Giáo trình môn Cơ khí đại cương
QUI TRÌNH CÔNG NGHỆ
QTCN là một phần của quá trình sản xuất nhằm trực tiếp làm thay đổi trạng thái của đối
tượng sản xuất theo một thứ tự chặt chẽ, bằng một công nghệ nhất định. Ví dụ: QTCN nhiệt luyện
nhằm làm thay đổi tính chất vật lý của vật liệu chi tiết như độ cứng, độ bền.v.v.Các thành phần
của quy trình công nghệ bao gồm:
a/ Nguyên công: là một phần của quá trình công nghệ do một hoặc một nhóm công nhân
thực hiện liên tục tại một chỗ làm việc để gia công chi tiết (hay một nhóm chi tiết cùng gia công
một lần).
b/ Bước: là một phần của nguyên công để trực tiếp làm thay đổi trạng thái hình dáng kỹ
thuật của sản phẩm bằng một hay một tập hợp dụng cụ với chế độ làm việc không đổi. Khi thay
đổi dụng cụ, thay đổi bề mặt, thay đổi chế độ.ta đã chuyển sang một bước mới.
c/ Động tác: là tập hợp các hoạt động, thao tác của công nhân để thực hiện nhiệm vụ của
bước hoặc nguyên công.
1.1.5. DẠNG SẢN XUẤT
Tuỳ theo quy mô sản xuất, đặc trưng về tổ chức, trang bị kỹ thuật và quy trình công nghệ
mà có các dạng sản xuất sau:
a/ Sản xuất đơn chiếc: là dạng sản xuất mà sản phẩm được sản xuất ra với số lượng ít và
thường ít lặp lại và không theo một quy luật nào. Chủng loại mặt hàng rất đa dạng, số lượng mỗi
loại rất ít vì thế phân xưởng, nhà máy thường sử dụng các dụng cụ, thiết bị vạn năng. Đây là dạng
sản xuất thường dùng trong sửa chữa, thay thế.
b/ Sản xuất hàng loạt: là dạng sản xuất mà sản phẩm được chế tạo theo lô (loạt) được lặp
đi lặp lại thường xuyên sau một khoảng thời gian nhất định với số lượng trong loạt tương đối
nhiều (vài trăm đến hàng nghìn) như sản phẩm của máy bơm, động cơ điện.v.v.Tuỳ theo khối
lượng, kích thước, mức độ phức tạp và số lượng mà phân ra dạng sản xuất hàng loạt nhỏ, vừa và
lớn. Trong sản xuất hàng loạt các dụng cụ, thiết bị sử dụng là các loại chuyên môn hoá có kèm cả
loại vạn năng hẹp.
c/ Sản xuất hàng khối: hay sản xuất đồng loạt là dạng sản xuất trong đó sản phẩm được
sản xuất liên tục trong một thời gian dài với số lượng rất lớn. Dạng sản xuất này rất dể cơ khí hoá
và tự động hoá như xí nghiệp sản xuất đồng hồ, xe máy, ô tô, xe đạp.v.v.
Tóm tắt nội dung tài liệu: Giáo trình môn Cơ khí đại cương
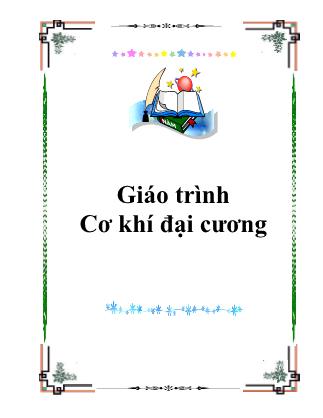
Giáo trình Cơ khí đại cương GIÁO TRÌNH: CƠ KHÍ ĐẠI CƯƠNG 1 CHƯƠNG 1 CÁC KHÁI NIỆM CƠ BẢN VỀ SẢN XUẤT CƠ KHÍ 1.1. CÁC KHÁI NIỆM VỀ QUÁ TRÌNH SẢN XUẤT 1.1.1. SƠ ĐỒ QUÁ TRÌNH SẢN XUẤT CƠ KHÍ Kỹ thuật cơ khí là môn học giới thiệu một cách khái quát quá trình sản xuất cơ khí và phương pháp công nghệ gia công kim loại và hợp kim để chế tạo các chi tiết máy hoặc kết cấu máy. Quá trình sản xuất và chế tạo đó bao gồm nhiều giai đoạn khác nhau được tóm tắt như sau: Tài nguyên thiên nhiên Chế tạo vật liệu Chế tạo phôi Gia công cắt gọt Xử lý và bảo vệ Chi tiết máy Quặng, nhiên liệu, chất trợ dung Luyện kim Đúc, cán, rèn dập, hàn... Tiện, phay, bào, khoan, mài... Nhiệt luyện, hoá nhiệt luyện, mạ, sơn... Phi kim Phế phẩm và phế liệu Phế phẩm và phế liệu Thép, gang, đồng, nhôm, hợp kim H.1.1.Sơ đồ quá trình sản xuất cơ khí 1.1.2. QUÁ TRÌNH THIẾT KẾ Là quá trình khởi thảo, tính toán, thiết kế ra một dạng sản phẩm thể hiện trên bản vẽ kỹ thuật, thuyết minh, tính toán, công trình v.v...Đó là quá trình tích luỹ kinh nghiệm, sử dụng những thành tựu khoa học kỹ thuật để sáng tạo ra những sản phẩm mới ngày càng hoàn thiện. Bản thiết kế là cơ sở để thực hiện quá trình sản xuất, là cơ sở pháp lý để kiểm tra, đo lường, thực hiện các hợp đồng. v.v... GIÁO TRÌNH: CƠ KHÍ ĐẠI CƯƠNG 2 1.1.3. QUÁ TRÌNH SẢN XUẤT: Quá trình sản xuất là quá trình tác động trực tiếp của con người thông qua công cụ sản xuất nhằm biến đổi tài nguyên thiên nhiên hoặc bán thành phẩm thành sản phẩm cụ thể đáp ứng yêu cầu của xã hội. Quá trình sản xuất thường bao gồm nhiều giai đoạn. Mỗi giai đoạn tương ứng với một công đoạn, một phân xưỡng hay một bộ phận....làm những nhiệm vụ chuyên