Bài giảng môn Cơ khí đại cương
Khái niệm về sản phẩm, chi tiết máy, phôi, cơ cấu máy:
Sản phẩm cơ khí: vật phẩm cuối cùng của một quá trình sản xuất.
VD: bánh răng, máy khoan, đai ốc,
Chi tiết máy: là đơn vị nhỏ nhất và hoàn chỉnh về mặt kỹ thuật
của máy. VD: bulong, cam,
Phôi: là vật phẩm ban đầu của một công đoạn sản xuất. VD: phôi
đúc, phôi rèn,
Bộ phận máy: gồm nhiều chi tiết máy liên kết với nhau. VD: hộp
tốc độ, bàn xe dao,
Cơ cấu máy: là một phần của máy hoặc bộ phận máy có chức
năng nhất định. VD: bánh vít- trục vít, bánh răng thanh răng,
Quá trình thiết kế, sản xuất và quá trình công nghệ
Quá trình thiết kế: phát thảo, tính toán, thiết kế ra một sản phẩm.
Quá trình sản xuất: tác động vào tài nguyên thiên nhiên biến
thành sản phẩm phục vụ con người.
Quá trình công nghệ: trực tiếp làm thay đổi trạng thái và tính chất
của đối tượng sản xuất.
Quy trình công nghệ: là văn kiện công nghệ ghi lại quá trình công
nghệ cụ thể.
Tóm tắt nội dung tài liệu: Bài giảng môn Cơ khí đại cương
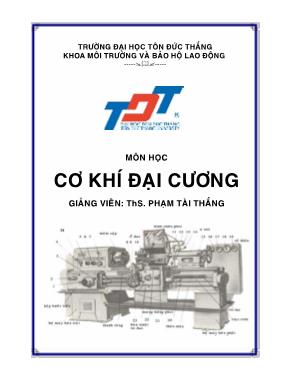
TRƯỜNG ĐẠI HỌC TÔN ĐỨC THẮNG KHOA MÔI TRƯỜNG VÀ BẢO HỘ LAO ĐỘNG -----# "----- MÔN HỌC CƠ KHÍ ĐẠI CƯƠNG GIẢNG VIÊN: ThS. PHẠM TÀI THẮNG 4/17/2010 1 TRƯỜNG ĐẠI HỌC TÔN ĐỨC THẮNG KHOA MÔI TRƯỜNG BHLĐ Ơ ĐẠ ƢƠ Tài liệu tham khảo Giới thiệu Đánh giá môn học Nội dung giảng dạy 2 GiỚI THIỆU Mơn học Cơ khí đại cương dùng để giảng dạy cho sinh viên hệ đại học ngành Bảo hộ lao động nhằm cung cấp kiến thức cơ bản về: Quá trình sản xuất cơ khí Chi tiết máy và cơ cấu máy điển hình Chất lượng bề mặt và độ chính xác gia cơng Các cơng nghệ gia cơng cắt gọt kim loại 3 TÀI LIỆU THAM KHẢO 1. Cơ khí đại cương. Hồng Tùng-Nguyễn Tiến Đào, NXB KHKT, 2006 2. Dung sai lắp ghép và kỹ thuật đo lường. Ninh Đức Tốn- Xuân Bảy, NXB GD 3. Máy cắt kim loại. Trường CĐKT Cao Thắng, 2000 4. Cơ khí đại cương. ĐH Đà Nẵng, 2002 4 ĐÁNH GIÁ MÔN HỌC Điểm thứ 1 (10%): Bài tập Điểm thứ 3 (70%): Kiểm tra cuối kỳ Điểm thứ 2 (20%): Kiểm tra giữa kỳ 4/17/2010 2 5 1.1. Khái niệm về sản phẩm, chi tiết máy, phôi, cơ cấu máy CHƯƠNG 1: MỘT SỐ KHÁI NIỆM CƠ BẢN VỀ SẢN XUẤT CƠ KHÍ 1.2. Quá trình thiết kế, sản xuất và quá trình công nghệ 1.3. Các thành phần của quá trình công nghệ 1.4. Các dạng sản xuất và hình thức tổ chức sản xuất 1.5. Các phương pháp gia công 6 1.1. Khái niệm về sản phẩm, chi tiết máy, phôi, cơ cấu máy: Sản phẩm cơ khí: vật phẩm cuối cùng của một quá trình sản xuất. VD: bánh răng, máy khoan, đai ốc, Chi tiết máy: là đơn vị nhỏ nhất và hoàn chỉnh về mặt kỹ thuật của máy. VD: bulong, cam, Phôi: là vật phẩm ban đầu của một công đoạn sản xuất. VD: phôi đúc, phôi rèn, Bộ phận máy: gồm nhiều chi tiết máy liên kết với nhau. VD: hộp tốc độ, bàn xe dao, Cơ cấu máy: là một phần của máy hoặc bộ phận máy có chức năng nhất định. VD: bánh vít- trục vít, bánh răng thanh răng, 7 1.2. Quá trình thiết kế, sản xuất và quá trình công nghệ Quá trình thiết kế: phát thảo, tính toán, thiết kế ra một sản phẩm. Quá trình sản xuất: tác động vào tài nguyên thiên nhiên biến thành sản phẩm phục vụ con người. Quá trình công nghệ: trực tiếp làm thay đổi trạng thái và tính chất của đối tượng sản xuất. Quy trình công nghệ: là văn kiện công nghệ ghi lại quá trình công nghệ cụ thể. 8 1.3. Các thành phần của quá trình công nghệ 1.3.1. Nguyên công: là một phần của quá trình công nghệ được hoàn thành liên tục, tại một chỗ làm việc và do một