Giáo trình Công nghệ đúc
1.1.1. Thực chất
Đúc là phương pháp chế tạo sản phẩm bằng cách rót kim loại lỏng vào khuôn có
hình dạng nhất định, sau khi kim loại hoá rắn trong khuôn ta thu được vật đúc có hình
dáng giống như khuôn đúc.
Nếu vật phẩm đúc đưa ra dùng ngay gọi là chi tiết đúc, còn nếu vật phẩm đúc phải
qua gia công áp lực hay cắt gọt để nâng cao cơ tính, độ chính xác kích thước và độ bóng
bề mặt gọi là phôi đúc.
Đúc có những phương pháp sau: đúc trong khuôn cát, đúc trong khuôn kim loại,
đúc dưới áp lực, đúc li tâm, đúc trong khuôn mẫu chảy, đúc trong khuôn vỏ mỏng, đúc
liên tục v.v. nhưng phổ biến nhất là đúc trong khuôn cát.
1.1.2. Đặc điểm
- Đúc có thể gia công nhiều loại vật liệu khác nhau: Thép, gang, hợp kim màu v.v.
có khối lượng từ một vài gam đến hàng trăm tấn.
- Chế tạo được vật đúc có hình dạng, kết cấu phức tạp như thân máy công cụ, vỏ
động cơ v.v.mà các phương pháp khó khăn hoặc không chế tạo được.
- Độ chính xác về hình dáng, kích thước và độ bóng không cao (có thể đạt cao nếu
đúc đặc biệt như đúc áp lực).
- Có thể đúc được nhiều lớp kim loại khác nhau trong một vật đúc.
- Giá thành chế tạo vật đúc rẻ vì vốn đầu tư ít, tính chất sản xuất linh hoạt, năng
suất tương đối cao.
- Có khả năng cơ khí hoá và tự động hoá.
- Tốn kim loại cho hệ thống rót, đậu ngót, đậu hơi.
- Dễ gây ra những khuyết tật như: thiếu hụt, rỗ khí, cháy cát v.v.
- Kiểm tra khuyết tật bên trong vật đúc khó khăn, đòi hỏi thiết bị hiện đại.
Tóm tắt nội dung tài liệu: Giáo trình Công nghệ đúc
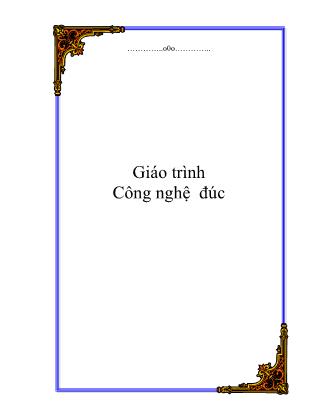
..o0o.. Giỏo trỡnh Cụng nghệ đỳc Giáo trình: công nghệ đúc Tr−ờng đại học bách khoa - 2006 1 ch−ơng 1 khái niệm chung 1.1. Thực chất, đặc điểm và công dụng 1.1.1. Thực chất Đúc là ph−ơng pháp chế tạo sản phẩm bằng cách rót kim loại lỏng vào khuôn có hình dạng nhất định, sau khi kim loại hoá rắn trong khuôn ta thu đ−ợc vật đúc có hình dáng giống nh− khuôn đúc. Nếu vật phẩm đúc đ−a ra dùng ngay gọi là chi tiết đúc, còn nếu vật phẩm đúc phải qua gia công áp lực hay cắt gọt để nâng cao cơ tính, độ chính xác kích th−ớc và độ bóng bề mặt gọi là phôi đúc. Đúc có những ph−ơng pháp sau: đúc trong khuôn cát, đúc trong khuôn kim loại, đúc d−ới áp lực, đúc li tâm, đúc trong khuôn mẫu chảy, đúc trong khuôn vỏ mỏng, đúc liên tục v.v... nh−ng phổ biến nhất là đúc trong khuôn cát. 1.1.2. Đặc điểm - Đúc có thể gia công nhiều loại vật liệu khác nhau: Thép, gang, hợp kim màu v.v... có khối l−ợng từ một vài gam đến hàng trăm tấn. - Chế tạo đ−ợc vật đúc có hình dạng, kết cấu phức tạp nh− thân máy công cụ, vỏ động cơ v.v...mà các ph−ơng pháp khó khăn hoặc không chế tạo đ−ợc. - Độ chính xác về hình dáng, kích th−ớc và độ bóng không cao (có thể đạt cao nếu đúc đặc biệt nh− đúc áp lực). - Có thể đúc đ−ợc nhiều lớp kim loại khác nhau trong một vật đúc. - Giá thành chế tạo vật đúc rẻ vì vốn đầu t− ít, tính chất sản xuất linh hoạt, năng suất t−ơng đối cao. - Có khả năng cơ khí hoá và tự động hoá. - Tốn kim loại cho hệ thống rót, đậu ngót, đậu hơi. - Dễ gây ra những khuyết tật nh−: thiếu hụt, rỗ khí, cháy cát v.v... - Kiểm tra khuyết tật bên trong vật đúc khó khăn, đòi hỏi thiết bị hiện đại. 1.1.3.Công dụng Sản xuất đúc đ−ợc phát triển rất mạnh và đ−ợc sử dụng rất rộng rãi trong các ngành công nghiệp. khối l−ợng vật đúc trung bình chiếm khoảng 40ữ80% tổng khối l−ợng của máy móc. Trong ngành cơ khí khối l−ợng vật đúc chiếm đến 90% mà giá thành chỉ chiếm 20ữ25%. Simpo PDF Merge and Split Unregistered Version - Giáo trình: công nghệ đúc 3.1.4. Phân loại Kỹ thuật đúc đ−ợc phân loại theo sơ đồ sau: Kỹ thuật đúc Tr−ờng đại học bách khoa - 2006 2 Đúc trong khuôn cát Đúc đặc biệt Đúc trong hòm khuôn Đúc trên nền x−ởng Đúc bằng d−ỡng gạt khuôn kim loại Đúc áp lực Đúc ly tâm Đúc liên tục Đúc trong khuôn vỏ mỏng Đúc trong khuôn mẫu chảy H.1.1. Sơ đồ phân loại ph−ơng pháp đúc Ch−ơng 2 Đúc trong khuôn cát 