môn khác nhau. Quá trình sản xuất được chia ra các công đoạn nhỏ, theo một quá trình công nghệ. 1.1.4. QUI TRÌNH CÔNG NGHỆ QTCN là một phần của quá trình sản xuất nhằm trực tiếp làm thay đổi trạng thái của đối tượng sản xuất theo một thứ tự chặt chẽ, bằng một công nghệ nhất định. Ví dụ: QTCN nhiệt luyện nhằm làm thay đổi tính chất vật lý của vật liệu chi tiết như độ cứng, độ bền.v.v...Các thành phần của quy trình công nghệ bao gồm: a/ Nguyên công: là một phần của quá trình công nghệ do một hoặc một nhóm công nhân thực hiện liên tục tại một chỗ làm việc để gia công chi tiết (hay một nhóm chi tiết cùng gia công một lần). b/ Bước: là một phần của nguyên công để trực tiếp làm thay đổi trạng thái hình dáng kỹ thuật của sản phẩm bằng một hay một tập hợp dụng cụ với chế độ làm việc không đổi. Khi thay đổi dụng cụ, thay đổi bề mặt, thay đổi chế độ...ta đã chuyển sang một bước mới. c/ Động tác: là tập hợp các hoạt động, thao tác của công nhân để thực hiện nhiệm vụ của bước hoặc nguyên công. 1.1.5. DẠNG SẢN XUẤT Tuỳ theo quy mô sản xuất, đặc trưng về tổ chức, trang bị kỹ thuật và quy trình công nghệ mà có các dạng sản xuất sau: a/ Sản xuất đơn chiếc: là dạng sản xuất mà sản phẩm được sản xuất ra với số lượng ít và thường ít lặp lại và không theo một quy luật nào. Chủng loại mặt hàng rất đa dạng, số lượng mỗi loại rất ít vì thế phân xưởng, nhà máy thường sử dụng các dụng cụ, thiết bị vạn năng. Đây là dạng sản xuất thường dùng trong sửa chữa, thay thế... b/ Sản xuất hàng loạt: là dạng sản xuất mà sản phẩm được chế tạo theo lô (loạt) được lặp đi lặp lại thường xuyên sau một khoảng thời gian nhất định với số lượng trong loạt tương đối nhiều (vài trăm đến hàng nghìn) như sản phẩm của máy bơm, động cơ điện.v.v...Tuỳ theo khối lượng, kích thước, mức độ phức tạp và số lượng mà phân ra dạng sản xuất hàng loạt nhỏ, vừa và lớn. Trong sản xuất hàng loạt các dụng cụ, thiết bị sử dụng là các loại chuyên môn hoá có kèm cả loại vạn năng hẹp. c/ Sản xuất hàng khối: hay sản xuất đồng loạt là dạng sản xuất trong đó sản phẩm được sản xuất liên tục trong một thời gian dài với số lượng rất lớn. Dạng sản xuất này rất dể cơ khí hoá và tự động hoá như xí nghiệp sản xuất đồng hồ, xe máy, ô tô, xe đạp.v.v... 1.1.6. KHÁI NIỆM VỀ SẢN PHẨM VÀ PHÔI a/ Sản phẩm: là một danh từ quy ước để chỉ một vật phẩm được tạo ra ở giai đoạn cuối cùng của một quá trình sản xuất, tại một cơ sở sản xuất. Sản phẩm có thể là máy móc hoàn chỉnh hay một bộ phận, cụm máy, chi tiết...dùng để lắp ráp hay thay thế. b/ Chi tiết máy: là đơn vị nhỏ nhất và hoàn chỉnh về mặt kỹ thuật của máy như bánh răng, trục cơ, bi v.v... GIÁO TRÌNH: CƠ KHÍ ĐẠI CƯƠNG 3 c/ Phôi: còn gọi là bán thành phẩm là danh từ kỹ thuật được quy ước để chỉ vật phẩm được tạo ra từ một quá trình sản xuất này chuyển sang một quá trình sản xuất khác. Ví dụ: sản phẩm đúc có thể là chi tiết đúc (nếu đem dùng ngay) có thể là phôi đúc nếu nó cần gia công thêm (cắt gọt, nhiệt luyện, rèn dập...) trước khi dùng. Các phân xưởng chế tạo phôi là đúc, rèn, dập, hàn, gò, cắt kim loại v.v.. 1.1.7. KHÁI NIÊM VỀ CƠ CẤU MÁY VÀ BỘ PHẬN MÁY a/ Bộ phận máy: đây là một phần của máy, bao gồm 2 hay nhiều chi tiết máy được liên kết với nhau theo những nguyên lý máy nhất định (liên kết động hay liên kết cố định) như hộp tốc độ, mayơ xe đạp v.v... b/ Cơ cấu máy: đây là một phần của máy hoặc bộ phận máy có nhiện vụ nhất định trong máy. Ví dụ: Đĩa, xích, líp của xe đạp tạo thành cơ cấu chuyển động xích trong xe đạp. 1.2. KHÁI NIỆM VỀ CHẤT LƯỢNG BỀ MẶT CỦA SẢN PHẨM Chất lượng bề mặt của các chi tiết máy đóng một vài trò rất quan trọng cho các máy móc thiết bị có khả năng làm việc chính xác để chịu tải trọng, tốc độ cao, áp lực lớn, nhiệt độ.v.v... Nó được đánh giá bởi độ nhẵn bề mặt và tính chất cơ lý của lớp kim loại bề mặt. 1.2.1. ĐỘ NHẴN BỀ MẶT (NHÁM) Bề mặt chi tiết sau khi gia công không bằng phẳng một cách lý tưởng như trên bản vẽ mà có độ nhấp nhô. Những nhấp nhô này là do vết dao để lại, của rung động trong quá trình cắt.v.v... h1 h2 h3 h4 h5 h6 h9h10 y1 yn y x L 0 H.1.2. Độ nhám bề mặt chi tiết RmaxĐường đỉnh Đường đáy Độ bóng bề mặt là độ nhấp nhô tế vi của lớp bề mặt (H.1.2) gồm độ lồi lõm, độ sóng, độ bóng (nhám). Để đánh giá độ nhấp nhô bề mặt sau khi gia công người ta dùng hai chỉ tiêu đó là Ra và Rz (µm). TCVN 2511- 95 cũng như ISO quy định 14 cấp độ nhám được ký hiệu √ kèm theo các trị số. - Ra là sai lệch trung bình số học các khoảng cách từ những điểm của profil đo được đến đường trung bình ox đo theo phương vuông góc với đường trung bình của độ nhấp nhô tế vi trên chiều dài chuẩn L. Ta có thể tính: R L ydxa L = ∫1 0 → ( ) ∑ = =++++= n i ina yn yyyy n R 1 321 1...1 . - Rz là chiều cao nhấp nhô tế vi trên chiều dài chuẩn L với giá trị trung bình của tổng các giá trị tuyệt đối của chiều cao 5 đỉnh cao nhất h1, h3, h5, h7, h9 và chiều sâu của 5 đáy thấp nhất h2, h4, h6, h8, h10 của profin trong khoảng chiều dài chuẩn. ( ) ( ) 5 1042921 hhhhhhRz +++−+++= LL . a/ H.1.3. Ký hiệu độ bóng a/ Ký hiệu độ bóng theo Ra b/ Ký hiệu độ bóng theo RZ b/ Rz202,5 Từ cấp 6 ÷ 12, chủ yếu dùng Ra, còn đối với các cấp 1 ÷ 5 và 13 ÷ 14 dùng Rz. khi ghi trên bản vẽ độ bóng được thể hiện như H.1.3. Trong thực tế sản xuất, tuỳ theo các phương pháp gia công khác nhau ta có các cấp độ bóng khác nhau. Ví dụ: GIÁO TRÌNH: CƠ KHÍ ĐẠI CƯƠNG 4 • Bề mặt rất thô, thô đạt cấp 1 ÷ 3 (Rz = 320 ÷ 40): đúc, rèn • Gia công nửa tinh và tinh đạt cấp 4÷6 (Rz = 40÷10, Ra = 2,5): tiện, phay, khoan. • Gia công tinh đạt cấp 6 ÷ 8 (Ra = 2,5 ÷ 0,32): khoét, doa, mài. Các giá trị thông số độ nhám bề mặt (TCVN 2511 - 78) Cấp Trị số nhám (µm) Chiều dài Phương pháp Ưng dụng độ nhám Ra Rz chuẩn L(mm) gia công 1 2 3 - - - 320 - 160 160 - 80 80 - 40 8 8 8 Tiện thô, cưa, dũa, khoan ... Các bề mặt không tiếp xúc, không quan trọng: giá đỡ, chân máy v.v... 4 5 - - 40 - 20 20 - 10 2,5 2,5 Tiện tinh, dũa tinh, phay... Bề mặt tiếp xúc tĩnh, động, trục vít, b. răng ... 6 7 8 2,5-1,25 1,25-0,63 0,63-0,32 - - - 2,5 0,8 0,8 Doa, mài, đánh bóng v.v... Bề mặt tiếp xúc động: mặt răng, mặt pittông, xi lanh, chốt v.v... 9 10 11 12 0,32-0,16 0,16-0,08 0,08-0,04 0,04-0,02 - - - - 0,8 0,25 0,25 0,25 Mài tinh mỏng, nghiền, rà, gia công đặc biệt, ph. pháp khác Bề mặt mút, van, bi, con lăn, dụng cụ đo, căn mẫu v.v... 13 14 - - 0,1 - 0,05 0,05 - 0,025 0,08 0,08 Bề mặt làm việc chi tiết chính xác, dụng cụ đo 1.2.2. TÍNH CHẤT CƠ LÝ CỦA LỚP BỀ MẶT SẢN PHẨM Tính chất cơ lý của lớp bề mặt gồm cấu trúc tế vi bề mặt, độ cứng tế vi, trị số và dấu của ứng suất dư bề mặt. Chúng ảnh hưởng nhiều đến tuổi thọ của chi tiết máy. Cấu trúc tế vi và tính chất cơ lý của lớp bề mặt chi tiết sau gia công được giới thiệu trên H.1.4: a/ Mặt ngoài bị phá huỷ (1) do chịu lực ép và ma sát khi cắt gọt, nhiệt độ tăng cao. Ngoài cùng là màng khí hấp thụ dày khoảng 2÷3 ăngstron (1Ă = 10-8cm), nó hình thành khi tiếp xúc với không khí và mất đi khi bị nung nóng. Sau đó là lớp bị ôxy hoá dày khoảng (40 ÷ 80)Ă. b/ Lớp cứng nguội (2) là lớp kim loại bị biến dạng dẻo có chiều dày khoảng 50.000Ă, với độ cứng cao thay đổi giảm dần từ ngoài vào, làm tính chất cơ lý thay đổi. Kim loại cơ bản từ vùng (3) trở vào. 1 2 3 h H.1.4. Tính chất cơ lý lớp bề mặt 1- Mặt ngoài bị phá huỷ 2- Lớp cứng nguội 3- Kim loại cơ bản h- Chiều sâu kim loại HB- Độ cứng HB 1.3. KHÁI NIỆM VỀ ĐỘ CHÍNH XÁC GIA CÔNG CƠ KHÍ GIÁO TRÌNH: CƠ KHÍ ĐẠI CƯƠNG 5 1.3.1. KHÁI NIỆM VỀ ĐỘ CHÍNH XÁC GIA CÔNG Độ chính xác gia công của chi tiết máy là đặc tính quan trọng của ngành cơ khí nhằm đáp ứng yều cầu của máy móc thiết bị cần có khả năng làm việc chính xác để chịu tải trọng, tốc độ cao, áp lực lớn, nhiệt độ v.v... Độ chính xác gia công là mức độ chính xác đạt được khi gia công so với yêu cầu thiết kế. Trong thực tế độ chính xác gia công được biểu thị bằng các sai số về kích thước, sai lệch về hình