hay một nhóm công nhân cùng thực hiện 1.3.2. Gá: là một phần của nguyên công được hoàn thành trong một lần gá đặt chi tiết 1.3.3. Vị trí: là một phần của nguyên công, được xác định bởi vị trí tương quan giữa chi tiết với máy hoặc giữa chi tiết với dụng cụ cắt 1.3.4. Bước: là một phần của nguyên công được đặc trưng bởi bề mặt, dao hoặc chế độ cắt 1.3.5. Đường chuyển dao: là một phần của bước để hớt đi một lớp kim loại, sử dụng cùng một dao và một chế độ cắt. 1.3.6. Động tác: là một hành động của người công nhân để điều khiển máy thực hiện việc gia công hay lắp ráp. 4/17/2010 3 9 1.4. Các dạng sản xuất và hình thức tổ chức sản xuất 1.4.1. Các dạng sản xuất: tùy theo sản lượng hàng năm và mức độ ổn định của sản phẩm mà người ta chia ra 3 dạng sản xuất: đơn chiếc, hàng loạt và hàng khối 1.4.2. Các hình thức tổ chức sản xuất: theo dây chuyền và không theo dây chuyền 10 1.5. Các phương pháp gia công 1.5.1. Phương pháp gia công cắt gọt (gia công có phoi): - Là phương pháp gia công dùng dụng cụ cắt để hớt đi 1 lớp vật liệu trên bề mặt chi tiết gia công 1.5.2. Phương pháp gia công không cắt gọt (gia công không phoi): - Là phương pháp gia công dùng dụng cụ để làm biến dạng dẻo lớp bề mặt chi tiết gia công ở trạng thái nguội hoặc nung nóng 1.5.3. Phương pháp gia công bằng điện lý và điện hóa: - Là phương pháp gia công đặc biệt để gia công các loại vật liệu có độ cứng cao, bề mặt phức tạp, kích thước nhỏ, 11 2.1. Khái niệm về chất lượng bề mặt của sản phẩm CHƯƠNG 2: CHẤT LƯỢNG BỀ MẶT VÀ ĐỘ CHÍNH XÁC GIA CÔNG CƠ KHÍ 2.2. Độ chính xác gia cơng cơ khí 2.2.1. Khái niệm về tính lắp lẫn trong ngành cơ khí 2.2.2. Khái niệm về kích thƣớc, dung sai, sai lệch giới hạn 2.2.3. Lắp ghép (khái niệm và phân loại) 2.2.4. Dung sai lắp ghép các bề mặt trơn 2.2.5. Dung sai hình dạng, dung sai vị trí và nhám bề mặt 12 2.1. Khái niệm về chất lượng bề mặt của sản phẩm: 2.1.1.1. Độ nhấp nhơ tế vi: 2.1.1. Các yếu tố đặc trƣng: Sai lệch trung bình số học Ra (m): n i i n L a y nn yyy dxxy L R 1 21 0 1... .)( 1 Chiều cao mấp mơ trung trình Rz (m): 5 )...()...( 1042931 hhhhhh Rz 4/17/2010 4 13 2.1.1.2. Độ sóng bề mặt: là chu kỳ không bằng phẳng của bề mặt chi tiết máy được quan sát trong phạm vi lớn hơn độ nhám bề mặt. 2.1.1.3. Tính chất cơ lý của lớp bề mặt: bao gồm lớp biến cứng bề mặt và ứng suất dư bề mặt. 14 2.1.2.1. Aûnh hưởng đến tính chống mòn: 2.1.2. Aûnh hưởng chất lượng bề mặt tới khả năng làm việc của chi tiết máy: => Aûnh hưởng đến độ chính xác của mối lắp - Độ nhám bề mặt càng lớn chi tiết mòn càng nhanh 2.1.2.2. Aûnh hưởng đến độ bền mỏi của chi tiết : - Độ nhám bề mặt càng lớn, chi tiết dễ phá hủy do mỏi 2.1.2.3. Aûnh hưởng đến tính chống ăn mòn hóa học của lớp bề mặt chi tiết: - Độ nhám bề mặt càng lớn, khả năng ăn mòn kim loại càng cao 15 2.2. Độ chính xác gia cơng cơ khí : - Là khả năng các chi tiết cĩ thể thay thế cho nhau mà khơng cần lựa chọn hay sửa chữa thêm vẫn đảm bảo yêu cầu kĩ thuật của mối ghép. 2.2.1. Khái niệm về tính lắp lẫn trong ngành cơ khí : 2.2.2. Khái niệm về kích thƣớc, dung sai, sai lệch giới hạn: 2.2.2.1. Kích thƣớc danh nghĩa: - Kích thước danh nghĩa là kích thước đã được tính tốn. Sau đĩ, quy trịn theo các giá trị cho trong dãy kích thước tiêu chuẩn - Ký hiệu: Kích thước danh nghĩa của trục là dN Kích thước danh nghĩa của lỗ là DN 16 2.2.2.2. Kích thƣớc thực: - Kích thước thực là