Giáo trình Kỹ thuật nguội
Hình chiếu mặt cắt chia lμm mấy loại? Chọn dùng thé nμo
1. Hình chiếu cả mặt cắt: Hình có đ?ợc khi dùng một mặt cắt toμn bộ chi tiết máy
gọi lμ hình chiếu cả mặt cắt
2. Hình chiếu nửa mặt cắt : Khi chi tiết máy có mặt phẳng đối xứng
có thể lấy đ?ờng tâm đối xứng lμm giớt hạn , mọt nửa vẽ hình chiếu nủa khia
vẽ thμnh hình chiếu mặt cắt : hình 1-9(2)a
3. Hình chiếu mặt cắt cục bộ: Hình có đ?ợc khi dùng
một phần mặt cắt
để cắt chi tiết máy thì gọi lμ hình chiếu mặt cắt cục bộ
.ranh giới giũa các phần
lμ đ?ờng nét
gợn sóng: hình
1-9(3).
Hìmh 1-9(3)
Hình chiếu mặt
cắt cục bộ
4. Hình chiếu mặt cắt xiên: Hình chiếu có đ?ợc khi dùng mặt cắt không song song
với bất cứ một mặt chiếu cơ bản nμo .đẻ cắt chi tiết .rồi chiếu lên mặt phẳng sonh
song với mặt cắt gọi lμ hình chiếu mặt cắ xiên .hình vẽ:
5.Hình chiếu mặt cắt bậc : Hình chiếu có đ?ợc khi dùnh nhiều mặt cắt song
song với nhau để cắt chi tiết máy gọi lμ hình cắt bậc .hình 1-9(5)
6 Hình chiếu mặt cắt xoay : hình tạo ra khi dùng hai mặt cắt giao nhau .Rồi đem
mặt cắt đó xoay đến vị trí song song với mặt chiếu đã chọn . Gọi lμ mặt cắt xoay .hình
1-9(6)
Tóm tắt nội dung tài liệu: Giáo trình Kỹ thuật nguội
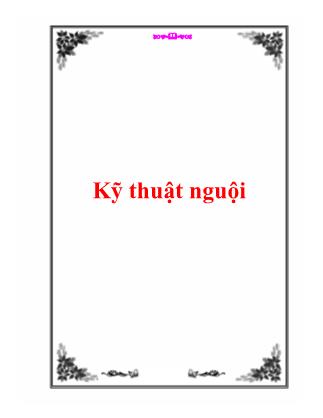
z Kỹ thuật nguội 1 Chơng 1: kiến thc cơ sơ Kỹ thuật Nguội 1. đơn vị độ dμi thờng dùng của công nghiệp cơ giới bao gồm đơn vị đo lờng lấy theo đơn vị quồc tế qui định đơn vị SI .đợc thể hiện dới bảng sau Bảng 1-1: đơn vị độ dμi Tên Ký hiệu Quan hệ đơn vị cơ bản mét ngμn mét centimet milimet mircomet m km cm mm um đơn vị cơ bản 103m 10-2m 10-3m 10-6m Trong công nghiệp cơ khí thông thờng dùng milimet lμm đơn vi đơn độ dμi .Nói chung trong các bản vẽ kĩ thuật chỉ ghi con số đơn vị hoặc khí hiệu khơng ghi đơn vị .Nhiều nớc hoặc một số bộ phận sử dụng đơn vị anh lμ inh: 1inh =25,4mm 2. đơn vị đo góc vμ quan hệ chuyển đổi thờng dùng Trong hệ đơn vị quốc tế,đơn vị SI góc phẳng lμ radian (rad).ngoái ra nớc ta còn sử dụng đơn vị độ(˚) phút (’ ) giây(” ) .Mối liên hệ giữa độ vμ radian đợc biểu thị qua công thức: 1rad = S 180 = 57,29570 Lợng Tên đơn vị Ký hiệu Quan hệ với đơn vị SI Góc Phẳng độ góc độ Phút Giây (˚) (’ ) 1˚ = ( S /180)rad 1’ =(1/60) 1” =(1/60)’ 3. hμm số lợng giác thờng dùng vμ ứng dụng Hμm số lợng giác thòng dùng có 4 loại : sin , cos , tang , cotg. Các hệ t5hức nμy đợc dùng trong tam giác vuông .Chúng đợc xác định bởi: sinA =a/c , cosA = b/c , tgA =a/b , cotgA =b/a Với c, a ,b lμ độ dμi các cạnh có các góc đối lμ C, A , B B C A 2 4. Định lý Pitago. ứng dụng Định lý Pitgo đợc áp dụng cho tam giác vuông.Bình phơng cạnh huyền bằng tổng bình phơng hai cạnh góc vuông. Tức: c2 = a2 + b2 Nếu biết hai cạnh bất kì của tam giác vuông có thể dụa vμo định lý trên để tìm cạnh thứ 3 5. Định lý sin , cos , ứng dụng của hμm số đó Định lý sin : vtrong ftam giác bất kì , độ dμi cạnh huỳên tỉ lệ sin góc đối của nó Tức lμ : C c B b A a sinsinsin Định lý cos :trong tam giác bất kì bình phơng cạnh đối của mọt góc nμo đó se bằng tổnh bình phơng hai cạnh còn lại tr đi hai lần tích hai cạnh kia với cos của góc giũa hai cạnh đó .Tức lμ : a2 = b2 + c2 – 2bccosA b2 = a2+ c2 - 2accosB c2 = a2 +b2 - 2abcosC 6. Độ côn lμ gì ? Độ côn thờng dùng mấy loại ? Độ côn (C) lμ tỉ số hiệu đầu to , đầu nhỏ với độ dμi hớng trục giũa hai đμu vật thể hình nón L D d độ côn thờng dùng trong công nghiệp cơ khí có : 1:100; 1:50 ; 1:5 ;...Cán hình côn nh mũi khoan doa lỗ , dao doa đều dùng độ côn M (0 ~ 6) 7. Cách tính chu vi diện tích của những hình học thờng gặp vμ diện tích bề mặt thể tích của khối hình học nh thế nμo công thức tính chu vi , diện tích hình hoc nh bảng 1-3. Công thức tính diện tích bề mặt ,thể tích khối hình học nh bảng 1-4. 3 Bảng 1-3: tính chu vi vμ diện tích hình học Tên hình Hình Chu vi Diện tích Tam giác A C B L = a+ b+ c S = ah 2 1 Vuông a L = 4a S = a2 Chữ nhật b a L = 2(a+b) S = a.b Bình hμnh A a b H L =2(a+b) S = a.AH Thoi A a B C H L =4.a S = 2 1 a.AH.BC Tròn R L = 2S R S = S R2 Lục giác đều nội tiếp R L = 6R S = 2,59 G R2 4 8. Thế nμo lμ hình chiếu , hình chiếu ba mặt ? Quy tắc chiếu của hình chiếu ba mặt Trong tiêu chuẩn bản vẽ cơ khí nhμ nớc quy định . Hình có đợc khi chiếu chi tiết máy lên mặt chiếu thì gọi lμ hình chiếu . Hình chiếu ba mặt nh hình 1-7. Hình đợc vẽ ra khi nhìn từ phía trớc gọi lμ hình chiếu đứng .Hình đợc vẽ ra khi nhìn từ trên xuống gọi lμ hình chiếu bằng .Hình đợc vẽ ra khi nhìn từ trái qua phải gọi lμ hình chiếu cạnh . nh hình 1-7: Hình 1-7 : sự hình thμnh 3 hìmh chiếu . 9. Hình chiếu mặt cắt lμ gì ? vẽ hình chiế mặt cắt cần lu ý điều gì ? Giả thiết cắt đi mọt phần chi tiết máy rồi vẽ hình chiếu phμn còn lại , gọi lμ hình chiếu mặt cắt .Khi vẽ cần lu ý mấy điểm sau : 1. mặt phẳng cắt nói chung phải lμ mặt phẳng đối xứng vμ phải song song hoặc vuông góc với một mặt chiếu nμo đó . 2. Hình chiếu mặt cắt dùng mặt cắt giả định .Cho nên sau khi lấy một hình chiếu mặt cắt mcòn các chi tiết khác vẫn vẽ theo chi tíet máy hoμn chỉnh . 3. Trong hình chiếu mặt cắt cần đánh dấu vị trí mặt cắt . 4. Bề mặt tiết diện cần vẽ đờng cắt với khgí hiệu vật liệu cho ở bảnh 1-5: hình chiếu chính hình chiếu trái hình chiếu xuống rộ ng 5 Bảng 1-5: Kí hiệu mặt cắt các loại vật liệu Vật liệu kim loại (tr loại có qui định kí hiệu mặt cắt riêng Gỗ dán Chi tiết cuộn dây , cuộn quấn Đất bùn quanh móng Vật liệu phi kim loại nh nhựa, cao su giấy dầu( tr loại có kí hiệu riêng Bê tông Cát lμm khuôn ,cát chèn, bột ,đá mμi ,s ,dao ,dao hợp kim cứng Bê tông cốt thép kính vμ vật liệu trong suốt Lới ( lới sμng, lới lọc) Mặt cắt dọc Gỗ Mặt cắ ngang Chất lỏng 10. Hình chiếu mặt cắt chia lμm mấy loại? Chọn dùng thé nμo 1. Hình chiếu cả mặt cắt: Hình có đợc khi dùng một mặt cắt toμn bộ chi tiết máy gọi lμ hình chiếu cả mặt cắt 2. Hình chiếu nửa mặt cắt : Khi chi tiết máy có mặt phẳng đối xứng có thể lấy đờng tâm đối xứng lμm giớt hạn , mọt nửa vẽ hình chiếu nủa khia vẽ thμnh hình chiếu mặt cắt : hình 1-9(2)a 6 Hình1-9(2)a Hình chiếu nửa mặt cắt 3. Hình chiếu mặt cắt cục bộ: Hình có đợc khi dùng một phần mặt cắt để cắt chi tiết máy thì gọi lμ hình chiếu mặt cắt cục bộ .ranh giới giũa các phần lμ đờng nét gợn sóng: hình 1-9(3). Hìmh 1-9(3) Hình chiếu mặt cắt cục bộ 4. Hình chiếu mặt cắt xiên: Hình chiếu có đợc khi dùng mặt cắt không song song với bất cứ một mặt chiếu cơ bản nμo .đẻ cắt chi tiết .rồi chiếu lên mặt phẳng sonh song với mặt cắt gọi lμ hình chiếu mặt cắ xiên .hình vẽ: A A 5.Hình chiếu mặt cắt bậc : Hình chiếu có đợc khi dùnh nhiều mặt cắt song song với nhau để cắt chi tiết máy gọi lμ hình cắt bậc .hình 1-9(5) 7 Hình 1-9(5): Mặt cắt bậc thang 6 Hình chiếu mặt cắt xoay : hình tạo ra khi dùng hai mặt cắt giao nhau .Rồi đem mặt cắt đó xoay đến vị trí song song với mặt chiếu đã chọn . Gọi lμ mặt cắt xoay .hình 1-9(6) A A A - A Hình 1-9 (6): Hình chiếu tiết diện xoay 7. Hình chiếu mặt cắt phức hợp : Hình có đợc khi dùng một số mặt cắt để cắt chi tiết máy gọi lμ hình chiếu mặt cắt phức hợp. Hình 1-9(7). Khi vẽ tất cả các hình chiếu mặt cắt phải đánh dấu toμn bộ vị trí hớng cắt. A A A - A Hình chiếu phức hợp 8 11. Hình mặt cắt lμ gì ? Hình mặt cắt vμ hình chiếu mặt cắt có gì khác nhau? Hình mặt cắt để cắt chi tiết máy , chỉ vẽnhng hình trên bề mặt bị cắt vμ đánh lí hiệu gọi lμ hình mặt cắt .nh hình vẽ: Hình chiếu mặt cắt ngoμi hình mặt cắt còn vẽ cả hình chiếu các bộ phận khác ở sau mặt cắt, nh hình thể hiện: Hình1-10: Hình mặt cắt 12. Bản vẽ kĩ thuật của chi tiết lμ gì ? bao gồm nội dung nμo ? Bản vẽ dung để trực tiếp chế tạo vμ kiểm nghiệm chi tiết máy trong sản xuất gọi lμ ban vẽ kĩ thuật của chi tiết( gọi tắt lμ bản