dáng hình học, sai lệch về vị trí tương đối giữa các yếu tố hình học của chi tiết được biểu thị bằng dung sai. Độ chính xác gia công còn phần nào được thể hiện ở hình dáng hình học lớp tế vi bề mặt. Đó là độ bóng hay độ nhẵn bề mặt, còn gọi là độ nhám. 1.3.2. DUNG SAI a/ Khái niệm: Khi chế tạo một sản phẩm, không thể thực hiện kích thước, hình dáng, vị trí chính xác một cách tuyệt đối để có sản phẩm giống hệt như mong muốn và giống nhau hàng loạt, vì việc gia công phụ thuộc vào nhiều yếu tố khách quan như độ chính xác của dụng cụ, thiết bị gia công, dụng cụ đo, trình độ tay nghề của công nhân v.v...Do đó mọi sản phẩm khi thiết kế cần tính đến một sai số cho phép sao cho đảm bảo tốt các yêu cầu kỹ thuật, chức năng làm việc và giá thành hợp lý. Dung sai đặc trưng cho độ chính xác yêu cầu của kích thước hay còn gọi là độ chính xác thiết kế và được ghi kèm với kích thước danh nghĩa trên bản vẽ kỹ thuật. Trị số dung sai kích thước (IT- µm) D (d) Cấp chính xác ≤ 3 > 3 ÷ 6 > 6 ÷ 10 > 10 ÷ 18 > 18 ÷ 30 > 30 ÷ 50 > 50 ÷ 80 > 80 ÷ 120 > 120 ÷ 180 >180 ÷ 250 5 6 7 8 9 10 11 12 4 6 10 14 25 40 60 100 6 8 12 18 30 48 75 120 8 9 15 22 36 58 90 150 8 11 18 27 43 70 110 180 9 13 21 33 52 84 130 210 11 16 25 39 62 100 160 250 13 19 30 46 74 120 190 300 15 22 35 54 87 140 220 350 18 25 40 63 100 160 250 400 20 29 46 72 115 185 290 460 D (d) - Kích thước danh nghĩa của chi tiết. b/ Dung sai kích thước: Dung sai kích thước là sai số cho phép giữa kích thước đạt được sau khi gia công và kích thước danh nghĩa. Đó là hiệu giữa kích thước giới hạn lớn nhất và nhỏ nhất hoặc hiệu đại số giữa sai lệch trên và sai lệch dưới. Theo TCVN 2244 - 99 cũng như ISO ký hiệu chữ in hoa dùng cho lỗ, ký hiệu chữ thường dùng cho trục. Trong đó: D (d): Kích thước danh nghĩa, sử dụng theo kích thước trong dãy ưu tiên của TCVN 192 - 66. GIÁO TRÌNH: CƠ KHÍ ĐẠI CƯƠNG 6 b/ Dung sai kích thước trục a/ Dung sai kích thước lỗ d d m ax d m inD D m ax D m in es ei E EI IT t IT l H.1.5. Dung sai kích thước trục và lỗ - Dmax, dmax: kích thước giới hạn lớn nhất. - Dmin, dmin: kích thước giới hạn nhỏ nhất. - ES = Dmax - D, es = dmax - d : sai lệch trên. - EI = Dmin - D, ei = dmin - d : sai lệch dưới. - ITl = Dmax - Dmin = ∆D = ES - EJ : khoảng dung sai của lỗ. - ITt = dmax - dmin = ∆d = es - ei : khoảng dung sai của trục. Dung sai lắp ghép là tổng dung sai của lỗ và trục. c/ Miền dung sai Lỗ là tên gọi được dùng để ký hiệu các bề mặt trụ trong các chi tiết. Theo ISO và TCVN miền dung sai của lỗ được ký hiệu bằng một chữ in hoa A, B, C..., ZA, ZB, ZC (ký hiệu sai lệch cơ bản) và một số (ký hiệu cấp chính xác), trong đó có lỗ cơ sở có sai lệch cơ bản H với EI = 0 (Dmin= D), cấp chính xác JS có các sai lệch đối xứng ( EIES = ). K íc h th ướ c da nh n gh ĩa e ef fg za zc f hg z zb x yv j k m p r Miền dung sai trục u t s c dcd b a H.1.6. Vị trí các miền dung sai của Trục và Lỗ + Sa i l ệc h K íc h th ướ c da nh n gh ĩa A B C C D EEF FG ZA ZC F HG J K MN P R S T U V ZYX JS Miền dung sai lỗ ZB Trục là tên gọi được dùng để ký hiệu các bề mặt trụ ngoài bị bao của chi tiết. Miền dung sai của trục được ký hiệu bằng chữ thường a, b, c..., za, zb, zc; trong đó trục cơ bản có cấp chính xác h với ei = 0 (dmax= d), cấp chính xác js có các sai lệch đối xứng ( eies = ). Tri số dung sai và sai lệch cơ bản xác định miền dung sai. Mỗi kích thước được ghi gồm 2 phần: kích thước danh nghĩa và miền dung sai. Trên bản vẽ chế tạo ghi kích thước danh nghĩa và giá trị các sai lệch. Ví dụ: trên bản thiết kế ghi φ20H7, φ40g6 còn trên bản vẽ chế tạo ghi kích thước tương ứng (tra bảng): φ20+0,021, ... φ40 0 0250 009−− ,, d/ Sai số hình dáng và vị trí: Sai số hình dáng hình học là những sai lệch về hình dáng hình học của sản phẩm thực so với hình dáng hình học khi thiết kế như độ thẳng, độ phẳng, độ côn... GIÁO TRÌNH: CƠ KHÍ ĐẠI CƯƠNG 7 Sai số hình dáng hình học Sai số vị trí tương đối các bề mặt TT Tên gọi Ký hiệu TT Tên gọi Ký hiệu 1 Dung sai độ thẳng 1 Dung sai độ song song 2 Dung sai độ phẳng 2 Dung sai độ vuông góc 3 Dung sai độ tròn 3 Dung sai độ đồng tâm 4 Dung sai độ đối xứng 4 Dung sai độ trụ 5 Dung sai độ giao nhau 6 D. sai độ đảo mặt đầu 7 D. sai độ đảo hướng kính Sai lệch vị trí tương đối là sự sai lệch vị trí thực của phần tử được khảo sát so với vị trí danh nghĩa như độ không song song, độ không vuông góc, độ không đồng tâm, độ đảo v.v...Các ký hiệu và ví dụ cách ghi các sai lệch này trên bảng trên. đ/ Cấp chính xác: Cấp chính xác được qui định theo trị số từ nhỏ đến lớn theo mức độ chính xác kích thước. TCVN và ISO chia ra 20 cấp chính xác đánh số theo thứ tự độ chính xác giảm dần là 01, 0, 1, 2, ...15, 16, 17, 18. Trong đó: - Cấp 01 ÷ cấp 1 là các cấp siêu chính xác. - Cấp 1 ÷ cấp 5 là các cấp chính xác cao, cho các chi tiết chính xác, dụng cụ đo. - Cấp 6 ÷ cấp 11 là các cấp chính xác thường, ... mà hệ thống van phân phối khí 7 sẽ tạo ra những đường dẫn khí khác nhau, làm cho pittông búa 8 có gắn thân pittông búa và đe trên 10 chuyển động hay đứng yên trong xi lanh búa 9. Đe dưới 11 được lắp vào gối đỡ đe 12, chúng được giữ chặt trên bệ đe 13. 14 11 12 13 10 9 8 7 6 5 3 4 2 1 Ngoài máy búa hơi trong thực tế còn sử dụng các loại máy sau đây trong rèn tự do: Máy búa hơi nước- không khí ép rèn tự do, Máy búa ma sát kiểu ván gỗ, Máy búa lò xo. H.4.8. Sơ đồ nguyên lý máy búa hơi 1- Động cơ điện 2- Bộ truyền đai 3- Trục khuỷu 4- Tay biên 5- Xi lanh ép 6-Pistông ép 7- Van phân phối khí 8- Pistông búa 9- Xi lanh búa 10- Đe trên 11- Đe dưới 12- gối đỡ đe 13-Bệ đe 14- bàn đạp điều khiển 4.5.3. NHỮNG NGUYÊN CÔNG CƠ BẢN CỦA RÈN TỰ DO a/ nguyên công vuốt: Nguyên công làm giảm tiết diện ngang và tăng chiều dài của phôi rèn. Dùng để rèn các chi tiết dạng trục, ống, dát mỏng hay chuẩn bị cho các nguyên công tiếp theo như đột lỗ, xoắn, uốn. Thông thường khi vuốt dùng búa phẳng, nhưng khi cần vuốt với năng suất cao hơn thì dùng búa có dạng hình chữ V hoặc cung tròn. c b0 b ∆h B L h h0s H.4.9. Sơ đồ vuốt kim loại GIÁO TRÌNH: CƠ KHÍ ĐẠI CƯƠNG 37 b/ Nguyên công chồn: Là nguyên công nhằm tăng tiết diện ngang và giảm chiều cao phôi. Nó thường là nguyên công chuẩn bị cho các nguyên công tiếp theo như đột lỗ, thay dạng thớ trong tổ chức kim loại, làm bằng đầu, chuyển đổi kích thước phôi. Có 2 dạng chồn: - Chồn toàn bộ: là nung cã chiều dài phôi, khi chồn thường xảy ra các trường hợp sau: Khi h d 0 0 2〈 thì vật chồn có dạng hình trống (a). Khi h d 0 0 2 2 5≈ ÷ , Tùy theo độ lớn của lực tác dụng mà có thể xảy ra các b, c, d. b P a P PP H.4.20. Chồn cục bộ H.4.19. Chồn toàn bộ b c Ptb Pnhỏ d PLớd0 h0 a - Chồn cục bộ: Chỉ cần nung nóng vùng cần chồn hay làm nguội trong nước phần không cần chồn rồi mới gia công. Cũng có thể nung nóng toàn bộ rồi gia công trong những khuôn đệm thích hợp. c/ Nguyên công đột lỗ: có 2 dạng Đột lỗ thông suốt: Nếu chi tiết đột mỏng và rộng thì không cần lật phôi trong quá trình đột. Cần phải có vòng đệm để dể thoát phoi. Nếu chiều dày vật đột lớn thì đột đến 70÷80% chiều sâu lỗ, lật phôi 1800 để đột phần còn lại. Nếu lỗ đột quá sâu (h/d ≥ 2,5) thì khi hết mũi đột ta dùng các trụ đệm để đột đến chiều sâu yêu cầu. Nếu lỗ đột có đường kính quá lớn (D>50÷100mm) nên dùng mũi đột rỗng để giảm lực đột. Đột lỗ không thông: Được coi như là giai đoạn đầu của đột lỗ thông, song để biết được chiều sâu lỗ đã đột thì trên mũi đột và trụ đệm phải được khắc dấu. không dùng được mủi đột rỗng. Nếu lỗ đột lớn trước hết dùng mũi đột nhỏ để đột, sau đó dùng mũi đột lớn dần cho đến đường kính yêu cầu. Vì rằng sự biến dạng trong khi đột lỗ không thông rất khó khăn. GIÁO TRÌNH: CƠ KHÍ ĐẠI CƯƠNG 38 4.6. DẬP THỂ TÍCH 4.6.1. KHÁI NIỆM CHUNG a/ Định nghĩa: Dập thể tích là phương pháp gia công áp lực trong đó kim loại biến dạng trong một không gian hạn chế bởi bề mặt lòng khuôn. Quá trình biến dạng của phôi trong lòng khuôn phân