2.1. Khái niệm về quá trình sản xuất đúc Quá trình sản xuất đúc bao gồm các công đoạn chính sau: Bộ phận kỹ thuật Bộ phận mộc mẫu Chế tạo hỗn hợp làm khuôn Chế tạo hỗn hợp làm lõi Làm khuôn Sấy khuôn Làm lõi Sấy lõi Nấu kim loại Lắp ráp khuôn và rót kim loại Phá khuôn lấy vật đúc Phá lõi khỏi vật đúc Làm sạch vật đúc H.2.1. Sơ đồ các bộ phận trong x−ởng đúc Kiểm tra chất l−ợng Simpo PDF Merge and Split Unregistered Version - Giáo trình: công nghệ đúc Phòng kỹ thuật có nhiệm vụ lập phiếu công nghệ và thiết kế các bản vẽ kỹ thuật: bản vẽ chi tiết, bản vẽ vật đúc, bản vẽ mẫu và bản vẽ hộp lõi rồi đ−a sang cho bộ phận mộc mẫu để chế tạo mẫu và hộp lõi và chuyển cho các bộ phận chế tạo khuôn và lõi. Sau khi sấy (hoặc không sấy) khuôn và lõi, tiến hành lắp ráp khuôn và rót kim loại. 2.2. các bộ phận cơ bản của một khuôn đúc Muốn đúc một chi tiết, tr−ớc hết phải vẽ bản vẽ vật đúc dựa trên bản vẽ chi tiết có tính đến độ ngót của vật liệu và l−ợng d− gia công cơ khí. Căn cứ theo bản vẽ vật đúc, bộ phận x−ởng mộc mẫu chế tạo ra mẫu và hộp lõi. Mẫu tạo ra lòng khuôn 6 - có hình dạng bên ngoài của vật đúc. Lõi 7 đ−ợc chế tạo từ hộp lõi có hình dáng giống hình dạng bên trong của vật đúc. Lắp lõi vào khuôn và lắp ráp khuôn ta đ−ợc một khuôn đúc. Để dẫn kim loại lỏng vào khuôn ta phải tạo hệ thống rót 10. Rót kim loại lỏng qua hệ thống rót này. Sau khi kim loại hoá rắn, nguội đem phá khuôn ta đ−ợc vật đúc. Lòng khuôn 6 phù hợp với hình dáng vật đúc, kim loại lỏng đ−ợc rót vào khuôn qua hệ thống rót. Bộ phận 11 để dẫn hơi từ lòng khuôn ra ngoài gọi là đậu hơi đồng thời còn làm nhiệm vụ bổ sung kim loại cho vật đúc khi hoá rắn còn gọi là đậu ngót. Hòm khuôn trên 1, hòm khuôn d−ới 9 để làm nửa khuôn trên và d−ới. Để lắp 2 nửa khuôn chính xác ta dùng chốt định vị 2. Vật liệu trong khuôn 4 gọi là hỗn hợp làm khuôn (cát khuôn). Để nâng cao độ bền của hỗn hợp làm khuôn trong khuôn ta dùng những x−ơng 5. Để tăng tính thoát khí cho khuôn ta tiến hành xiên các lỗ thoát khí 8. 1- Hòm khuôn trên 2- Chốt định vị 3- Mặt phân khuôn 4- Cát khuôn 5- X−ơng khuôn 6- Lòng khuôn 7- Lõi 8- Rãnh thoát khí 9- Hòm khuôn d−ới 10- Hệ thống rót 11- Đậu hơi (hoặc đậu ngót) 11 10 6 7 8 9 H.2.2. Các bộ phận chính của một khuôn đúc cát 5 4 3 2 1 Tr−ờng đại học bách khoa - 2006 3 Simpo PDF Merge and Split Unregistered Version - Giáo trình: công nghệ đúc 2.3. Hỗn hợp làm khuôn và làm lõi Hỗn hợp làm khuôn và làm lõi gồm: cát, đất sét, chất kết dính, chất phụ, n−ớc v.v... Có 2 loại: loại cũ (đã dùng) và loại mới chế tạo 2.3.1. Yêu cầu đối với hỗn hợp làm khuôn và làm lõi Hỗn hợp cần có những tính chất sau: a/ Tính dẻo Tính dẻo là khả năng biến dạng vĩnh cữu của hỗn hợp sau khi bỏ tác dụng của ngoại lực. Tính dẻo tăng khi n−ớc trong hỗn hợp tăng đến 8%, đất sét và chất dính tăng, hạt cát nhỏ. b/ Độ bền Độ bền của hỗn hợp là khả năng chịu tác dụng của ngoại lực mà không bị phá huỷ. Độ bền tăng khi hạt cát nhỏ, không đồng đều và sắc cạnh, độ mịn chặt của hỗn hợp tăng, l−ợng đất sét tăng, l−ợng n−ớc tăng đến 8 %. - Khuôn t−ơi có sức bền nén ≤ (6ữ8) N/ cm2. - Khuôn khô có sức bền nén ≤ (8ữ30) N/ cm2. - Khi nhiệt độ tăng đến 9000C thì sức bền nén tăng 2ữ3 lần Để đánh giá độ bền ta dùng giới hạn bền nén, đ−ợc tính theo công thức sau: δ = P E (N/ cm2) với : P - lực nén; F- diện tích tiết diện ngang mẫu thử c/ Tính lún Tính lún là khả năng giảm thể tích của hỗn hợp khi chịu tác dụng của ngoại lực, cần có tính lún để ít cản trở vật đúc co khi đông đặc và làm nguội, tránh đ−ợc nứt nẻ, công vênh. Tính lún tăng khi dùng cát sông hạt to, l−ợng đất sét ít, chất kết dính ít, chất phụ (mùn c−a, rơm vụn, bột than) tăng. d/ Tính thông khí Tính thông khí của hỗn hợp là khả năng cho phép khí lọt qua những kẻ hở nhỏ giữa những hạt cát của hỗn hợp. Tính thông khí cần có để vật đúc không bị rỗ khí.Tính thông khí tăng khi hạt cát to và đều, l−ợng đất sét