được chỉ sau khi cắt một thời gian nhất định thường từ 2 - 15 phút. Trên cơ sở về lý thuyết quá trình tuyền nhiệt ta có thể xác định sự phân bố nhiệt trong phoi, dụng cụ và chi tiết gia công bằng cách giải phương trình vi phân tổng quát truyền nhiệt trong chất rắn (phương trình nhiệt vật lý cắt gọt). Có thể viết phương trình quá trình truyền nhiệt trong không gian và thời gian dưới dạng: 1 ( ) ( ) ( ) x y zV V Vc x x y y z z x y z θ θ θ θ θ θ θα θ α θ α θτ ρ ⎧ ⎫⎡ ⎤∂ ∂ ∂ ∂ ∂ ∂ ∂ ∂ ∂ ∂⎡ ⎤ ⎡ ⎤= + + + + +⎨ ⎬⎢ ⎥⎢ ⎥ ⎢ ⎥∂ ∂ ∂ ∂ ∂ ∂ ∂ ∂ ∂ ∂⎣ ⎦ ⎣ ⎦⎣ ⎦⎩ ⎭ trong đó: c - là nhiệt lượng riêng của vật nhận nhiệt. ρ - là khối lượng riêng của vật nhận nhiệt. α(θ) - là hệ số dẫn nhiệt. θ - là nhiệt độ vật nhận đựơc. τ - là thưòi gian truyền nhiệt. x, y, z - là các phương truyền nhiệt. Vx, Vy, Vz - là các vectơ truyền nhiệt theo các phương tương ứng. Hình 5.12 - Phương pháp chụp ảnh Hình 5.13 - Phương pháp đo nhiệt bằng lazer C5 NHIET CAT CGKL 12 GVC NGUYỄN THẾ TRANH - TRẦN QUỐC VIỆT Phương trình trên có thể viết lại dưới dạng phương trình vi phân dẫn nhiệt theo nhiệt động học là: ( )1 . ( ). vQdiv grad c c θ α θ θτ ρ ρ ∂ = +∂ Nếu xem hệ số dẫn nhiệt α(θ) là hằng số và nguồn nhệt bên trong Qv không tồn tại (thực tế trong cắt gọt không có nguồn nội nhiệt này), ta có thể viết phương trình vi phân dưới dạng: .aθ θτ ∂ = Δ∂ trong đó: 1a cρ= và 2 2 2 2 2 2x y z θ θ θθ ∂ ∂ ∂Δ = + +∂ ∂ ∂ Phương trình này có vế trái biểu thị sự biến thiên của nhiệt độ theo thời gian, vế phải biểu thị sự biến thiên của nhiệt độ trong không gian. Hình 5.14 - Trường nhiệt độ của dụng cụ Hình 5.15 - Trường nhiệt độ của chi tiết Hình 5.16 - Phân bố nhiệt trên mặt trước dao Hình 5.17 - Phân bố nhiệt trên mặt sau dao C5 NHIET CAT CGKL 13 GVC NGUYỄN THẾ TRANH - TRẦN QUỐC VIỆT Phương trình này có các nghiệm khác nhau cho các điều kiện biên khác nhau liên quan đến thời gian và không gian trong phoi, dụng cụ và chi tiết. Theo kết quả nghiên cứu quá trình cắt, nhiệt độ của phoi tại điểm cụ thể ở khoảnh khắc tức thời có thể coi là kết quả tác động của hai nguồn nhiệt: nguồn trên mặt cắt (mặt trượt) biến dạng đàn hồi bậc nhất và nguồn ma sát trên mặt trước dao. Do vậy ở đây chỉ tính sự dẫn nhiệt trong một hướng duy nhất đó là hướng trục x, tức là theo chiều dày của phoi. Giải phương trình: 2 2.a x θ θ τ ∂ ∂=∂ ∂ với các điều kiện biên thích hợp ta sẽ thu được nghiệm đó là nhiệt độ tại một điểm trên mặt trước dao hay điểm cần khảo sát trên phoi. 2. Tính toán nhiệt cắt theo phương trình thực nghiệm. Các công thức tính nhiệt cắt theo lý thuyết chủ yếu dùng trong công tác nghiên cứu. Trong thực tế việc tính nhiệt cắt có thể thực hiện một cách