Giáo trình Cơ sở cắt gọt kim loại - Chương 3: Biến dạng và ma sát khi cắt kim loại
Cắt kim loại là dùng dụng cụ cắt hớt bỏ đi lớp dư gia công cơ khỏi chi tiết để nhận được
bề mặt đã gia công trên chi tiết theo những yêu cầu cho trước.
Lớp lượng dư gia công cơ đã bị hớt bỏ đi khỏi chi tiết gọi là phoi cắt.
Phần kim loại sát đầu dao còn liên kết với chi tiết và phoi khi cắt được gọi là vùng cắt.
Phoi, bề mặt đã gia công và vùng cắt là đối tượng để nghiên cứu cơ chế cắt gọt.
Phương hướng nghiên cứu cơ chế cắt gọt là tìm mối quan hệ giữa hiện tượng cắt gọt và
cơ học. Với phương hướng đó từ trước thế kỷ XIX tới nay cả về thực nghiệm lẫn lý thuyết
con người đã đạt được những kết quả đáng kể. Tuy nhiên, cơ chế cắt gọt còn đang là đề tài
cần tiếp tục làm rõ.
Bạn đang xem tài liệu "Giáo trình Cơ sở cắt gọt kim loại - Chương 3: Biến dạng và ma sát khi cắt kim loại", để tải tài liệu gốc về máy hãy click vào nút Download ở trên
Tóm tắt nội dung tài liệu: Giáo trình Cơ sở cắt gọt kim loại - Chương 3: Biến dạng và ma sát khi cắt kim loại
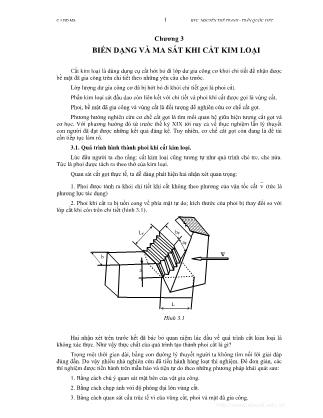
C 3 BD MS 1 GVC NGUYỄN THẾ TRANH - TRẦN QUỐC VIỆT Chương 3 BIẾN DẠNG VÀ MA SÁT KHI CẮT KIM LOẠI Cắt kim loại là dùng dụng cụ cắt hớt bỏ đi lớp dư gia công cơ khỏi chi tiết để nhận được bề mặt đã gia công trên chi tiết theo những yêu cầu cho trước. Lớp lượng dư gia công cơ đã bị hớt bỏ đi khỏi chi tiết gọi là phoi cắt. Phần kim loại sát đầu dao còn liên kết với chi tiết và phoi khi cắt được gọi là vùng cắt. Phoi, bề mặt đã gia công và vùng cắt là đối tượng để nghiên cứu cơ chế cắt gọt. Phương hướng nghiên cứu cơ chế cắt gọt là tìm mối quan hệ giữa hiện tượng cắt gọt và cơ học. Với phương hướng đó từ trước thế kỷ XIX tới nay cả về thực nghiệm lẫn lý thuyết con người đã đạt được những kết quả đáng kể. Tuy nhiên, cơ chế cắt gọt còn đang là đề tài cần tiếp tục làm rõ. 3.1. Quá trình hình thành phoi khi cắt kim loại. Lúc đầu người ta cho rằng: cắt kim loại cũng tương tự như quá trình chẻ tre, chẻ nứa. Tức là phoi được tách ra theo thớ của kim loại. Quan sát cắt gọt thực tế, ta dễ dàng phát hiện hai nhận xét quan trọng: 1. Phoi được tánh ra khỏi chi tiết khi cắt không theo phương của vận tốc cắt v (tức là phương lực tác dụng) 2. Phoi khi cắt ra bị uốn cong về phía mặt tự do; kích thước của phoi bị thay đổi so với lớp cắt khi còn trên chi tiết (hình 3.1). Hình 3.1 Hai nhận xét trên trước hết đã bác bỏ quan niệm lúc đầu về quá trình cắt kim loại là không xác thực. Như vậy thực chất của quá trình tạo thành phoi cắt là gì? Trọng một thời gian dài, bằng con đường lý thuyết người ta không tìm nổi lời giải đáp đúng đắn. Do vậy nhiều nhà nghiên cứu đã tiến hành hàng loạt thí nghiệm. Để đơn giản, các thí nghiệm được tiến hành trên mẫu bào và tiện tự do theo những phương pháp khái quát sau: 1. Bằng cách chú ý quan sát mặt bên của vật gia công. 2. Bằng cách chụp ảnh với độ phóng đại lớn vùng cắt. 3. Bằng cách quan sát cấu trúc tế vi của vùng cắt, phoi và mặt đã gia công. a b bF aF V LF L C 3 BD MS 2 GVC NGUYỄN THẾ TRANH - TRẦN QUỐC VIỆT Sau đây chúng ta nghiên cứu một số thí nghiệm điển hình nhằm khám phá cơ chế cắt gọt. 3.1.1. Thí nghiệm so sánh mẫu nén và cắt: Mô hình thí nghiệm được mô tả hình 3.2. a. Thí nghiệm cắt nén mẫu b. Thí nghiệm cắt mẫu với dao có γ = 00 Hình 3.2 Khi quan sát thí nghiệm nén mẫu, người ta thấy rằng: các phân tử kim loại dưới sức ép của đầu nén bị biến dạng, phương biến dạng là phương