Giáo trình Chuẩn đoán động cơ
Khái niệm chung về chẩn đoán kỹ thuật động cơ
Động cơ đốt trong là một tổ hợp phức tạp của nhiều cụm và chi tiết máy. Trong quá trình vận hành, dưới tác dụng của các yếu tố ma sát như tải trọng, vận tốc trượt, nhiệt độ. gây ra các hư hỏng (mài mòn, tróc rỗ, mỏi, xâm thực, ăn mòn.) làm thay đổi kích thước chi tiết và biến dạng hình dáng hình học (cong, vênh, uốn, xoắn) hoặc thay đổi cơ tính của vật liệu. Kết quả là các trạng thái làm việc như khe hở lắp ghép của bạc- trục ngày càng tăng, độ kín khít nhóm xy lanh-xéc măng-pit tông suy giảm, quy luật nạp thải khí, cung cấp nhiên liệu bị thay đổi v.v. Tất cả những điều đó làm xấu đi tính năng kinh tế kỹ thuật của động cơ đến mức không thể tiếp tục làm việc được và phải đưa chúng vào sửa chữa.
Các hư hỏng trong động cơ điêden tập trung vào các bô phận và hệ thống gồm: Nhóm pit tông-xy lanh-xéc măng, Cơ cấu trục khuỷu-thanh truyền, Cơ cấu phối khí, Hệ thống nhiên liệu; Những hư hỏng của các hệ thống khác chiểm tỉ lệ không lớn.
Tình trạng chất lượng của động cơ phụ thuộc vào chất lượng của các chi tiết lắp ghép trên chúng và được đặc trưng bởi các thông số như: kích thước và khe hở lắp ghép, độ song song, đồng tâm, vuông góc, mức độ kín khít v.v.
Trong quá trình làm việc, các thông số thể hiện chất lượng bên trong sẽ phản ánh ra bên ngoài dưới một loạt các biểu hiện gián tiếp như: Công suất, Thành phần khí thải, Nhiệt độ nước làm mát, Nhiệt độ dầu bôi trơn, Tiếng ồn và va đập, Hàm lượng mạt kim loại trong dầu bôi trơn, Áp suất cuối kỳ nén, Áp suất dầu bôi trơn, Độ lọt khí các te, Mức tiêu hao nhiên liệu và dầu bôi trơn v.v.
Giữa các thông số bên trong và các biểu hiện ra bên ngoài của chúng có mối qua hệ chặt chẽ với nhau, ví dụ: Khe hở pít tông - xy lanh - xéc măng tăng do tình trạng mài mòn, sẽ làm công suất động cơ bị giảm, và độ lọt khí các te tăng cao; Hoặc khe hở giữa đuôi xu páp và đòn bẩy bị tăng do mòn các chi tiết này, sẽ làm tiếng gõ đuôi xu páp phát triển mạnh lên.
Như vậy để xác định tình trạng mài mòn, hư hỏng của các chi tiết bên trong, chỉ cần đo giá trị của các thông số biểu hiện ra bên ngoài đại diện cho chúng mà không cần phải tháo máy, đó chính là thực chất của công việc chẩn đoán kỹ thuật.
Tóm tắt nội dung tài liệu: Giáo trình Chuẩn đoán động cơ
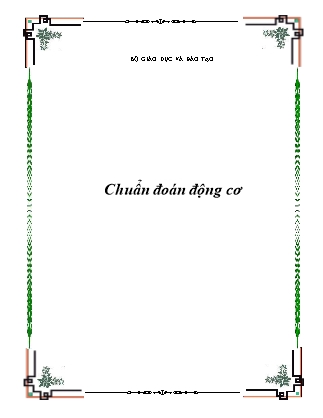
BỘ GIÁO DỤC VÀ ĐÀO TẠO Chuẩn đoán động cơ A - lý thuyÕt chÈn do¸n tr¹ng th¸I kü thuËt ®éng c¬ Sau khi häc song bµi häc nµy, Sinh viªn cã kh¶ n¨ng: Tr×nh bµy kh¸i niÖm, c¸c chØ tiªu ®¸nh gi¸ vµ ph¬ng ph¸p chÈn ®o¸n ®éng c¬. Tr×nh bµy c¸ch sö dông c¸c lo¹i thiÕt bÞ kiÓm tra chÈn ®o¸n th«ng thêng trong c«ng t¸c chÈn ®o¸n kü thuËt ®éng c¬. Thùc hiÖn an toµn vµ vÖ sinh c«ng nghiÖp. 1. Các vấn đề chung 1.1. Khái niệm chung về chẩn đoán kỹ thuật động cơ Động cơ đốt trong là một tổ hợp phức tạp của nhiều cụm và chi tiết máy. Trong quá trình vận hành, dưới tác dụng của các yếu tố ma sát như tải trọng, vận tốc trượt, nhiệt độ... gây ra các hư hỏng (mài mòn, tróc rỗ, mỏi, xâm thực, ăn mòn..) làm thay đổi kích thước chi tiết và biến dạng hình dáng hình học (cong, vênh, uốn, xoắn) hoặc thay đổi cơ tính của vật liệu. Kết quả là các trạng thái làm việc như khe hở lắp ghép của bạc- trục ngày càng tăng, độ kín khít nhóm xy lanh-xéc măng-pit tông suy giảm, quy luật nạp thải khí, cung cấp nhiên liệu bị thay đổi v.v.. Tất cả những điều đó làm xấu đi tính năng kinh tế kỹ thuật của động cơ đến mức không thể tiếp tục làm việc được và phải đưa chúng vào sửa chữa. Các hư hỏng trong động cơ điêden tập trung vào các bô phận và hệ thống gồm: Nhóm pit tông-xy lanh-xéc măng, Cơ cấu trục khuỷu-thanh truyền, Cơ cấu phối khí, Hệ thống nhiên liệu; Những hư hỏng của các hệ thống khác chiểm tỉ lệ không lớn. Tình trạng chất lượng của động cơ phụ thuộc vào chất lượng của các chi tiết lắp ghép trên chúng và được đặc trưng bởi các thông số như: kích thước và khe hở lắp ghép, độ song song, đồng tâm, vuông góc, mức độ kín khít v.v. Trong quá trình làm việc, các thông số thể hiện chất lượng bên