Đề cương Chế tạo phôi hàn
Lắp van giảm áp vào bình khí.
a, Thổi sạch bụi bẩn trước khi lắp van giảm áp.
- Quay cửa xả về phía trái người thao tác.
- Để tay quay tại van của bình.
- Mở và đóng nhanh van khí từ 1~2 lần.
b. Lắp van giảm áp ôxy.
- Kiểm tra gioăng của van giảm áp.
- Lắp van giảm áp ôxy vào bình sao cho lỗ xả khí của van an toàn hướng xuống phía dưới.
- Dùng mỏ lết siết chặt đai ốc.
- Để van giảm áp nghiêng 450.
c, Lắp van giảm áp axêtylen.
- Kiểm tra gioăng của van giảm áp.
- Điều chỉnh phần dẫn khí vào van giảm
áp nhô ra khỏi mặt trong của đồ gá khoảng 20mm.
- Để van giảm áp nghiêng 450.
- Xiết chặt gá kẹp.
d, Nới lỏng vít điều chỉnh van giảm áp.
- Nới lỏng vít điều chỉnh cho tới khi tay quay nhẹ
ncắtg.
Bạn đang xem 20 trang mẫu của tài liệu "Đề cương Chế tạo phôi hàn", để tải tài liệu gốc về máy hãy click vào nút Download ở trên
Tóm tắt nội dung tài liệu: Đề cương Chế tạo phôi hàn
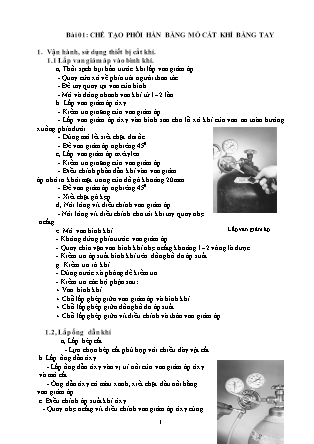
Bài 01: CHẾ TẠO PHÔI HÀN BẰNG MỎ CẮT KHÍ BẰNG TAY Vận hành, sử dụng thiết bị cắt khí. 1.1 Lắp van giảm áp vào bình khí. a, Thổi sạch bụi bẩn trước khi lắp van giảm áp. - Quay cửa xả về phía trái người thao tác. - Để tay quay tại van của bình. - Mở và đóng nhanh van khí từ 1~2 lần. b. Lắp van giảm áp ôxy. - Kiểm tra gioăng của van giảm áp. Lắp van giảm áp - Lắp van giảm áp ôxy vào bình sao cho lỗ xả khí của van an toàn hướng xuống phía dưới. - Dùng mỏ lết siết chặt đai ốc. - Để van giảm áp nghiêng 450. c, Lắp van giảm áp axêtylen. - Kiểm tra gioăng của van giảm áp. - Điều chỉnh phần dẫn khí vào van giảm áp nhô ra khỏi mặt trong của đồ gá khoảng 20mm. - Để van giảm áp nghiêng 450. - Xiết chặt gá kẹp. d, Nới lỏng vít điều chỉnh van giảm áp. - Nới lỏng vít điều chỉnh cho tới khi tay quay nhẹ ncắtg. e. Mở van bình khí - Không đứng phía trước van giảm áp - Quay chìa vặn van bình khí nhẹ ncắtg khoảng 1~2 vòng là được. - Kiểm tra áp suất bình khí trên đồng hồ đo áp suất. g. Kiểm tra rò khí - Dùng nước xà phòng để kiểm tra - Kiểm tra các bộ phận sau: + Van bình khí. + Chỗ lắp ghép giữa van giảm áp và bình khí. + Chỗ lắp ghép giữa đồng hồ đo áp suất. + Chỗ lắp ghép giữa vít điều chỉnh và thân van giảm áp. 1.2, Lắp ống dẫn khí a, Lắp bép cắt - Lựa chọn bép cắt phù hợp với chiều dày vật cắt. Lắp ống dẫn khí b. Lắp ống dẫn ôxy - Lắp ống dẫn ôxy vào vị trí nối của van giảm áp ôxy và mỏ cắt. - Ống dẫn ôxy có màu xanh, xiết chặt đầu nối bằng van giảm áp. c. Điều chỉnh áp suất khí ôxy - Quay nhẹ ncắtg vít điều chỉnh van giảm áp ôxy cùng chiều kim đồng hồ. - Điều chỉnh áp suất ôxy ở mức 1,5 kg/cm2 d. Lắp ống dẫn khí Axêtylen. - Lắp ống dẫn axêtylen vào vị trí nối của van giảm áp axêtylen và mỏ cắt. - Ống dẫn axêtylen có màu đỏ, xiết chặt đầu nối bằng van giảm áp bằng vòng hãm. e. Điều chỉnh áp suất khí axêtylen - Quay nhẹ các vít điều chỉnh van giảm áp axêtylen cùng chiều kim đồng hồ. - Điều chỉnh áp suất axêtylen ở mức 0,15 kg/cm2 1.3, Kiểm tra rò khí. - Kiểm tra các vị trí sau: + Phần lắp ghép đồng hồ áp suất khí ra mỏ cắt với van giảm áp. + Phần nối ống dẫn khí vào van giảm áp. + Phần nối ống dẫn khí