thành 3 giai đoạn: giai đoạn đầu chiều cao của phôi giảm, kim loại biến dạng và chảy ra xung quanh, theo phương thẳng đứng phôi chịu ứng suất nén, còn phương ngang chịu ứng suất kéo. Giai đoạn 2: kim loại bắt đầu lèn kín cửa ba-via, kim loại chịu ứng suất nén khối, mặt tiếp giáp giữa nữa khuôn trên và dưới chưa áp sát vào nhau. Giai đoạn cuối: kim loại chịu ứng suất nén khối triệt để, điền đầy những phần sâu và mỏng của lòng khuôn, phần kim loại thừa sẽ tràn qua cửa bavia vào rãnh chứa bavia cho đến lúc 2 bề mặt của khuôn áp sát vào nhau. p 1 2 3 4 5 6 H.4.21. Sơ đồ kết cấu của một bộ khuôn rèn 1-khuôn trên; 2- rãnh chứa ba-via; 3- khuôn dưới; 4- chuôi đuôi én; 5- lòng khuôn; 6- cửa ba-via b/ Đặc điểm - Độ chính xác và độ bóng bề mặt phôi cao (cấp 6 - 7; RZ = 80 ÷ 20) - Chất lượng sản phẩm đồng đều và cao, ít phụ thuộc tay nghề công nhân. - Có thể tạo phôi có hình dạng phức tạp hơn rèn tự do. - Năng suất cao, dễ cơ khí hoá và tự động hóa. - Thiết bị cần có công suất lớn, độ cứng vững và độ chính xác cao. - Chi phí chế tạo khuôn cao, khuôn làm việc trong điều kiện nhiệt độ và áp lực cao. Bởi vậy dập thể tích chủ yếu dùng trong sản xuất hàng loạt và hàng khối. 4.6.2. THIẾT BỊ DẬP THỂ TÍCH Thiết bị dùng trong dập thể tích bao gồm nhiều loại khác nhau như thiết bị nung, thiết bị vận chuyển, máy cắt phôi, thiết bị làm nguội, thiết bị kiểm tra v.v...Tuy nhiên ở đay ta chỉ nghiên cứu một số máy gia công chính. Dập thể tích đòi hỏi phải có lực dập lớn, bởi vậy các máy dập phải có công suất lớn, độ cứng vững của máy cao. Mặt khác, do yêu cầu khi dập khuôn trên và khuôn dưới phải định vị chính xác với nhau, chuyển động của đầu trượt máy dập phải chính xác, ít gây chấn động. Trong dập thể tích thông dụng nhất là sử dụng các loại máy sau: máy búa hơi nước - không khí nén, máy ép trục khuỷu, máy ép thuỷ lực, máy ép ma sát trục vít. a/ Máy ép thủy lực Các máy ép thuỷ lực là các loại máy rèn truyền dẫn bằng dòng chất lỏng (dầu hoặc nước) có áp suất cao. Máy được chế tạo với lực ép từ 300 - 7.000 tấn. Máy ép thủy lực có ưu điểm là lực ép lớn, chuyển động của đầu ép êm và chính xác, điều khiển hành trình ép và lực ép dễ dàng. Nhược điểm của máy ép thuỷ lực là chế tạo phức tạp, bảo dưỡng khó khăn. GIÁO TRÌNH: CƠ KHÍ ĐẠI CƯƠNG 39 Để tạo áp lực ép lớn, trong các máy ép thủy lực thường dùng bộ khuếch đại áp suất với hai xi lanh: xi lanh hơi (1) và xi lanh dầu (3). Pittông (2) có hai phần đường kính khác nhau, phần nằm trong xi lanh hơi có đường kính lớn (D) và phần nằm trong xi lanh dầu có đường kính bé (d). Với áp suất hơi p1, áp suất dầu (p2) được tính theo công thức sau: p p D d2 1 2 2= ⋅ b/ Máy ép trục khuỷu Máy ép trục khuỷu có lực ép từ 16÷10.000 tấn. Máy này có loại hành trình đầu con trượt cố định gọi là máy có hành trình cứng; có loại đầu con trượt có thể điều chỉnh được gọi là hành trình mềm. Nhìn chung các máy lớn đều có hành trình mềm. Trên máy ép cơ khí có thể làm được các công việc khác nhau: rèn trong khuôn hở, ép phôi, đột lỗ, cắt bavia v.v... Sơ đồ nguyên lý được trình bày trên hình sau: Nguyên lý làm việc của máy như sau: Động cơ (1) qua bộ truyền đai (2) truyền chuyển động cho trục (3), bánh răng (4) ăn khớp với bánh răng (7) lắp lồng không trên trục khuỷu (5). Khi đóng li hợp (6), trục khuỷu (8) quay, thông qua tay biên (8) làm cho đầu trượt (9) chuyển động tịnh tiến lên xuống, thực hiện chu trình dập. Đe dưới (10) lắp trên bệ nghiêng có thể điều chỉnh được vị trí ăn khớp của khuôn trên và khuôn dưới. Đặc điểm của máy ép trục khuỷu: chuyển động của đầu trượt êm hơn máy búa, năng suất cao, tổn hao năng lượng ít, nhưng có nhược điểm là phạm vi điều chỉnh hành trình bé, đòi hỏi tính toán phôi chính xác và phải làm sạch phôi kỹ trước khi dập. Đến đầu ép Hơi H.4.22. Máy ép trục khuỷu 10 9 8 7 6 5 4 32 1 Bộ khuyết đại áp suất P1 P2 D d 3 2 1 GIÁO TRÌNH: CƠ KHÍ ĐẠI CƯƠNG 40 4.7. KỸ THUẬT DẬP TẤM 4.7.1. KHÁI NIỆM CHUNG a/ Thực chất: Dập tấm là một phương pháp gia công áp lực tiên tiến để chế tạo các sản phẩm hoặc chi tiết bằng vật liệu tấm, thép bản hoặc thép dải. Dập tấm được tiến hành ở trạng thái nguội (trừ thép cácbon có S > 10mm) nên còn gọi là dập nguội. Vật liệu dùng trong dập tấm: Thép cácbon, thép hợp kim mềm, đồng và hợp kim đồng, nhôm và hợp kim nhôm, niken, thiếc, chì vv...và vật liệu phi kim như: giấy cáctông, êbônít, fíp, amiăng, da, vv... b/ Đặc điểm: Năng suất lao động cao do dễ tự động hoá và cơ khí hoá. Chuyển động của thiết bị đơn giản, công nhân không cần trình độ cao, đảm bảo độ chính xác cao. Có thể dập được những chi tiết phức tạp và đẹp, có độ bền cao..v.v... c/ Công dụng: Dập tấm được dùng rộng rãi trong các ngành công nghiệp đặc biệt ngành chế tạo máy bay, nông nghiệp, ôtô, thiết bị điện, dân dụng v.v... 4.7.2. CÔNG NGHỆ DẬP TẤM Công nghệ dập tấm được đặc trưng bởi 2 nhóm nguyên công chính: nguyên công cắt và nguyên công tạo hình. A/ NHÓM NGUYÊN CÔNG CẮT Cắt phôi là nguyên công tách một phần của phôi khỏi phần kim loại chung. Nguyên công này có 3 loại: cắt đứt, cắt phôi, đột lỗ. a/ Cắt đứt: Là nguyên công cắt phôi thành từng miếng theo đường cắt hở, dùng để cắt thành từng dải có chiều rộng cần thiết, cắt thành miếng nhỏ từ những phôi thép tấm lớn. Có các loại máy cắt đứt sau: + + + + B β S H.4.23.Máy cắt lưỡi dao song song Máy cắt lưỡi dao song song: - Góc trước β =2÷30 - Cắt được các tấm rộng B ≥ 3200 mm, chiều dày S đến 60 mm. - Chỉ cắt được đường thẳng, chiều rộng tấm cắt phải nhỏ hơn chiều dài dao. - Đường cắt thẳng, đẹp, hành trình dao nhỏ; Lực cắt tương đối lớn: P = 1,3.B.S.σ c (N). B - chiều rộng cắt của phôi (mm); S - chiều dày phôi cắt (mm). σ c - Giới hạn bền cắt của phôi σ c = (0,6÷0,8)σb (N/mm2). Máy cắt dao nghiêng: - Lưỡi dao dưới nằm ngang, lưỡi dao trên nghiêng một góc α= 2÷60. - Góc cắt δ = 75÷850; góc sau γ = 2÷30. - Độ hở giữa 2 dao Z = 0,05 ÷ 0,2mm - Lực cắt không lớn, cắt được các tấm dày; Cắt được các đường cong; Đường cắt không thẳng và nhẵn. Hành trình của dao lớn: + + + + S δ γ α H.4.24.Máy cắt lưỡi dao nghiêngZ GIÁO TRÌNH: CƠ KHÍ ĐẠI CƯƠNG 41 α β P = 1,3 0 5 2, . .S tg cσ α (N) Máy cắt chấn động: Máy có 2 lưỡi dao nghiêng tạo thành một góc α = 24÷300; góc trước β = 6÷70, khi cắt lưỡi cắt trên lên xuống rất nhanh (2000÷3000 lần/phút) và với hành trình ngắn 2÷3 mm. Cắt được tấm có S ≤ 10 mm. H.4.25. Máy cắt chấn động Máy cắt dao đĩa một cặp dao: c/ Hai dao nghiêng a/ Dao đĩa có tâm trục song song h S B D D SB ϕ b/ Máy cắt dao dưới nghiêng B D h Z H.5.26. Máy cắt dao đĩa một cặp dao Máy cắt nhiều dao đĩa. - Lưỡi cắt là 2 đĩa tròn quay ngược chiều nhau; máy có thể có hai hoặc nhiều cặp đĩa cắt. - Góc cắt 900; Z = (0,1 ÷ 0,2)S - Đường kính dao đĩa: D =(40 ÷ 125)S (mm). - Chiều dày dao: B = 15 ÷ 30 (mm) - Vận tốc cắt: v = 1 ÷ 5 m/s - Vật liệu làm dao: 5XBC Máy này dùng để cắt các đường thẳng và đường cong chiều dài tuỳ ý mỏng < 10 mm. b/ Dập cắt và đột lỗ: Đây là nguyên công cắt mà đường cắt là một chu vi kín. Về nguyên lý dập cắt và đột lỗ giống nhau chỉ khác nhau về công dụng. Đột lỗ là quá trình tạo nên lỗ rỗng trên phôi, phần vật liệu tách khỏi phôi gọi là phế liệu, phần còn lại là phôi để đi qua nguyên công tạo hình. Đối với dập cắt thì phần cắt rời là phôi phần còn lại là phế liệu. Một số thông số kỹ thuật cần lưu ý: - Chày và cối phải có cạnh sắc để tạo thành lưỡi cắt, giữa chày và cối có khoảng hở Z = (5% ÷ 10%)S. - Khi đột muốn có kích thước lỗ đột đã cho thì kích thước của chày chọn bằng kích thước của lỗ, còn kích thước của cối lớn hơn 2Z. Chày vát lõm phía trong để tạo thành rãnh cắt. - Khi cắt phôi có kích thước đã cho thì kích thước của cối bằng kích thước của phôi còn của chày nhỏ thua 2Z. Các loại đầu chày B D Z H.5.26. Máy cắt dao đĩa một cặp dao z H.4.27. Sơ đồ dập cắt và đột lỗ P - Lực cắt hoặc đột P GIÁO TRÌNH: CƠ KHÍ ĐẠI CƯƠNG 42 + Khi đường cắt tròn: P = 1,25π.d.s.