trong sẽ phản ánh ra bên ngoài dưới một loạt các biểu hiện gián tiếp như: Công suất, Thành phần khí thải, Nhiệt độ nước làm mát, Nhiệt độ dầu bôi trơn, Tiếng ồn và va đập, Hàm lượng mạt kim loại trong dầu bôi trơn, Áp suất cuối kỳ nén, Áp suất dầu bôi trơn, Độ lọt khí các te, Mức tiêu hao nhiên liệu và dầu bôi trơn v.v. Giữa các thông số bên trong và các biểu hiện ra bên ngoài của chúng có mối qua hệ chặt chẽ với nhau, ví dụ: Khe hở pít tông - xy lanh - xéc măng tăng do tình trạng mài mòn, sẽ làm công suất động cơ bị giảm, và độ lọt khí các te tăng cao; Hoặc khe hở giữa đuôi xu páp và đòn bẩy bị tăng do mòn các chi tiết này, sẽ làm tiếng gõ đuôi xu páp phát triển mạnh lên. Như vậy để xác định tình trạng mài mòn, hư hỏng của các chi tiết bên trong, chỉ cần đo giá trị của các thông số biểu hiện ra bên ngoài đại diện cho chúng mà không cần phải tháo máy, đó chính là thực chất của công việc chẩn đoán kỹ thuật. 1.2. Các chỉ tiêu đánh giá trạng thái chất lượng động cơ Đối với động cơ, việc xem xét chúng có hoạt động bình thường hay không, được dựa theo các mặt sau: Động cơ dễ khởi động, chạy ổn định ở các chế độ vòng quay. Công suất động cơ đảm bảo, thể hiện qua khả năng mang tải, có tính năng tăng tốc và vượt dốc tốt. Động cơ không nóng quá và không có các tiếng gõ kim loại bất thường. Tiêu hao nhiên liệu trong phạm vi cho phép. Khí xả không màu hoặc có màu nâu nhạt khi sử dụng công suất tối đa. Không có hiện tượng rò rỉ nhiên liệu, dầu, nước ở các mối ghép, ống nối. Khi có một yếu tố nào đó không đạt, cần phải kiểm tra (chẩn đoán) để tìm ra nguyên nhân và khắc phục kịp thời. Động cơ chỉ được phép vận hành khi tất cả các đặc tính kỹ thuật đều nằm trong giới hạn cho phép. 1.3. Phân loại các phương pháp chẩn đoán a. Chẩn đoán chung Dựa vào các thông số phản ánh chung trạng thái chất lượng của động cơ để chẩn đoán, bao gồm: Công suất hữu ích Nhiệt độ và thành phần khí xả Tổn thất cơ giới Mức độ ồn và va đập Hàm lượng mạt kim loại trong dầu bôi trơn b. Chẩn đoán hệ thống Dùng các thông số phản ánh trạng thái chất lượng của từng cơ cấu, hệ thống trong động cơ làm chẩn đoán. Những thông số được sử dụng thường là: - Hệ thống nhiên liệu động cơ điêden: Góc phun sớm Áp suất phun Lượng nạp chu trình, độ đồng đều lượng nạp giữa các nhánh - Hệ thống bôi trơn: Độ chênh lệch áp suất dầu bôi trơn trước và sau lọc Áp suất dầu trên đường dầu chính Áp suất mở các van an toàn trên đường dầu chính và lọc dầu - Hệ thống phối khí: Lưu lượng khí nạp Độ kín xu páp và đế - Hệ thống làm mát: Độ chênh lệch nhiệt độ nước làm mát trước và sau két Nhiệt độ bắt đầu mở van hằng nhiệt Nhiệt độ bắt đầu mở van điện từ đóng ly hợp quạt gió hoặc van điều chỉnh dầu vào khớp nối thuỷ lực của quạt gió c. Chẩn đoán riêng Nhằm xác định hư hỏng của một số chi tiết trong động cơ, các chẩn đoán riêng cho các nhóm chi tiết như sau: - Nhóm pít tông - xéc măng - xi lanh : Lượng khí lọt xuống các te trong một đơn vị thời gian Mức độ tiêu hao dầu nhờn thành muội than Độ rò rỉ khí nén trong buồng cháy (thử ở trạng thái tĩnh) Độ chân không đường nạp Áp suất cuối kỳ nén - Nhóm thanh truyền - trục khuỷu và bạc Áp suất dầu bôi trơn trên đường dầu chính Tiếng gõ trục - bạc Cường độ va đập của nhóm pít tông thanh truyền khi thay đổi liên tục áp suất khí nén trong buồng cháy (thử ở trạng thái tĩnh) 2. Các phương pháp chẩn đoán động cơ 2.1. Chẩn đoán động cơ theo trạng thái khởi động Trạng thái khởi động thể hiện độ chính xác của các thông số lắp ráp cũng như sự làm việc tốt của các bộ phận và hệ thống của động cơ. Khi một động cơ điêden khó nổ cần có biện pháp kiểm tra và xử lý thích hợp. Trước tiên cần kiểm tra thùng nhiên liệu xem còn nhiên liệu không và khoá nhiên liệu đóng hay mở. Nếu thùng nhiên liệu và khoá nhiên liệu mở thì có thể do các nguyên nhân sau: Tắc nhiên liệu hoặc lẫn nước trong nhiên liệu: Kiểm tra lại lõi lọc và thùng nhiên liệu xem có bị lẫn nước và cặn bẩn gây tắc lọc không. Trong đường nhiên liệu có không khí: Cần kiểm tra xả hết khí ra khỏi hệ thống và xiết chặt lại các