vào mỏ cắt. + Các van của mỏ cắt + Phần lắp ghép bép cắt vào đầu mỏ cắt. 1.4,Xả khí hỗn hợp. - Trước khi xả kiểm tra xung quanh không có lửa. - Mở van axêtylen khoảng 10 giây. - Kiểm tra khí xả bằng cách đưa mỏ cắt lại gần thùng nước và quan sát mặt nước. 1.5, Lấy ngọn lửa cắt. 1.5.1 Mồi lửa. - Mở van axêtylen khoảng 1/2 vòng quay. - Mở van ôxy khỏang1/4 vòng quay. - Quay mỏ cắt ra xa người thao tác, dùng bật lửa mồi lửa. 1.5.2 Điều chỉnh ngọn lửa trung tính. - Mở thêm van axêtylen và xác định công suất ngọn lửa. - Mở từ từ van ôxy và điều chỉnh nhân ngọn lửa để lấy được ngọn lửa trung hoà. 1.5.3 Tắt ngọn lửa. - Đóng van axêtylen trước sau đó đóng van ôxy. 2.Chế độ cắt khí Chiều dày tấm,mm Số hiệu đầu cắt Đường kính lỗ, mm Tốc độ cắt cm/phút Áp lực khí ,at Lưu lượng khí, lít/giờ Ôxy Axêtylen Ôxycắt Ôxy nung nóng Axêtylen 3 ÷ 5 00 0,8 65 ÷ 70 3,0 0,2 1.000 370 330 5 ÷ 10 0 1,0 60 ÷ 65 3,0 0,2 1.500 370 330 10 ÷ 15 1 1,2 50 ÷ 60 4,0 0,3 2.900 500 460 15 ÷ 25 2 1,4 40 ÷ 50 4,0 0,3 4.000 500 460 25 ÷ 35 3 1,6 30 ÷ 40 4,0 0,3 5.200 500 460 35 ÷ 50 4 1,8 25 ÷ 30 5,0 0,4 8.100 720 650 50 ÷ 100 5 2,1 20 ÷ 25 5,0 0,4 11.000 720 650 100 ÷ 150 6 2,4 15 ÷ 20 5,0 0,4 15.000 1.000 900 150 ÷ 200 7 2,8 10 ÷ 15 6,0 0,5 24.000 1.000 900 200 ÷ 350 8 3,2 8 ÷ 10 6,0 0,5 30.000 1.450 1.300 3. Gá phôi. - Kê phôi lên cách mặt đất chừng 300 mm. Đảm bảo xỉ thoát tốt. 4. Kỹ thuật cắt phôi bằng ngọn lửa ôxy – Khí cháy 4.1, Lấy ngọn lửa cắt. a. Mồi lửa. - Mở van axêtylen khoảng 1/2 vòng quay. - Mở van ôxy khỏang1/4 vòng quay. - Quay mỏ cắt ra xa người thao tác, dùng bật lửa mồi lửa. b. Điều chỉnh ngọn lửa trung tính. - Mở thêm van axêtylen và xác định công suất ngọn lửa. - Mở từ từ van ôxy và điều chỉnh nhân ngọn lửa để lấy được ngọn lửa trung hoà. c. Tắt ngọn lửa. - Đóng van axêtylen trước sau đó đóng van ôxy. 4.2 Kỹ thuật cắt bằng ngọn lửa khí cháy - Đối với các tấm dày, khi bắt đầu cắt mỏ cắt để nghiêng với góc 5 ÷ 100, còn trong quá trình cắt thì để góc 20 ÷ 300 ; còn khi bắt đầu cắt các tấm mỏng (chiều dày nhỏ hơn 50mm) mỏ cắt được đặt gần như vuông góc với chi tiết. - Khi cắt các phôi tròn vị trí của mỏ cắt lúc bắt đầu và trong quá trình cắt được giới thiệu trong hình 4-2 Hình 4-2: Vị trí của mỏ cắt khi cắt Thép tròn - Khi cắt bằng ngọn lửa khí cháy khoảng cách từ đầu cắt đến bề mặt chi tiết được chọn theo bảng sau: Chiều dày kim loại mm 3 ÷ 10 10 ÷ 25 25 ÷ 50 50 ÷ 100 100 ÷ 200 200 ÷ 300 Khoảng cách từ đầu cắt đến chi tiết 2 ÷ 3 3 ÷ 4 3 ÷ 5 4 ÷ 6 5 ÷ 8 7 ÷ 10 - Chiều rộng rãnh cắt phụ thuộc và phương pháp cắt. Cắt bằng máy cho mép cắt phẳng hơn và chiều rộng rãnh cắt nhỏ hơn cắt bằng tay. Chiều dày kim loại càng lớn thì chiều rộng rãnh cắt càng lớn. Chiều dày kim loại mm 5 ÷ 15 15 ÷ 30 30 ÷ 60 60 ÷ 100 100 ÷ 150 Chiều rộng rãnh cắt mm 2 ÷ 2,5 2,5 ÷ 3 3 ÷ 3,5 3,5 ÷ 4,5 4,5 ÷ 5,5 - Tốc độ cắt (tốc độ dịch chuyển của đầu cắt) cần phải phù hợp với tốc độ cháy của kim loại. Độ ổn định và chất lượng của quá trình cắt phụ thuộc vào tốc độ cắt. 5.An toàn khi cắt phôi bằng ngọn lửa ôxy – Khí cháy 5.1 Kỹ thuật an toàn với người vận hành - Thường