kích thước kích đo trực tiếp trên chi tiết gia cơng bằng những dụng cụ đo - Ký hiệu: Kích thước thực của trục là: dt Kích thước thực của lỗ là: Dt 2.2.2.3. Kích thƣớc giới hạn: - Kích thước giới hạn là kích thước lớn nhất và nhỏ nhất mà kích thước thực của chi tiết đạt yêu cầu nằm trong phạm vi đĩ - Ký hiệu: + Kích thước giới hạn lớn nhất dmax , Dmax + Kích thước giới hạn nhỏ nhất dmin , Dmin 4/17/2010 5 17 2.2.2.4. Dung sai: - Dung sai là hiệu số giữa kích thước giới hạn lớn nhất và kích thước giới hạn nhỏ nhất. - Ký hiệu: Dung sai chi tiết trục : Td Dung sai chi tiết lỗ : TD 2.2.2.5. Các sai lệch giới hạn: - Sai lệch trên: là hiệu đại số giữa kích thước giới hạn lớn nhất và kích thước danh nghĩa - Ký hiệu: Sai lệch trên es, ES - Sai lệch dưới: là hiệu đại số giữa kích thước giới hạn nhỏ nhất với kích thước danh nghĩa - Ký hiệu: Sai lệch dưới ei, EI 18 2.2.3. Lắp ghép (khái niệm và phân loại): 2.2.3.1. Khái niệm: - Lắp ghép: là sự phối hợp các chi tiết một cách cố định (như bulơng gắn vào đai ốc) hoặc phối hợp di động (như trục quay trong ổ, sự chuyển động của vít me, đai ốc trong máy tiện) để tạo thành một mối ghép. 2.2.3.2. Phân loại: a. Lắp ghép cĩ độ hở (lắp lỏng): - Là mối ghép cĩ kích thước của trục luơn luơn nhỏ hơn kích thước của lỗ - Kí hiệu: + Độ hở lớn nhất : S max + Độ hở nhỏ nhất : S min + Dung sai lắp ghép : T S 19 b. Lắp ghép cĩ độ dơi (lắp chặt): - Là mối ghép cĩ kích thước của lỗ luơn luơn nhỏ hơn kích thước của trục. - Ký hiệu: + Độ dơi lớn nhất : Nmax + Độ dơi nhỏ nhất : Nmin + Dung sai lắp ghép : TN c. Lắp ghép trung gian: - Là mối ghép mà tuỳ theo kích thước của trục và lỗ mà mối ghép cĩ độ hở hoặc độ dơi . - Ký hiệu: + Độ hở lớn nhất : Smax + Độ dơi lớn nhất : Nmax + Dung sai lắp ghép : TS,N 20 2.2.3.3. Biểu diễn sơ đồ phân bố miền dung sai lắp ghép: - Trục tung: biểu thị giá trị các sai lệch giới hạn, tính bằng micromet 1m (10-3 mm) - Trục hồnh (đường 0): biểu thị vị trí KTDN, tại đây các sai lệch giới hạn bằng 0 4/17/2010 6 21 2.2.4. Dung sai lắp ghép các bề mặt trơn: 2.2.4.1. Hệ thống dung sai: - Cơng thức dung sai: T = a.i i - đơn vị dung sai a - hệ số phụ thuộc vào mức độ chính xác của kích thước. 2.2.4.2. Hệ thống lắp ghép: a. Hệ thống lỗ cơ bản: lỗ cơ bản cĩ sai lệch cơ bản là H với: + Sai lệch dưới EI = 0 + Sai lệch trên ES = + TD b. Hệ thống trục cơ bản: trục cơ bản cĩ sai lệch cơ bản là h với : + Sai lệch trên es = 0 + Sai lệch dưới ei = - Td 22 c. Sai lệch cơ bản: xác định vị trí của miền dung sai so với kích thước danh nghĩa. Cĩ 2 trường hợp: + SLCB là sai lệch dưới (ei, EI) + SLCB là sai lệch trên (es, ES) Đối với lỗ : sai lệch cơ bản lần lượt được ký hiệu bằng các mẫu tự viết hoa là A, B, C, CD, E, EF, G, H, J(JS), K, M, N, P, R, T, U, V, X, Y ,Z, ZA, ZB, ZC. Đối với trục : sai lệch cơ bản lần lượt được ký hiệu bằng các mẫu tự viết thường là a, b, c, cd, d, e, ef, f, g, h, j(js), k, m, n, p, r, s, t, u, v, y, z, za, zb, zc. 23 d. Ký hiệu qui ước của kích thước và lắp ghép: - Ký hiệu của kích thước: KTDN + chữ cái sai lệch cơ bản + cấp chính xác - Ký hiệu lắp ghép: KTDN của mối ghép + ký hiệu miền dung sai của lỗ + ký hiệu miền dung sai trục 24 e. Lắp ghép tiêu chuẩn: 3 nhĩm + Nhĩm lắp lỏng gồm các kiểu lắp: , a H , h A ,... h H , h B + Nhĩm lắp trung gian gồm các kiểu lắp: , sj H , m H , k H , h J S , h M , h K , n H h N ,... b H + Nhĩm lắp chặt