khớp nối của đường nhiên liệu. Góc phun sớm nhiên liệu sai: Cần kiểm tra và chỉnh lại góc phun sớm theo quy định. Động cơ dùng loại bơm tổng thì việc kiểm tra góc bắt đầu cấp nhiên liệu của các xi lanh đã được làm trên băng thử. Như vậy khi điều chỉnh chỉ cần đặt chính xác thời điểm cấp của nhánh bơm số 1 so với góc quay trục khuỷu là được. Xác định góc phun sớm bằng súng kiểm tra thời điểm hoặc dùng ống thời kế. Nếu sai lệch trên 3o góc quay trục khuỷu thì cần phải điều chỉnh lại. Cách điều chỉnh góc phun sớm tuỳ thuộc vào cấu tạo cụ thể từng loại bơm cao áp; Có 3 loại kết cấu điều chỉnh phổ biến là: Xoay khớp nối bơm với động cơ. Xoay vỏ bơm cao áp trên thân động cơ. Thay đổi vị trí lắp của bích trung gian so với bánh răng dẫn động bơm cao áp, cứ thay đổi một vị trí lắp khác có thể điều chỉnh được 1o30' góc quay trục cam tức là 3o góc quay trục khuỷu. Khe hở xu páp sai: Kiểm tra và điều chỉnh lại theo quy định. Trời lạnh dầu bôi trơn đặc, khi khởi động khó quay động cơ với tốc độ nhanh nên máy khó nổ. Có thể dùng biện pháp sấy nóng nước, dầu bôi trơn hoặc không khí để nâng nhiệt độ buồng cháy. Đối với các động cơ có trang bị vòi phun nhiên liệu trên đường nạp hay dùng bu gi sấy phải kiểm tra xem những bộ phận này có hoạt động hay không. Áp suất nén yếu, có thể do: Mòn pít tông, xéc măng khí, xy lanh, hở xupáp, hoặc hở đệm nắp máy. Đổ một ít dầu nhờn vào đường ống hút để bao kín buồng cháy làm tăng áp suất nén, nếu không hiệu quả là do bị hở, phải tìm nguyên nhân và xử lý (xiết lại gujông nắp xy lanh, đệm hỏng phải thay đệm mới, xu páp hở phải mài rà lại...) Bộ đôi pít tông - xy lanh bơm cao áp, bộ đôi kim phun mòn: Phải đưa lên thiết bị cân bơm để kiểm tra, thay mới và điều chỉnh lại theo đúng các điều kiện kỹ thuật của bơm; Lúc lắp bơm cao áp phải kiểm tra lại góc phun sớm. Nếu thay bộ đôi kim phun phải kiểm tra và điều chỉnh lại áp suất bắt đầu mở kim phun theo quy định của nhà sản xuất. Số vòng quay động cơ lúc tăng lúc giảm: Kiểm tra xem bộ điều tốc hoạt động có nhạy không, thanh răng bơm cao áp có bị kẹt hay không, đường nhiên liệu có lẫn khí hay nước không và tìm cách khắc phục. 2.2. Chẩn đoán động cơ theo công suất hữu ích a. Đặc điểm chung Công suất chịu ảnh hưởng của rất nhiều yếu tố như: Chất lượng quá trình cháy, độ kín khít của nhóm chi tiết bao kín buồng cháy, sự làm việc của các hệ thống phối khí-nhiên liệu- đánh lửa, trạng thái nhiệt độ, tổn thất ma sát.v.. Những hiện tượng công suất giảm đột ngột so với định mức thường là do các sự cố như góc đánh lửa sớm, góc phun sớm sai (do lắp sai hoặc do bộ tự động điều chỉnh phun sớm làm việc tồi), bỏ máy do cong vênh xu páp, kẹt-gãy xéc măng, hư hỏng vòi phun-bơm cao áp v.v. b. Các nguyên nhân làm giảm công suất Không đủ áp suất nén do nhóm bao kín buồng cháy không tốt. Bình lọc khí tắc. Bộ tuốc bin tăng áp làm việc không tốt. Khe hở xu páp sai. Bó bạc hoặc bó pít tông-xy lanh do thiếu dầu bôi trơn, do dãn nở nhiệt (quan sát khí thải, kiểm tra nhiệt độ của: động cơ, nước, dầu bôi trơn để xác định nguyên nhân). Đường dẫn nhiên liệu bị gián đoạn: Do hết nhiên liệu, do hệ thống bị tắc hoặc hở. Góc phun sớm sai. Bộ đôi bơm cao áp, bộ đôi kim phun mòn làm thiếu dầu phun vào xy lanh. Bộ đôi kim phun bị kẹt dẫn đến bỏ máy. Van cao áp (van một chiều) bị hở làm nhiên liệu không cấp được lên vòi phun làm bỏ máy (tháo đai ốc của ống cao áp nối với bơm, dùng bơm tay bơm căng nhiên liệu, nếu thấy dầu tràn ra khỏi đầu răc co là van hở). Vòng quay động cơ không đạt do bộ điều tốc cắt quá sớm. c. Biểu hiện của động cơ khi công suất yếu Nóng máy Khói đậm màu Tăng tốc kém Không kéo được tải lớn Áp suất nén yếu Trong một số trường hợp, máy có tiếng kêu bất thường, tốc độ không ổn định và tăng tiêu hao nhiên liệu, dầu bôi trơn. d. Phương pháp đo công suất khi chẩn đoán động cơ Việc đo công suất trên băng thử có độ chính xác cao, song chỉ dùng trong trường hợp kiểm tra động cơ sau đại tu vì phương pháp này tốn nhiều công tháo lắp, thiết bị phức tạp. Để đảm bảo phép đo thực hiện nhanh chóng phù