AB và CD tạo với phương của ngoại lực tác dụng P một góc ψ xác định đối với từng loại vật liệu (thép ψ = 450). Điều tương tự đó cũng xảy ra đối với mẫu cắt (hình 3.2.b.), nhưng phương CD thì các phân tố kim loại đã bị phần kim loại trên mẫu chặn lại. Do đó phương biến dạng chỉ còn là AB. Kết quả trên đã cho ta kết luận quan trọng là: thực chất quá trình tách phoi ra khỏi chi tiết là quá trình biến dạng của các phần tử kim loại dưới sức ép của đầu dao. 3.1.2. Thí nghiệm quan sát sự dịch chuyển của các phần tử kim loại khi cắt. Để tiếp tục làm rõ bản chất của quá trình cắt kim loại, người ta tiến hành một thí nghiệm khác. ở thí nghiệm này, các phần tử kim loại trên mặt bên của mẫu được đánh dấu. Khi cắt ta P' Dao V Foi P 1 2 3 3' 2' B F FR R r Aψ ψ ψ Hình 3.3 d Chi tiÕt 0 ψ ψ B C D A P ψ B A Dao b/ a/ C 3 BD MS 3 GVC NGUYỄN THẾ TRANH - TRẦN QUỐC VIỆT quan sát sự dịch chuyển của các phần tử kim loại đã được đánh dấu đó. Ví dụ trên hình 3.3. mô tả quá trình dịch chuyển của phần tử kim loại P khi cắt. Từ P đến 1 phần tử kim loại dịch chuyển gần như song song với phương vận tốc cắt v . Qua khỏi điểm 1, đáng lẻ phần tử kim loại chuyển đến điểm 2', nhưng thực tế thì nó dịch đến điểm 2. Đoạn 2'2 gọi là lượng trượt của phần tử kim loại P tại thời điểm 2. Điểm 1 là điểm bắt đầu trượt của phần tử kim loại P khi cắt. Tương tự như vậy ở thời điểm 3 lượng trượt là 3'3 . Tiếp tục cắt, sau khi qua khỏi điểm 3 phần tử kim loại P di chuyển đến điểm 4. Đoạn đường 34 song song với mặt trước của dao. Điều đó có nghĩa là đến thời điểm 3 thì quá trình trượt của phần tử kim loại P đã kết thúc và nó đã chuyển thành phoi cắt. Điểm 3 được gọi là điểm kết thúc trượt của phần tử kim loại P khi cắt. Bằng cách đánh dấu như vậy ta xây dựng được đường dịch chuyển của phân tố kim loại P khi cắt là 1234P'P . Trong đó đoạn 4P' là một cung cong về phía mặt tự do của phoi có bán kính R?P. Điểm 4 được xác định bằng cách: từ điểm tách rời sự tiếp xúc giữa phoi và mặt trước dao (E) ta kẻ (EF) vuông góc với mặt trước dao (EF ⊥ OE). EF sẽ cắt đường 1234P'P tại 4. Nếu quan sát vô số điểm trên mặt bên của mẫu cắt, ta sẽ nhận được vô số đường dịch chuyển của các phần tử kim loại tương ứng; đồng thời xác lập được mặt cắt trượt OA và mặt kết thúc trượt OC. Vùng giới hạn bởi mặt bắt đầu trượt OA và mặt kết thúc trượt OC gọi là vùng trượt. Thí nghiệm trên được tiến hành với tốc độ cắt v = 0,002 m/ph. Trong thực tế, tốc độ cắt lớn hơn rất nhiều so với tốc độ đã thí nghiệm, do đó tốc độ biến dạng trượt cũng rất lớn, Chính vì vậy mặt bắt đầu trượt OA và mặt kết thúc trượt OC gần như trùng nhau. Kinh nghiệm cho thấy khoảng cách giữa 2 mặt này rất nhỏ, trong khoảng 0,03 - 0,2 mm. Để đơn giản cho việc nghiên cứu tính toán sau này, người ta coi 2 mặt )A và OC trùng nhau, gọi là mặt trượt OM, tạo với phương vận tốc cắt v một góc β1 gọi là góc trượt (hay góc tách phoi). Nghiên cứu quá trình cắt kim loại, thường người ta để ý tới 3 trạng thái biến dạng: biến dạng dẻo, biến dạng đàn hồi và sự gãy vỡ. Những thí nghiệm đã chứng tỏ rằng: phoi cắt và lớp kim loại dưới mặt sau dao (bề mặt đã gia công) bao giờ cũng phát sinh biến dạng dẻo. Điều đó khẳng định rằng: dòn không phải là bản chất của vật liệu mà chỉ là trạng thái của chúng mà thôi. Từ quan điểm về cắt gọt, giữa những vật liệu dòn và vật liệu dẻo không thể xác định rõ giới hạn, bởi vì cùng một vật liệu có thể trở thành dòn hoặc dẻo tuỳ thuộc vào tải trọng tác