vẽ chi tiết ), nh hình 9 60 ,5 6 36 ,5 9 1 45° KT NV 679,4 93,39 249,19 A-BR0,02 121,4 17 7, 31 14 9, 31 A B 121,4 12 3, 65 0,02 Phan văn Kiên Phạm văn Giang TRUC Thép C45 TLKL 1845 1:1 Yêu cầu kĩ thuật 2. Bề mặt A gia công tiện 1.Nhiệt luyện bề mặt đến độ cứng HRC 40~50 13. Phơng pháp cơ bản đọc bản vẽ chi tiết ? Mục đích đọc bản vẽ chi tiết lμ lam cho chi tiết gia công phù hợp với yêu cầu bản vẽ . Trớc tiên cần xem rõ tên ,vật liệu chế tạo ,số bản vẽ tỉ lệ vμ kết cấu kichcs thớc Tiến hμh phân tích các hình chiếu ,tìm hiểu thêm hình dáng kết cấu thực tế của linh kiện ,bề mặt gia công Phân tích yêu cầu kích thớc yêu cầu kĩ thuật ,độ chính xác ,độ bóng vμ xác định phơng phápgia công . 14. Cách vẽ ren? 1. Dùng nét đậm để biểu thị đỉnh ren ,nét mảnh biểu thị đáy ren . hình chiếu vuông góc với truc ren vòng tron nét mảng thể hiện đáy ren ,chỉ vẽ 3/4 vòng . 2. Dùng nét đậm để thể hiện đờng bao ranh giới cuối cùng của toμn bộ ren 3. Bất kể lμ ren trong hay ren ngoaid đờng gạch mặt cắt phải tới đờng nét đậm 10 4. Tất cả cách đờng ren không nhìn thấy đều phải vẽ bằng nét đứt . 5. Khi vẽ rn không xuyên thấu ,thờng phảI vẽđộ phân lỗ khoan vμ độ sâu phần ren 6. Cần thể hiện dạng ren thì cắt riêng phần một đoạn ren . 7. Dùng hình chiếu mặt cats để thể hiện sự liên kết ren trong ,ren ngoμi .Phần ăn ren vμo nhau vẽ theo cách vẽ ren ngoμi .Cách bộ phận khác vẫn vẽ theo chách riêng của nó . 15. Cách vẽ then hoa Trong tiêu chuẩn bản vẽ nhμ nớc qui định cách vẽ then hoa vuông có qui định nh sau: 1. khi vẽ then hoa ngoμi, trong hình chiếu mặt chiếu song song với đờng trục then hoa , đờng kính lớn vμ đờng kính nhỏ của nó vẽ bằng nét kiền đậm vμ nét kiền mảnh , đòng thời dùng mặt cắt đẻ vẽ một phần hoặc tòan bộ dạnh răng . hình 1-18. D b 11 Hình 1-18 : then hoa ngoμi. 2. khi vẽ then hoa trong đều phải dùng nét liền đậm để vẽ đờng kính lớn vμ đờng kính nhỏ .Đồng thời dùng hình chiếu cục bộ vẽ một phần hoặc toμn bộ dạng răng. Hình 1-19 d Hình 1-19: cách vẽ then hoa trong 3. Đầu kết thúc chiều dμi lμm việc vμ đμu mút chiều dμi phần đuôi của then hoa ,đều phải dùng nét liền mảnh đẻ vẽ vμ vuông góc với đờng trục ,phần đuôi vẽ thμnh đòng xiên góc xiên của no thờng tạo thμnh góc 30˚ với đờng trục . hình 1-18 4. khi dùng hình chiếu mặt cắt để thể hiện liên kết then hoa thì phần liên kết của nó vẽ theo then hoa ngoμi . Hình 1-20 A A A A Hìmh 1-20: Cách vẽ liên kết then hoa Cách vẽ then hoa thân khai cũng giống nh then hoa vuông.Chỉ dùng đờng nét chấm để vẽ đờng tròn phân độ vμ đờng phân độ. 16. Cách vẽ bánh răng, thanh răng , bánh vít (vô tận) vμ trục vít (vô tận ) Trong tiêu chuẩn nhμ nớc qui định. Khi vẽ bánh răng, thanh răng , bánh vít (vô tận) vμ trục vít (vô tận ) vẽ đờng tròn đỉnh răng bằng nét kiền đậm .đờng tròn chân 12 răng vẽ bằng nét liền mảnh có thể bỏ không vẽ , nhng trong hình chiếu mặt cắt dùng đờng nét liền đậmđể vẽ .Đờng phân độ vẽ bằng đờng chấm gạch .Hình vẽ : Hình 1-21: Cách vẽ ăn khóp ngoμi ; Răng (xiên chữ V thẳng) của bánh răng trụ tròn Cách vẽ trục vít vμ bánh vít 13 Bánh răng thanh răng 17. Cách vẽ lò xo xoắn nh thế nμo Trong tiêu chuẩn nhμ nớc qui định. Hình chiếu lên mặt chiếu song song với đờng trục lò xo xoắn phải vẽ theo qui định ở bảng 1-6: (trong tμi liệu tham khảo) Hình chiếu Hình chiếu mặt cắt hình biểu ý 18. Bản vẽ lắp lμ gì ? Bao gồm các nội dung gì ? Định nghĩa: Bản vẽ thể hiện nguyên lý hoạt động của cụm chi tiế , máy vμ quan hệ lăp ráp giữa các bộ phận gọi lμ bản vẽ lắp Nội dung chủ yéu của bản vẽ lắp: 1. Thể hiện vị trí tơng đối , quan hệ lắp ráp ,hình thức liên kết , nguyên lý hoạt động , hình dáng kết cấu chủ yếu của máy vμ của các linh kiện . 2 Thể hiện kích thớc các chi tiết , kích thớc ngoμi của khối chi tiết hoặc bộ máy 3. Thuyết minh tính năng của bộ máy hoặc cụm chi tiết ,yêu cầu kĩ thuật về lắp ráp ,kiểm nghiệm ,nghiệm thu vμ qui cach sủ dụng . 