hợp với đặc điểm của công việc chẩn đoán, thường áp dụng một số phương pháp đo công suất như sau: - Đo mô men chủ động trên bánh xe: Áp dụng cho động cơ lắp trên các phương tiện vận tải; Dùng thiết bị đo lực phanh trên bánh xe, từ đó tính được mo men và công suất động cơ. Sai số chính của phương pháp là khó biết chính xác hiệu suất các bộ truyền trên xe cần đo. - Phương pháp đo không phanh: Phương pháp này sử dụng tổn thất cơ giới của các xy lanh không làm việc để tạo tải cho xy lanh cần đo, áp dụng đối với động cơ nhiều xy lanh. Khi đo, lần lượt cho từng xy lanh làm việc (các xy lanh còn lại được tháo ống dẫn dầu cao áp tới vòi phun) và đo số vòng quay tương ứng của động cơ. Công suất của động cơ được xác định như sau: Nđo = Neđm - k(nđm - ntb) Trong đó: Neđm nđm ntb ni k : Công suất định mức của động cơ : Số vòng quay định mức : Trị số trung bình của các vòng quay đo = åni/i : Số vòng quay đo của từng xi lanh : Hệ số kinh nghiệm, đối với động cơ 4 xy lanh lắp trên máy kéo, k= 0,022¸0,040 - Đo công suất bằng phương pháp gia tốc Cách đo này dựa trên nguyên tắc công suất càng cao thì thời gian tăng tốc từ số vòng quay nhỏ đến vòng quay định mức càng ngắn và ngược lại. Thiết bị ИM-2M do Nga chế tạo dựa trên nguyên tắc này, sử dụng cảm biến điện từ lắp trên vỏ hộp bánh đà của động cơ, khi một răng của vành răng khởi động quét qua cảm biến sẽ tạo ra một xung điện hình sin, với tần số xung f = n.z - n : số vòng quay động cơ trong một giây - z : số răng của vành răng khởi động trên bánh đà Rõ ràng khi thời gian tăng tốc càng ngắn, số vòng quay động cơ trong một giây càng tăng, dòng cảm ứng sinh ra trong mạch điện càng lớn. Xung điện sau khi qua các bộ điều biến, bộ nhớ và so sánh với xung mẫu phát ra từ máy phát xung chuẩn, được tính toán để báo trên đồng hồ chỉ thị (là các điện kế), thành hai đại lượng: số vòng quay và công suất động cơ. Giá trị vạch chia của đồng hồ chỉ thị công suất động cơ đã được xác định trước bằng các thử nghiệm trên động cơ mẫu, vì vậy thiết bị đo này chỉ áp dụng với một số loại động cơ nhất định do nhà chế tạo quy định. Về thực chất đây là phép đo theo kiểu so sánh, nên độ chính xác không cao. - Đo công suất bằng phương pháp phân tích khí xả: Về nguyên tắc: biết thành phần khí xả có thể tính được lượng nhiên liệu tham gia vào phản ứng cháy trong xy lanh, nếu xác định được hiệu suất có ích của động cơ, sẽ tính được công suất mà nó phát ra. Trên các thiết bị chẩn đoán hiện đại, sử dụng máy tính điện tử, người ta có thể xây dựng phần mềm tính toán cho phép nhập dữ liệu của động cơ trước khi đo, dùng phương pháp phân tích thành phần khí xả chung và thành phần khí xả khi ngắt từng xy lanh, sẽ xác định được công suất chung động cơ và riêng từng xy lanh cần đo. Phép đo này có những sai số do khó xác định chính xác các hệ số đầu vào của loại động cơ cần khảo nghiệm. - Đo công suất bằng áp suất có ích trung bình trong xy lanh Ngày nay những thiết bị đo hiện đại cho phép đo được một cách nhanh chóng giá trị áp suất trong xy lanh của động cơ đang làm việc và vẽ được đồ thị áp suất trong xy lanh theo góc quay trục khuỷu. Từ đó ta xác định được trị số áp suất có ích trung bình và tính được công suất động cơ theo công thức: Ne = petb.Vh.i.n/30t (kW) Với: petb Vh i n t : Áp suất có ích trung bình (MPa) : Dung tích công tác của một xi lanh (lít) : Số xi lanh trên động cơ : Số vòng quay động cơ trong 1 phút : Số kỳ của động cơ Thiết bị gồm các cảm biến đo áp suất gắn trong bu-gi hoặc trong vòi phun đã được thiết kế đặc biệt và dao động ký điện tử để vẽ đồ thị áp suất đã đo được. Kết quả đo được số hóa và đưa vào máy tính để tính toán, vẽ đồ thị, lưu trữ hoặc in ra giấy một cách nhanh chóng, thuận tiện. 2.3. Chẩn đoán động cơ theo thành phần khí xả Thành phần khí xả phản ánh tình trạng chung của động cơ về quá trình chuẩn bị và đốt cháy hỗn hợp, nó phụ thuộc vào các yếu tố như: Chất lượng của hệ thống nhiên liệu và phối khí làm ảnh hưởng tới tỉ lệ hỗn hợp và sự hoà trộn đồng đều nhiên liệu-không khí cũng như tổ chức quá trình