đơn giản hơn bằng các phương trình kinh nghiệm. Các phương trình kinh nghiệm này được xây dựng trên cơ sở nghiên cứu và khảo sát ảnh hưởng của các điều kiện cắt gọt như vật liệu gia công, dụng cụ cắt, chế độ cắt và một số các yếu tố khác đến nhiệt cắt bằng thực nghiệm. a. Ảnh hưởng của vật liệu gia công đến nhiệt cắt. Các tính chất về cơ học và nhiệt của vật liệu gia công có ảnh hưởng đáng kể đến nhiệt cắt. Nhiệt cắt thấp hơn khi gia công hợp kim so với khi gia công thép nhờ khả năng biến dạng nhỏ hơn của hợp kim. Có thể nhận xét một cách tổng quát rằng khi cắt vật liệu giòn do công biến dạng rất bé và lực cắt đơn vị không đáng kể nên nhiệt cắt thấp hơn khi cắt vật liệu dẻo. Độ cứng và độ bền của vật liệu gia công càng lớn thì nhiệt cắt càng lớn do có quan hệ với công biến dạng. Nhiệt cắt cơ bản phụ thuộc vào nhiệt dung và đặc biệt phụ thuộc vào tính chất dẫn nhiệt của vật liệu gia công và vật liệu làm dao. Ảnh hưởng của vật liệu gia công đến nhiệt cắt trong điều kiện thí nghiệm cắt với a=1mm, b=1mm và v=1m/ph được biểu thị bằng hằng số thực nghiệm Cθ. b. Ảnh hưởng của vật liệu làm dao đến nhiệt cắt. Vật liệu làm dao cũng có đặc tính tương tự như vật liệu chi tiết gia công. Loại vật liệu dao nào có tính dẫn nhiệt tốt thì khi cắt nhiệt cắt sẽ thấp và ngược lại. Yếu tố quyết định của dao về cao thấp của nhiệt cắt sinh ra là cấu trúc thành phần hoá học của vật liệu xác định tính tương đồng hoá học của nó với vật liệu gia công, mặt khác là lý tính của nó như tính dẫn nhiệt và hệ số ma sát. Ảnh hưởng của tính dẫn nhiệt sẽ tăng khi tăng tốc độ cắt, giảm góc cắt, giảm chiều dày phoi. Với tốc độ cắt thấp thì ảnh hưởng của độ dẫn nhiệt nhỏ. Kích thước thân dao cũng có ảnh hưởng như vậy đến nhiệt cắt vì nó ảnh hưởng đến khả năng dẫn nhiệt của dụng cụ cắt. Kích thước càng lớn thì nhiệt sinh ra khi cắt càng thấp. C5 NHIET CAT CGKL 14 GVC NGUYỄN THẾ TRANH - TRẦN QUỐC VIỆT c. Ảnh hưởng của tốc độ cắt. Giá trị số mũ xθ phụ tuộc vào vật liệu gia công và vùng vận tốc cắt. Khi v=15-45 m/ph thì xθ = 0,5 đối với gia công thép và xθ = 0,35-0,45 đối với gia công gang. Khi v=45-180 m/ph thì xθ = 0,23 đối với gia công thép và xθ = 0,18 đối với gia công gang. d. Ảnh hưởng của chiều dày cắt. Chiều dày cắt ảnh hưởng đến nhiệt cắt ít hơn so với vận tốc cắt. Khi tăng chiều dày a hay lượng chạy dao s thì nhiệt cắt tăng nhưng không phải tăng tuyến tính. Giá trị trung bình của số mũ yθ từ thực nghiệm: Đối với thép: yθ = 0,3; gang: yθ = 0,2. Trong các yếu tố cắt thì tốc độ cắt là yếu tố có ảnh hưởng lớn nhất đến nhiệt cắt. Khi tăng tốc đọ cắt thì nhiệt cắt lúc đầu tăng nhanh, sau khi đã đạt được độ lớn nhất định thì