4 Các ô mục để thể hiện tên , vật liệu, số lợng của chi tiết máy cùng bảng kê chi tiết . 14 19. Phơng pháp đọc bản vẽ láp . 1. Tên của chi tiết máy hoặc bộ máy , đến bảng chi tiết vμ yêu cầu kĩ thuật ,số lợng chi tiết , tính năng vμ qui cách của máy . 2. Phân tích hìng chiếu , xem kết cấu các kinh kiện vá xμc dịnh quan hệ lắp ghép .Phân chia chi tiết khác nhau ,tìm hiểu hình dáng vμ tác dụng các chi tiết ,tìm ra quan hệ lắp ráp giữa các chi tiết 3. Tổng hợp, qui nạp hiểu rõ nguyên lý hoạt động . Tính năng chủ yếu của bộ máy 20. Sai số gia công lμ gì ?Tính lắp lẫn lμ gì? Sai số gia công : Lợng biến động giữa tham số thực tế tham số lý tởng của chi tiết ,linh kiện gọi lμ sai số gia công. Sai số gia công nói chung bao gồm sai số kích thớc ,sai số hình dáng vμ vị trí , Độ bónh bề mặt độ lợn sóng bề mặt . Tính lắp lẫn : trong số những chi tiết có cùng qui cách đợc chế tạo hμng loạt ,lấy bất kì mμ không cần chọn lựa vμ sửa chữa nμo có thể lắp vμo máy (hoặc bộ phận máy ) .Có thể đáp ứng đợc yêu cầu tính năng vốn có của máy thì chi tiết máy ,bộ phận máy đó có tính lắp lẫn . Muốn có đợc hμng loạt chi tiết lắp lẫn phải hạn chế dung sai gia công nhất định . 21. Kích thớc cơ bản , kích thớc thục tế ,vμ kích thớc giới hạn lμ gì ? Kích thớc cơ bản: lμ kích thớc thiết kế qui định Kích thớc cơ bản dùng các đơn vị đô tiêu chuẩn về chiều dμi , đờng kính . Kích thớc thục tế: lμ kích thớc thông qua đo đạc mμ có. Do khi đo tồn tại sai số ,cho nên kích thớc thực tế không hẳn lμ trị số thật .ngoμi ra còn ảnh hởng bởi sai số hình học kích thớc của chi tiết cũng không hoμn toμn bằng nhau . Kích thớc giới hạn: lμ trị số giới hạn cho phép kích thớc chi tiết biến động . Có kích thớc giới hạn lớn nhất vμ kích thớc giới hạn nhỏ nhất . Kích thớc giói hạn lấy kích thớc cơ bản lμm gốc đẻ xác định .Hình 1-26. 611,83 ± 0,5 28 6, 84 ±0 .0 2 36 5, 61 ±0 .0 2 Hình 1-26 22.Sai số kích thớc , sai số trên ,sai số dới, sai số gới hạn vμ sai số thực tế lμ gì ? 15 Qui định kí hiệu của sai số Sai số kích thớc :lμ hiệu đại số của một kích thớc nμo đó trừ đi kích thớc cơ bản tơng ứng của nó . (gọi tắt lμ sai số ) Sai số trên :lμ hiệu đại số lớn nhất vμ kích thớc cơ bản tơng ứng của chi tiết . Sai số dới :lμ hiệu đại số giữa kích trớc nhỏ nhất vμ kích thớc cơ bản .tất cả gọi chung lμ sai số giới hạn Sai số thực tế :Lμ hiệu đại số giữa kích thớc thực tế vμ kích thớc cơ bản tơng ứng . Qui định kí hiệu của sai số: Tiêu chuẩn nhμ nớc qui định : Sai số trên của lỗ lμ ES ; Sai số dới của lỗ lμ EI ; Sai số trên của trục lμ es : Sai số dới của trục lμ ei. Hình vẽ dới . Kí ch th uớ c cơ b ản esei E I E S K íc h th Ư ớc g iớ i h ạn tr ục K íc h th Ư ớc lớ n nh ất lỗ K íc h th Ư ớc g iớ i h ạn n hỏ n hấ t l ỗ nh â 23. Sai số cho phép (dung sai )kích thớc lμ gì ? Nó quan hệ thế nμo với sai số giới hạn ? Lợng biến động cho phép của kích thớc chi tiết máy gọi lμ dung sai kích thớc gọi tắt lμ dung sai .Trị số của dung sai bằng hiệu giữa kích thớc giới hạn lớn nhất vμ kích thớc giới hạn nhỏ nhất hoặc bằng hiệu sai số trên vμ sai số dới .Do kích thớc giới hạn lớn nhất luôn lớn hơn kích thớc giới hạn nhỏ nhất cho nên trị số dung sai luôn dơng . Quan hệ giữa sai số giới hạn vμ dung sai . Đợc thể hiện trong hình 1-27. 24. Hình dải dung sai lμ gì? Đờng không lμ gì ? Thế nμo lμ dung sai kích thớc ? 16 Do trị số tơng đối của dung sai rất nhỏ cho nên để đơqn giản hoá hình biểu diễn dung sai vμ lắp ráp không cần vẽ lỗ vμ trục, chỉ cần vẽ dải dung sai của lỗ vμ trục phóng to .