cháy; Trạng thái nhiệt độ động cơ; Chất lượng quá trình nén trong động cơ đieden; Phẩm chất của nhiên liệu v.v.. a. Biểu hiện của khí xả: Thông thường ta có thể quan sát khí xả qua màu sắc của nó như sau: Khí thải không màu hoặc có màu nâu rất nhạt khi động cơ phát công suất tối đa chứng tỏ quá trình cháy tốt. Khí thải có màu nâu sẫm hoặc đen: Thừa nhiên liệu do hệ thống nhiên liệu hỏng (điều chỉnh sai lượng nhiên liệu cung cấp, vòi phun không sương, áp suất phun quá thấp, góc phun sớm sai...) Thiếu không khí do cản trở lớn ở đường nạp (tắc bầu lọc khí, bướm gió mở không hết...). Tuốc bin-máy nén làm việc không tốt (với động cơ tăng áp). Động cơ bị quá tải hoặc do chạy ép ga, ép số. Khí thải có màu xanh đậm: do lọt dầu nhờn vào buồng cháy khi nhóm xec măng-xi lanh không đảm bảo kín khít Khí thải màu xanh nhạt lúc có lúc không: thường do bỏ máy. Khí thải có màu trắng: máy lạnh hoặc có nước lọt vào buồng cháy. b. Phương pháp phân tích khí xả: Hiện nay thiết bị phân tích khí được sử dụng chủ yếu là loại đo nhanh, ví dụ: thiết bị dùng phổ kế hồng ngoại đo lượng CO; Dùng phương pháp quang hoá đo lượng NO, NO2 ; Thiết bị dò i-on hoá ngọn lửa để xác định thành phần HC v.v.. Để kiểm tra sự tồn tại muội than (bồ hóng) trong khí xả của động cơ đieden, thường dùng phương pháp kiểm tra độ cản quang hoặc xác định mức độ làm đen giấy lọc của luồng khí xả. Khi tiến hành phân t ... tiÕp xóc, van solenoid h, lß xo van g·y. B¬m truyÒn nhiªn liÖu h. B¬m cao ¸p h háng Pitt«ng BCA g·y. Trôc BCA g·y. Then ®Çu trôc BCA h. §øt d©y ®ai §éng c¬ bÞ bã kÑt: §éng c¬ míi ®¹i tu. ThiÕu dÇu b«i tr¬n. Lµm m¸t kh«ng tèt. 4.3. Ph¬ng ph¸p t×m pan §éng c¬ ®ang næ dõng l¹i §éng c¬ dõng tõ tõ §éng c¬ dõng ®ét ngét KiÓm tra nhiªn liÖu ®Õn BCA Quay trôc khuûu kiÓm tra Quay Kh«ng quay KiÓm tra ®éng c¬ KiÓm tra BCA KiÓm tra d©y ®ai Tèt S¬ ®å 21 Ph¬ng ph¸p t×m Pan ®éng c¬ ®ang næ dõng l¹i Tham kh¶o Nªu hiÖn tîng, ph¬ng ph¸p t×m pan: Sè 1. ®Êu sai c«ng t¾c khëi ®éng. TiÕp ®iÓm ®ång xu kh«ng dÉn ®iÖn. Sè 2. nghÑt b×nh läc nhiªn liÖu. Kªnh toµn bé xupap. ®Æt b¬m cao ¸p sai. Sè 3. hÖ thèng nhiªn liÖu lät giã. ®Æt b¬m cao ¸p sai. C«ng t¾c x«ng h. Sè 4. HÕt nhiªn liÖu hay nghÑt èng dÉn. Kªnh toµn bé xupap. NghÑt toµn bé ®êng èng n¹p. Bµi 4: Pan ®éng næ kh«ng b×nh thêng 1. §éng c¬ quay kh«ng ®Òu 1.1. HiÖn tîng §éng c¬ quay kh«ng ®Òu, m¸y bÞ rung, khãi x¶ kh«ng ®Òu, c«ng suÊt gi¶m. 1.2. Nguyªn nh©n Nhiªn liÖu cã lÉn giã hoÆc níc B¬m cao ¸p B¬m truyÒn bÞ mßn. Pitt«ng BCA mßn. Vßi phun: ¸p suÊt phun kh«ng ®Òu. Mét vµi kim phun ¸p suÊt qu¸ thÊp hoÆc kÑt më. Mét vµi kim phun ¸p suÊt qu¸ cao hoÆc kÑt ®ãng. ¸p suÊt nÐn c¸c xylanh kh«ng ®Òu Xupap kh«ng kÝn hoÆc bÞ kªnh. §Öm n¾p m¸y kh«ng kÝn, mèi ghÐp gi÷a vßi phun víi ®éng c¬ kh«ng kÝn Pitt«ng, xylanh, xÐcm¨ng mßn. 1.3. Ph¬ng ph¸p t×m pan: §éng c¬ quay kh«ng ®Òu GiÕt m¸y KiÓm tra lät giã KiÓm tra BCA KiÓm tra kªnh xupap KiÓm tra vßi phun KiÓm tra ¸p suÊt nÐn ®éng c¬ M¸y kh«ng ®Òu M¸y ®Òu Tèt Tèt Tèt S¬ ®å 22 Ph¬ng ph¸p t×m Pan ®éng c¬ quay kh«ng ®Òu 2. C«ng suÊt ®éng c¬ kh«ng ®ñ 2.1. HiÖn tîng §éng c¬ næ. C«ng suÊt ®éng c¬ kh«ng ®ñ (nhÊt lµ khi kÐo t¶i), tèc ®é ®éng c¬ gi¶m, khãi x¶ kh«ng b×nh thêng. 2.2. Nguyªn nh©n Nhiªn liÖu cung cÊp kh«ng ®ñ Nhiªn liÖu cã lÉn giã hoÆc níc. èng dÉn nhiªn liÖu bÞ bÓ, nghÑt. B×nh läc nhiªn liÖu nghÑt. B¬m truyÒn mßn. Pitt«ng BCA mßn. B¬m cao ¸p ®iÒu chØnh sai: §iÒu chØnh tèc ®é cùc ®¹i sai, lîng cung cÊp Ýt, bé ®iÒu tèc chØnh sai. Vßi phun ¸p suÊt phun kh«ng ®óng. Kim phun bÞ mßn. Chïm tia phun kÐm. Thêi ®iÓm phun kh«ng ®óng: Sím hay muén ¸p suÊt nÐn thÊp Xupap kh«ng kÝn hoÆc bÞ kªnh. §Öm n¾p m¸y kh«ng kÝn, vßi phun kh«ng kÝn. Pitt«ng, xylanh, xecm¨ng mßn. Mét vµi m¸y chÕt hoÆc yÕu Nhiªn liÖu cung cÊp kh«ng tèt hay ¸p suÊt nÐn kh«ng ®¶m b¶o. 1.3. Ph¬ng ph¸p t×m pan C«ng suÊt ®éng c¬ kh«ng ®ñ GiÕt m¸y Kh«ng ®Òu M¸y ®Òu Kiªm tra nhiªn liÖu vÒ Tèt Kh«ng tèt KiÓm tra thêi ®iÓm phun X¶ giã - KiÓm tra èng dÉn nhiªn liÖu. - B×nh läc nhiªn liÖu. KiÓm tra c¸c vßi phun KiÓm tra BCA KiÓm tra phÇn ¸p suÊt nÐn KiÓm