cường độ tăng chậm lại và đường cong của hàm số phụ thuộc θ = f(v) gần tiệm cận với nhiệt độ nóng chảy của vật liệu gia công. Bằng thực nghiệm ta có thể thiết lập được mối quan hệ giữa nhiệt cắt và tốc độ cắt theo công thức sau: . xvC v θθθ = Hình 5.18 - Quan hệ giữa θ và v Hình 5.19 - Quan hệ giữa chiều dày cắt a đến nhiệt cắt Khi tăng lượng chạy dao (cũng như tăng a) áp lực của phoi trên dao tăng, công ma sát trên mặt trước tăng, nhiệt cắt ở vùng biến dạng bậc nhất tăng, tuy nhiên hệ số co rút phoi giảm, tổng công biến dạng cho một đơn vị thể tích giảm, điều kiện truyền nhiệt tốt hơn vì chiều dày phoi lớn lên và diện tích tiếp xúc giữa dao vbà phoi được mở rộng, nhiệt cắt vì vậy có tăng nhưng không tăng nhanh như khi tăng tốc độ cắt. Bằng thực nghiệm ta có thể thiết lập được mối quan hệ giữa nhiệt cắt và chiều dày cắt theo công thức sau: . yaC a θθθ = C5 NHIET CAT CGKL 15 GVC NGUYỄN THẾ TRANH - TRẦN QUỐC VIỆT e. Ảnh hưởng của chiều rộng cắt. Chiều rộng cắt b (hay chiều sâu cắt t) có ảnh hưởng đến nhiệt cắt ít hơn so với lượng chạy dao. f. Ảnh hưởng của các thông số hình học dao. Góc nghiêng chính φ, bán kính mũi dao R cũng ảnh hưởng tới độ lớn của nhiệt cắt, ta dễ dàng nhận biết qua sự thay đổi của chiều dày cắt a và chiều rộng cắt b dẫn đến sự thay đổi mức độ biến dạng và khả năng tản nhiệt. Để đặc trưng các ảnh hương này đến nhiệt cắt ta dùng các hệ số điều chỉnh nhiệt cắt Kφθ và KRθ. Ngoài ra sự mài mòn của dụng cụ làm thay đổi hình dáng hình học phần cắt và góc độ dao cũng làm cho nhiệt cắt thay đổi. Nói chung dụng cụ càng bị mòn thì nhiệt cắt tăng. Dung dịch trơn nguội tưới vào vung cắt khi cắt sẽ làm cho nhiệt cắt giảm nhanh vì ngoài tác dụng làm nguội, dung dịch còn có tác dụng bôi trơn giảm đáng kể ma sát trong quá trình cắt. Tuy nhiên cần phải chọn phương pháp và lưu lương tưới phù hợp thì mới tăng hiệu quả giảm nhiệt. Tóm lại, bằng phương pháp thực nghiệm, sau khi xử lý các số liệu nhận được, ta có thể thiết lập được phương trình kinh nghiệm tính toán nhiệt cắt như sau: . . . .x y zC v a b Kθ θ θθ θθ = hay '. . . .x y zC v s t Kθ θ θθ θθ = Hình 5.20 - Quan hệ giữa nhiệt cắt với b Khi tăng chiều sâu cắt, một mặt tải trọng trên một đơn vị chiều dài lưỡi cắt không đổi, mặt khác khi tăng t do φ không đổi nên chiều dài phần làm việc của lưỡi cắt tuy có tăng nhưng điều kiện truyền nhiệt tốt hơn. Kết quả là nhiệt cắt thay đổi ít. Từ kết quả thực nghiệm ta thiết lập được mối quan hệ giữa nhiệt cắt θ và chiều rộng cắt b như sau: . zbC b θθθ = Ta có đối với thép: zθ = 0,05-0,14 đối với gang: zθ = 0,04
File đính kèm:
giao_trinh_co_so_cat_got_kim_loai_chuong_5_hien_tuong_nhiet.pdf