Đó chíng lμ hình mμ ta thờng gọi lμ dung sai vμ lắp ráp gọi tắ lμ hình dải dung sai .Hình 1-28. Trong hình dải dung sai xác định một đờng góc chuẩn gọi lμ đờng “không” .Tức lμ đờng sai số bằng không 25. Dung sai tiêu chuẩn lμ gì ? Dung sai tiêu chuẩn chia lμm mấy cấp ? Để đảm bảo cho chức năng vμ tính lắp lẫncủa linh kiện ,phải có yêu cầu dung sai đối với kích thớc lắp ráp trên linh kiện .Căn c vμo tiêu chuẩn nhμ nớc dung sai tiêu chuẩn chia thμnh 20 cấp ký hiệu của nó đợc biểu thị bằng chữ số ả rập ,lần lợt lμ ITO1 ,ITO, IT1, Đến IT18. Cấp độ chính xác giảm dần theo th tự ; còn dung sai tiêu chuẩn tơng ứng lại lần lợt tăng .Tức C ... ròn nh hình 7-51. Các bớc thao tác nh sau: Trớc tiên ghép chi tiết gia công, khoan lỗ theo đờng kẻ, tiến hμnh vát góc miệng lỗ, sau đó cho đinh tán vμo lỗ, dùng đột ép chặt để ép vật liệu tấm (hình a), tán sơ phần lòi ra của đinh tán (hình b), rồi sơ bộ tán tạo hình (hình c), sau cùng dùng mũi tán để sửa (hình d). (a) ép chặt vật liệu tấm (b) Tán sơ đầu đinh Đờng kính đinh tán d -2,5 3,35 4 5-8 Lắp tinh d+0,1 d+ 0,2 Đờng kính lỗ thông Lắp thô d+ 0,2 d+0,4 d+0,5 d+0,6 Đờng kính đinh tán d 10 12 14-16 18 20 - 27 30 - 36 Lắp tinh d+0,3 d+0,4 d+0,5 Đờng kính lỗ thông Lắp thô d+1 d+1 d+1,5 d+2 273 (c)Tạo hình đầu đinh (d)Sửa lại Hinh7-51 Quá trình tán nối đinh tán đầu nửa tròn Có hai cách tán nối đinh tán đầu chìm. Một cách lμ dùng đinh tán thμnh phẩm để nối; một cách khác lμ, căn cứ vμo độ dμi cần thiết của đinh tán, dùng thép tròn tăng thêm 2 đầu tán tạo thμnh đinh tán. Quá trình tán nối loại sau nh hình 7-52 thể hiện. Bốn bớc đầu giống nh tán nối đinh tán đầu tròn, các bớc tiếp theo lμ: Trớc tiên tán thô mặt 1 vμ 2 ở chính giữa, rồi tán mặt 2, tiếp đó tán mặt 1, sau cùng sửa lại chỗ cao. Nếu dùng đinh tán thμnh phẩm thì chỉ cần tán một đầu, lμm phẳng đầu chìm lμ đợc. Hình 7-52 Quá trình tán nối đinh tán tán đầu chìm Quá trình tán nối đinh tán rỗng nh hình 7-53 thể hiện. Trớc tiên cho đinh tán vμo lỗ, dùng đột nống (hoặc đột tơng tự) để đột ép miệng lỗ đinh nở ra áp sát vμo miệng lỗ chi tiết, rồi dùng đột đặc biệt lμm cho mép miệng lỗ đinh tán lật ra áp phẳng sát vμo lỗ chi tiết. Hình 7-53 Quá trình tán nối đinh tán rỗng. 35. Thế nμo lμ chồn mép? Chồn mép đinh vμ chồn mép tấm nh thế nμo? ở chỗ ghép nối của mối tán tất sẽ có khe hở nhất định, khiến chất khí hoặc chất lỏng trong bình chứa áp lực bị rò. Do đó đối với khe hở xuất hiện trong quá trình tán 274 nối của cẩu kiện ghép nối kiên cố cần áp dụng phơng pháp đánh búa, cán ép để chồn mép. Đó gọi lμ chồn mép tán. Chồn mép chia ra chồn đinh vμ chồn mép tấm. Trớc khi chồn mép, phải dùng đục bạt để bạt hết xơ xờm của mép đinh tán ( tránh lμm xây xớc vật liệu tấm vμ đinh tán). Sau đó, nh hình 7-54 thể hiện, dùng đục chồn đánh theo mép đinh tán, rồi vừa di chuyển đục vừa gỗ vμo cán đục để vật liệu chung quanh đầu đinh chồn ép sát vμo vật liệu tấm, sau cùng dùng đục tù để tiến hμnh thao tác nh trên lμn cho nó dần thu vμo. Sau khi chồn mép đinh, hình dạng đầu đinh tán phải chính xác vμ bảo đảm bề mặt đóng, không xơ xờm. Trớc khi chồn mép tấm, cần gia công cạnh tấm thμnh có độ vát 70- 750, nh hình 7-55. Khi thu mối trớc tiên dùng đục vát mở rãnh ở mép ghép nối, gõ một lợt ven mép, sau đó dùng đục tù chồn chặt mép, tấm ở dới rãnh nh hình 7-56 thể hiện. Trên cùng một kết cấu, chồn mép đinh trớc, chồn mép tấm sau. Nếu chồn mép tấm trớc, do cạnh vật liệu tấm bị ép dẫn đến lμm tăng thêm khe hở, loại khe hở nμy dùng cách chồn mép đinh rất khó khắc phục. Nếu chồn mép đinh trớc, do vật liệu tấm đã đợc tán chặt ở chỗ đinh tán, lực thực hiện khi chồn mép tấm khó có thể lμm bung cạnh tấm, nhờ thế mμ có thể tránh xuất hiện khe hở bên trong. Điều cần lu ý lμ khi bình chứa đang chịu áp lực bởi chất lỏng hoặc chất khí thì không cho phép tiến hμnh công việc chồn mép, nếu không sẽ dẫn đến hậu quả nghiêm trọng xảy ra ở chỗ khác. Hình 7-54 Chồn mép đinh tán Hình 7-55 Độ vát cạnh tấm 275 36. Tháo dỡ mối tán nh thế nμo? Tháo dỡ chi tiết tán nối phải cắt bỏ đinh tán, đột đinh ra khỏi