gồm các kiểu lắp: , p H zc H , h P h ZC ,... h R ,... r H 4/17/2010 7 25 2.2.5. Dung sai hình dạng, dung sai vị trí và nhám bề mặt: 2.2.5.1. Sai lệch, dung sai hình dạng của các bề mặt: a. Sai lệch hình dạng: được tính bằng khoảng cách lớn nhất từ các điểm của profin thực tới profin áp theo phương vuơng gĩc với bề mặt áp. Ký hiệu: - Bao gồm: Sai lệch độ tròn, profin mặt cắt dọc, đđộ trụ, độ phẳng, b. Dung sai hình dạng: giá trị cho phép lớn nhất của sai lệch hình dạng. Ký hiệu: T 2.2.5.2. Sai lệch, dung sai vị trí của các bề mặt: a. Sai lệch vị trí: là sai lệch giữa vị trí thực của các bề mặt, các đường trục hoặc các mặt phẳng đối xứng với chuẩn. Kí hiệu: - Bao gồm: Sai lệch độ song song, vuông góc, đồng tâm, b. Dung sai vị trí: giá trị cho phép lớn nhất của sai lệch vị trí. Kí hiệu T 26 2.2.5.3. Cách ghi dung sai hình dạng và dung sai vị trí: + Ơ thứ nhất : ghi dấu hiệu tượng trưng + Ơ thứ hai: ghi trị số dung sai tính bằng mm. + Ơ thứ ba: ghi chữ cái ký hiệu chuẩn 27 3.1. Chỉ tiêu kinh tế kỹ thuật CHƯƠNG 3: NĂNG SUẤT LAO ĐỘNG VÀ GIÁ THÀNH SẢN PHẨM 3.2. Giá thành sản phẩm 3.3. Biện pháp tăng năng suất lao động, giảm giá thành sản phẩm 28 3.1. Chỉ tiêu kinh tế kỹ thuật : Tht = Tcbkt + Ttc . n + Tht: thời gian hồn thành cả loạt sản phẩm + Tcbkt: thời gian chuẩn bị kết thúc cho mỗi loạt + n: số chi tiết gia cơng (chiếc, cái) + Ttc: thời gian gia cơng từng chiếc cho mỗi nguyên cơng Ttc = T0 + Tp + Tpv + Tk Với: T0: thời gian cơ bản Tp: thời gian phụ Tpv: thời gian phục vụ Tk: thời gian nghỉ ngơi và làm những việc sinh lý tự nhiên 3.1.1. Chỉ tiêu về thời gian T: 4/17/2010 8 29 + Ttc: thời gian tạo ra một đơn vị sản phẩm 3.1.2. Chỉ tiêu về năng suất N: tcT N 1 3.2. Giá thành sản phẩm: - Giá thành sản phẩm là năng suất lao động của xã hội, là tất cả các chi phí bằng tiền trong một đơn vị sản phẩm - Giá thành bao gồm tiền vật liệu, tiền cơng nhân, tiền khấu hao cơng cụ lao động, thuế, nhà cửa, 30 3.3. Biện pháp tăng năng suất lao động, giảm giá thành sản phẩm: 3.3.1. i gian chuẩn bị kết thúc cho mỗi loạt Tcbkt: 3.3.2. i gian cơ bản T0: 3.3.3. i gian phụ Tp: 3.3.4. i gian phục vụ Tpv: 3.3.5. i gian nghỉ ngơi và nhu cầu sinh Tk: 31 4.1. Một số chi tiết máy điển hình: CHƢƠNG 4: CHI TiẾT MÁY VÀ CƠ CẤU MÁY ĐiỂN HÌNH 4.2. Một số mối ghép điển hình: 4.3. Các hình thức truyền động: 4.4. Các cơ cấu truyền động: 32 4.1. Một số chi tiết máy điển hình: - Là chi tiết máy dùng để đỡ các chi tiết máy quay, truyền động, - Gồm: Trục tâm, trục truyền, trục truyền chung, trục thẳng, trục bậc, 4.1.1. Trục: - Dùng để đỡ các trục quay, truyền tải trọng từ trục đến giá đỡ. - Gồm: ổ đỡ, đỡ chặn, chặn, ổ bi, đũa, kim, 4.1.2. Ổ lăn: 4/17/2010 9 33 - Là một loại ổ trục, dùng để đỡ các trục quay nhằm mục đích giảm ma sát. - Gồm: ổ đỡ, chặn, đỡ chặn, một nữa, hai nữa, 4.1.3. Ổ trƣợt: 34 4.2. Một số mối ghép điển hình: - Là mối ghép được liên kết bởi đinh tán, thường dùng trong các mối ghép chịu tải trọng rung, va đập: đường ray, cầu sắt, 4.2.1. Mối ghép đinh tán: - Cĩ 2 phương pháp: tán nĩng và tán nguội 35 4.2.2. Mối ghép ren: Mối ghép bulong – đai ốc - Là mối ghép được liên kết bởi bulong – đai ốc hoặc vít, vít cấy. Thường dùng cho mối ghép tháo lắp nhiều lần - Mối ghép dễ bị tháo lỏng khi chịu tải rung động 36 4.2.3. Mối ghép then và then hoa: - Dùng để cố định các chi tiết máy trên trục theo phương tiếp tuyến, truyền