dụng lên nó. Khi cắt kim loại, tác dụng nhiệt cũng gây nhiều khó khăn cho việc giải đáp các hiện tượng xảy ra trong quá trình cắt. Theo các kết quả thí nghiệm cho thấy: Khi tốc độ biến dạng tăng lên thì nhiệt trong vật thể biến dạng cũng tăng lên. Tính dẻo của kim loại thay đổi theo nhiệt. Với những cản trở như vậy cho nên mãi đến nay việc giải thích cơ chế của quá trình cắt gọt còn tồn tại nhiều mâu thuẫn. Song trong đó, ý kiến giải thích khá tập trung là: Quá trình hình thành phoi cắt là quá trình trượt dần hay trượt liên tục của các phần tử kim loại theo mặt trượt của chúng [2]. Hiện tượng phoi bị uốn cong về phía mặt tư do của chúng sau khi ra khỏi mặt EF được giải thích như sau: Các phần tử kim loại sau khi ra khỏi vùng trượt thì quá trình trượt cơ bản đủ kết thúc. Nhưng trong khi đó thì các phần tử kim loại nằm sát và tiếp xúc với mặt trước dao vẫn bị mặt trước dao chèn ép. ma sát, do đó vẫn tiếp tục bị biến dạng. Kết quả của sự chèn ép này là các hạt kim loại ở vùng tiếp xúc bị ép dài ra khi thành phoi. Thể hiện sự kéo dài đó là OE > OF. Mặt khác từ ở vùng OE bị mặt trước dao ma sát, sau khi ra khỏi điểm E, các phần tử kim loại đột ngột được tự do. Do tập hợp những nguyên nhân trên, sau khi ra khỏi mặt EF phoi bị uốn cong về phía mặt tự do của chúng - tức là r < R. C 3 BD MS 4 GVC NGUYỄN THẾ TRANH - TRẦN QUỐC VIỆT 3.1.3. Các dạng phoi khi cắt kim loại: Phoi được hình thành là một kết quả của quá trình biến dạng và ma sát khi cắt. Tuỳ thuộc vào loại vật liệu gia công, các điều kiện tiến hành cắt gọt mà phoi được tạo thành có nhiều dạng khác nhau. Như vậy một cách ngược lại, từ dạng phoi cắt ta có thể phán đoán được vật liệu gia công và những điều kiện cắt đã thực hiện. Trong nghiên cứu về cơ chế cắt gọt, xuất phát từ những mục đích nghiên cứu khác nhau, đã có nhiều cách phân loại dạng phoi khác nhau. Nói chung không dễ dàng trong việc phân biệt một cách rõ ràng các dạng phoi cắt. Vì vậy nói đến dạng phoi cắt là giới thiệu trong những trường hợp kiểm tra cụ thể mà thôi. A. Nhóm phoi gãy vụn (phoi vụn) B. Nhóm phoi liên tục. 3.1.3.1. Phoi gãy vụn. Thường khi cắt vật liệu dòn hoặc những vật liệu dẻo với tốc độ cắt tương đối nhỏ thì phoi được tạo ra bị gãy vụn gọi là phoi vụn (hình 3.4). Hình 3.4 Các phần tử phoi chèn ép lẫn nhau ngay trước lưỡi cắt của dao. Lúc đó ứng suất trong phoi đã đạt tới giới hạn bền nén của vật liệu cắt, và gãy vụn. Kích thước mỗi hạt phoi thường rất nhỏ, thường nhỏ hơn 1cm3. Các hạt phoi được gãy theo đường biên giới các hạt, do đó khi hình thành phoi vụn thì bề mặt đã gia công lưu lại các nhấp nhô. Mặt khác do quá trình gãy vụn phoi xảy ra liên tục khi cắt, cho nên dao động về lực cắt cũng lớn. Điều đó cũng ảnh hưởng xấu đến chất lượng bề mặt đã gia công. Trong thực tế khi gia công tinh và gia công có yêu cầu bề mặt cao, cần chú ý tránh tạo phoi vụn bằng cách chọn chế độ cắt hợp lý. 3.1.3.2. Phoi liên tục. Sự hình thành phoi liên tục là đặc trưng khi cắt những vật liệu dẻo. Các phần tử phoi khi được tách ra không bị gãy rời ra mà còn dính vào nhau thành dãy liên tục. Phoi liên tục lại được phân thành 3 nhóm: a. Phoi xếp, Dao phôi chi tiÕt Thêi gian t (ph) L ùc c ¾t ( N ) C 3 BD MS 5 GVC NGUYỄN THẾ TRANH - TRẦN QUỐC VIỆT b. Phoi dây, c. Phoi lẹo dao. 1. Phoi xếp. Hình 3.5 Cũng trong những điều kiện tạo phoi gãy vụn, nếu ta tăng tốc độ cắt lên đến một giới hạn nào đó thì các phần tử phoi tạo ra sẽ không bị gãy thành các hạt vụn, mà