lỗ. Đối với chi tiết tán nối tơng đối lớn có thể trực tiếp dùng đục đục đứt đầu đinh tán, rồi dùng đột để đột đinh tán ra. Khi bề mặt chi tiết tán không cho phép xây xớc, có thể dùng phơng pháp khoan lỗ để tháo. Phơng pháp tháo đinh tán đầu chìm thờng dùng nh hình 7-57 thể hiện. Trớc tiên dùng đục mũi đục lỗ tâm trên đầu đinh tán, sau đó dùng mũi khoan có đờng kính nhỏ hơn đờng kính đinh tán 1mm để khoan lỗ. Độ sâu lỗ hơi sâu hơn chiều cao của đinh tán; rồi dùng đột nhỏ hơn đờng kính lỗ để đột đinh tán ra, Tháo đinh tán đầu tròn nh hình 7-58 thể hiện. Trớc tiên bạt bằng đầu đinh tán; rồi dùng đục mũi đục lỗ tâm, dùng khoan để khoan lỗ độ sâu bằng độ cao đầu tán nối; sau đó dùng que thép thích hợp đút vμo lỗ, bẻ gẫy đầu đinh tán; sa cùng dùng đột để đột đinh tán ra. Hình 7-57 Tháo đinh tán đầu chìm 276 Hình 7-58 Tháo đinh tán đầu tròn. 37. Sử dụng súng tán đinh tán nh thế nμo? Phơng pháp thao tác cơ bản súng tán đinh nh hình 7-59 thể hiện. Sau khi tì chặt cây chống vμo đầu đinh tán, tay giữ chặt súng, sao cho đờng tâm của súng tán, cối tán vμ đinh tán trùng nhau. Khi lõm cối của cối tán tiếp xúc với đầu thân đinh, trớc tiên mở van gió nhỏ, đến khi thân đinh hợi bị tán tù mμ không bị cong, mới mở van gió to. Nếu có hiện tợng thân đinh bị cong hay đầu tán bị lệch, có thể nghiêng súng tán để hiệu chỉnh. Sau cùng, nghiêng súng tán vμ xoay một vòng quanh đầu tán để chung quanh cối tán vμ chi tiết vật liệu tấm ép chặt, tán nối chặt chắc. (a)Miệng cối tiếp xúc với thân đinh tán (b) Tán thô thμnh đầu đinh (c) Tán chặt thanh đầu đinh (d) Xoay cối tán lμm cho chung quanh đinh ép chặt với vật liệu. Hình 7-59 Sơ đồ thể hiện quá trình dùng súng tán đinh để tán nối. áp suất khí nén mμ súng tán sử dụng không nên nhỏ hơn số trị trong bảng 7- 8. Trớc khi nối với ống khí, nên cho ít dầu nhờn lμm trơn, vμ thổi khí (nhằm đề phòng chất bẩn vμ nớc lọt vμo trong súng tán) sau đó mới đấu với ống gió. Khi lắp cối tán, trớc tiên dùng dây thép cột chặt cối với súng tán nhằm tránh rơi cối. Khi sử dụng, không đợc tuỳ tiện chạm vμo công tắc. Công việc tán nối kết thúc phải kịp thời tháo cối tán vμ pít tông trong súng tán ra để bảo quản hợp lý. Bảng 7- 8: Quan hệ giữa áp suất khí nén với đờng kính đinh tán Đờng kính đinh tán (mm) 13 16 19 22 trở lên 277 áp suất khí nén (10 N/cm2) 3 4 5 6 38. Trong tán nối, có thể xuất hiện vấn đề gì? Giải quyết nh thế nμo? Những vấn đề có thể phát sinh khi tán đinh tán đầu chìm có mấy điểm sau: 1> Chọn đờng kính đinh tán không hợp lý, độ dμi thân đinh quá ngăn, nh hình 7-60 thể hiện. 2> Sai về lỗ đinh; có 2 trờng hợp: + Lỗ đinh quá nhỏ, phải dùng sức mới cho đợc đinh vμo lỗ, khiến đầu của nó không thể áp sát vμo chi tiết gia công; do đó đầu tán cũng quá nhỏ, nh hình 7-61 thể hiện. + Lỗ đinh tán của hai chi tiết gia công cha trùng nhau, đinh tán cho vμo sẽ bị cong, từ đó lμm giảm diện tích chịu lực của thân đinh tán; mμ hai đầu đinh cũng không ở trên cùng một đờng thẳng nh hình 7- 62 thể hiện. 3> Vấn đề ở lỗ đầu chìm. Góc của lỗ đầu chìm quá lớn mμ lại quá nông, đầu đinh tán sau khi dũa bằng sẽ trở nên mỏng rất dễ nứt, do đó kết cấu không chắc chắn, nh hình 7-63 thể hiện. Nếu góc của lỗ đầu chìm quá nhỏ, nh hình 7- 64 thể hiện, đầu tán ghép cũng không chắc chắn, do thời gian đánh búa vμo đầu tán ghép quá lâu, vật liệu dễ trở nên cứng, giòn. Nh hình 7- 65 thể hiện, đầu chìm tán về một bên vật liệu tấm mỏng, vật liệu đinh không lắp đầy lỗ chìm, do đó không đạt đợc hiệu quả tán nối tốt. Hình 7- 60 Hình 7- 61 278 4> Lỗ đinh tán cha doa vát miệng lỗ. Cho dù lμ miệng lỗ dới đinh tán đầu nửa tròn cũng phải có góc vát nếu không chỗ tiếp giáp giữa thân đinh tán với đầu đinh không thể áp sát đến vật liệu tấm, tán nối sẽ không chắc chắn, nh hình 7- 66 thể hiện, Hình 7- 66 Hình 7- 67 5> Vấn đề khi ép chặt vật liệu