tra m¸y chÕt hay yÕu - KiÓm tra kªnh xupap. - KiÓm tra vßi phun. - kiÓm tra phÇn ¸p suÊt nÐn Tèt Tèt Tèt Tèt S¬ ®å 23 Ph¬ng ph¸p t×m Pan c«ng suÊt ®éng c¬ kh«ng ®ñ 4. §éng c¬ bÞ nãng 4.1. Hiªn tîng Lµm viÖc nhiÖt ®é ®éng c¬ qu¸ cao, níc lµm m¸t s«i. 4.2. Nguyªn nh©n HÖ thèng lµm m¸t: ThiÕu níc. D©y ®ai láng hay qu¹t giã h. B¬m níc h háng. Bäng níc hay kÐt níc cÆn bÈn. HÖ thèng b«i tr¬n: ThiÕu nhít b«i tr¬n hay chÊt lîng kÐm. B¬m nhít mßn hay chØnh van æn ¸p sai. M¹ch nhít nghÑt. Cung cÊp nhiªn liÖu kh«ng ®óng: ThiÕu nhiªn liÖu hay thiÕu giã. Thêi ®iÓm phun qu¸ sím hay qu¸ muén. §éng c¬ bã kÑt: §éng c¬ míi söa chi tiÕt chuyÓn ®éng qu¸ khÝt hay nhiÖt ®é ®éng c¬ qu¸ cao. 4.3. Ph¬ng ph¸p t×m pan: ®éng c¬ bÞ nãng KiÓm tra HTLM KiÓm tra HTBT KiÓm tra ®éng c¬ bã kÑt KiÓm tra phÇn cung cÊp nhiªn liÖu Tèt Tèt Tèt S¬ ®å 24 Ph¬ng ph¸p t×m Pan®éng c¬ bÞ nãng 5. §éng c¬ bÞ déng 5.1. HiÖn tîng §éng c¬ næ cã tiÕng déng nhÊt lµ khi t¨ng ga. 5.2. Nguyªn nh©n Thêi ®iÓm phun qu¸ sím. ¸p suÊt phun cao. Buång ®èt nhiÒu muéi than. T×nh tr¹ng kü thuËt ®éng c¬ kh«ng tèt: Khe hë pitt«ng - xylanh lín, chèt pitt«ng mßn, cæ trôc hay cæ biªn mßn. 5.3. Ph¬ng ph¸p t×m pan §éng c¬ bÞ déng KiÓm tra thêi ®iÓm phun KiÓm tra c¸c vßi phun KiÓm tra vßi phun Nghe tiÕng gâ chÈn ®o¸n h háng C¸c xylanh Mét vµi xylanh Tèt Tèt S¬ ®å 25 Ph¬ng ph¸p t×m Pan®éng c¬ bÞ déng Tham kh¶o H·y nªu hiÖn tîng, ph¬ng ph¸p t×m pan khi ®éng c¬ bÞ c¸c pan sau: Sè 01. ®Æt b¬m cao ¸p muén (næ ®îc). nghÑt mét phÇn ®êng èng nap. Kªnh xupap x¶ m¸y 2. ¸p suÊt phun m¸y 2 qu¸ cao. Sè 2 . §Æt b¬m sím (næ ®îc). ¸p suÊt c¸c vßi phun cao. Kªnh xupap x¶ m¸y 3. Bµi 5: Pan ®éng næ khãi x¶ kh«ng b×nh thêng 1. Khãi x¶ mµu ®en hoÆc x¸m sËm 1.1. HiÖn tîng §éng c¬ næ khãi x¶ cã mµu ®en hoÆc x¸m sËm, ®éng c¬ kÐo kháe hay kh«ng kháe. NhÊt lµ khi t¨ng ga. 1.2. Nguyªn nh©n: Do nhiªn liÖu ChÊt lîng nhiªn liÖu kÐm. Vßi phun: ¸p suÊt phun thÊp, nhiªn liÖu phun kh«ng s¬ng, bÞ nhá giät. Thêi ®iÓm phun muén. B¬m cao ¸p: ®iÒu chØnh d nhiªn liÖu, bé ®iÒu tèc chØnh sai. ThiÕu kh«ng khÝ B×nh läc giã nghÑt. §êng èng n¹p bÞ nghÑt mét phÇn. §êng èng x¶ bÞ nghÑt mét phÇn. Xupap më nhá: chØnh khe hë nhiÖt sai, ®òa cong, cam xupap mßn. B¬m giã (turbo) h hay ®iÒu chØnh sai. PhÇn ®éng c¬ §éng c¬ bÞ qu¸ t¶i. ¸p suÊt nÐn thÊp: Pitt«ng-xecm¨ng-xylanh mßn, xupap kh«ng kÝn, ®Öm n¾p m¸y kh«ng kÝn. 1.3. Ph¬ng ph¸p t×m pan: §éng c¬ næ khãi x¶ cã mµu ®en hoÆc x¸m sËm. T¨ng ga cã hai trêng hîp x¶y ra: Trêng hîp 1 C«ng suÊt ®éng c¬ lín ( §éng c¬ kÐo kháe) KiÓm tra vÝt ®iÒu chØnh tèc ®é cùc ®¹i §iÒu chØnh l¹i tèc ®é cùc ®¹i KiÓm tra ®iÒu chØnh BCA: - Bé ®iÒu tèc. - Lîng nhiªn liÖu cung cÊp Tèt Kh«ng tèt S¬ ®å 26 Ph¬ng ph¸p t×m Pan®éng c¬ khãi x¶ mµu ®en hoÆc x¸m sËm Trêng hîp 2 C«ng suÊt ®éng c¬ gi¶m Quan s¸t khãi - KiÓm tra b×nh läc giã. - KiÓm tra b¬m giã. - KiÓm tra ®êng èng n¹p. - KiÓm tra èng x¶. KiÓm tra chÊt lîng nhiªn liÖu KiÓm tra thêi ®iÓm phun KiÓm tra ¸p suÊt nÐn GiÕt m¸y KiÓm tra ¸p suÊt phun KiÓm tra xupap, ®òa ®Èy KiÓm tra èng n¹p, èng x¶ m¸y yÕu KiÓm tra chÊt lîng vßi phun Khãi ®en ®Òu Khãi ®en kh«ng ®Òu YÕu M¹nh Tèt Tèt Tèt Tèt S¬ ®å 27 Ph¬ng ph¸p t×m Pan c«ng suÊt ®éng c¬ gi¶m Chó ý: Khãi x¶ kh«ng ®Òu. GiÕt m¸y thÊy m¸y m¹nh hay yÕu, khãi ®en gi¶m hoÆc mÊt, h háng thuéc m¸y (xylanh) ®ã. ¸p suÊt phun thÊp Ýt m¸y m¹nh, nÕu qu¸ thÊp m¸y yÕu 2. Khãi x¶ mµu tr¾ng 2.1. HiÖn tîng: §éng c¬ næ khãi x¶ mµu tr¾ng ®Òu hoÆc kh«ng ®Òu. C«ng suÊt ®éng c¬ gi¶m. 2.2. Nguyªn nh©n Nhiªn liÖu cã lÉn giã hoÆc níc Thêi ®iÓm phun sím hoÆc muén nhiÒu Cã mét vµi m¸y (xylanh) chÕt ¸p suÊt phun qu¸ thÊp, kim phun kÑt më, chÊt lîng phun qu¸ kÐm. ¸p suÊt nÐn qu¸ thÊp: Xupap bÞ kªnh hay kh«ng kÝn, ®Öm n¾p m¸y hay vßi phun kh«ng kÝn, pitt«ng-xylanh-xecm¨ng mßn, t¾c cöa n¹p, xupap më nhá hay kh«ng më. §éng c¬ ch¹y kh«ng t¶i qu¸ l©u 2.3. Ph¬ng ph¸p t×m pan M¸y chÕt hay yÕu Khãi x¶ mµu tr¾ng Tr¾ng ®Òu Tr¾ng kh«ng ®Òu KiÓm tra nhiªn liÖu KiÓm tra thêi ®iÓm phun GiÕt m¸y KiÓm tra xupap kªnh hay kh«ng më KiÓm tra vßi phun Tèt Tèt KiÓm tra t¾c cöa n¹p Tèt KiÓm tra