τcp (N); + Khi đường cắt bất kỳ: P = 1,25L.s.τcp (N). s - chiều dày phôi (mm); d - đường kính phôi hoặc lỗ đột (mm). L - chu vi đường cắt (mm); τcp- giới hạn bền cắt (N/mm2). B/ NHÓM NGUYÊN CÔNG TẠO HÌNH Là những nguyên công dịch chuyển một phần của phối đối với phần khác mà phôi không bị phá huỷ. a/ Nguyên công uốn: Là nguyên công làm thay đổi hướng của trục phôi. Trong quá trình uốn cong lớp kim loại phía trên bị nén, lớp kim loại phía ngoài bị kéo, lớp kim loại ở giữa không bị kéo nén gọi là lớp trung hoà. Khi bán kính uốn cong càng bé thì mức độ nén và kéo càng lớn có thể làm cho vật uốn cong bị nứt nẻ. Lúc này lớp trung hoà có xu hướng dịch về phía uốn cong. Vị trí và kích thước lớp trung hoà được xác định bởi bán kính lớp trung hoà: ρ α α β= +⎛⎝⎜ ⎞ ⎠⎟ r S S 2 . . . (r - bán kính uốn trong; S - chiều dày phôi (mm); ρ - bán kính lớp trung hoà) b/ Nguyên công dập vuốt: Dập vuốt là nguyên công chế tạo các chi tiết rỗng có hình dạng bất kỳ từ phôi phẳng và được tiến hành trên các khuôn dập vuốt. Khi dập vuốt có thể làm mỏng thành hoặc không làm mỏng thành. - Dập vuốt không làm mỏng thành + Chọn hình dạng và kích thước phôi: Nếu chi tiết là hình hộp đáy chữ nhật thì phôi có dạng hình bầu dục hay elíp, còn nếu chi tiết là hình hộp đáy vuông hoặc hình trụ đáy tròn thì phôi là miếng cắt tròn. Nếu S < 0,5 mm thì diện tích phôi bằng diện tích mặt trong hoặc diện tích mặt ngoài của chi tiết, còn nếu S > 0,5mm thì lấy bằng diện tích lớp trung hoà của chi tiết (kể cã đáy). + Xác định số lần dập vuốt: Khi dập vuốt tuỳ theo tính dẻo của vật liệu mỗi lần dập cho phép dập thành chi tiết có đường kính nhất định. Hệ số dập cho phép được tính như sau: m = d D ct ph = 0,55÷0,95 ; Như vậy: m d D1 1= ⇒ d1 = m1.D; tương tự ta có: d2 = m2.d1 = m1.m2.D; dn = m1.m2.m3...mn.D. d1 d2 d3 dct D Chày Lớp trung hoà r ρx.S Cối H.4.28. Nguyên công uốn H.4.29. Quá trình dập vuốt 1. chày ép; 2. khuôn ép, 3. phôi k.loại; 4. vành ép 1 2 3 4 d1 D PQ Q S Lấy giá trị trung bình: m m mtb nn= − 2 31 . ...m Số lần dập n của phôi có dường kính D thành chi tiết có đường kính dn: n d m m n tb = + −1 1lg lg( . ) lg D + Quá trình dập vuốt: Những chi tiết có phôi là tấm dày thì tiến hành trên khuôn không cần vành ép, nhưng nếu phôi là tấm mỏng sẽ xảy ra hiện tượng nhăn xếp ở thành sản phẩm nên dùng thêm vành ép. GIÁO TRÌNH: CƠ KHÍ ĐẠI CƯƠNG 43 - Dập vuốt làm mỏng thành: Được thực hiện khi độ hở giữa chày và khuôn nhỏ hơn chiều dày phôi. Đường kính giảm ít, chiều sâu tăng nhiều và giảm chiều dày thành phôi. Để rút ngắn số lần dập giãn, một số lần dập đầu không làm mỏng thành, sau đó mới dập giãn làm mỏng thành. c/ Uốn vành: Là phương pháp chế tạo các chi tiết có gờ, đường kính D chiều cao H, đáy chi tiết rỗng. Phôi uốn vành phải đột lỗ với d trước, sau đó dùng chày và khuôn để tạo vành. z =( 0,3-0,8)S P S0 S S0 rch H.4.30. Dập vuốt không làm mỏng thành d H S D R D1 H.4. 31. Sơ đồ uốn vành d d0 - Bán kính lượn của chày và khuôn R = (5÷10)S. - Khe hở giữa chày và cối Z = (8÷10)S. - Lỗ bé dùng chày đầu hình cầu hoặc hình chóp. - Để không xảy ra nứt mép ở vùng lỗ đột thì phải có hệ số uốn vành hợp lý: Ku = d/D = 0,62÷0,78 d/ Tóp miệng: Là nguyên công làm cho miệng của phôi rỗng (thường là hình trụ) thu nhỏ lại. Phần tóp nhỏ lại có thể là hình côn, côn và trụ, nửa hình cầu v.v...Khuôn dưới làm nhiệm vụ định vị chi tiết, khuôn trên có lỗ hình côn đường kính giảm dần, phần cuối của khuôn trên là hình trụ. Để tránh xảy ra hiện tượng xếp ở miệng tóp thì: K d d = = ÷0 1 2 1 3, , Khi cần tóp đến chi tiết có đường kính nhỏ hơn giới hạn cho phép thì phải qua một số lần tóp. e/ Miết Miết là phương pháp chế tạo các chi tiết tròn xoay mỏng. Đặc biệt miết được dùng để chế tạo những chi tiết có đường kính miệng thu nhỏ vào và thân phình ra như bi đông, lọ hoa...kế tiếp sau nguyên công dập vuốt. Cần ép H.4.32. Sơ đồ miết Khuôn Tựa Phôi
File đính kèm:
giao_trinh_mon_co_khi_dai_cuong.pdf