tấm: Đối với lỗ đinh do đột ra phải dùng đột lμm phẳng cạnh mép. Nếu cạnh lỗ bị xơ xờm thì đầu không tán không thể áp chặt vμo bề mặt vật liệu tấm, vμ khi tán nóng sẽ lμm cho một phần vật liệu thân đinh tán chảy ép vμo khe hở giữa vật liệu tấm khiến đầu tán không đủ để lấp đầy lỗ đầu chìm, 279 nh hình 7- 67 thể hiện. Ngoμi ra cho dù khoan lỗ, trớc khi tán cũng cần ép chặt tấm với nhau, nếu không một phần thân đinh cũng sẽ bị chèn ép chảy ra khe hở giữa vật liệu tấm; khiến mối tán không chắc nh hình 7- 68 thê hiện. 6> Vấn đề khi tán thô đầu tán ghép: Hớng đặt lực khi tán thô lên đầu tán cần đúng đờng trục của đinh tán, nếu không đinh tán sẽ bị cong, khiến đầu tán bị lệch; không thể lấp đầy lỗ đầu chìm, nh hình 7- 69 thể hiện. 7> Độ dμi thân đinh không thích hợp: Thân đinh tán quá dμi, nh hình 7- 70 thể hiện, đầu tán sẽ bị cao hơn mép lỗ đầu chìm vμ trùm lên bề mặt chi tiết gia công. Nếu dũa bỏ phần cao đi thì bề mặt chi tiết sẽ xuất hiện vết lõm không thể khắc phục. Nếu thân đinh tán quá ngắn thì không thể lấp đầy lỗ đầu chìm, mối tán sẽ không chắc nh hình 7- 71 thể hiện. Hình 7- 70 Hình 7- 71 Vấn đề có thể xảy ra khi đinh tán đầu nửa tròn có các điểm sau đây: 1> Chọn kích thớc đinh tá không hợp lý. Hình 7- 72 thể hiện, đờng kính đinh tán vμ đờng kính lỗ không phù hợp yêu cầu. Thân đinh tán không thể lấp đầy lỗ tán, sẽ bị cong trong lỗ, phần dôi ra ngoμi của thân đinh quá ngắn, không thể lμm thμnh đầu tròn. Hình 7- 72 Hình 7- 73 2> Cha ép chặt tấm cần tán nối. Sau khi tán thân đinh tán bị ép vμo khe giữa hai tấm nh hình 7- 73 thể hiện. 280 3> Đầu tán không phù hợp yêu cầu. Thân đinh tán quá dμi khi tán thô, hớng đánh búa lại không chính xác, khiến thân đinh bị cong, đầu tán bị lệch, nh hình 7- 74 thể hiện. Hình 7 -74 Hình 7-75 4> Miệng lỗ đinh không phù hợp yêu cầu, nh hình 7- 75 thể hiện, miệng lỗ cha doa góc vát, chỗ góc tròn của thân đinh tán bị kẹp cản ở ngoμi lỗ tán, đầu đinh không tán không thể áp sát vμo vật liệu tấm. Chỗ giữa đầu tán vμ thân đinh không có góc tròn, dễ bị đứt nứt. Nếu vật liệu tấm mỏng bị đục cối ép quá mức sẽ xảy ra tình hình dát mỏng, lμm cho chung quanh đinh phồng lên nh hình 7 -76 thể hiện. Nếu thân đinh quá ngắn, đầu tán bẹt, không thể dùng khuôn cối tán để tán thμnh đầu tròn, nh hình 7- 77 thể hiện, cờng độ mối tán nh vậy sẽ không đủ. Hình 7-76 Hình7-77 5> Vấn đề nảy sinh khi sử dụng cối tán, nh hình 7- 78 thể hiện, cối tán đặt nghiêng trên đầu đinh tán, một bản cối tán đè thμnh vết trên vật liệu tấm, vật liệu tấm mỏng bị dát mỏng phồng lên. Nếu thân đinh tán quá dμi sẽ khiến vật liệu tấm d thừa đùn thμnh bánh quanh cối tán, nh hình 7- 79 thể hiện. Nếu chọn cối tán quá nhỏ, vật liệu d thừa sẽ bị đùn lại ở chung quanh đầu tán, cũng sẽ lμm cho cờng độ của đầu tán không đủ, nh hình 7- 80 thể hiện. Ngoμi ra, đầu tán ghép quá hẹp, 281 chung quanh sẽ bị cối tán dập đứt, còn ở giữa lại không đủ vật liệu, cũng sẽ khiến cờng độ mối tán không đủ, nh hình 7- 81 thể hiện. Tình trạng giảm cờng độ mối tán do độ dμi đinh không đủ vμ cối tán chọn lựa quá lớn nh hình 7- 82 vμ hình 7- 83 thể hiện. Hình 7- 80 Hình 7- 81 282 39. Thế nμo lμ "hμn thiếc"? dụng cụ chủ yếu để "hμn thiếc" có những gì? Hình 7- 84 Phơng pháp dùng vật liệu hμn bằng kim loại dễ nóng chảy (nhiệt độ nóng chảy dới 3250C) để nối liền chi tiết kim loại thì gọi lμ "hμn thiếc". Khi hμn thiếc, chi tiết hμn không nóng chảy. Căn cứ vμo yêu cầu khác nhau của hμn thiếc mμ áp dụng phơng pháp thao tác khác nhau vμ chọn công cụ phù hợp; nh mỏ hμn thiếc, nồi nóng chảy thiếc hμn, thiết bị cảm ứng của hμn cảm ứng, đèn khò trong hμn lửa Ngoμi ra, còn phải chuẩn bị các dụng cụ hỗ trợ liên quan nh đũa, kìm hμn, giá đỡ mỏ hμn vμ bình đựng dung dịch hμn. Dựa vμo hình thức gia nhiệt, mỏ hμn chia ra: mỏ hμn nung, mỏ hμn điện, súng hμn hơi nh