xuyên kiểm tra tình trạng của bình, sự hoạt động của dụng cụ kiểm tra - đo lường các cơ cấu an toàn và phụ tùng của bình. Thường xuyên kiểm tra tình trạng và các cơ cấu an toàn của các máy có liên quan đến bình khí nén là máy nén khí PVMA và máy cắt tôn (hoặc máy khác dùng khí nén). Thường xuyên kiểm tra bộ lọc bụi và mức dầu của máy nén khí. - Vận hành bình một cách an toàn theo đúng quy trình. Kịp thời và bình tĩnh xử lý theo đúng qui trình khi có sự cố xảy ra, đồng thời báo ngay cho người phụ trách biết những hiện tượng không an toàn của bình. - Trong khi bình đang hoạt động, không được làm việc riêng hoặc bỏ vị trí công tác. 5.2 Kỹ thuật an toàn với bình khí ôxy - Bình chứa ôxy phải để xa ngọn lửa trần ít nhất là 5 mét. - Khi lắp van giảm áp, phải mở khóa van nhẹ nhàng để tránh xảy ra hiện tượng nổ chai ôxy. - Không được để các chai ôxy gần các chất dễ cháy, dễ bắt lửa như: xăng, dầu mỡ.... - Khi vận chuyển các chai ôxy phải nhẹ nhàng, dùng xe chở chuyên dùng, tránh va chạm, không để tiếp xúc với dầu mỡ. 5.3 Kỹ thuật an toàn với van giảm áp: - Van giảm áp của loại nào chỉ được dùng riêng cho khí ấy, không được dùng lẫn lộn. - Trước khi lắp van giảm áp phải kiểm tra van khóa của bình ôxy có dầu mỡ, bụi bẩn không? - Khi ngừng làm việc hàn hoặc cắt, trước khi đóng van khóa của bình chứa khí phải nới lỏng vít hiệu chỉnh trên van giảm áp đến khi kim chỉ vạch 0 thì dừng lại. - Thường xuyên kiểm tra mối nối của van với bình khí xem có hở không để xử lý. Bài 02: CHẾ TẠO PHÔI HÀN TỪ VẬT LIỆU THÉP TẤM BẰNG MÁY CẮT KHÍ CON RÙA 1. Cấu tạo, nguyên lý làm việc của thiết bị cắt bán tự động. 1.1 Cấu tạo của thiết bị cắt bán tự động - Thiết bị cắt bán tự động bao gồm : + Máy cắt con rùa + Bình khí ôxy, axêtylen (hoặc khí gas), + Dây dẫn khí. + Đồng hồ đo áp. + Ray chạy máy. 1.2 Nguyên lý cắt bán tự động. - Máy chuyển động trên thanh ray định hình nhờ động cơ một chiều có tốc độ điều khiển được bằng núm xoay. Bánh dẫn hướng đảm bảo máy luôn bám theo đường ray, còn bánh chuyển động có nhiệm vụ truyền chuyển động từ động cơ qua hộp giảm tốc. Vận hành thiết bị cắt bán tự động. Đấu điện vào máy nén khí. Lắp ống dẫn khí từ máy nén khí vào nguồn cắt. Đấu điện vào nguồn cắt. Kiểm tra rò khí: chỗ nối máy nén khí và dây khí, chỗ nối dây khí và nguồn cắt. Đóng cầu dao điện Nhấn công tắc tại tay cắt phát sinh hồ quang sau khi đã kẹp mát vào chi tiết. 3. Thông số kỹ thuật cắt bán tự động. Hình 6-1 giới thiệu máy cắt khí tự động IK – 12 Hunter Hình 6-1:Máy cắt IK – 12 Hunter Thông số kỹ thuật như sau: Điện áp sử dụng: 220V xoay chiều, 50/60 Hz Tốc độ cắt 100 ÷ 1000mm/phút Động cơ 24V một chiều, 2800 vòng/phút Chiều dày cắt max: 100mm (khi dùng mỏ cắt No 5) Góc nghiêng mỏ cắt: 0 ÷ 450 Ray cắt: dài 1800mm Khối lượng máy 9,8 Kg 4. Kỹ thuật cắt phôi bằng máy cắt con rùa - Đặt ray lên phôi, đưa máy vào ray. - Điều chỉnh mỏ căt dọc theo đúng đường vạch dấu. - Đối với các tấm dày, khi bắt đầu cắt mỏ cắt để nghiêng với góc 5 ÷ 100, còn trong quá trình cắt thì để góc 20 ÷ 300 ; còn khi bắt đầu cắt các tấm mỏng (chiều dày nhỏ hơn 50mm) mỏ cắt được đặt gần