tải trọng từ trục đến chi tiết máy lắp trên trục và ngược lại. - Ví dụ: ghép bánh răng với trục, a. Mối ghép then: - Bao gồm: mối ghép then bằng, then bán nguyệt, then vát Mối ghép then bán nguyệt 4/17/2010 10 37 - Mối ghép then hoa được xem như mối ghép then bằng gồm nhiều then làm liền với trục. Dùng với tải trọng lớn, yêu cầu độ đồng tâm cao hoặc cần di trượt bạc dọc b. Mối ghép then hoa: Mối ghép then hoa 38 4.3. Các hình thức truyền động: - Dùng để truyền chuyển động giữa hai trục song song và xa nhau, làm việc dựa trên lực ma sát giữa dây đai và bánh đai nên cĩ hiện tượng trượt đai 4.3.1. Bộ truyền đai : 1 2 2 1 )1( n n D D i - Tỷ số truyền động: 39 - Dùng để truyền chuyển động giữa hai trục song song hoặc cắt nhau - Gồm: Bộ truyền bánh răng trụ, răng nghiêng, bánh răng cơn, 4.3.2. Bộ truyền bánh răng: - Tỷ số truyền động: 1 2 2 1 n n Z Z i Bộ truyền bánh răng trụ 40 - Dùng để truyền chuyển động giữa hai trục vuơng gĩc với nhau trong khơng gian 4.3.3. Bộ truyền trục vít – bánh vít: Bộ truyền bánh răng trụ - Tỷ số truyền động: 1 2 n n Z K i 4/17/2010 11 41 - Dùng để truyền chuyển động giữa hai trục song song với nhau và cách xa nhau hoặc truyền chuyển động từ một trục dẫn đến nhiều trục bị dẫn 4.3.4. Bộ truyền xích: - Tỷ số truyền động: 1 2 2 1 n n Z Z i 42 - Dùng biến đổi chuyển động quay thành chuyển động tịnh tiến 4.3.4. Bộ truyền vít – đai ốc: - Độ dịch chuyển của đai ốc: KtnS .. 43 4.4. Các cơ cấu truyền động: -Truyền động vơ cấp cho ta tốc độ bất kỳ giữa 2 tốc độ giới hạn nmax và nmin. - Gồm: bánh đai cơn đai dẹt, bán cơn ma sát con lăn , 4.4.1. Truyền động vơ cấp : 44 - Cho tốc độ nhất định giữa 2 tốc độ giới hạn nmax và nmin. - Gồm: cơ cấu bánh răng di trượt, nooc-tơng, ly hợp vấu, 4.4.2. Truyền động phân cấp : Cơ cấu ly hợp vấuCơ cấu bánh răng di trượt 4/17/2010 12 45 - Biến chuyển động quay từ động cơ thành chuyển động tới – lui của dao cắt, thường sử dụng cơ cấu Culit 4.4.3. Truyền động gián đoạn: 46 5.1. Nguyên lý cắt gọt kim loại CHƢƠNG 5: GIA CƠNG CẮT GỌT KIM LoẠI 5.2. Một số phương pháp gia công cắt gọt kim loại 5.3. Các phương pháp gia công đặc biệt 47 5.1. Nguyên lý cắt gọt kim loại: - là quá trình con người sử dụng dụng cụ cắt để hớt bỏ lớp kim loại thừa khỏi chi tiết, nhằm đạt được những yêu cầu cho trước về hình dáng, kích thước, vị trí tương quan giữa các bề mặt và chất lượng bề mặt của chi tiết gia cơng 5.1.1. Phân loại các phương pháp cắt gọt kim loại: a. Theo nguyên lý tạo hình: gia công chép hình, theo vết, bao hình b. Theo yêu cầu kỹ thuật: gia công thô, bán tinh, tinh c. Theo máy gia công: gia công tiện, phay, bào, mài, d. Theo bề mặt gia công: gia công mặt phẳng, trụ ngoài, trụ trong, 48 5.1.2. Hệ thống công nghệ trong gia công cắt gọt: - Bao gồm: máy, dao, đồ gá và chi tiết gia cơng a. Máy: cung cấp năng lượng và các chuyển động cần thiết b. Dao: trực tiếp cắt bỏ lớp lượng dư ra khỏi chi tiết c. Đồ gá: xác định và giữ vị trí tương quan giữa dao và chi tiết d. Chi tiết gia cơng: là đối tượng của quá trình cắt gọt 5.1.3. Các bề mặt hình thành trong quá trình gia công cắt gọt : 4/17/2010 13 49 5.1.4. Các chuyển động cắt gọt : a. Chuyển động chính (chuyển động cắt): - Là chuyển động tạo hình giữa dụng cụ cắt với bề mặt gia cơng để tạo ra phoi và tiêu hao năng lượng cắt lớn nhất - VD: chuyển động thẳng (bào, xọc, ) hay chuyển động quay trịn (tiện, khoan, ) b. Chuyển động bước tiến: - Là những chuyển động tiếp tục tạo phoi, gồm chuyển động chạy dao s và chuyển động theo phương chiều sâu cắt t 50 5.1.5. Quá trình tạo phoi: a. Bản chất của quá trình tạo phoi: - Đó là quá trình biến dạng trượt của các phần tử kim loại theo các mặt trượt của chúng. b. Các dạng phoi: - Gồm các dạng: phoi vụn, phoi xếp, phoi dây. 51 5.1.6. Nhiệt cắt: - Nhiệt lượng sinh ra trong quá trình cắt: Q = Q 1 + Q 2 + Q 3 + Q 4 Trong đó: Q: nhiệt lượng sinh ra trong quá trình cắt Q 1 : công ma sát trong giữa các phần tử vật liệu gia công Q 2 : công ma sát ngoài giữa phoi và mặt trước dao. Q 3 : công ma sát giữa bề mặt chi tiết gia công và mặt sau dao. Q 4 : công cắt đứt phoi. - Sự truyền nhiệt: + Nếu Q=100% thì Qphoi = 75%; Qdao = 20%; Qct = 4%; Qmt = 1% mtctdaophoi QQQQQ 52 5.1.7. Sự mòn dao: a. Mòn mặt sau b. Mòn mặt trước d, e. Mòn mũi dao - Nguyên nhân: dao mòn do nhiệt cắt, ma sát giữa dao và phôi, ma sát giữa dao và phoi + Dao mòn sẽ làm cho lực cắt tăng lên, rung động tăng, độ nhám bề mặt tăng lên, nhiệt cắt tăng, + Có thể phục hồi bằng cách mài lại các góc độ của dao theo yêu cầu gia công 4/17/2010 14 53 - Là thời gian làm việc liên tục giữa 2 lần mài dao, ký hiệu là T (phút). - Phụ thuộc vào nhiều yếu tố: vật liệu làm dao, vật liệu gia công, thông số hình học của dao, chế độ cắt, dung dịch trơn nguội, . . . - Được qui định trong sổ tay: thường là 30, 60, 90 hay 120 phút, Tuổi bền dao: Biện pháp giảm mòn dao: - Để giảm mòn dao, cần phải có các biện pháp giảm nhiệt, giảm lực ma sát như: + Sử dụng dung dịch trơn nguội như: xút, êmunxi, nước xà phòng, + Chọn chế độ cắt (s, t, v) hợp lý + Chọn vật liệu chế tạo dao hợp lý, góc độ dao mài đúng yêu cầu + Tăng cường độ cứng vững của hệ thống công nghệ (máy, dao, phôi, đồ gá) 54 5.2. Một số phương pháp gia công cắt gọt kim loại: 5.2.1. Phương pháp tiện: -Là phương pháp gia công thông dụng nhất để tạo mặt trụ tròn xoay trong và ngoài, tiện ren, tiện côn, vạt mặt đầu, cắt đứt, . . . + Chuyển động cắt chính là chuyển động quay tròn của chi tiết. + Chuyển động chạy dao là chuyển động tịnh tiến của bàn xe dao 55 Mâm cặp: dùng để định vị và kẹp chặt phôi khi gia công - Các dụng cụ khi tiện: Mũi chống tâm: dùng để đỡ chi tiết có chiều dài lớn Giá đỡ (luy- nét): giúp tăng độ cứng vững khi gia công chi tiết dài, kém cứng vững 56 5.2.2. Phương pháp phay: - Phay là phương pháp gia công kim loại phổ biến, là một trong những phương pháp gia công đạt năng suất cao + Chuyển động cắt chính: chuyển động quay tròn của dao. + Chuyển động chạy dao: chuyển động tịnh tiến của chi tiết + Chuyển động chiều sâu cắt t: nâng lên hạ xuống của bàn máy 4/17/2010 15 57 + Phay thuận: là phương pháp phay mà chiều quay của dao cùng chiều với hướng tịnh tiến của phôi tại điểm tiếp xúc A - Phương pháp phay thuận và phay nghịch: + Phay nghịch: là phương pháp phay mà chiều quay của dao ngược chiều với hướng tịnh tiến của phôi tại điểm tiếp xúc A 58 5.2.3. Phương pháp bào, xọc: - Là phương pháp gia công cắt gọt phôi có bề mặt phẳng. Xọc được xem như là bào đứng + Chuyển động cắt chính: chuyển động tịnh tiến Đi – Về của dao + Chuyển động chạy dao: chuyển động tịnh tiến của bàn máy + Chuyển động chiều sâu cắt t: bàn máy nâng lên hoặc hạ xuống 59 Đặc điểm: - Bào dùng để gia công mặt phẳng và các mặt định hình có đường sinh thẳng. Đặc biệt đối với những rãnh dài và hẹp - Xọc có thể gia công các mặt trong lỗ lớn như rãnh then trên bánh răng. - Bào và xọc cho năng suất thấp vì: + Số lưỡi cắt tham gia cắt gọt ít. + Tốn nhiều thời gian cho hành trình chạy không. + Vận tốc cắt thấp . 