chúng tạo thành các mảnh phoi có liên kết và chồng xếp lên nhau (Hình 3.5.a,b). Bằng mắt thường ta cũng có thể phân biệt được các phần tử phoi xếp. Các phần tử phoi được tách ra khi cắt, chúng bị hàn dính vào nhau, nhưng sự kết dính đó chỉ cần một lực tác động nhỏ cũng đủ tách ra từng miếng một. 2. Phoi dây. Phoi dây là một loại phoi liên tục, các phần tử phoi liên kết nhau thành chuỗi liên tục (hình 3.5.c). Phoi dây được tạo thành khi cắt các loại vật liệu dẻo với tốc độ tương đối lớn. Biến dạng cắt khi tạo phoi dây là bé nhất. Vì vậy trong những trường hợp gia công tinh ta cần cố gắng tạo phoi dây bằng cách nâng cao tốc độ cắt. Khi tạo phoi dây, do phoi được hình thành một cách liên tục, do đó lực cắt khá ổn định, ít rung động. Nhờ vậy dễ đạt độ bóng bề mặt cao. Trong sản xuất cần lưu ý: phoi dậy một mặt dễ gây tai nạn cho công nhân đứng máy, mặt khác có thể cuốn vào chi tiết gây cào xước trên bề mặt đã gia công. Do vậy khi cắt phoi ra dây cần chú ý sử dụng các cơ cấu cuốn và bẻ phoi. 3. Phoi lẹo dao: Nói chung khi cắt tạo ra phoi dây hoặc phoi liên tục thì thường xảy ra hiện trượng: các phần tử kim loại của chi tiết gia công bị tách ra dính trên mặt trước, mặt sau dao; dính trên mặt đang và đã gia công của chi tiết. Các khối kim loại dính như vậy được gọi là khối lẹo dao. Hiện tượng này được gọi là khối lẹo dao. Độ cứng của các khối lẹo dao cao hơn nhiều so với độ cứng bản thân vật liệu chi tiết. Khối lẹo dao được xuất hiện, lớn lên đến một độ lớn nào đó thì bị phân ra làm 3 thành phần: - Một phần dính trên mặt đang và đã gia công của chi tiết. v β1 a v β1 b v β1 c α Dao chi tiÕt α Dao chi tiÕt α Dao chi tiÕt α Dao chi tiÕt α C 3 BD MS 6 GVC NGUYỄN THẾ TRANH - TRẦN QUỐC VIỆT Hình 3.6 - Một phần dính lên phoi và bị phoi mang ra ngoài. - Một phần dính trên mặt trước và mặt sau dao, phần này lại tiếp tục lớn lên đến một mức độ nào đó lại chia làm 3 thành phần. Phoi lẹo dao thực chất là phoi liên tục nhưng trọng những điều kiện cắt cụ thể nó mang thoe các khối lẹo dao (hình 3.6). Hiện tượng lẹo dao có ảnh hưởng lớn tới quá trình cắt kim loại. Khối lẹo dao hình thành trên đầu dao làm thay đổi góc trước và góc sau của dao, đồng thời nó trực tiếp mài cà lên các bề mặt trực tiếp tiếp xúc với nó. Công tác nghiên cứu cắt gọt cho thấy: các khối leo dao sinh ra, lớn lên và mặt đi một cách liên tục, gây rung động cho quá trình cắt, do đó tạo nhấp nhô trên bề mặt đã gia công của chi tiết. Nói chung, hiện tượng lẹo dao cần nên tránh khi cắt kim loại. Kinh nghiệm cho thấy: có thể giảm hoặc triệt tiêu hiện tượng lẹo dao bằng cách giảm mức độ biến dạng và ma sát khi cắt. Mức độ biến dạng cắt có thể giảm bằng cách tăng tốc độ cắt gọt và tăng góc trước của dao. Mức độ ma sát có thể giảm bằng cách mài bóng mặt trước và mặt sau của dao hoặc dùng dung dịch bôi trơn - làm nguội để vừa giảm ma sát vừa giảm nhiệt độ khi cắt. Những biện pháp này cần được chú ý khi gia công tinh. Như chúng ta thấy, phoi cắt có thể phân loại được bằng nhiều cách khác nhau. Nhưng nghiên cứu một cách tổng quát thì hình dạng của phoi phụ thuộc vào vật liệu chi tiết gia công và các điều kiện cắt gọt. Nếu cắt với tốc độ rất nhỏ, thì đối với mọi vật liệu gia công ta đều nhận được phoi gãy vụn. Khi cắt các vật liệu dẻo mà tăng tốc độ cắt lên thì hình thành phoi liên tục. Tuỳ thuộc sự tăng lên của vận tốc cắt sẽ xuất hiện phoi xếp hoặc phoi dây. Khi cắt những vật liệu dòn với tốc độ cắt rất cao cũng