như vuông góc với chi tiết. - Khi cắt bằng ngọn lửa khí cháy khoảng cách từ đầu cắt đến bề mặt chi tiết được chọn theo bảng sau: Chiều dày kim loại mm 3 ÷ 10 10 ÷ 25 25 ÷ 50 50 ÷ 100 100 ÷ 200 200 ÷ 300 Khoảng cách từ đầu cắt đến chi tiết 2 ÷ 3 3 ÷ 4 3 ÷ 5 4 ÷ 6 5 ÷ 8 7 ÷ 10 - Chiều rộng rãnh cắt phụ thuộc và phương pháp cắt. Cắt bằng máy cho mép cắt phẳng hơn và chiều rộng rãnh cắt nhỏ hơn cắt bằng tay. Chiều dày kim loại càng lớn thì chiều rộng rãnh cắt càng lớn. Chiều dày kim loại mm 5 ÷ 15 15 ÷ 30 30 ÷ 60 60 ÷ 100 100 ÷ 150 Chiều rộng rãnh cắt mm 2 ÷ 2,5 2,5 ÷ 3 3 ÷ 3,5 3,5 ÷ 4,5 4,5 ÷ 5,5 - Tốc độ cắt (tốc độ dịch chuyển của đầu cắt) cần phải phù hợp với tốc độ cháy của kim loại. Độ ổn định và chất lượng của quá trình cắt phụ thuộc vào tốc độ cắt. 5. An toàn khi cắt phôi bằng máy cắt con rùa 5.1 Kỹ thuật an toàn với bình khí ôxy - Bình chứa ôxy phải để xa ngọn lửa trần ít nhất là 5 mét. - Khi lắp van giảm áp, phải mở khóa van nhẹ nhàng để tránh xảy ra hiện tượng nổ chai ôxy. - Không được để các chai ôxy gần các chất dễ cháy, dễ bắt lửa như: xăng, dầu mỡ.... - Khi vận chuyển các chai ôxy phải nhẹ nhàng, dùng xe chở chuyên dùng, tránh va chạm, không để tiếp xúc với dầu mỡ. 5.2 Kỹ thuật an toàn với van giảm áp: - Van giảm áp của loại nào chỉ được dùng riêng cho khí ấy, không được dùng lẫn lộn. - Trước khi lắp van giảm áp phải kiểm tra van khóa của bình ôxy có dầu mỡ, bụi bẩn không? - Khi ngừng làm việc hàn hoặc cắt, trước khi đóng van khóa của bình chứa khí phải nới lỏng vít hiệu chỉnh trên van giảm áp đến khi kim chỉ vạch 0 thì dừng lại. - Thường xuyên kiểm tra mối nối của van với bình khí xem có hở không để xử lý. BÀI 03. CHẾ TẠO PHÔI HÀN TỪ VẬT LIỆU THÉP TẤM BẰNG MÁY CẮT LƯỠI THẲNG 1. Cấu tạo, nguyên lý làm việc của máy cắt đột liên hợp CD13. 1.1 Đặc tính kỹ thuật của máy cắt đôt liên hợp CD13. TT Thông số Đơn vị Trị số 1 Cắt đột vật liệu có giới hạn bền lớn nhất kg/mm2 45 2 Khoảng cách từ tâm đầu cột đến tcắth máy mm 400 3 Kích thước thép tấm cắt được Chiều dày cắt Max Chiều dài nhát cắt mm mm 13 100 4 Kích thước thép hình cắt được Thép góc L Thép tròn Thép vuông mm mm mm 80x80x8 F30 25x25 5 Đột lỗ - Lực đột - Lỗ đột lớn nhất với chiều dày d = 8 - Số nhát cắt tấn mm nhát/phút 45 F20 45 6 Động cơ 3 pha: - Công suất (N) - Số vòng quay (n) KW V/p 4,5 1420 7 Trọng lượng máy kg 2.070 8 Kích thước bao gói (dài x rộng x cao) m 1400x900x1650 1.2 Các bộ phận điều khiển chính của máy. 1 – Cữ chặn phôi thanh. 2 – Cữ đặt phôi thanh. 3 – 10: Các nút điện chạy và dừng máy. 4 – Cần điều khiển cắt 5 – Các vị trí điều chỉnh khe hở con lắc và bôi trơn. 6 – Cữ chặn phôi tấm khi cắt. 7 – Cữ chặn phôi khi đột. 8 – Cần điều khiển đột. 9 – Cần kiểm tra vị trí chày và cối đột. 1.3 Sơ đồ nguyên lý làm việc của máy. 3 2 1 7 6 5 4 Hình 1-1: Sơ đồ nguyên lý làm việc của máy 1 – Động cơ điện 2 – Bánh đà 3 – Trục lệch tâm 4 – Cơ cấu đột 5 – Con lắc 6 – Dao cắt thép tấm 7 – Dao cắt thép hình 2. Vận hành máy. 2.1 Lau chùi sạch sẽ toàn bộ máy, bơm mỡ hoặc tra dầu vào các vị trí bôi trơn. Kiểm tra điều chỉnh các vít và sự hoạt động nhẹ ncắtg