t¾c èng n¹p KiÓm tra ¸p suÊt nÐn t×m h háng Tèt Tèt S¬ ®å 28 Ph¬ng ph¸p t×m Pan®éng c¬ Khãi x¶ mµu tr¾ng Chó ý: Trêng hîp khãi tr¾ng kh«ng ®Òu khi giÕt m¸y thÊy m¸y chÕt hoÆc yÕu ®ång thêi thÊy khãi tr¾ng mÊt hoÆc gi¶m. Trêng hîp gi¶m cã thÓ pan ë nhiÒu m¸y. 3. Khãi x¶ mµu xanh 3.1. HiÖn tîng §éng c¬ næ khãi x¶ mµu xanh ®Òu hoÆc kh«ng ®Òu. C«ng suÊt ®éng c¬ kh«ng gi¶m hoÆc gi¶m. 3.2. Nguyªn nh©n Do nhít b«i tr¬n vµo buång ®èt: Pitt«ng-xylanh-xecm¨ng mßn, hay bÞ trÇy, xecm¨ng bÞ bã kÑt. Mùc nhít qu¸ cao. Nhít trong läc giã qu¸ nhiÒu (lo¹i läc ít). èng dÉn híng xupap mßn hoÆc phèt nhít h. §éng c¬ ch¹y kh«ng t¶i qu¸ l©u. 3.3. Ph¬ng ph¸p t×m pan Khãi x¶ mµu xanh KiÓm tra mùc nhít cat-te KiÓm tra ¸p suÊt nÐn t×m h háng nguyªn nh©n (a) KiÓm tra mùc nhít läc giã C«ng suÊt gi¶m C«ng suÊt kh«ng gi¶m Tèt Tèt KiÓm tra nguyªn nh©n (d) S¬ ®å 29 Ph¬ng ph¸p t×m Pan®éng c¬ Khãi x¶ mµu xanh Chó ý Khãi x¶ mµu xanh kh«ng ®Òu. Cã thÓ h háng ë mét vµi xylanh bÞ nhít lªn buång ®èt. Khãi xanh do ch¹y kh«ng t¶i l©u. cho ®éng c¬ ho¹t ®éng tèc ®é cao mét lóc sÏ hÕt. Bµi 6: kiÓm tra ¸p suÊt nÐn (compression) Sö dông ®ång hå kiÓm tra ¸p suÊt nÐn (compression-meter) ®o ¸p suÊt nÐn trong buång ®èt. §©y lµ lo¹i ®ång hå chuyªn dïng cã gi¸ trÞ ®o tèi ®a 17kg/cm2 hoÆc 250psi, trong ®ång hå cã van ®Ó gi÷ ¸p suÊt nÐn ®o ®îc trong buång ®èt. ®ång hå ®îc nèi víi ®Çu cã nóm cao su l¾p vµo læ vßi phun. H×nh 37. §o ¸p suÊt nÐn ViÖc ®o ¸p suÊt nÐn ta cã thÓ x¸c ®Þnh ®îc c¸c h háng lµm ¶nh hëng ®Õn ¸p suÊt nÐn nh: Pitt«ng-xylanh-xecm¨ng bÞ mßn, xupap kh«ng kÝn, ®Öm n¾p m¸y kh«ng kÝn. ViÖc ®o ¸p suÊt nÐn thùc hiªn nh sau: 1. §iÒu kiÖn vµ chuÈn bÞ tríc khi kiÓm tra 1.1. §iÒu kiÖn Nhít b«i tr¬n ph¶i ®óng mùc vµ ®¶m b¶o chÊt lîng. NhiÖt ®é ®éng c¬ ®óng quy ®Þnh (800C-900C). Accu ph¶i ®ñ dung lîng. 1.2. ChuÈn bÞ Th¸o b×nh läc giã. Th¸o tÊt c¶ c¸c vßi phun. Më d©y ®iÖn ®Õn van t¾c m¸y (van solenoid). L¾p ®Çu ®o vµ ®ång hå vµo læ vßi phun cña xylanh cÇn kiÓm tra. 1.3. Ph¬ng ph¸p kiÓm tra Khëi ®éng ®éng c¬ trôc khuûu quay, xylanh thùc hiÖn 4 ®Õn 5 lÇn nÐn. Quan s¸t t¨ng ¸p suÊt trªn ®ång hå. Ghi l¹i gi¸ trÞ ¸p suÊt trªn ®ång hå P1.(§Ó chÝnh x¸c ta cã thÓ ®o 2-3 lÇn). So s¸nh P1 víi ¸p suÊt nÐn quy ®Þnh P cña nhµ chÕ t¹o. P1 < P (quy ®Þnh) kho¶ng 1 kg/cm2 hay 14 psi ta cÇn kiÓm tra l¹i. Cho mét Ýt dÇu nhít vµo lç vßi phun (10CC-15CC ), chê vµi phót. Khëi ®éng ®éng c¬ kiÓm tra l¹i nh trªn, ghi gi¸ trÞ P1. ¸p suÊt nÐn tïy theo sè liÖu tõng ®éng c¬, nÕu kh«ng biÕt ta dùa vµo tû sè nÐn theo b¶ng: 1.4. B¶ng ¸p suÊt nÐn quy ®Þnh theo tû sè nÐn: Tû sè nÐn ¸p suÊt nÐn (psi) ¸p suÊt nÐn (kg/cm2) 6/1 100 7,1 7/1 120 8,4 8/1 140 10,0 9/1 160 11,5 10/1 180 12,7 11/1 200 14,2 2. ChÈn ®o¸n t×nh tr¹ng kü thuËt ®éng c¬ NÕu P1 kh«ng thÊp h¬n P (quy ®Þnh) t×nh tr¹ng kü thuËt cßn tèt. NÕu P1 > P (quy ®Þnh) buång ®èt ®ãng nhiÒu mô«i than. NÕu P1 < P (quy ®Þnh) pitt«ng-xylanh-xecm¨ng mßn. CÇn biÕt: Ngêi ta cã thÓ kiÓm tra ¸p suÊt nÐn theo kinh nghiÖm ®Ó chÈn ®o¸n t×nh trang kü thuËt cñ ®éng c¬ khi kh«ng cã thiÕt bÞ kiÓm tra. Theo dâi lóc khëi ®éng, ho¹t ®éng cña ®éng vµ quan s¸t khãi x¶ theo ph¬ng ph¸p t×m pap, ChÈn ®o¸n lµ ®éng c¬ thiÕu ¸p suÊt nÐn, ta thùc hiÖn: Cho nhít vµo xylanh (qua èng n¹p) nÕu dÓ khëi ®éng, c«ng suÊt t¨ng hay m¸y (xylanh) m¹nh h¬n, do pit«ng-xylanh-xecm¨ng mßn. NÕu vÉn b×nh thêng do xupap hay ®Öm n¾p m¸y kh«ng kÝn. Quan s¸t thÊy h¬i tho¸t ra nhiÒu ë lç ch©m nhít do pit«ng-xylanh-xecm¨ng mßn Quan s¸t bªn ngoµi ®Öm n¾p m¸y, trong kÐt lµm m¸t níc thÊy cã thæi h¬i hay nhít lÉn trong níc do ®Öm n¾p m¸y kh«ng kÝn. Bµi tËp 7: Nghe tiÕng gâ cña ®éng c¬ §«ng c¬ lµm viÖc th«ng thêng ph¸t ra hai lo¹i tiÕng kªu: TiÕng kªu khÝ ®éng häc ph¸t ra ë ®êng èng n¹p trong qu¸ tr×nh nap, trong xylanh (kÝch næ) qu¸ tr×nh ch¸y, qu¸ tr×nh th¶i khÝ th¶i ra khái èng th¶i. TiÕng kªu c¬ giíi (tiÕng gâ) do sù va ®Ëp gi÷ c¸c chi tiÕt chuyÓn ®éng trong c¬ cÊu ®éng vµ c¬ cÊu ph©n phèi khÝ. B×nh thêng tiÕng gâ nhÑ, khi c¸c chi tiÕt mßn tiÕng gâ ph¸t ra lín g©y tiÕng ån khi ®éng c¬ ho¹t ®éng, cã nh÷ng h háng