có thể nhận được phoi liên tục. 3.2. Quá trình hình thành bề mặt đã gia công trên chi tiết. ở phần "quá trình hình thành phoi", do đối tượng nghiên cứu là phoi nên ta đã lý tưởng hoá đầu dao là hoàn toàn sắc nhọn. Thực tế cho thấy rằng: dù dao được chế tạo từ loại vật liệu gì và mài sắc bằng cách nào thì đầu dao cũng không thể sắc nhọn lý tưởng được mà luôn luôn tồn tại một phần có bán kính ρ. Ví dụ: dao thép gió tuỳ thuộc vào điều kiện mài sắc, bán kính đầu dao tồn tại trong khoảng ρ = 10-18 μm; dao hợp kim cứng thì ρ=18-20 μm. Một thực tế khác cũng không thể bỏ qua khi nghiên cứu quá trình hình thành bề mặt đã gia công là sự tiếp xúc, ma sát giữa bề mặt sau dao và bề mặt đã gia công của chi tiết khi cắt. Sự tiếp xúc này một mặt do quá trình mài mòn mặt sau của dao gây nên, mặt khác do biến dạng đàn hồi của lớp kim loại sát bề mặt đã gia công gây nên. Những thực tế không thể bỏ qua đó được miêu tả ở mô hình 3.7. Ta hãy khảo sát khả năng dịch chuyển của 3 phần tử kim loại O, O1 và O2 trong quá trình cắt. Tương tự như trong trường hợp cắt mẫu kim loại ở hình 3.2 ta dễ dàng có nhận xét. Dao V Δh Cs hs Vc2 R Vc1 aF Δa F E a phoi R R ψ ψ ψ Phương vận tốc cắt Phương trượt của kim loại Phương lực ép C 3 BD MS 7 GVC NGUYỄN THẾ TRANH - TRẦN QUỐC VIỆT Hình 3.7 1. Phương trượt của hạt kim loại tạo với áp lực pháp tuyến lên phần tử kim loại đó một góc ψ. 2. Tại O (phân tử kim loại O) có phương trượt v c // v . 3. Tại O1 (phần tử kim loại O1) có phương trượt hướng về phía phoi, do đó có khả năng trượt để thành phoi. 4. Tại O2 (phần tử kim loại O2) có phương trượt hướng về phía chi tiết gia công. Do đó sự trượt bị chặn lại - không thể thành phoi cắt. Từ những nhận xét trên cho ta rút ra kết luận rất quan trọng như sau: Khi cắt, những phần tử kim loại trên trên lớp cắt có chiều dày a nằm trên mặt OF sẽ bị trượt và tạo thành phoi; những phần tử kim loại nằm trước mặt OF sẽ bị đầu dao nén ép để tạo thành bề mặt đã gia công của chi tiết. Lớp kim loại bị nén ép đó có chiều dày Δa. Lớp kim loại Δa bị biến dạng dưới sức ép của đầu dao và mặt sau dao. Hình 3.8 Hình 3.9 B A O3 O β1 τ τ τ τ δ δ δ δ δ' δ' V phoi N hi Öt ® é ®o Dao BÒ mÆt ®· gia c«ng Chi tiÕt 0 0,5mm C 3 BD MS 8 GVC NGUYỄN THẾ TRANH - TRẦN QUỐC VIỆT Sự biến dạng của lớp kim loại Δa xảy ra cả biến dạng dẻo và biến dạng đàn hồi. Do biến dạng đàn hồi nên khi ra khỏi mặt sau dao một phần của lớp kim loại được phục hồi 1 lượng Δh < Δa. Phân tích trạng thái ứng lực của các phần tử kim loại trong khu vực bị chèn ép ta thấy: các phần tử kim loại nằm trong vùng từ O đến O3 vừa chịu ứng lực nén σ do đầu dao ép, vừa chịu ứng suất kéo τ do ma sát giữa mặt dao và các phần tử kim loại trên chi tiết sát đó. Cũng tương tự như vậy đối với các phần tử kim loại trong khu vực O2 A. Riêng trong vùng AB thì các phần kim loại trên chi tiết do sự giãn nở đột ngột từ vùng chèn ép ra trạng thái tự do bị các phần tử kim loại trước nó và sau nó kéo ra (hình 3.8). Do hiện tượng kéo giãn đột ngột đó nên bề mặt đã gia công dễ phát sinh các vết nứt tế vi. Bên cạnh tải trong lực phức tạp như vậy, bề mặt đã gia công còn nhận tác dụng nhiệt cũng hết sức phức tạp (Hình 3.9). Tải trọng lực và tải trọng nhiệt phức tạp như vậy cho bề mặt đã gia công những hiện tượng cơ - lý cũng hết sức phức tạp. Những hiện tượng đó là: 1. ứng suất dư phát sinh ra trong lớp bề mặt sát bề mặt đã gia công. 2. Một lớp mỏng của lớp bề mặt đã gia công bị hoá bền (hay bị