và chất kết dính ít, độ dầm chặt của hỗn hợp giảm, chất phụ nhiều và l−ợng n−ớc < 4 %. Để đánh giá khả năng thoát khí của hỗn hợp làm khuôn, ng−ời ta dùng độ thông khí K: K = Q L F P t . . . .100 với: Q : l−ợng thông khí thổi qua mẫu (cm3). L : chiều cao của mẫu (cm). Tr−ờng đại học bách khoa - 2006 4 F : diện tích tiết diện ngang của mẩu ( cm2 ) Simpo PDF Merge and Split Unregistered Version - Giáo trình: công nghệ đúc P : áp suất của khí tr−ớc khi qua mẫu ( N/ cm2 ) t : thời gian không khí thoát qua mẫu ( phút ) Trong thực nghiệm, ng−ời ta lấy: Q = 2000 cm3; L = 50 mm; D = 50 mm, do đó khi thí nghiệm chỉ cần xác định thời gian không khí thoát qua mẫu. g/ Tính bền nhiệt Tính bền nhiệt của hỗn hợp là khả năng không bị cháy, chảy và mềm ra ở nhiệt độ cao. Tính bền nhiệt tăng khi l−ợng cát thạch anh Si02 tăng, hạt cát to và tròn, các tạp chất dễ chảy (Na2O, K2O, CaO, Fe2O3) trong hỗn hợp càng ít. Tổng số những chất dễ chảy này phải ≤ 1,5ữ20% đối với thép và phải ≤ 5ữ7% đối với gang, để đúc kim loại màu không quá 10ữ12%. Hỗn hợp làm khuôn cho tất cả các loại vật đúc không đ−ợc chứa (Na2O + K2O) quá 1%, CaO ≤ 1ữ2% và Fe2O3 ≤ 3ữ4%. e/ Độ ẩm Là l−ợng n−ớc chứa trong hỗn hợp đó, đ−ợc xác định bằng công thức sau: X = g g g − 1 100% . với: g- khối l−ợng hỗn hợp t−ơi; g1- khối l−ợng hỗn hợp khô. Độ ẩm tăng khi l−ợng n−ớc trong hỗn hợp tăng, nh−ng độ ẩm phải ≤ 6- 8% vì nếu nhiều hơn sẽ làm cho sức bền, tính thoát khí giảm. Độ ẩm đối với khuôn t−ơi đúc: gang : 4,5ữ5,5%; thép: 4,5%; nhôm: 4ữ5%. f/ Tính bền lâu Là khả năng làm việc đ−ợc lâu và nhiều lần của hỗn hợp, đ−ợc xác định: C = R r 100% . với : R- sức bền sẵn có của hỗn hợp, r- sức bền sau một thời gian sử dụng. 2.3.2. các loại vật liệu làm khuôn và làm lõi Chủ yếu là cát, đất sét, chất dính kết, chất phụ v.v... a/ Cát Thành phần chủ yếu của cát là SiO2, ngoài ra còn có Al2O3, CaCO3, Fe2O3... Phân loại cát - Theo nơi lấy cát: gồm cát núi hạt sắc cạnh, cát sông hạt tròn đều. - Theo độ hạt: Ng−ời ta xác định độ hạt của cát theo kích th−ớc lỗ rây. Số hiệu rây gọi theo kích th−ớc lỗ của nó (hạt) đ−ợc phân nhóm: Tên cát Nhóm Số hiệu rây Kích th−ớc hạt (mm ) Tr−ờng đại học bách khoa - 2006 5 Simpo PDF Merge and Split Unregistered Version - Giáo trình: công nghệ đúc Tr−ờng đại học bách khoa - 2006 6 cát thô rất to to vừa nhỏ rất nhỏ mịn bột 063 04 0315 02 016 01 0063 005 1 - 063 - 04 063 - 04 - 0315 04 - 0315 - 02 0315 - 02 - 016 02 - 016 - 01 016 - 01 - 0063 01 - 0063 - 005 0063 - 005 - nhỏ 0,4 ữ 1 0,315 ữ 0,63 0,2 ữ 0,4 0,16 ữ 0,315 0,1 ữ 0,2 0,063 ữ 0,16 0,05 ữ 0,1 < 0,05 - Theo thành phần thạch anh ( SiO2): Loại cát 1K 2K 3K 4K L−ợng chứa SiO2 (%) 97 96 94 90 - Theo thành phần đất sét: Tên cát Ký hiệu Liên xô Số l−ợng đất sét chứa trong cát (%) Cát thạch anh K < 2 Cát gầy T 2ữ10 Cát nữa béo ΠЖ 10ữ20 Cát béo Ж 20ữ30 Cát rất béo OЖ 30ữ50 Ký hiệu cát và chọn cát Ký hiệu cát: theo thành phần thạch anh và độ hạt. ví dụ: 2K 063A; 2K 016B; với: 2K : là loại cát thạch anh số 2; 063, 016: là độ hạt. A,B : là cát ở rây trung bình của bộ 3 rây > 50% Chọn cát: - Tuỳ thuộc khối l−ợng vật đúc, kim loại vật đúc mà ta chọn loại cát, thành phần và độ hạt nhất định. - Để làm khuôn t−ơi đúc gang xám, m vật đúc < 200kg, ta dùng cát gầy (T) độ hạt 01; 016; 02; 04. - Vật đúc có khối l−ợng m = 200ữ2000 kg, gang trắng thì dùng cát nữa mỡ tăng thạch anh (để chịu nhiệt), độ hạt P 16 - 04. Vd : T04A; K02A. - Để làm khuôn lõi đúc thép m< 500kg, dùng cát thạch anh (K) độ hạt P 16- 02. Ví dụ: K02A; K016B; K016A. - Để đúc kim loại màu ta dùng cát nữa mỡ, độ hạt 01; 016; 02, thạch anh ít. vd : 016A; 01A. b/ Đất sét Simpo PDF Merge and Split Unregistered Version - Giáo trình: công nghệ đúc Thành phần chủ yếu: cao lanh mAl2O3, nSiO2, qH2O, ngoài ra còn có tạp chất: CaCO3, Fe2O3, Na2CO3. Đặc điểm: Dẻo, dính khi có l−ợng n−ớc thích hợp, khi sấy thì độ bền tăng nh−ng dòn, dễ vỡ, không bị cháy khi rót kim loại vào. Phân loại đất sét: - Theo thành phần khoáng chất : Đất sét th−ờng hay cao lanh có sẵn trong tự nhiên. Thành phần chủ yếu là Al2O3.2SiO2.2H2O, loại này để làm khuôn đúc th−ờng, có màu trắng, khả năng hút n−ớc kém, tính dẻo và dính kém, bị co ít khi sấy. Nhiệt độ nóng chảy cao (1750ữ17850C). Đất sét bentônit (I ) thành phần chủ yếu là: Al2O3.4SiO2.H2O. Nó là đất sét trắng có tính dẻo dính lớn, khả năng hút n−ớc và tr−ơng nở lớn, bị co nhiều khi sấy, hạt rất mịn, nhiệt độ chảy thấp (1250ữ13000C). Do núi lửa sinh ra lâu ngày biến thành. Loại này để làm khuôn quan trọng cần độ dẻo, bền cao. - Phân loại đất sét theo khả năng dính kết + Loại dính kết ít (M): có độ bền nén t−ơi 0,5ữ 0,8 kg/cm2; độ bền nén khô < 3,5 kg/cm2. Loại này th−ờng dùng làm khuôn đúc kim loại màu, nhỏ, vừa. + Loại dính kết vừa (C): có độ bền nén t−ơi 0,79ữ1,1 kg/cm2; độ bền nén khô < 3,5ữ5,5 kg/cm2. + Loại dính kết bền (B): có độ bền nén t−ơi >1,1 kg/cm2; độ bền nén khô trên 5,5 kg/cm2. - Phân loại theo khả năng bền nhiệt + Nhóm 1: bền nhiệt cao, chịu đ−ợc t0 ≥ 15800C. + Nhóm 2: bền nhiệt vừa, chịu đ−ợc t0: 1350ữ15800C. + Nhóm 3: bền nhiệt thấp, chịu đ−ợc t0 ≤ 13500C. Chọn đất sét: - Để đúc thép: th−ờng dùng cao lanh (φ), loại rất bền (B) và có khả năng chịu nhiệt cao. - Để đúc gang: dùng cao lanh loại dính kết, chịu nhiệt vừa, bền và rất bền cho cả khuôn t−ơi và khô. - Để đúc hợp kim màu: th−ờng dùng cao lanh dính kết vừa và cao, bền nhiệt thấp. c/ Chất kết dính: Chất dính kết là những chất đ−a vào hỗn hợp làm khuôn, lõi để tăng tính dẻo của hỗn hợp. Yêu cầu: - Khi trộn vào hỗn hợp, chất dính kết phải phân bố đều. Tr−ờng đại học bách khoa - 2006 7 Simpo PDF Merge and Split Unregistered Version - Giáo trình: công nghệ đúc Tr−ờng đại học bách khoa - 2006 8 - Không làm dính hỗn hợp vào mẫu và hợp lõi và dễ phá khuôn lõi. - Khô nhanh khi sấy và không sinh nhiều khí khi rót kim loại . - Tăng độ dẻo, độ bền và tính bền nhiệt cho khuôn và lõi. - Phải rẻ, dễ kiếm, không ảnh h−ởng đến sức khoẻ công nhân. Những chất dính kết th−ờng dùng: - Dầu: dầu lanh, dầu bông, dầu trẩu... đem trộn với cát và sấy ở t0=200ữ2500C , dầu sẽ bị oxy hoá và tạo thành màng oxyt hữu cơ bao quanh các hạt cát làm chúng dính kết chắc với nhau. - N−ớc đ−ờng (mật): dùng để làm khuôn, lõi khi đúc thép. Loại này khị sấy bề mặt, khuôn sẽ bền nh−ng bên trong rất dẻo nên vẫn đảm bảo độ thoát khí và tính lún tốt. Khi rót kim loại nó bị cháy, do đó tăng tính xốp, tính lún, thoát khí và dễ phá khuôn nh−ng hút ẩm nên sấy xong phải dùng ngay. - Bộ hồ: (nồng độ 2,5ữ3%) hút n−ớc nhiều, tính chất nh− n−ớc đ−ờng, dùng làm khuôn t−ơi rất tốt. - Các chất dính kết hoá cứng: Nhựa thông, ximăng, hắc ín, nhựa đ−ờng. Khi sấy chúng chảy lỏng ra và bao quanh các hạt cát. Khi khô chúng tự hoá cứng làm tăng độ bền, tính dính kết cho khuôn. Th−ờng th−ờng dùng loại ximăng pha vào hỗn hợp khoảng 12%, độ ẩm của hỗn hợp 6ữ8%, để trong không khí 24ữ27 giờ có khả năng tự khô, loại này rất bền. - N−ớc thuỷ tinh: chính là các loại dung dịch silicat Na2O.nSiO2.mH2O hoặc K2O.nSiO2.mH2O sấy ở 200ữ2500C, nó tự phân huỷ thành nSiO2.(m-p)H2O là loại keo rất dính. Khi thổi CO2 vào khuôn đã làm xong, n−ớc thuỷ tinh tự phân huỷ thành chất keo trên, hỗn hợp sẽ cứng lại sau 15ữ30 phút. d-Các chất phụ Chất phụ là các chất đ−a vào hỗn hợp để khuôn và lõi có một số tính chất đặc biệt nh− nâng cao tính lún, tính thông khí, làm nhẵn mặt khuôn, lõi và tăng khả năng chịu nhiệt cho bề mặt khuôn lõi, gồm 2 loại: - Chất phụ gia: trong hỗn hợp th−ờng cho thêm mùn c−a, rơm vụn, phân trâu bò khô, bột than... Khi rót kim loại lỏng vào khuôn, những chất này cháy để lại trong khuôn những lỗ rỗng làm tăng tính xốp, thông khí, tính lún cho khuôn lõi. Tỉ lệ khoảng 3% cho vật đúc thành mỏng và 8% cho vật đúc thành dày. - Chất sơn khuôn: Để mặt khuôn nhẵn bóng và chịu nóng