của các cần gạt, tay quay, cữ chặn phôi 2.2 Đấu tiếp đất cho máy. Tháo các dây đai thang và đấu điện vào động cơ. - Ấn các nút khởi động máy. Nếu động cơ quay ngược chiều với mũi tên đã vẽ trên máy thì phải đấu điện lại cho đúng chiều. Sau đó mắc lại các dây đai cho máy làm việc. (Chú ý rằng đối với người sử dụng có kinh nghiệm thì có thể đóng ngắt điện thật nhanh để kiểm tra chiều quay của dông cơ và bánh đà mà không cần phải tháo dây đai. 2.3 Cho động cơ làm việc, cho máy làm việc không tải khoảng 15 phút trong thời gian đó sử dụng thử các cần điều khiển cắt và cần điều khiển đột xem các lưỡi dao đi xuống có bình thường không. Chú ý vị trí của chày cối đột và cối đột nếu không chính xác sẽ bị vỡ chày và cối đột. 2.4 Cho dừng máy, điều chỉnh các khe hở dao tấm, dao hình, chày cối đột theo vật liệu sử dụng và theo bảng hướng dẫn dưới đây. Khe hở (mm) Chiều dày tôn gia công Đến 2 2 đến 4 4 đến 6 6 đến 8 8 đến 10 10 đến 13 Cắt 0,12 0,25 0,4 0,58 0,75 1 Đột 0,08 0,15 0,25 0,5 0,70 0,9 Khi đã điều chỉnh khe hở đạt yêu cầu thì cố định chặt các vít tăng, đai ốc hãm và tiếp tục cho máy chạy không tải 15 phút nữa. Chú ý rằng: Trên máy có bố trí 2 nút điện dừng máy và 2 nút điện chạy máy ở 2 đầu của máy để thao tác cho thuận tiện. 3. Khai triển, vạch dấu phôi. - Đọc bản vẽ xác định kích thước phôi. - Dùng thước lá mũi vạch, vạch dấu phôi theo kích thước bản vẽ. 4. Kỹ thuật cắt phôi bằng máy, bằng tay. 4.1: Thao tác cắt thép tấm. - Cho máy chạy - Đưa thép tấm vào lưỡi cắt - Vặn cữ chặn phôi đến vị trí phù hợp - Kéo cần điều khiển xuống sẽ thực hiện được việc cắt thép. 4.2 Thao tác cắt hình, tròn, vuông. - Cho máy chạy - Điều chỉnh cữ chặn phôi phù hợp - Đưa phôi vào lỗ cắt - Điều chỉnh cữ chặn phôi để đảm bảo an toàn khi cắt. - Kéo cần điều khiển xuống sẽ thực hiện được việc cắt. 4.3 Thao tác đột - Chọn và gá lắp chày và cối đột cho phù hợp - Dùng tay điều khiển để kiểm tra điều chỉnh vị trí giữa chày và cối. - Cho máy chạy và đưa phôi và lỗ đột - Vặn cữ chặn phôi xuống cách mặt phôi khoảng 1mm - Kéo cần điều khiển sẽ thực hiện viêc đột. 4.4 Thao tác cắt bằng tay - Kiểm tra thiết bị cắt bằng tay đảm bảo an toàn trước khi thực hiện công viêc cắt. - Đưa phôi đã vạch dấu vào vị trí dao cắt. - Điều chỉnh đường vạch dấu trùng với lưỡi dao cắt. - Kéo cần điều khiển sẽ thực hiện việc cắt. 5. Kỹ thuật nắn phôi. - Đeo găng tay, dùng búa nguội để năn phôi. - Đặt phôi lên đe thuyền dùng búa nguội nắn thẳng phôi. - Nắn phôi thẳng, phẳng. - Làm sạch bavia. 6. Công tác an toàn và vệ sinh công nghiệp. - Sử dụng bảo hộ lao động hợp lý. - Vận cắth máy cắt đột đảm bảo an toàn, đúng quy trình. - Đảm bảo công tác vệ sinh sau khi thực tập. Bài 04: CHẾ TẠO PHÔI HÀN TỪ VẬT LIỆU THÉP HÌNH BẰNG MÁY CẮT LƯỠI ĐĨA 1. Cấu tạo, nguyên lý làm việc của máy Đá cắt Vật cắt Động cơ Ê tô Tay quay ê tô Tay cầm Nắp chắn bảo vệ Các bộ phận chính của máy: - Động cơ. - Ê tô, tay quay ê tô - Cầu dao điện - Đá cắt - Tay cầm. - Nắp chắn bảo vệ. 2. Khai triển, vạch dấu phôi a. Chuẩn bị - Vạch dấu 20 mm cách đều trên thanh thép góc. - Kiểm tra độ vuông góc giữa đá cắt và ê