biến cứng) 3. Trên bề mặt đã gia công xuất hiện các vết nứt tế vi. Hình 3.10 Tổng hợp những kết quả nghiên cứu quá trình thành phoi và quá trình hình thành bề mặt đã gia công, được đúc kết thành lý thuyết 5 vùng biến dạng khi cắt (hình 3.10). Vùng I là vùng bắt đầu phát sinh biến dạng khi cắt. Hình thành biến dạng chủ yếu trong vùng này là biến dạng đàn hồi. Những phần tử kim loại càng gần mặt OA thì mức độ biến dạng càng tăng. OA là giới hạn chuyển biến từ biến dạng đàn hồi sang trạng thái biến dạng dẻo (trượt). Vùng II là vùng biến dạng dẻo của vật liệu gia công. Các phần tử kim loại càng gần mặt OC được coi như dần hoàn thành biến dạng dẻo sắp sửa tách ra trở thành các phần tử phoi. Đây là vùng biến dạng mảnh liệt nhất. Dao phoiV III II I IV Chi tiÕt A C C 3 BD MS 9 GVC NGUYỄN THẾ TRANH - TRẦN QUỐC VIỆT Vùng III là vùng ma sát giữa mặt trước của dao với các phần tử kim loại phoi cắt sau khi ra khỏi vùng biến dạng dẻo II. Do ma sát nên bề mặt này của phoi sau khi ra khỏi mặt trước dao rất nhẵn bóng. Vùng IV là vùng biến dạng và ma sát giữa mặt sau dao với các phần tử kim loại trên bề mặt đã gia công nằm sát mặt dao. Về biến dạng thì đây là vùng vừa có biến dạng đàn hồi, vừa có biến dạng dẻo. Vùng V là vùng của các phần tử kim loại đã hoàn thành biến dạng và trở thành phoi cắt. 3.3. Các thông số đặc trưng mức độ biến dạng và ma sát khi cắt. Trong phần 3.1 và 3.2 ta đã lần lượt nghiên cứu một cách định tính bản chất của quá trình cắt kim loại - đó là quá trình biến dạng và ma sát khi cắt. Để đặc trưng về mặt định lượng mức độ biến dạng và ma sát khi cắt, các nhà nghiên cứu đã lần lượt đưa ra các hệ số: 1. Hệ số co rút phoi K 2. Hệ số trượt tương đối ε. 3. Góc tách phoi β1. 4. Hệ số ma sát μ Những hệ số này về mặt giá trị có thể được xác định bằng tính toán cũng như bằng con đường thực nghiệm. Ta sẽ lần lượt nghiên cứu các hệ số đó. 3.3.1. Hiện tượng co rút phoi và hệ số co rút phoi K 3.3.1.1. Khái niệm. Như những nhận xét ở phần 3.1. kích thước của phoi tách ra không giống các kích thước lớp cắt tương ứng khi nó còn nằm trên chi tiết. - Hiện tượng này gọi là hiện tượng co rút phoi. Theo kinh nghiệm thì: aF > a lF < l bF ≈ b Trong đó: a và aF là chiều dày lớp cắt và phoi lF và l là chiều dài phoi và lớp cắt. bF và b là chiều rộng phoi và lớp cắt. Theo lý thuyết kéo - nén thuận tuý trong sức bền vật liệu thì ta gọi tỉ số kích thước mẫu trước và sau khi nén (hoặc kéo) là hệ số co rút. ứng dụng lý thuyết đó vào hiện tượng co rút phoi ta có: Hệ số phoi rút theo chiều dày là: Ka = aF / a > 1 Hệ số co phoi rút theo chiều dài là: Kl = l/ lF > 1 Hệ số co phoi rút theo chiều rộng là: Kb = bF / b ≈ 1 Do định luật bảo toàn về thể tíc, tức là V = VF (thể tích lớp cắt bằng thể tích phoi được tách ra từ lớp cắt tương ứng), ta có: Ka = Kl = aF / a = l/lF (3.1) Đứng về quan điểm toán học thuần tuý thì rõ ràng Ka = Kl = -∞ ÷ +∞. Nhưng về quan điểm cắt gọt nếu Ka = Kl thì có nghĩa là không xảy ra quá trình biến dạng khi cắt. Điều đó hoàn toàn vô lý, bởi vì đã cắt gọt thì tất yếu xảy ra quá trình biến dạng và ma sát. C 3 BD MS 10 GVC NGUYỄN THẾ TRANH - TRẦN QUỐC VIỆT Thực tế cắt gọt đã chứng minh: hệ số co rút phoi K = Ka = Kl chỉ có ý nghĩa vật lý nếu K ≥ 1,5. Điều này thể hiện tính gần đúng của việc đặc trưng mức độ biến dạng và ma sát khi cắt. Các tài liệu nghiên cứu chỉ ra rằng: sai số đặc trưng biến dạng khi cắt của hệ số co rút phoi khoảng 20%[1]. Mặc dù hệ số co rút phoi