tốt, ng−ời ta th−ờng quét lên bề mặt lòng khuôn, lõi một lớp sơn, có thể là bột than, bột gratit, bột thạch anh hoặc dung dịch của chúng với đất sét. Bột than và gratit quét vào thành khuôn, khi rót kim loại vào nó sẽ cháy tạo thành CO, CO2 làm thành môi tr−ờng hoàn nguyên rất tốt, đồng thời tạo ra một lớp khí ngăn cách giữa kim loại lỏng với mặt lòng khuôn làm cho mặt lòng khuôn không bị cháy cát và tạo cho việc phá khuôn dễ dàng. Simpo PDF Merge and Split Unregistered Version - Giáo trình: công nghệ đúc Tr−ờng đại học bách khoa - 2006 9 2.3.3. hỗn hợp làm khuôn, lõi a/ Hỗn hợp làm khuôn : có hai loại Cát áo: Dùng để phủ sát mẫu khi chế tạo khuôn nén cần có độ bền, dẻo cao, đồng thời nó trực tiếp ti ... đúc ly tâm mà khuôn quay theo trục thẳng đứng. Do khuôn quay theo trục thẳng đứng nên mỗi phần tử kim loại lỏng chịu một lực ly tâm và trọng lực, vì vậy bề mặt tự do của kim loại lỏng sẽ là một đ−ờng parabôlôit. Điều này có thể dễ dàng chứng minh đ−ợc nếu ta lấy điểm A có tọa độ X, Y trên hệ tọa độ Oxy nh− hình bên. Phần tử A chịu một lực ly tâm là: P = m.x.ω2 và chịu tác dụng của trọng lực là: Q = m.g. Hợp lực của P, Q là R tạo với Q một góc là α: Ta có: x gg.m .x.m Q P tg 22 ω=ω==α y ω Simpo PDF Merge and Split Unregistered Version - Giáo trình: công nghệ đúc Tr−ờng đại học bách khoa - 2006 50 Theo tính chất của đ−ờng tiếp tuyến thì: x gdx dy tg 2ω==α ; do đó: 2 22 x g2 ydx.x g dy ω=⇒ω= Ph−ơng trình này là một đ−ờng parabol. Vậy nếu hình đó quay quanh trục Oy thì nó sẽ tạo thành một mặt parabôlôit. Từ ph−ơng trình này, ta có thể tính đ−ợc số vòng quay của khuôn khi đúc ly tâm đứng nh− sau: Gọi tọa độ bề mặt trong vật đúc X B1 B, XB2 B, YB1 B, YB2 B nh− trên hình sau: Ta có: 12 2 1 Y g 2X ω= ; 22 2 2 Y g 2X ω= Do đó: ( ) ( )( )21212122221 XXXXYYg2XX −+=−ω=− Gọi XB1 B + XB2 B = 2R Btb B (R Btb B: bán kính trung bình bề mặt trong vật đúc) XB1 B - XB2 B = ∆ YB1 B - YB2 B = H Thay vào trên ta có: H. g2 .R.2 2th ω=∆ ở đây, ω: vận tốc góc; ⎟⎠ ⎞⎜⎝ ⎛π=ω s 1 30 n. ; g: gia tốc trọng tr−ờng; g = 981 cm/s P2 P Ta có: H. n. 30.981.2 .R.2 22 2 th π=∆ Vậy: ( )ph/vg .R H 300n tb ∆ ≈ . Th−ờng, n = 600 ữ 1500 vg/ph. Từ công thức này, ta thấy nếu n cố định, H càng lớn thì ∆ càng lớn, tức là nếu chiều cao vật đúc càng lớn thì chênh lệch bán kính trong của vật đúc càng lớn. Vì vậy, ph−ơng pháp đúc ly tâm đứng chỉ dùng để đúc những vật ngắn. b) Đúc ly tâm nằm Đúc ly tâm nằm là đúc ly tâm mà khuôn quay theo ph−ơng nằm ngang. Để kim loại rải đều theo chiều dài của khuôn, ng−ới ta dùng một máng rót, khi rót kim loại vào khuôn máng rót di chuyển dọc theo trục quay của khuôn. O XB1 XB2 H = Y B 1B - Y B 2 YB2 YB1 R Bth B ∆ = XB1 B - XB2 X YB Simpo PDF Merge and Split Unregistered Version - Giáo trình: công nghệ đúc Tr−ờng đại học bách khoa - 2006 51 Ph−ơng pháp này khi đúc ống thì chiều dày của vật đúc ở hai đầu không có sự chênh lệch nhau, đ−ờng kính trong và ngoài của vật đúc là những vòng tròn đồng tâm nhau. Nh−ng đúc ly tâm nằm do phải dùng máng rót kim loại nên không thể đúc đ−ợc những ống có đ−ờng kính nhỏ. Số vòng quay của khuôn ng−ời ta tính bằng công thức sau: ( )ph/vg r k n 0= Trong đó: r là bán kính của vật đúc (cm); k B0 B: hệ số phụ thuộc vào kim loại vật đúc; đúc gang k B0 B = 1800 ữ 2500; đúc thép k B0 B = 2150 ữ 2730; đúc đồng đỏ k B0 B = 2000 ữ 2200; đúc đồng thanh k B0 B = 1900; đúc nhôm k B0 B = 2600 ữ 3500. Để kim loại chảy đều vào trong khuôn, đôi khi ng−ời ta đặt trục quay của khuôn nghiêng với mặt phẳng ngang một góc α ≤ 5 P0 P. 11.3.3- Khuôn đúc ly tâm Khuôn đúc ly tâm làm việc trong điều kiện rất khó khăn (nhiệt độ thay đổi, chịu áp lực của kim loại lỏng và lực ly tâm). Vì thế, yêu cầu vật liệu làm khuôn cần có cơ tính cao. Ng−ời ta th−ờng dùng gang hợp kim, thép C và thép hợp kim để làm khuôn đúc ly tâm. Để tăng tính thoát khí, vật đúc nguội chậm và khi đúc vật định hình... ng−ời ta