tô. Ke vuông 3. Vận cắth máy. 3.1. Tháo đá cắt - Tháo lắp bảo vệ. - Dùng cà lê tháo mũ ốc, lấy vành giữ đá ra ngoài. - Tháo đá cắt. Nắp chắn bảo vệ Bu lông Vành chặn đá cắt Đá cắt Bu lông bắt chặt Nắp bảo vệ Vành chặn đá Đai ốc Đá cắt 3.2. Lắp đá cắt - Kiểm tra hư hại của đá. - Đặt đá cắt vào trục quay. - Lắp vành giữ đá và vặn chặt mũ ốc bằng cà lê (chú ý không vặn mũ ốc quá chặt hoặc chưa đủ chặt hoặc lắp đá không đồng tâm). - Đậy nắp bảo vệ. 3.3. Chạy thử - Nối ổ cắm với nguồn điện. - Bật công tắc. - Cho máy chạy không khoảng 3 phút, kiểm tra không có điều gì bất bình thường xảy ra. Công tắc 4. Kỹ thuật cắt phôi bằng máy cắt lưỡi đĩa. 4.1. Lắp vật cắt - Xiết vừa phải vật cắt trong ê tô. - Hạ thấp đá cho chạm nhẹ vào vật. - Điều chỉnh vị trí cắt. (Điều chỉnh vạch dấu trùng với mép ngoài của đá). - Xiết chặt vật cắt một cách cẩn thận sao cho vật cắt ở vị trí nằm ngang. Đá cắt Dấu cắt Vị trí cắt Thước đo 4.2 Thao tác cắt - Đeo kính bảo hộ. - Đứng tránh hướng quay của đá. - Bật công tắc. - Hạ thấp tay cầm và bắt đầu cắt một cách từ từ. - Không tác dụng lực quá mạnh lên đá khi cắt. - Khi mạch cắt gần đứt, giảm bớt tốc độ cắt (giảm lực ấn). Vị trí người cắt Hướng quay của đá 4.2. Tháo vật cắt - Sau khi cắt đứt, nâng tay cầm đưa đá cắt về vị trí ban đầu. - Tắt công tắc. - Khi đá đã dừng hẳn, tháo vật cắt ra khỏi ê tô. 5. An toàn khi sử dụng máy cắt lưỡi đĩa. - Đấu điện đảm bảo an toàn. - Lắp đá cắt đảm bảo đúng tâm, đá cắt không bị rạn nứt, siết chặt bu lông. - Kẹp phôi khi cắt chắc chắn. - Máy cắt phải có nắp chắn bảo vệ. - Người cắt phải nắm rõ quy trình vận cắth máy và các điều kiện an toàn của máy Bài 05: CHẾ TẠO PHÔI HÀN TỪ VẬT LIỆU THÉP TẤM BẰNG MÁY CẮT PLASMA 1.Đặc điểm, công dụng của phương pháp cắt plasma 1.1 Đặc điểm của phương pháp cắt plasma - Căt plasma dựa trên đặc điểm hồ quang nén có khả năng xuyên sâu vào kim loại và làm nóng chảy nó theo mép cắt - Có thể dùng khí Argon, hỗn hợp argon + nitơ, Hyđrô và không khí. - Khi cắt bằng plasma thì vật cắt không tham gia vào mạch tạo hồ quang. Hồ quang cháy giữa điện cực volfram và thành trong của đầu cắt. Điện cực được nối với cực âm của nguồn điện. Cực dương nối với đầu cắt. 1.2 Công dụng của phương pháp cắt plasma - Có thể cắt được tất cả các kim loại và hợp kim với vùng ảnh hưởng nhiệt có kích thước bé. - Cắt được các tấm kim loại và hợp kim có chiều dày nhỏ và trung bình. - Hồ quang plasma được sử dụng để cắt các kim loại không thể cắt hoặc khó cắt nếu sử dụng phương pháp cắt khác, như thép hợp kim chống ăn mòn (thép không gỉ), nhôm. magiê, gang, đồng. 2.Cấu tạo, nguyên lý làm việc của thiết bị cắt plasma 2.1 Cấu tạo của thiết bị cắt plasma. - Thiết bị cắt plasma bao gồm : Nguồn cắt, máy nén khí, bộ phận lọc và điều chỉnh áp lực khí nén và tay cắt. Máy nén khí yêu cầu phải có lưu lượng tối thiểu 165 lít/phút, áp lực khí nén tối thiểu phải đạt 4at. Bộ phận lọc và điều chỉnh áp lực khí nén có tác dụng ngăn chặn bụi, hơi nước đi vào tay cắt làm hỏng điện cực volfram, đồng thời dùng để điều chỉnh áp lực khí nén đi vào nguồn cắt. 2.2 Nguyên lý cắt plasma - Khi cắt