K không đặc trưng hoàn toàn cho quá trình biến dạng và ma sát khi cắt, song nó có ý nghĩa cơ học ở chỗ nếu K càng lớn tức là mức độ biến dạng càng lớn. Mặt khác việc xác định giá trị hệ số K tương đối đơn giản, do đó ở mức độ định tính người ta vẫn hay dùng hệ số K để đặc trưng cho mức độ biến dạng khi cắt. 3.3.1.2. Cách xác định giá trị hệ số K. Giá trị hệ số K thường được xác định bằng thực nghiệm hoặc thông qua việc đo trực tiếp các kích thước phoi ở lớp cắt, hoặc bằng cách cân đo trọng lượng phoi. 1. Xác định K bằng cách đo trực tiếp kích thước lớp cắt và phoi. Hình 3.11 Để có lớp cắt và phoi cắt có thể đo được dễ dàng, ta chuẩn bị mẫu thí nghiệm như hình 3.11. Mẫu được chuẩn bị là một trụ ngắn có đường kính D, chiều sâu cắt là t. Mẫu có kẻ 2 rãnh đối xứng có bề rộng e. Để giảm va đập khi cắt ta nhồi vào rãnh phoi đồng. Mẫu được cắt tự do. Theo hình 3.11, chiều dài trung bình của lớp cắt tính được: ( ) 2 D tL eπ −= − Tương tự ta có: 1 2 2 F F F L LL += Theo định nghĩa ta có: 1 2 ( ) 2 L a F F D t eK K K L L π − −= = = + (3.2) 2. Xác định K bằng cách cân phoi. Với phương pháp này không cần chuẩn bị mẫu. Sau khi cắt ta tiến hành cân trọng lượng của phoi cắt ra. Giả thiết cân được trọng lượng là Q (G). Phoi ®ång t e D LF1 LF2 C 3 BD MS 11 GVC NGUYỄN THẾ TRANH - TRẦN QUỐC VIỆT Thể tích lớp cắt tương ứng dễ dàng tính được theo công thức: V = Q / ξ (mm3) ξ là tỉ trọng của vật liệu chi tiết gia công. (G/cm3). Thể tích lớp cắt còn có thể biểu diễn dưới dạng: V = s.t.L (mm3) s là lượng chạy dao khi cắt (mm/vg) t là chiều sâu cắt khi cắt (mm). L là chiều dài của lớp cắt (mm) Kết hợp những công thức trên, ta có: L = 1000 Q/s.t.ξ (mm) (3.3) LF ta đo được tương tự như thí nghiệm đo trên. Lúc đó ta có: 1000 . . .L F QK K s t Lξ= = (3.4) 3.3.2. Biến dạng khi cắt và hệ số trượt tương đối ε. Sức bền vật liệu đã nghiên cứu: nếu có 1 phân tố kim loại ABCD, dưới tác dụng của ngoại lực bị biến dạng trượt xô lệch tới vị trí ABC'D' (hình 3.12) thì hệ số đặc trưng cho biến dạng trượt thuần tuý đó là hệ số trượt tương đối ε, được viết dưới dạng: x y ε Δ= Δ Hình 3.12 Hình 3.13 Như phần 3.1 đã phân tích: thực chất quá trình cắt kim loại là biến dạng và ma sát. Trong đó biến dạng dẻo dưới hình thức trượt khi tạo phoi được coi là đặc trưng. ứng dụng kết quả của cơ học, người ta đưa ra hệ số trượt tương đối ε khi cắt: x y ε Δ= Δ Δx = DI + ID'; Δy = BI; DI/BI = tg (β1 - γ); ID'/BI = cotgβ1 Vậy: ε = tg(β1 - γ) + cotgβ1 = 1 1 1 1 sin( ) cos cos( ) sin β γ β β γ β − +− Qui đồng mẫu số và chú ý các công thức lượng giác: aF C C' τ τ D' B D Δx A Δy A C V γ Δy Δx D D’ a β1 B C’ I C 3 BD MS 12 GVC NGUYỄN THẾ TRANH - TRẦN QUỐC VIỆT sin(β1 - γ) = sinβ1cosγ - sinγcosβ1 cos(β1 - γ) = sinβ1sinγ + cosβ1cosγ sin2β1 + cos2β1 = 1 ta nhận được công thức: 1 1 cos sin cos( ) γε β β γ= − (3.5) Từ công thức (3.5) ta có nhận xét: Khi cắt nói chung góc độ của dao là xác định và không đổi, trong trường đó, rõ ràng: ε = f(β1) Công tác nghiên cứu cho thấy: mặc dù hệ số trượt tương đối ε có đặc trưng một cách bản chất hơn quá trình cắt kim loại, song quá trình cắt không thuần tuý chỉ có biến dạng trượt, do đó hệ số ε khi đặc trưng cho mức độ biến dạng và ma sát khi cắt có sai số khoảng 4%. 