hình 7- 84 thể hiện. 40. Khi gia nhiệt mỏ hμn, cần chú ý điều gì? Khi gia nhiệt mỏ hμn, nhiệt độ gia nhiệt không đợc quá 5000C (đầu mỏ hμn bắt đầu có mμu đỏ sẫm). Khi gia nhiệt mỏ hμn bằng lửa, phải đốt đầu to của mỏ hμn mμ không đợc đốt đầu đỏ (đầu dùng để hμn, gọi lμ mặt tiếp xúc). Nếu bị ôxy hoá, 283 đầu nhỏ của mỏ hμn không chấm đợc vật liệu hμn, cho nên trớc khi chấm hμn phải dùng đá Amoniclorat để mμi bỏ oxít đồng. 41. Tác dụng của thuốc hμn lμ gì? Thuốc hμn thờng dùng trong hμn thiếc thờng có những loại nμo? Tác dụng chủ yếu của thuốc hμn lμ khử bỏ chất oxy hoá ở chỗ khe hμn. Vì lớp ôxy hoá bám ở bề mặt kim loại sẽ ngăn cách sự tiếp xúc giữa vật liệu hμn với kim loại chi tiết, không thể hμn nối đợc. Thuốc hμn thông qua phản ứng hoá học để lμm sạch lớp oxy hoá trên bề mặt kim loại. Thuốc hμn thờng dùng trong hμn thiếc có dung dịch chorua kẽm dùng trong hμn nối mạ thiếc, đồng vμ hợp kim đồng; Axit Clohydric dùng trong hμn nối kẽm vμ chi tiết mạ kẽm, đầu hμn dùng trong hμn nối các kim loại, nhựa thông dùng trong hμn nối chì vμ các loại linh kiện điện tử. 42. Pha chế thuốc hμn clorua kẽm nh thế nμo? Thuốc hμn clorua kẽm có thể pha chế bằng axit clohydric loãng với kẽm. Khi cho kẽm vμo trong axit clohydric sẽ sinh ra nhiều khí hidro, nhiều bọt khí bốc ra từ Axit Clohydric, cứ tiếp tục cho thêm kẽm, cho đến lúc cơ bản không còn sủi bọt nữa lμ có thể dùng. Khi pha chế cần chú ý an toμn, không đợc để dung dịch axit trμn ra ngoμi. 43. Độ lớn khe hở có ảnh hởng gì đến mối hμn? Hμn lμ sau khi gia nhiệt lμm cho vật liệu hμn nóng chảy thμnh dung dịch, chảy vμo hμn, sau khi đông kết lại sẽ gắn chặt với vật liệu gốc. Nếu mối hμn quá lớn thì vật liệu hμn khó lấp đầy mối hμn. Nói chung, khe mối hμn nên vμo khoảng 0,05 - 0,2 mm. Để bảo đảm khe hở mối hμn, khi hμn cần dùng kìm hμn kẹp chặt chi tiết rồi mới hμn. 44. Mối hμn có những hình thức chủ yếu nμo? Dựa vμo yêu cầu nối liền, hình thức mối hμn có thể quy thμnh: mối hμn đối, mối hμn chữ T, mối hμn xiên vμ mối hμn chồng nh hình 7- 85 thể hiện. Mối hμn đối chủ yếu dùng để hμn nối chồng vật liệu tấm có độ dμy khoảng 1mm; mối hμn chữ T dùng nối đối chính diện từ hai chi tiết trở lên vuông góc với nhau; mối hμn xiên dùng để nối đối lẫn nhau giữa các chi tiết có dạng xiên; hμn chồng dùng để hμn nối hai hoặc trên hai chi tiết song song hoặc chồng lên nhau; mối hμn cắm dùng để hμn linh kiện điện tử với tấm mạch in. 284 Hình 7- 85 Hình thức mối hμn 45. Hμn tấm mạch in nh thế nμo? Tấm mạch in lμ tấm mạch điện đợc chế tạo bằng cách in chụp rời, ăn mòn lớp đồng mỏng dán chặt trên tấm nền cách điện. Hμn tấm mạch in phải dùng mỏ hμn công suất nhỏ, nh hình 7- 86. Mỏ hμn điện nóng trong tiêu hao điện ít, nhỏ, nhẹ, gia nhiệt nhanh; loại nóng ngoμi, nhiệt độ đều, giữ nhiệt tốt, bền. Mặt tiếp xúc của đầu mỏ hμn điện có thể căn cứ vμo điểm hμn lớn hay nhỏ mμ dũa thμnh hình dáng thích hợp, vμ bôi một lớp thiếc lên mặt tiếp xúc. Thuốc hμn, vật liệu hμn cũng không thể sử dụng thiếc hμn vμ nớc cờng toan bình thờng mμ phải dùng dây thiếc hμn bọc colophan vμ colophan. Để tiện sử dụng, có thể hoμ colophan vμo cồn 95% lμm thμnh dung dịch cồn colophan. Nếu lớp đồng của tấm mạch in không mạ vμng, mạ bạc hoặc mạ thiếc chì thì trớc khi hμn cần dùng giấy nhám mịn đánh bóng bề mặt vμ bôi một lớp nớc colophan. Dây dẫn linh kiện cũng phải dùng giấy nhám mịn hoặc dao con cạo sạch lớp oxy hoá ở bề mặt vμ bôi một ít thuốc hμn, chấm thiếc sẵn để dùng khi hμn. Trớc tiên, chấm mỏ hμn đã gia nhiệt vμo một ít thiếc, sau đó mới cho mỏ hμn tiếp xúc với điểm hμn trên tấm đồng vμ dây dẫn, sau 2- 3 giây thì nhấc Hình 7- 86 Mỏ hμn điện. 285 mỏ hμn ra. Điểm hμn phải bóng, chắc. Nếu thời gian dμi quá dễ lμm hỏng linh kiện hoặc lμm bong lớp đồng khô tấm nền do bị nóng.
File đính kèm:
giao_trinh_ky_thuat_nguoi.pdf