bằng hồ quang plasma thì dưới tác dụng của nhiệt độ cao trong hồ quang nén, khí cắt 2 khi đi qua vùng tích điện hồ quang sẽ bị ion hóa rất mạnh, tạo thành luồng plasma làm nóng chảy kim loại mép cắt. Hồ quang 1 tạo thành giữa kim loại cắt 4 và điện cực volfram không nóngchảy 5 phân bố bên trong đầu cắt 6. Chất khí tạo plasma được đưa vào buồng hồ quang và thoát ra khỏi vòi cắt dưới dạng cột khí hình trụ . Anod là kim loại cần cắt trong trường Hình 5-1: Sơ đồ nguyên lý cắt plasma hợp hồ quang trực tiếp hoặc thân vòi cắt trong trường hợp gián tiếp. Thân vòi cắt củng được sử dụng như anod ở giai đoạn khởi động cắt, việc gây hồ quang được thực hiện bằng cách tạo điện áp trong khoảng không gian hồ quang thông qua nguồn điện cắt và dưới dạng điện áp cao, tần số cao. Catod của mỏ cắt được chế tạo từ kim loại có nhiệt độ nóng chảy cao và đặc tính bức xạ điện tử tốt. ví dụ : Vonfram cho môi trường plasma trung tính , Zr hoặc hafnium cho môi trường mang tính oxi hóa cao Vận hành thiết bị cắt plasma. Đấu điện vào máy nén khí. Lắp ống dẫn khí từ máy nén khí vào nguồn cắt. Đấu điện vào nguồn cắt. Kiểm tra rò khí: chỗ nối máy nén khí và dây khí, chỗ nối dây khí và nguồn cắt. Đóng cầu dao điện Nhấn công tắc tại tay cắt phát sinh hồ quang sau khi đã kẹp mát vào chi tiết. 4.Chế độ cắt plasma Thông số chế độ cắt. - Cắt mồi : Cắt từ mép tấm hoặc đánh thủng. Khi đánh thủng , tốc độ cắt nhỏ hơn 1,5 – 2 lần tốc độ cắt thông thường. - Cắt thẳng hoặc cắt theo biên dạng cong cho trước. - Kết thúc cắt. - Tốc độ cắt : Công thức : v = 0.24.I.U.η / γ.b.s.S ( cm/s). Trong đó : I – dòng cắt ( A). U – điện áp cắt ( V). η = 0.3 hiệu suất hồ quang γ khối lượng riêng vật cắt. b chiều rộng khe cắt. S ethanol nóng chảy ( KJ/ g). Kỹ thuật cắt plasma Cắt tiếp xúc bằng tay. Khi cắt các tấm có chiều dày nhỏ hơn 9 ÷ 12mm có thể cho điện cực tiếp xúc với bề mặt vật cắt. Trình tự thao tác như sau: - Ấn công tắc ở tay cắt, hồ quang mồi được tạo ra sau ,5 giây. - Đưa đầu cắt lại gần vị trí cắt với khoảng cách chừng 1 ÷ 3mm, hồ quang plasma sẽ hình thành; hồ quang mồi tự động cắt. - Cho đầu cắt tiếp xúc với bề mặt vật cắt, dịch chuyển tay cắt theo đường cắt đã vạch. - Đến cuối đường cắt, nhấc tay cắt lên 1 ÷ 3mm, cắt đứt hẳn tấm kim loại cần cắt. - Hồ quang plasma ngắt. Hồ quang mồi 1 ÷ 3mm Plasma Nhỏ hơn 9 ÷ 12mm 1 ÷ 3mm Hình 5-2: Sơ đồ cắt tiếp xúc bằng tay. 5.2 Cắt không tiếp xúc bằng tay. Hồ quang mồi 2 ÷ 4mm Plasma Lớn hơn 9mm Sử dụng khi cắt các tấm có chiều dày trung bình (>9mm). Trình tự thao tác như sau: Hình 5-3: Sơ đồ cắt không tiếp xúc bằng tay Ấn công tắc ở tay cắt, hồ quang mồi được tạo ra sau ,5 giây. Đưa đầu cắt lại gần vị trí cắt cách bề mặt vật cắt 2 ÷ 4mm, hồ quang plasma sẽ hình thành. - Giữ khoảng cách giữa đầu cắt và bề mặt vật cắt trong khoảng 2 ÷ 4mm, di chuyển đầu cắt để cắt. - Đến cuối đường cắt cho tốc độ chậm lại một chút để cắt rời phần cuối đường cắt. - Hồ quang plasma ngắt. 6. An toàn khi cắt plasma - Tiến ồn, tần số cao. - Khí thải, hơi thoát ra từ quá trình cắt ( Oxit kim loại, ozon, oxit nitơ .) - Bức xạ hồ quang, bức xạ nhiệt. - Điện