3.3.3. Góc tách phoi (hoặc góc hướng trượt) β1 Nếu như hệ số co rút phoi K được đưa ra trên cơ sở kéo, nên thuần tuý; hệ số trượt hướng đến ε được dẫn ra từ lý thuyết trượt thuần tuý, thì góc tách phoi β1 được thiết lập không kèm theo giả định nào cả. Góc tách phoi β1 được xác lập trên cơ sở mô hình cắt tự do như ở hình 3.14. Trên hình 3.14: θ là góc ma sát trên mặt trước dao. Tức là: θ = arctgμ μ là hệ số ma sát. Hình 3.14 Từ hình 3.14 ta có: β1 + ω = ψ ω = θ - γ hoặc β1 = ψ - arctgμ + γ (3.6) m n a ω V aF γ γ ψ θ N R β1 C 3 BD MS 13 GVC NGUYỄN THẾ TRANH - TRẦN QUỐC VIỆT ψ là góc đặc trưng cho loại vật liệu bị biến dạng. Sức bền vật liệu đã chứng minh được: với những loại vật liệu thường dùng trong chế tạo máy thì ψ = 45 - 50 0 Cũng từ hình 3.14 ta có: tgβ1 = am , m = Fa cosγ - n n = a.tgγ Vậy tgβ1 = F a.cos a - a.sin γ γ Kết hợp với công thức (3.1) và rút gọn, ta có: β1 = cosarctg K - sin γ γ (3.7) 3.3.4. Hiện tượng ma sát và hệ số ma sát khi cắt. Khi cắt có 2 khu vực ma sát: 1. Khu vực ma sát giữa phoi và mặt trước dao 2. Khu vực ma sát giữa bề mặt đã gia công và mặt sau dao. Hình 3.15 Trong quá trình cắt kim loại, dưới tác dụng của áp lực và ma sát giữa các phần tử kim loại của phoi với lớp bề mặt đã gia cồn xuất hiện trễ. Tức là các phần tử kim loại của phoi, của lớp bề mặt đã gia công cách xa mặt trước và mặt sau dao di chuyển nhanh, trong khi đó các phần tử kim loại tiếp xúc với mặt trước dao và mặt sau dao di chuyển chậm lại (hình 3.15). Hiện tượng trễ gây nên cho nội bộ phoi cắt và lớp bề mặt đã gia công biến dạng và ứng suất cắt. Tổng lực biến dạng giữa các phần tử phoi và lớp bề mặt đã gia công gọi là Lực nội ma sát. Chi tiết Phoi Dao Líp bÒ mÆt ®¸ gia c«ng C 3 BD MS 14 GVC NGUYỄN THẾ TRANH - TRẦN QUỐC VIỆT Thực nghiệm đã chứng minh rằng: lực ma sát trên mặt trước và mặt sau dao chủ yếu là do lực nội ma sát. Lực thắng lực nội ma sát đó là ứng suất cắt của bản thân vật liệu. Theo định nghĩa chung về hệ số ma sát ta có: μc = F/N F là lực ma sát. N là lực ép pháp tuyến. Trong đó: F = τc.A N = σ.A τc và σc là ứng suất cắt và ứng suất nén trung bình của lớp phoi sát mặt trước dao và lớp bề mặt đã gia công. A là diện tích bề mặt tiếp xúc giữa phoi và mặt trước dao (hoặc giữa bề mặt đã gia công và mặt sau dao) Từ đó, ta có: μc = c c τ σ (3.8) Kết quả của thực nghiệm cho thấy: τc và σc không phải là những hằng số mà là những số thay đổi theo những điều kiện cắt gọt, trong đó trong cùng một thay đổi về điều kiện cắt thì sự thay đổi giá trị σc lớn hơn τc. Chính sự thay đổi này dẫn đến sự thay đổi của μc. Nói chung hệ số ngoại ma sát giữa 2 vật liệu tiếp xúc có chuyển động tương đối với nhau là một hằng số. Trái lại hệ số nội ma sát giữa các vật liệu tiếp xúc có chuyển động tương đối với nhau là số thay đổi phụ thuộc vào tải trọng tác dụng lên hệ. Nghiên cứu bản chất của quá trình cắt là phát hiện các qui luật phát sinh ra trong quá trình cắt. Trên cơ sở đó đi tìm hiểu tới các yếu tố ảnh hưởng đến quá trình cắt gọt, nhằm mục đích điều khiển các qui luật đó theo hướng có lợi cho con người. Trên cơ sở hàng loạt các thí nghiệm, người ta đã tìm ra các yếu tố ảnh hưởng chính đến biến dạng và ma sát khi cắt là: 1. Tính chất của vật liệu chi tiết gia công. 2. Chế độ cắt. 3. Các thông số hình học của dao. Qui luật ảnh hưởng của các yếu tố trên đến các hệ số đặc trưng biến dạng và ma sát khi cắt có thể đc kết ở bảng 3.1. Bảng 3.1 Vật liệu chi tiết Chế độ cắt Dung dịch trơn nguội Thông số hình học dao Yếu tố ảnh hưởng Kμβi σB t s v Lit/ph γ r ϕ K μc βi C 3 BD MS 15 GVC NGUYỄN THẾ TRANH - TRẦN QUỐC VIỆT
File đính kèm:
giao_trinh_co_so_cat_got_kim_loai_chuong_3_bien_dang_va_ma_s.pdf