nguy c¬ lµm ph¸ huû c¸c chi tiÕt, c«ng suÊt gi¶m, hao nhiªn liÖu. §Ô x¸c ®Þnh tiÕng gâ ph¸t ra do ®©u, tõ xylanh nµo yªu cÇu ph¶i cã nhiÒu kinh nghiÖm vµ rÌn luyÖn l©u dµi. Tuy nhiªn ®Ó x¸c ®Þnh t¬ng ®èi chÝch x¸c tiÕng gâ ph¸t ra tõ chi tiÕt nµo ta cã thÓ sö dông èng nghe chuyªn dïng hoÆc tua vÝt ¸p vµo tai ®Ó nghe, ®ång thêi kÕt hîp víi c¸c hiÖn tîng pan ë trªn. H×nh 38. Dông cô nghe tiÕng gâ 5 1 2 3 4 6 3 7 H×nh 39. Vïng nghe tiÕng gâ B¶ng ®Æc trng cho c¸c tiÕng gâ, vÞ trÝ nghe nh sau: B¶ng ®Æc trng tiÕng gâ Nguyªn nh©n ph¸t ra tiÕng gâ NhiÖt ®é ®éng c¬ Tèc ®é ®éng c¬ Vïng nghe §Æc trng tiÕng gâ Xö lý HËu qu¶ (1) (2) (3) (4) (5) (6) (7) B¹c lãt cæ trôc Nãng Lªn xuèng ga 5 NÆng nÒ, trÇm cã chu kú. Khi giÕt 2 m¸y hai bªn cæ trôc tiÕng gâ gi¶m (rÇm rÇm) - NhÑ chê kª ho¹ch söa ch÷a. NÆng tiÕn hµnh söa ch÷a. Ch¸y ho¨c trãc b¹c cæ trôc, trÇy xít cæ tôc B¹c lãt cæ biªn Nãng Lªn xuèng ga 4 Ng¾n, trÇm, cã chu kú. Khi giÕt m¸y tiÕng gâ gi¶m (cäc cäc) - NhÑ chê kª ho¹ch söa ch÷a. - NÆng tiÕn hµnh söa ch÷a. Ch¸y ho¨c trãc b¹c biªn , trÇy xít cæ biªn Pitt«ng vµ xylanh Nguéi Tèc ®é thÊp 3 TiÕng gâ gißn, thanh, gi¶m dÇn khi m¸y nãng. GiÕt m¸y tiÕng gâ gi¶m (r¾c r¾c) - NhÑ chê kª ho¹ch söa ch÷a. - NÆng tiÕn hµnh söa ch÷a - Hao nhiªn liÖu, nhít b«I tr¬n. - BÓ th©n pitt«ng. Chèt pitt«ng Nguéi T¨ng ga 3 TiÕng gâ ®anh râ, gi¶m ®I khi giÕt m¸y (l¸ch t¸ch) - NhÑ chê kª ho¹ch söa ch÷a. - NÆng tiÕn hµnh söa ch÷a. Lµm chèt vµ cµ mßn nhanh xÐcm¨ng Nguéi CÇm chõng 3 NhÑ khã nghe Chê kÕ ho¹ch söa ch÷a Mß r·nh xecm¨ng B¶ng ®Æc trng tiÕng gâ (1) (2) (3) (4) (5) (6) (7) Khe hë xupap Nguéi CÇm chõng 1 NhÑ, râ ®Òu t¨ng ga lÉn lén khã nghe (l¸ch t¸ch) §iÒu chØnh l¹i §u«i xupap vµ cß mæ mßn nhanh, mÊt c«ng suÊt Con ®éi víi èng dÉn híng Nguéi CÇm chõng L¾p con ®éi Nh tiÕng gâ xupap Chê kÕ ho¹ch söa ch÷a Con ®éi mßn nhanh Gèi ®ì trôc cam Nãng CÇm chõng L¾p trôc cam NhÑ trÇm khã biÕt - NhÑ chê kª ho¹ch söa ch÷a. NÆng tiÕn hµnh söa ch÷a. Gi¶m ¸p suÊt nhít b«i tr¬n B¸nh r¨ng hoÆc sªn cam Nãng Lªn xuèng ga 6 TiÕng rÝt hó dÓ ph¸t hiÖn Chê kÕ ho¹ch söa ch÷a B¸nh r¨ng hoÆc nh«ng sªn mßn nhanh B¸nh ®µ lâng Mäi nhiÖt ®é Lªn xuèng ga 7 TiÕng gâ rÊt lín, rÊt trÇm (rÇm rÇm) SiÕt l¹i bu-l«ng b¸nh ®µ G·y bu-l«ng b¸nh ®µ ly hîp bÞ trît Næ däng (kÝch næ) Nãng T¨ng ga 2 TiÕng gâ rÊt ®anh (l¸ch t¸ch) chØnh gãc ®¸nh löa hay gãc phun. c¹o muéi than. Cong thang truyÒn, bÓ pitt«ng. - Gi¶m c«ng suÊt. Môc lôc Néi dung Trang Lêi nãi ®Çu 0 A- Lý thuyÕt chÈn ®o¸n tr¹ng th¸i kü thuËt ®éng c¬ 1 1. Các vấn đề chung 1 2. Các phương pháp chẩn đoán động cơ 4 B - ChÈn ®o¸n tr¹ng th¸i kü thuËt vµ xö lý pan ®éng c¬ x¨ng 16 1. §¨c tÝnh kü thuËt cña mét sè lo¹i ®éng c¬ X¨ng 16 Bµi tËp 1: VËn hµnh vµ ®iÒu chØnh chÕ ®é kh«ng t¶i 19 Bµi tËp 2: §Æt löa cho ®éng c¬ x¨ng 23 Bµi tËp 3: Pan hÖ thèng ®¸nh löa 26 Bµi tËp 4: Pan hÖ thèng nhiªn liÖu x¨ng 37 Bµi tËp 5: Pan tæng hîp ®éng c¬ x¨ng 54 C - ChÈn ®o¸n tr¹ng th¸i kü thuËt vµ xö lý pan ®éng c¬ §iezen 64 1. §¨c tÝnh kü thuËt cña mét sè lo¹i ®éng c¬ §iezen 64 Bµi tËp 1: VËn hµnh ®éng c¬ §iezen 67 Bµi tËp 2: C©n chØnh kim phun, c©n chØnh vµ ®Æt b¬m cao ¸p 69 Bµi tËp 3: Pan ®éng c¬ kh«ng næ ®îc 80 Bµi tËp 4: Pan ®éng c¬ næ kh«ng b×nh thêng 87 Bµi tËp 5: Pan ®«ng c¬ næ khãi x¶ kh«ng b×nh thêng 92 Bµi tËp 6: KiÓm tra ¸p suÊt nÐn 97 Bµi tËp 7: Nghe tiÕng gâ cña ®éng c¬ 100 Tµi liÖu tham kh¶o Ngô Thành Bắc – Nguyễn Đức Phú – Chẩn đoán trạng thái kỹ thuật của ôtô – NXB khoa học và kỹ thuật - 1986 Phạm Minh Tuấn - Động cơ đốt trong - NXB khoa học và kỹ thuật - 1999 V.X. Kalixki, A.L. Mandôn, G.E. mNagula - Ô tô - NXB công nhân kỹ thuật - Hà Nội 1982 Đinh Ngọc Ân-Khai thác kỹ thuật các kết cấu mới của ô tô Nhật Bản-NXB khoa học và kỹ thuật-Hà Nội 1995 Trần Văn Tế - Động lực học và dao động của động cơ đốt trong - Trường ĐH Bách khoa Hà Nội - 1997 Lê Viết Lượng – Lý Thuyết động cơ ĐIEZEN – NXBGD – 2004 Nguyễn Tấn Tiến – Nguyên lý động cơ đốt trong – NXBGD – 2004 Nguyễn Thế Đạt – Giáo trình an toàn lao động – NXBGD - 2004
File đính kèm:
giao_trinh_chuan_doan_dong_co.doc