60 5.2.4. Phương pháp khoan, doa: Khoan: - Là phương pháp gia công lỗ thông dụng, với đường kính ≤ 35mm + Chuyển động cắt chính là chuyển động quay tròn của dao + Chuyển động chạy dao là chuyển động dọc trục chi tiết của dao 4/17/2010 16 61 Doa: - Là phương pháp gia công tinh lỗ sau khi khoan, sửa sai kích thước. - Không doa được lỗ bít đáy - Mũi doa có nhiều lưỡi cắt hơn mũi khoan 62 5.2.5. Phương pháp mài: - Mài dùng để gia công tinh, nâng cao độ chính xác và độ bóng + Chuyển động cắt chính là chuyển động quay tròn của đá mài + Chuyển động chạy dao s: chuyển động tịnh tiến của chi tiết + Chuyển động điều chỉnh chiều sâu cắt t: của đầu mang đá 63 Đặc điểm: - Ở đá mài, các lưỡi cắt không giống nhau. - Tốc độ cắt khi mài rất cao khoảng 30 m/s. - Độ cứng của hạt mài cao, cắt được thép đã tôi, hợp kim cứng. - Nhiệt độ phát sinh trong quá trình mài rất lớn. - Trong quá trình cắt, đá mài có khả năng tự mài sắc một phần. - Việc điều chỉnh quá trình mài rất khó khăn 64 5.3. Các phương pháp gia công đặc biệt: 5.3.1. Đặc điểm: - Gia công được bề mặt phức tạp, kích thước nhỏ, vật liệu có độ cứng cao. - Không cần sử dụng dụng cụ gia công có độ cứng cao hơn vật liệu gia công. - Tiết kiệm được nguyên liệu, nâng cao hệ số sử dụng vật liệu. - Đạt năng suất, chất lượng và hiệu quả kinh tế cao trong trường hợp rất rất khó hoặc không thể gia công bằng phương pháp khác - Thiết bị đắt tiền, tốn kém 4/17/2010 17 65 - Là phương pháp gia công điện vật lý bằng cách phóng điện ăn mòn vật liệu gia công khi truyền năng lượng qua rãnh dẫn điện 5.3.2. Các phương pháp gia công đặc biệt: a. Gia công bằng tia lửa điện: 66 - Là quá trình hoà tan điện cực dương trong môi trường chất điện phân khi có dòng điện đi qua b. Gia công điện hóa: 67 - Là quá trình là cung cấp dao động siêu âm cho dụng cụ cắt hoặc chi tiết gia công, tạo ra sự dịch chuyển tương đối giữa bề mặt gia công và lưỡi cắt với tốc độ lớn, tần số cao, biên độ dịch chuyển nhỏ, . . . c. Gia công siêu âm: 68 6.1. Tổng quan về cơ khí hóa – tự động hóa: CHƯƠNG 6: CƠ KHÍ HÓA – TỰ ĐỘNG HÓA TRONG SẢN XUẤT CƠ KHÍ 6.1.1. Khái niệm: a. Cơ khí hóa: - Là sự thay thế sức lực của con người bằng máy móc để thực hiện nhanh chóng những công việc nặng nhọc - Người công nhân chỉ có việc điều chỉnh máy hoặc vận hành mà không phải dùng sức để gá lắp vật, di chuyển dao, b. Tự động hóa: - Là sự phát triển hoàn chỉnh của cơ khí hóa, trong đó thiết bị điều khiển tự động sẽ thay thế việc điều khiển bằng tay. - Tự động hóa cũng có thể tiến hành toàn bộ hoặc từng phần 4/17/2010 18 69 6.1.2. Ý nghĩa: - Cơ khí hóa và tự động hóa không chỉ có ý nghĩa về mặt kinh tế, kỹ thuật mà nó còn có ý nghĩa rất to lớn về mặt xã hội. Nó giúp cho người lao động giảm bớt nặng nhọc, rút ngắn thời gian gia công, giảm bớt tai nạn lao động, các yếu tố độc hại, yếu tố nguy hiểm, - Cơ khí hóa và tự động hóa là mục tiêu, phương hướng chính về tiến bộ kỹ thuật của các quốc gia trên thế giới. 70 6.2. Nguyên tắc ứng dụng cơ khí hóa – tự động hóa: Muốn ứng dụng cơ khí hóa – tự động hóa cần phải đáp ứng các nhu cầu cơ bản sau: + Công suất lớn + Tốc độ cao + Phương tiện, điều kiện hiện