áp cao gây nguy hiểm. + Để giảm tác hại của các yếu tố trên, các biện pháp an toàn lao động đối với hàn và cắt nói chung đều được áp dụng. Ngoài ra người ta còn sử dụng nước để tăng độ an toàn và cải thiện điều kiện làm việc khi cắt. Bài 06: MÀI MÉP HÀN, MÉP CÙN BẰNG MÁY MÀI CẦM TAY 1.Cấu tạo, nguyên lý làm việc của các loại máy mài. 1.1 Cấu tạo của máy mài 2 đá. Cấu tạo gồm các bộ phận chính sau: Đá mài Kính bảo vệ Bệ tỳ Động cơ Nắp bảo vệ Chân đỡ máy. 1.2: Nguyên lý chuyển động. Trên tất cả các loại máy mài chuyển động chính v là chuyển động vòng của đá mài. Chuyển động chạy dao trên máy mài rất khác nhau phụ thuộc vào ính chất từng máy. 2. Vận hành máy mài 2.1 Máy mài 2 đá a. Kiểm tra an toàn - Quay đá bằng tay, kiểm tra xem có các vết xước hoặc nứt không. - Kiểm tra, đảm bảo khe hở giữa bệ tỳ và đá không lớn quá 3 mm. - Kiểm tra đảm bảo khe hở giữa kính bảo vệ và đá không lớn quá 10 mm. Khoảng 10 mm Khoảng 3 mm b. Bắt đầu chạy máy - Không đứng thẳng ở phía trước đá mài. - Bật công tắc nguồn, chờ cho đá quay đủ tốc độ tiêu chuẩn. Nếu nhiều tiếng ồn hoặc rung thì phải tắt máy kiểm tra. Bệ tỳ Tránh Tránh 2.1 Máy mài cầm tay a. Kiểm tra an toàn - Đeo kính bảo hộ và găng tay. - Kiểm tra không có chất dễ cháy nổ ở gần khu vực làm việc. - Kiểm tra không có người đứng trên hướng các tia lửa bắn ra. Kính bảo hộ Găng tay b. Kiểm tra máy mài: - Kiểm tra đá mài trước khi lắp. - Kiểm tra tình trạng lắp chặt của đá. Cà lê chuyên dùng c. Cắm phích cắm vào nguồn - Kiểm tra công tắc trên máy ở vị trí OFF. - Cắm phích nối dây tiếp đất. ổ cắm - Cắm phích cắm vào nguồn. Nối đất d. Cầm máy mài - Cầm máy mài chắc chắn bằng cả hai tay. e. Bật công tắc - Gạt công tắc về vị trí ON. - Để máy mài chạy không khoảng 1 phút. - Kiểm tra không có gì bất bình thường xảy ra trong quá trình máy chạy. - Chạy không tải h. Tắt công tắc - Nâng đá lên khỏi bề mặt vật. - Tắt công tắc. - Đợi đá đứng yên. - Đặt đá mài trên giá đỡ. 3. Kỹ thuật mài 3.1 Mài 2 đá - Cầm mũi sửa đá bằng cả hai tay và tỳ vào bệ tỳ. - Đẩy mũi sửa đá cho chạm vào mặt đá. - Di chuyển mũi sửa đá nhẹ nhàng sang trái và phải, mài đá cho đến hết các vết lõm và mặt đá bằng phẳng. 3.2: Mài cầm tay - Cầm chếch máy một góc khoảng 150 ~ 300 và cho cạnh đá tiếp xúc với vật. - Di chuyển đá trên mặt vật về phía trước, phía sau, sang phải và sang trái với lực ấn đều. 4. An toàn khi mài Chú ý khi sử dụng máymài: - Luôn đeo kính bảo hộ và găng tay. - Không sử dụng đá có đường kính lớn hơn tiêu chuẩn. - Luôn có bước chạy không trước khi mài. - Không tỳ đá quá mạnh hoặc đột ngột vào vật. - Để các chất dễ cháy nổ xa nơi làm việc. - Cầm máy mài cẩn thận và chú ý chỗ để chân khi mài. - Nếu tỳ đá quá mạnh vào vật khi mài, đá sẽ bị cháy. - Máy mài cầm tay thường được dùng để mài gỉ sét trên bề mặt vật trước khi hàn, mài xỉ hàn trong các khe rãnh hoặc mài các cạnh sau khi cắt. Phòng chống điện giật - Cần phải lắp đặt một áp tô mát phù hợp vào nguồn điện đồng thời áp tô mát phải làm việc với độ tin cậy cao. - Tránh làm việc ở nơi ẩm ướt dễ gây ra điện giật
File đính kèm:
de_cuong_che_tao_phoi_han.doc