có thể làm vỏ khuôn bằng kim loại còn phân bên trong bằng cát khuôn, đất sét, thạch cao. Để lấy vật đúc khỏi khuôn, dùng chốt đẩy vật đúc; để làm nguội khuôn cần đặt một hệ thống t−ới n−ớc. 11.4. đúc trong khuôn mẫu chảy 11.4.1- Khái niệm Đúc trong khuôn mẫu chảy thực chất là đúc trong khuôn cát nh−ng mẫu đ−ợc làm bằng vật liệu dễ chảy. Ph−ơng pháp này có −u điểm sau: - Có thể đúc đ−ợc những vật đúc rất phức tạp và đúc đ−ợc những hợp kim khỏ chảy nh− thép không gỉ, thép gió... - Độ chính xác và độ bóng bề mặt vật đúc rất cao vì: độ chính xác của mẫu chảy lớn, không có mặt phân khuôn nên không có sự sai lệch khuôn và khuyết tật do lắp ráp khuon gây ra, không có nguyên công rút mẫu nên giảm đ−ợc sai số do việc rút mẫu, rót kim loại lỏng vào khuôn đã đ−ợc nung nóng nên giảm ứng suất nhiệt do đó vật đúc ít bị nứt, cong vênh. Nh−ng có nh−ợc điểm là: c−ờng độ lao động cao, chu trình sản xuất dài, giá thành chế tạo khuôn cao. Đúc trong khuôn mẫu chảy đ−ợc dùng nhiều trong sản xuất hàng loạt để chế tạo các loại dụng cụ nh− dao phay, dao chuốt; chế tạo các loại bánh răng; líp xe đạp; đĩa H.11.4. sơ đồ đúc ly tâm nằm Simpo PDF Merge and Split Unregistered Version - Giáo trình: công nghệ đúc Tr−ờng đại học bách khoa - 2006 52 môtô; các phụ tùng trong máy nổ... vật đúc có khối l−ợng từ 0,02 ữ 100kg; chiều dày đến 0,3mm và đ−ờng kính lỗ đến 2mm. 11.4.2- Công nghệ chế tạo vật đúc trong khuôn mẫu chảy Quá trình công nghệ đúc trong khuôn mẫu chảy gồm những b−ớc sau: - Chế tạo mẫu gốc: mẫu gốc có hình dáng giống hệt vật đúc, mẫu gốc dùng để chế tạo khuôn ép. Vật liệu để chế tạo mẫu gốc có thể là thép, đồng thau, gỗ, chất dẻo... Ph−ơng pháp chế tạo mẫu gốc giống nh− chế tạo mẫu thông th−ờng tức là có thể đúc hoặc gia công cơ khí. Khi chế tạo mẫu gốc cần phải tính đến độ co và l−ợng d− của mẫu gốc, độ co và l−ợng d− của khuôn ép, độ co của vật đúc... Một số nơi dùng ngay chi tiết làm mẫu gốc nh−ng nh− thế không chính xác. - Chế tạo khuôn ép: Khuôn ép có thể làm bằng kim loại, ximăng hoặc thạch cao. Chế tạo khuôn ép đ−ợc tiến hành bằng gia công áp lực, đúc, gia công cơ khí hoặc đúc rồi gia công cơ khí. Kết cấu của khuôn ép cũng th−ờng chia làm hai nửa khuôn (để dễ lấy mẫu chảy ra khỏi khuôn ép), có hệ thống rót để rót mẫu chảy vào khuôn. Yêu cầu chế tạo khuôn ép chính xác và nhẵn bóng vì nó quyết định độ bóng, độ chính xác của mẫu chảy. - Chế tạo vật liệu dễ chảy: Vật liệu dễ chảy bao gồm nhựa thông, sáp, paraphin, stêarin. Thành phần vật liệu dễ chảy th−ờng dùng nh− sau: 70% nhựa thông + 20% sáp + 10% paraphin. H.11.5. Quy trình công nghệ đúc trong khuôn mẫu chảy Simpo PDF Merge and Split Unregistered Version - Giáo trình: công nghệ đúc Tr−ờng đại học bách khoa - 2006 53 hoặc 30% paraphin + 70% stêarin. Nhiệt độ chảy của vật liệu dễ chảy th−ờng là 50 ữ 90 P0 PC. Yêu cầu vật liệu dễ chảy không đ−ợc mềm ra ở nhiệt độ d−ới 30 ữ 35 P0 PC, đồng thời phải có tính chảy loãng để điền đầy khuôn ép. Ng−ời ta nấu vật liệu dễ chảy trong lò nồi, điện trở hoặc cảm ứng. Khi nấu cần phải khuấy đều và gạt bỏ những tạp chất khác nổi trên vật dễ chảy. - Chế tạo mẫu chảy: ép vật liệu dễ chảy vào khuôn ép với áp suất khoảng 2at. Để nguội cho mẫu đông đặc rồi mở khuôn ép, lấy mẫu và sửa mẫu. - Lắp một số mẫu với nhau thành một nhóm mẫu chảy có chung hệ thống rót: mục đích để tăng năng suất đúc. - Chế tạo khuôn: sơn một lớp dung dịch chịu nhiệt lên nhóm mẫu chảy , thành phần sơn thừng là: 90% bột cát thạch anh + 7% cao lanh + 3% grafit trộn với dung dịch 20% n−ớc thuỷ tinh + 80% n−ớc. Th−ờng sơn 2 ữ 3 lần đối với mẫu nhỏ, 4 ữ 5 lần đối với mẫu lớn. Sau mỗi lần sơn ta rắc một lớp cát thạch anh và sấy ngoài không khí trong 30 ữ 40 phút. Chiều dày lớp sơn cần đảm bảo là 1 ữ 1,5 mm. Sau đó đem nhóm mẫu chảy đã đ−ợc sơn lớp vỏ chịu nhiệt đi làm khuôn cát bằng cách đặt vào trong hòm khuôn và tiến hành làm khuôn trên máy rung (khuôn cát chỉ để tăng sức bền cho lớp vỏ). Sau đó sấy ở nhiệt độ 100 ữ 120 P0 PC để cho mẫu chảy ra ngoài và ta thu đ−ợc khuôn đúc. Đối với những chi tiết nhỏ, có thể không cần làm thêm khuôn cát ở ngoài mà đem nhóm mẫu đã đ−ợc sơn lớp cát chịu nhiệt nhúng vào n−ớc nóng hoặc hơ nóng ở nhiệt độ 80 ữ 90 P0 PC làm mẫu chảy chảy ra ngoài và ta thu đ−ợc lòng khuôn. - Sấy khuôn: sấy khuôn trong lò ở nhiệt độ 850 ữ 900 P0 PC để đốt cháy hợp chất dễ chảy còn sót lại, đồng thời tăng độ bền và tăng tính thông khí cho khuôn. - Nấu chảy kim loại, rót kim loại vào khuôn, dở khuôn và làm sạch vật đúc. 11.5. đúc trong khuôn vỏ mỏng 11.5.1- Khái niệm Đúc trong khuôn vỏ mỏng là dạng đúc trong khuôn cát nh−ng thành khuôn mỏng chừng 6 ữ 8mm. Đúc trong khuôn vỏ mỏng có những đặc điểm sau: - Có thể đúc đ−ợc gang, thép, kim loại màu (nh− khuôn cát), khối l−ợng vật đúc đến 100kg, độ chính xác đạt cấp 7. - Khuôn vỏ mỏng là khuôn khô, nhẵn bóng, thông khí tốt, truyền nhiệt kém, không hút n−ớc và bền nên cho phép nhận đ−ợc vật đúc ít rỗ, xốp, nứt và những khuyết tật khác. Đồng thời giảm đ−ợc hao phí kim loại cho hệ thống rót vì không cần hệ thống rót lớn nh− trong khuôn cát. Simpo PDF Merge and Split Unregistered Version - Giáo trình: công nghệ đúc Tr−ờng đại học bách khoa - 2006 54 - Do tính truyền nhiệt kém nên khi đúc gang không bị hoá trắng. Nhiệt độ rót có thể nhỏ hơn trong khuôn cát chừng 20 ữ 30 P0 PC. - Đơn giản hoá quá trình dở khuôn và làm sạch vật đúc. Quá trình chế tạo khuôn vỏ mỏng dễ cơ khí hoá và tự động hoá. Hỗn hợp khuôn vỏ mỏng bao gồm bột cát thạch anh với 4ữ6% punvebakêlit (punvebakêlit là hỗn hợp của fênôn và urêtrôpin, nó dễ đông đặc, dễ nhào trộn với cát, cất giữ thuận lợi nh−ng đắt và hiếm). Hỗn hợp khuôn cát và punvêkakêlit có đặc tính là ở nhiệt độ 200 ữ 250 P0 PC phần tử fênôn chảy ra và có khả năng dính kết các hạt cát với nhau, tự hoá cứng tạo nên hỗn hợp khuôn có độ bền khoảng 20 ữ 50 N/cm P2 P. Sau khi đã hoá cứng, nó không có khả năng chảy ra nữa mặc dù nung nóng đến nhiệt độ cao hơn 250P0 PC. 11.5.2- Công nghệ chế tạo vật đúc trong khuôn vỏ mỏng Trình tự đúc trong khuôn vỏ mỏng nh− sau: - Ghép mẫu vào tấm mẫu: dùng mẫu bằng kim loại kẹp chặt trên tấm mẫu bằng thép hoặc gang xám. Làm sạch mẫu và tấm mẫu rồi phun lên trên một lớp cách mẫu bằng dầu mazut. - Nung nóng mẫu và tấm mẫu đến nhiệt độ 220 ữ 250 P0 PC. - Lấy mẫu và tấm mẫu ra khỏi lò, quay đi 180P0 P rồi kẹp chặt với thùng chứa hỗn hợp làm khuôn. - Quay thùng chứa hỗn hợp khuôn cùng với mẫu và tẫm mẫu 180P0 P. Vật liệu làm khuôn sẽ đè lên mẫu và tấm mẫu. Nhờ mẫu và tấm mẫu nóng nên làm các phần tử fênôn chảy ra và liên kết các hạt cát với nhau. Giữ ở vị trí đó trong khoảng 12ữ20 giây, ta sẽ đ−ợc chiều dày lớp khuôn khoảng 6ữ8mm. - Quay thùng chứa hỗn hợp khuôn cùng với tấm mẫu trở về vị trí ban đầu - Lấy tấm mẫu, mẫu cùng với lớp khuôn vỏ mỏng đem sấy ở nhiệt độ 350 ữ 370 P0 PC trong 1 ữ 2 phút để làm chảy đều những phần tử punvebakêlit còn sót lại, làm dính kết đều các hạt cát, nâng cao độ bền cho khuôn. - Tách khuôn vỏ mỏng khỏi mẫu và tấm mẫu. - Làm một nửa khuôn kia cũng theo trình tự trên. Quá trình làm lõi cũng t−ơng tự nh− quá trình làm khuôn nh−ng làm trên máy thổi cát. Sau đó tiến hành lắp khuôn, lõi: ghép hai nửa khuôn bằng cách dán hoặc kẹp. Để tăng độ bền cho khuôn nhất là khi đúc những chi tiết lớn, sau khi kẹp các nửa khuôn với nhau, ta đem đặt khuôn vỏ mỏng vào hòm khuôn và làm khuôn cát bao bọc xung quanh hoặc kẹp thêm bằng một khung kim loại. Cuối cùng đem rót kim loại vào khuôn, dỡ khuôn và thu nhận vật đúc. Simpo PDF Merge and Split Unregistered Version - Giáo trình: công nghệ đúc Tr−ờng đại học bách khoa - 2006 55 11.6. đúc liên tục 11.6.1- Khái niệm Đúc liên tục là quá trình rót kim loại lỏng đều và liên tục vào một khuôn bằng kim loại, xung quanh hoặc bên trong khuôn có n−ớc l−u thông làm nguội (còn gọi là bình kết tinh). Nhờ truyền nhiệt nhanh nên kim loại lỏng sau khi rót vào khuôn đ−ợc kết tinh ngay. Vật đúc đ−ợc kéo liên tục ra khỏi khuôn bằng những cơ cấu đặc biệt (nh− con lăn, bàn kéo...). Đúc liên tục có các đặc điểm sau: - Có khả năng đúc đ−ợc các loại ống, thỏi và các dạng định hình khác bằng thép, gang, kim loại màu, có tiết diện không đổi và chiều dài không hạn chế; đúc đ−ợc tấm kim loại thay cho cán, đặc biệt là có thể đúc đ−ợc các loại tấm bằng gang. - Kim loại đông đặc dần dần từ phía d−ới lên trên và đ−ợc bổ sung liên tục nên không bị rỗ co, rỗ khí, rỗ xỉ, ít bị thiên tích; có độ mịn chặt cao, thành phần hoá học đồng nhất và cơ tính cao. Vì đúc trong khuôn kim loại nên tổ chức nhỏ mịn, cơ tính cao và chất l−ợng bề mặt tốt. - Năng suất cao, giảm hao phí chế tạo khuôn, không tốn kim loại vào hệ thống rót, phế phẩm ít nên giá thành chế tạo thấp. Nh−ng đúc liên tục có nh−ợc điểm chủ yếu là tốc độ nguội quá nhanh gây nên ứng suất bên trong lớn, làm cho vật đúc dễ bị nứt (nhất là những kim loại có sự chuyển pha ở thể đặc). Cũng vì lý do này kim loại vật đúc bị hạn chế. Để khắc phục hiện t−ợng này, ng−ời ta có thể làm nguội khuôn bằng dầu mà không dùng n−ớc. Ngoài ra còn nh−ợc điểm là không đúc đ−ợc vật phức tạp, vật có tiết diện thay đổi. 11.6.2- Các loại đúc liên tục a/ Đúc ống liên tục: Quá trình đúc tiến hành nh− sau: Tr−ớc tiên kẹp đầu mồi 7 trên tấm đỡ 4. Đ−a tấm đỡ 4 ép sát đáy khuôn 8. Rót kim loại lỏng từ thùng rót 2 qua máng rót 3 vào khuôn đến mức cách mặt trên khuôn 20 ữ 25mm. Khi kim loại đông đặc ta quay vítme 5 bằng động cơ 6 để hạ tấm đỡ 4, đầu mồi 7 đi xuống, do đó kéo vật đúc 7 dần dần ra khỏi khuôn. Khuôn và lõi luôn luôn đ−ợc n−ớc l−u thông làm nguội. Để dễ kéo vật ra khỏi khuôn, nâng cao độ bóng bề mặt vật đúc và hạn chế nứt trên bề mặt vật đúc, trong quá trình đúc, ng−ời ta còn cho khuôn chuyển động khứ hồi dọc theo ph−ơng chuyển động của vật đúc. Tr−ớc tiên cho khuôn chuyển động từ trên xuống d−ới một khoảng 8 ữ 10mm cùng tốc độ chuyển động của vật đúc. Rồi cho khuôn chuyển động thật nhanh một đoạn đ−ờng 2 ữ 3mm, cuối cùng cho khuôn chuyển động từ d−ới lên trên ng−ợc Simpo PDF Merge and Split Unregistered Version - Giáo trình: công nghệ đúc Tr−ờng đại học bách khoa - 2006 56 chiều chuyển động của vật đúc với hành trình khoảng 10 ữ 13mm và tốc độ lớn hơn tốc độ lúc đầu. Cứ thế trong quá trình đúc, khuôn luôn chuyển động khứ hồi: nhờ ma sát giữa thành khuôn với vật đúc làm cho bề mặt vật đúc nhẵn bóng và vật đúc chỉ ra khỏi khuôn sau khi đã chuyển biến pha nên không bị nứt. Để dễ lấy vật đúc ra khỏi khuôn, ng−ời ta còn cho vào thành lòng khuôn, lõi một lớp dầu mazut; l−ợng dầu cần dùng từ 120 ữ 150 (g/tấn) kim loại. Vật liệu làm khuôn và những thông số đúc: vật liệu làm khuôn cần chọn loại dẫn nhiệt tốt, th−ờng để đúc kim loại màu thì khuôn làm bằng hợp kim đồng hoặc hợp kim nhôm, chiều dày khuôn 6 ữ 8mm. Nhiệt độ rót cho mọi hợp kim th−ờng lấy 30 ữ 50 P0 PC trên đ−ờng lỏng, tốc độ rót và chiều cao khuôn tùy thuộc vào hợp kim đúc. Ví dụ khi đúc ống, thỏi có đ−ờng kính 100 ữ 400mm bằng hợp kim silumin chiều cao khuôn 100ữ150mm, tốc độ rót 2ữ3 m/h, nhiệt độ rót trên đ−ờng lỏng 30ữ50 P0 PC. b/ Đúc tấm: Quá trình đúc tiến hành nh− sau: Rót kim loại lỏng từ thùng chứa 1 vào cốc rót 2, qua máng dẫn 3 vào khe hở giữa 2 con lăn 4 (bên trong có n−ớc làm nguội và quay ng−ợc chiều nhau) tạo ra tấm 5. Ph−ơng pháp này có thể chế tạo các tấm bằng gang, thép, kim loại màu thay cho cán. Đối với gang có thể đúc đ−ợc tấm mỏng từ 0,7 ữ 1,2 mm. Nhiệt độ rót n−ớc gang từ 1370 ữ 1400 P0 PC. Tấm gang ra khỏi khuôn bên ngoài nguội nh−ng bên trong vẫn nóng nên có thể đem dập thành các đồ vật hoặc cắt thành phiến nhỏ. Sau khi ủ ng−ời ta có thể uốn đ−ợc. H.11.7. Sơ đồ đúc tấm. Simpo PDF Merge and Split Unregistered Version -
File đính kèm:
giao_trinh_cong_nghe_duc.pdf