đại, một người có thể điều khiển nhiều máy đồng thời. + Giảm thời gian lao động, tăng năng suất, giảm giá thành và hiệu quả kinh tế đạt cao nhất 6.3. Cơ khí hóa trong sản xuất cơ khí: - Trong sản xuất cơ khí, các công việc cần thiết phải được cơ khí hóa thường là các công việc nặng nhọc như: vận chuyển phôi, lắp đặt máy, lắp ráp các chi tiết máy lớn, gá đặt phôi, Các phương tiện cần được trang bị là: cầu trục, palăng, xe rùa, xe nâng, băng tải, 71 6.4. Tự động hóa trong sản xuất cơ khí: 6.4.1. Điều khiển thụ động (passive control): - Là dạng điều khiển dựa trên một chương trình đã được định sẵn trước đó nhưng công việc điều chỉnh thông số rất hạn chế. Ví dụ: điều khiển bằng cam, bằng bìa đục lỗ, 6.4.2. Điều khiển chủ động (active control): - Là dạng điều khiển dựa trên một chương trình đã được định sẵn trước đó nhưng có khả năng kiểm soát thông số của quá trình và điều chỉnh dữ liệu đầu vào. Ví dụ: điều khiển kỹ thuật số CNC, 72 6.5. Ứng dụng kỹ thuật CAD – CAM – CNC trong sản xuất cơ khí: 6.5.1. CAD (Computer Aided Design): thiết kế nhờ sự trợ giúp của máy tính - Sử dụng phần mềm như: Auto Cad, Pro E, Solid Work, Mechanical Desktop, - Rất tiện lợi khi chỉnh sữa hay thay đổi thông số. 6.5.2. CAM (Computer Aided Manufacturing): gia công nhờ sự trợ giúp của máy tính - Các phần mềm CAM chuyên dùng như: Master Cam, - Tiết kiệm chi phí và tránh tình trạng gia công chi tiết bị phế phẩm do chương trình sai. 6.5.3. CNC (Computer Numerical Control): điều khiển kỹ thuật số - CNC giúp giảm thời gian phụ, thay dao tự động, hiệu chỉnh sai số dễ dàng, đặc biệt gia công CNC rất an toàn cho người lao động. 4/17/2010 19 73 CHƯƠNG 7: VẬT LIỆU DÙNG TRONG CƠ KHÍ 7.1. Các tính chất cơ bản: 7.2. Thép 7.3. Gang: 74 7.1 Các tính chất cơ bản: - Là những đặc trưng cơ học biểu thị khả năng của kim loại hay hợp kim chịu được tác động của các loại tải trọng. 7.1.1. Cơ tính: - Là tính chất của kim loại thể hiện qua các hiện tượng vật lý khi thành phần hóa học không thay đổi. 7.1.2. Lý tính: - Là độ bền của kim loại đối với những tác dụng hóa học của các chất khác nhau như O 2 , H 2 O, axit, .. mà không bị phá hủy. 7.1.3. Hóa tính: - Là tính chịu được các dạng gia công khác nhau như: đúc, rèn, 7.14. Tính công nghệ: 75 7.2.1. Thép cacbon: 7.2. Thép: Là hợp chất của Fe-C (%C<2.14%; Mn 0.8%; Si 0.4%; P 0.05%, S 0.05%) Ký hiệu thép: + Thép chất lượng thường: CT31, CT33 + Thép chất lượng tốt: C40, C45, + Thép cacbon dụng cụ: CD80, CD50, . 76 7.2.2. Thép hợp kim: Là thép ngồi sắt và cacbon người ta cịn đưa thêm vào các nguyên tố hợp kim để tăng tính chất của thép theo ý muốn. - Giới hạn lượng chứa để phân biệt tạp chất và nguyên tố hợp kim: Mn: 0.8-1.0%; Si: 0.5-0.8%; Cr: 0.2-0.8%; Ni: 0.2-0.6%; W: 0.1-0.5%; Mo: 0.05-02%; Ti: 0.1%; Cu: 0.1%; B: 0.002% Ký hiệu thép: + TCVN 1759-75 quy định mác thép như sau: 9Mn2, 12Cr18Ni9TiĐ, 4/17/2010 20 77 7.3. GANG: - Là hợp chất của sắt và cacbon (%C>2.14%) và một ít các nguyên tố Mn, Si, P, S. - Các loại gang thơng dụng thường chứa: 2.04.0%C, 0.43.5%Si, 0.201.5%Mn, 0.040.65%P, 0.020.15%S. Gang xám: - Được ký hiệu bằng chữ GX. Ví dụ: GX15-32 cĩ giới hạn bền kéo nhỏ nhất là 150 Mpa và giới hạn bền uốn nhỏ nhất là 320MPa Gang cầu: - Được ký hiệu bằng chữ GC. Ví dụ: GC42-12 cĩ giới hạn bền kéo nhỏ nhất là 420 MPa và độ dãn dài tương đối 12%
File đính kèm:
giao_trinh_co_khi_dai_cuong.pdf